With every completion, operators can fine-tune their designs. More stages or fewer? More proppant or less?
But what actually drives production improvements? Operators are increasingly seeking low-cost means of determining just that, often pushing readily available data through analytical workflows to determine what’s working. And just what is it worth, anyway, to get the completion right?
As long-sought technology allowing operators to optimize their fractures in real time nears reality, the question arises of how much value a perfect fracture will bring to the bottom line.
Autonomous intelligent fracturing (AIF) capabilities require automated completions equipment responding to decisions that are based on low-cost, real-time measurements fed into optimization models which then determine the value of changing a stage’s design parameters to improve it. Hess wanted to know if it was worth pursuing such a technologically ambitious goal, Craig Cipolla, principal engineering advisor at Hess, told an Unconventional Resources Technology Conference (URTeC) audience in June.
To answer that question, Hess carried out modeling studies to estimate the value of the perfect stage, detailed in URTeC 4044071. That study used the uniformity index (UI), a metric that quantifies completion effectiveness of the stages.
While engineers design completions with a goal of reaching a perfect UI of 1.0, “very rarely do we see a uniformity index of 1. We see something less than that,” Cipolla said.
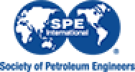