This study develops a workflow to design a proactive workover-optimization workflow by use of genetic algorithms (GAs). The work explored whether a “steered” GA, created by the addition of screening and advanced sampling methods to a “pure” GA, provides sufficient simplification of the problem to make it suitable for routine use in the field. Ultimately, a significant added field value was achieved by the “steered” GA when compared with the “pure” GA.
Introduction
The ultimate goal of field-development optimization is to maximize the objective function while reducing the uncertainty associated with the project value. Efficient reservoir-production planning requires a degree of well-control flexibility. Intelligent wells equipped with downhole flow-control devices and sensors inherently have a greatly increased flexibility to respond to (often unexpected) changes in the well and reservoir performance. Downhole inflow-control valves (ICVs) are used to control the well zonal flow rates. These valves are available in open/close, multiple-position-discrete, or infinitely-variable-position types.
The completion design team is tasked with selecting an appropriate valve type according to the selected production scenario. Model uncertainties and difficulties in finding the optimal ICV control strategy for a dynamic reservoir model often result in the application of reactive control when operating the ICVs, despite the fact that a proactive strategy potentially delivers the highest added value during the field’s life.
A workover operation is often required during the well’s operational life to address well-integrity and flow-assurance problems. The only option available for a conventional well to provide a level of well- and reservoir-management flexibility similar to that achieved by an intelligent well is to carry out an additional type of workover operation (i.e., one that is aimed at improving the well and/or reservoir performance). These are normally carried out as a reaction to observed changes in the well performance. Addressing such problems in a reactive mode carries the risk that the improvement in the well’s performance may not be apparent in the short term or may involve a long-term recovery loss caused by water or gas coning or inefficient reservoir sweep.
Field-workover screening algorithms have been proposed to identify the workovers with the highest added value, but it is clear that a reliable and effective tool able to screen and explore the large search space of the potential workovers and that adds value to the reservoir-management process is not currently available. The search will need to consider the overall performance of the field throughout a specified period while respecting all operational limitations, as well as taking into account the risks and costs of the intervention.
The nature of a workover operation in an interval resembles having an imaginary open/close ICV installed across the interval. This study uses a GA optimization search procedure—one of the most commonly used algorithms in proactive optimization of intelligent wells—to find optimal control strategies by considering both the well and field scale to assign workovers optimally at the full-field level.
Improved Optimization Tools
The GA is a subcategory of evolutionary algorithms that combine a structured information exchange with a “survival-of-the-fittest” approach similar to natural evolutionary mechanisms. GAs are capable of working with discrete and continuous variables and have the advantage of being easily modified for different problems. Hybridization with surrogate models can be added to speed up the optimization. Three advantages of GAs that are important in engineering problems similar to the one described here are:
- The algorithm returns multiple solutions.
- The algorithm is robust.
- Parallel processing is possible.
The working principle of GAs is based on representing a population of individuals (i.e., model solutions) as chromosomes, each of which has an importance (i.e., the objective function’s) value. These chromosomes are then introduced into an evaluation procedure in which selection, reproduction, crossover, and mutation are applied in several iterative sequences. At the end of the evaluation procedure, the best chromosome is taken as the optimized solution.
Application of artificial-intelligence methods to petroleum-engineering problems often requires an appropriate degree of engineering insight to guide the optimizer and to reduce the problem’s dimensionality. This is especially important when the objective-function evaluation is time consuming—for instance, when a dynamic reservoir simulation is being used. On the other hand, an unnecessarily strong steering of the search algorithm by engineering knowledge can affect the search adversely and might lead to a local, rather than a global, optimum being identified. For a discussion of the process of defining the search space and screening the variables by use of case-specific knowledge, please see the complete paper.
Workover Planning in a Real Field
The described methodology has been applied successfully to a large, dead-oil field reservoir-simulation model (Field A) that had been history matched to the first 6 years of production data. The model geology consists of four reservoir formations composed of highly permeable sand layers with thin, interbedded shale layers. In some horizons, these shale layers thicken into shale zones. There is an active aquifer supplemented by a water-injection scheme to support the field pressure. The combination of faults and heterogeneous reservoir properties makes it difficult to achieve an effective sweep of the oil toward the production wells. More than 30 oil producers have been placed within the reservoir. A limited volume of lift gas is available to be distributed among the producers to sustain the production.
