With exploration in harsh environments and consequent high-pressure and high-temperature conditions, calculating reservoir properties has become complex and changes in pressure-transient response need to be understood and appreciated by taking appropriate measures. The challenges arising with drilling and testing of high-pressure/high-temperature (HP/HT) gas wells that produce hydrogen sulfide (H2S) and carbon dioxide (CO2) in the Krishna Godavari basin are discussed.
Introduction
In the exploration campaign in the Krishna Godavari basin off the east coast of India, four wells were drilled, discovering a very tight gas reservoir with an average pressure of 12,000 psi and an average recorded temperature of 360°F and classified as an HP/HT reservoir, as shown in Fig. 1. This paper discusses the experience drilling four wells with a jackup rig in average water depth of 60 m.
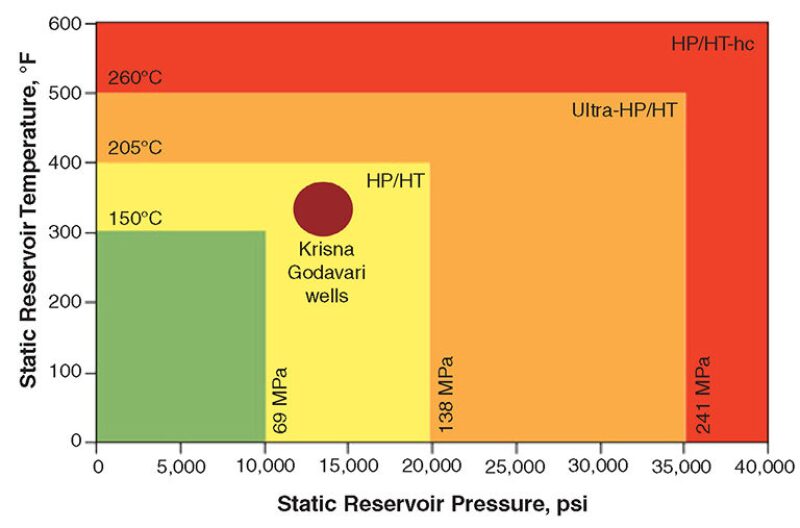
Well-A was the first well. Well-B discovered and flowed gas from stratigraphy below the section encountered in Well-A. Well-C encountered the same sands found in Well-A, and additional shallower sands not encountered in Well‑A or Well‑B were discovered. The reservoir section is overlain by shale. Well-A was drilled in six sections because it was the first exploratory well; the other three wells were drilled in five sections. All wells had sections of 36-, 26-, 17½-, 12¼-, and 8½-in. hole and Well-A had an additional 6-in. section. These sections were cased with 30-, 20-, 13⅜-, 9⅝-, and 7-in. liner casings, respectively, and Well-A included a 5-in. liner. The reservoir section expected in 8½-in. hole from seismic and log data was proved while drilling Well-A and was appraised in Well-B, Well-C, and Well-D. Well-A and Well-B were drilled to total depth with water-based mud (WBM). The 12¼-in. section of Well-C was drilled with WBM, while the 8½-in. section was drilled with synthetic-oil-based mud (SOBM). The shale sections and reservoir section in Well-D were drilled using SOBM. The mud program was designed on the basis of the pore-pressure-leakoff-test (LOT) vs. depth chart shown in Fig. 2.
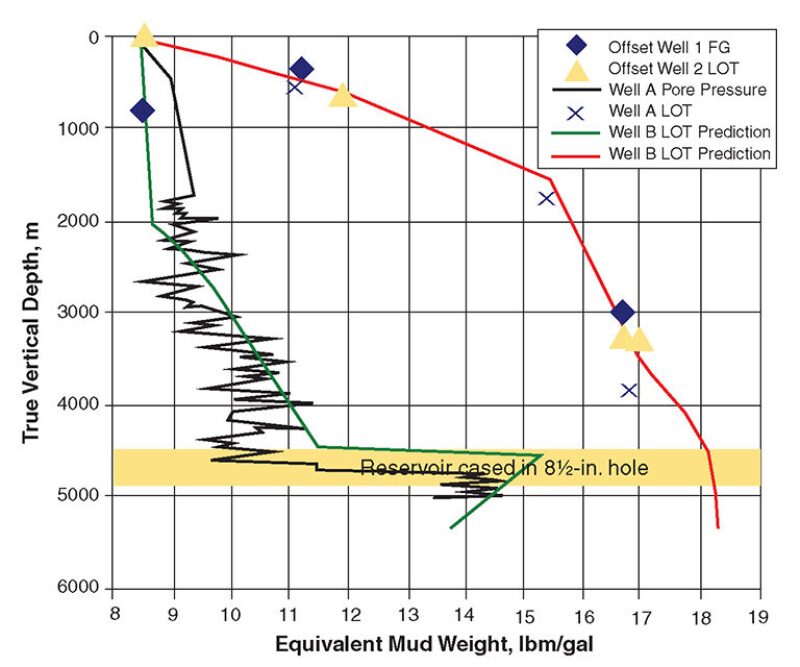
This environment is very harsh, and problems faced during drilling and testing were the result of unexpected variations in high pressure and temperature. To mitigate problems associated with the HP/HT environment, it was highly important that extensive planning be performed before any drilling, testing, or stimulation operation. Seven drillstem tests (DSTs) were performed in the four wells, with bottomhole pressure and temperature as high as 12,600 psi and 410°F, respectively. HP/HT tools were used during these DSTs, stressing the selection of elastomer. The selection of proper-grade tubing, HP/HT-rated seal packer, gauges, and explosives was considered to be of great importance. The surface-equipment package was selected to meet the HP/HT requirement of these wells because of the H2S, CO2, and sand-production problems. Health, safety, and environmental issues needed special care to eliminate any loss of life or damage to property without compromising the objectives of the operation.
Challenges While Drilling
In HP/HT reservoirs, controlling pressure and temperature is the most challenging safety concern. All activities, including drilling, completion, and well testing, expose equipment to the harsh operating environment. Operating conditions approach the upper limit of hardware parameters, thus increasing the chances of tool failure or metal fatigue that could lead to lost rig time, cost overruns, and high replacement costs. To ensure safe and efficient operations, standard operating procedures should be set and followed strictly. Quality-control procedures for all materials and equipment should be established to ensure that temperature and pressure operating limits are not exceeded.
Drilling Fluid. During exploration, a significant understanding of the lithology, formation tops, and associated drilling risks and operational hazards must be acquired. High temperatures have a strong influence on mud rheology, which has a direct relationship with drilling efficiency by affecting well hydraulics and the suspension of cuttings. A well-designed mud program is essential, and a good mud program preserves desirable rheological properties at high temperature. It also balances the mud weight to contain formation pressure with minimum invasion to achieve a satisfactory rate of penetration in the wells. During development, all intervals above the reservoir sections were drilled with WBM. Before entering the reservoir section, the mud system was switched to an SOBM, which is better suited for drilling water-sensitive shale. Adequate salinity was determined through field experience. Oil-based mud (OBM) usually allows faster drilling than WBM while providing excellent shale stability. OBMs are suited to drill formations in which the bottomhole temperature exceeds WBM tolerances, especially in the presence of contaminants (e.g., water, gas, cement, and salt) up to 550°F. An OBM has a thin filter cake, and the friction between the pipe and the wellbore is minimized, thus reducing the risk of differential sticking. Also, it is especially suited for highly deviated and horizontal wells. Pipe corrosion is controlled because oil is the external phase and it coats the pipe. The most interesting properties regarding corrosion are that oil is nonconductive, additives are thermally stable and do not form corrosive products, and bacteria do not thrive in OBM. However, SOBM was chosen over OBM because SOBM is more readily biodegradable than OBM, the base viscosity is higher than that of OBM at normal conditions, SOBM is less toxic than OBM, and it provides good hole gauge and a good environment for logging.
Temperature Limit for Logging-While-Drilling (LWD) and Measurement-While-Drilling (MWD) Tools. The LWD and MWD tools should be rated for conditions of 400°F and 12,000 psig. These tools have been used in the wells with reasonably good success. Occasionally, there have been problems of temporary and permanent data loss. These issues were diagnosed as tool failure primarily caused by high temperature, excessive vibration/shock, or both. Because service companies are expanding the operating range of these tools, the tools should be able to be deployed with more confidence in the future. The primary concerns regarding high temperature are reduction in strength and the change in corrosion mechanisms. Usually, higher temperatures increase the severity of corrosion. Pitting, crevice formation, and stress-corrosion cracking are intensified by an increase in temperature. The presence of H2S, CO2, and chlorides aggravates the situation.
Drilling Problems. The 12¼-in. section was drilled mainly through the shale overlying the sandstone formations, and was drilled with WBM with KCl and an enhanced polyglycol system, except in Well‑D because it was the last well drilled in the series of four wells and was planned from the learnings obtained from the previous wells. In spite of many additives used in WBM for clay-hydration and -inhibition drilling, this section encountered problems such as low rate of penetration, hole-cleaning problems because of cavings falling in the wellbore, wellbore fill, stuck pipe, bit balling, and high torque values damaging topdrive systems, all of which were attributed to clay swelling resulting from hydration. The same problems were observed while drilling the 8½-in. section with WBM. Therefore, the 8½-in. section in Well‑C was drilled with SOBM because the problems with clay hydration in shale were alleviated. Hence, SOBM was used to drill the 12¼- and 8½-in. sections in Well‑D. No problems relating to clay hydration were experienced while drilling with SOBM because SOBM did not destabilize clay. However, most of the effects from high temperature and pressure occurred when the bottomhole temperature reached 410°F, requiring continuous circulation of mud to cool the LWD and MWD tools for proper functioning. As a result of the high temperature, high wear, and high bottomhole pressure, rubber elements from the mud motor were seen at shakers. The mud pH had to be kept higher than program to compensate for reduction in pH with the very high temperatures. Gelation also had been an issue with WBM used in the very-high-temperature environment. The mud weight had to be kept close to 14.9 lbm/gal in the 8½‑in. section to overcome reservoir pressures and to overcome swabbing effects along with the density reduction with higher temperature. The low-gravity solids while drilling were a major problem in these sections because they obstructed the shakers with increased viscosity from clays, and drilling fluid had to be diluted and sheared to reduce fluid loss at the shakers and flowline. A mud cooler also was required to cool the mud.
Modular Formation Tester. A comprehensive study was carried out to analyze the reservoir by use of wireline-log data, core data, and well-test results. Formation tops were available from the logs and were used for modeling. Shale volume, total porosity, effective porosity, and water saturation were calculated with standard techniques. The core data were used to calibrate the log analysis and understand the mineralogical behavior. All four wells were logged with the same log suites, including caliper, gamma ray, formation-capture cross-section, acoustic, neutron, density, and deep-resistivity logs. The difference between the density and neutron logs and the aluminum content observed from the elemental-capture-spectroscopy (ECS) tool were used as shale indicators. Density-log data were used to estimate porosity. Formation-capture cross section was used as a clay indicator along with ECS aluminum values. Porosity was calculated from density/neutron data corrected for clay effects. Because SOBM was used in the 8½-in. section, the log data and hole quality were excellent. Clay volume was computed from gamma ray, neutron, and formation-capture cross-section logs. The neutron and formation capture showed similar results, but the gamma ray showed deviation caused by mineralogical effects. Clay indicators are logs that enable estimating shale volume in shaly sands. Multiple clay indicators were used to ensure correctness of calculated shale volume. The gamma ray data were ineffective when thorium content of the sands was high. Log interpretation showed that a large section of sandstone is interbedded with claystone and siltstone in the reservoir.
Challenges While Well Testing
Careful planning and tool/equipment selection were critical to successful well tests. Possible operational problems include the following:
- Temperature restrictions of the flow head and surface equipment during the flow period
- Gauge and downhole-tool failure resulting from exposure to high bottomhole temperatures
- Selecting suitable perforation charges for HP/HT environments
Most of the these issues were addressed by careful planning, meticulous test design, and proper selection of tools and equipment suitable for the HP/HT environment.
Elastomers. The following conditions should be considered before selecting elastomers.
Fluids to be Sealed. The type of well fluid should be considered, including drilling mud and aggressive brines such as formites or calcium bromides. Acids and alcohols also are important parameters for selection.
Temperature Range. Include the minimum and maximum operating conditions along with thermal cycling and potential exclusions. Some seals are not appropriate for low temperatures. High temperature will soften elastomers, increasing the rate of diffusion of liquids and gases and accelerating chemical degradation. These can occur irrespective of the service pressures involved.
Pressure Range. Maximum and minimum operating ranges must be considered along with the compression and decompression rate if the pressure is high. High pressures increase the possibility of physical-based-deterioration processes such as extrusion (when gases are involved).
DST Tools. All DST materials exposed to H2S should meet the conditions established in NACE Standard MR-01-75 for the region vulnerable to sulfide-stress corrosion. Here, it was necessary to use materials that were not very hard, with a Rockwell hardness coefficient, or HRC, ≤22, except in the case of corrosion-resistant alloys for which hardness may be greater. It should be kept in mind that the need to use materials with a lower hardness may conflict with mechanical-resistance requirements that must be met by the string. The DST tools should be of HP/HT rating and should be pressure and function tested off line to at least 80% of their maximum pressure rating. Tools that have a ball mechanism or flapper operation should be redressed before running them in the hole. Gauge carriers should be coupled with gauges and pressure tested to determine the error resolution. A sufficient quantity of O-rings should be available, and a new ring should be used each time to minimize pressure losses downhole. Rupture disks should be marked clearly according to the calculations to eliminate chances of error while installing them before running the tool in the hole. The DST-string design should have adequate backup valves to minimize unexpected conditions. Apart from the DST tools, there should be a sufficient number of crossovers depending on the type of connection of tools used.
Tubing Selection. Produced gas contained approximately 4–6% CO2 and 100 ppm H2S, which is corrosive when combined with produced water. Duplex, Super Duplex, or Inconel 718, 725, 825, or 925 tubing is advised in such conditions, although it is possible to inject corrosion inhibitor downhole and to use carbon-steel tubing. The tubing is resistant to corrosion and requires minimal operational maintenance. In recent years, this tubing has been the standard for corrosive applications. Tubing threads should be inspected closely by the tubing-running service provider, and only those that qualify at the minimum torque values should be run in the hole.
Packer Selection. When testing deep high-pressure gas wells, collapse and tension along the casing/liner and test string constitute a true cause for concern. The casing/liner may collapse below the packer, while the test string may collapse above the packer during attempts to flow. When reverse-circulation valves are being opened, collapse of the tubing/test tools may occur immediately above the packer if backpressure in the test string is inadequate. Tensioning may cause the tubing to rupture immediately below the control head during hydrostatic testing of the test string. In packer selection, consideration must be given to the behavior of the packer material if CO2 or H2S is expected in the reservoir fluids. If alloys such as K-Monel (resistant to hydrogen embrittlement) are used, the possibility of galvanic corrosion at the packer/casing-steel interface must be examined. Generally, packer fluid occupies the primary annulus and usually is brine with low corrosive action. Potential leaks can be caused by elastomeric extrusion or the temperature/chemical effects on the elastomer. Packing-element failure could be caused by insufficient load applied to pack off against the casing, or the element being damaged during installation. Packers sometimes fail when the sealing element extrudes through the backup element.
Explosives. The perforation explosive should be selected on the basis of maximum temperature and the time that it will stay in hole. There are three varieties of explosives, shown in Fig. 3, that qualify for high-temperature conditions: HNS, HMX, and RDX. Their reliability with temperature decreases with time. Tubing-conveyed perforating guns should be used to reduce or avoid formation damage. Perforating should be conducted with an underbalance of 1,500 to 2,000 psi, using a diesel or water cushion, with the well beginning production immediately following the perforation operation. Underbalancing should not exceed 2,000 psi, to avoid bottomhole-equipment damage. The firing head should have a backup (i.e., hydraulic firing head as primary method and mechanical as a backup) in case of primary-method failure.
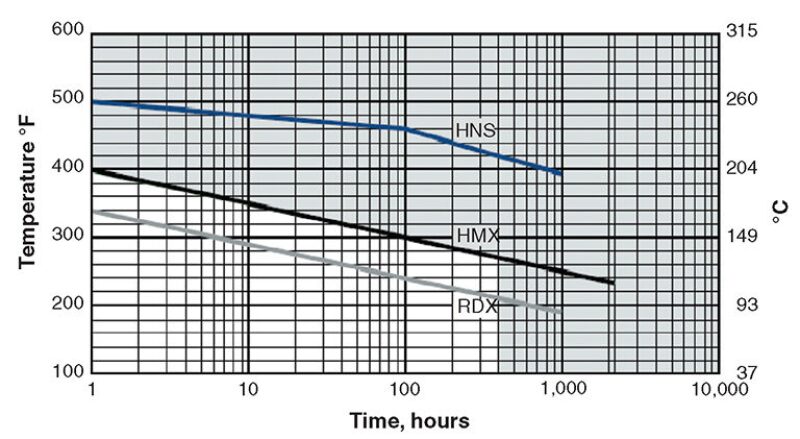
Gauges. Even if the electronic memory gauges are extremely well specified, it is highly advisable that high-temperature mechanical gauges be used as backup gauges. Electronic high-temperature gauges have a high failure rate when exposed to harsh conditions over long periods of time. Electronic and mechanical pressure gauges should be placed on gauge carriers with the largest capacity and the smallest external diameter possible. A minimum of four electronic and two mechanical gauges should be used on test strings. Gauge carriers should be placed above the packer and above the test string’s weakest point so that in the worst case the downhole data can be retrieved.
Problems. Among the DSTs performed in the four wells, a few problems were common and consumed much rig time, thereby adding cost to the program. The HP/HT package was selected for well tests, yet many of the tools and much of the surface equipment failed because of unexpectedly high temperatures and sand production. The pressure testing and repairing of the tools before the run required much time. Normal procedure was followed for well testing (i.e., a test run followed by the DST run).
There were several DSTs performed on these four wells, providing many lessons. The HP/HT-rated O-rings should be selected to avoid unnecessary pressure drops resulting from their failure. During sand production, it was necessary to pass the flow through a sand filter before going to the choke manifold, to avoid abrasions or washouts of equipment and connections. Metal-to-metal seals should be changed before final equipment rig up because disassembling the equipment and pressure testing it again requires significant time. To ensure functionality downhole, all DST tools with moving parts, such as balls or flappers, should be redressed and pressure tested to 80% of their maximum rating for proper operation before running in the hole. Rupture-disk ratings should be marked separately to avoid confusion while installing them before running the tool. A minimum of four gauges should be run for any operation to obtain more-reliable data and to ensure that at least two of the guages actually function, thus yielding a reliable quantitative interpretation of the test in terms of such information as depletion, productivity, damage, and permeability. While running in hole, care must be taken to prevent breaking down of weak formations. With a small clearance between the packer element and the hole wall, pressure builds up under the packer that can cause lost circulation. The DST assembly should be pulled out slowly to avoid packer damage. If the pressure continues to increase at the choke manifold even after downhole shut-in, one should not rush to operate the tool again because the problem may be the result of expansion of the gas column trapped between the downhole-tester valve and the choke manifold.
Apart from practical experiences, the test program should include the complete sequence of events, a comprehensive contingency plan, all aspects of safety, and calculation of test-string tension. Further, DSTs should be based on the strictest safety standards and operational procedures. With all data collected into a single volume, all necessary information may be consulted rapidly and directly. Quality control of the material and equipment should be efficacious and rigorous, especially in terms of exposure to high concentrations of H2S.
This article, written by Senior Technology Editor Dennis Denney, contains highlights of paper SPE 155320, “Offshore Drilling and Well Testing of an HP/HT Gas Well: A Case Study,” by Prerak H. Shah, SPE, Harsh T. Pandya, SPE, Harsh Sharma, and Arpit Saxena, SPE, Gujarat State Petroleum Corporation, prepared for the 2012 SPE Oil and Gas India Conference and Exhibition, Mumbai, 28–30 March. The paper has not been peer reviewed.