Producers are controlled by the minimum bottomhole pressure, the tubinghead pressure, and the group liquid rate. Wells are grouped on the basis of location and the produced-water cut, which is a translation of the available capacity of the surface facilities. The internal optimizer provided by a commercial reservoir simulator was used to optimally distribute the lift gas among the production wells.
This history-matched model suggests that the field is able to maintain the maximum-oil-rate limit in the short term, with a gradual decline starting from (the fictitious date of) the third quarter of 2001. A recommendation for a workover in a conventional well during the plateau period is unlikely to be accepted by management because of the associated costs and operational risks without any gains in oil production. By contrast, the plateau period in a field developed with intelligent wells presents the ideal opportunity to apply a proactive strategy at the completion-zone level to maximize future oil recovery. This is because, during the plateau period, there will be no operational costs, no oil losses, and a minimal risk to the completion because of the high level of reliability achieved by current ICV completions.
This methodology was tested during the gradual-decline period to find the optimum 3-year workover program for the target period of 1 January 2003 to 1 January 2006 (Fig. 1). In this paper, individual oil-bearing geological zones are treated as distinct intervention units. Each zone includes several grid layers in the simulation model. Workover operations involve a production stoppage, increased cost, and risk of loss of the well. The positive contribution of the intervention emerges only as the production profile improves. This fact also implies that sufficient time must be allowed between the last workover and the date of the final economic analysis for the workover to become profitable. Interventions were, therefore, considered only during the first 30 months of the 36-month period being considered. The (final) 6-month period after the last intervention was modeled only to provide the production data for the economic analysis. For the integrated economic model used in this methodology, please see the complete paper.
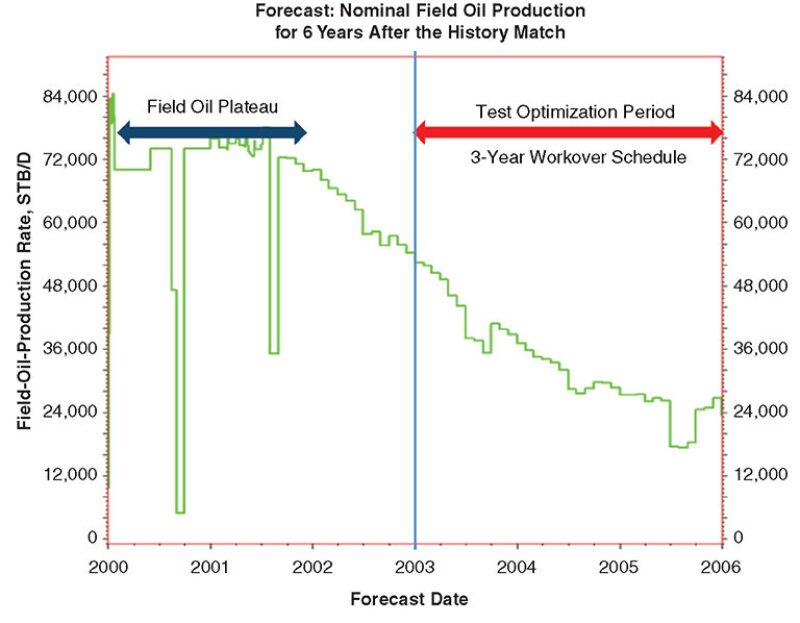
Field-Scale Optimization
This paper discusses two workflows to illustrate the integration of the engineering knowledge into evolutionary algorithms. The initial test considered 107 variables when a GA was used without any engineering-knowledge-driven screening (referred to as a “pure” GA). The large number of constrained variables with interdependencies affects the performance of the GA search algorithm negatively. This interdependency is especially visible when the shut-in time for a newly opened zone is sought. The closing date of a zone that is opened during the period under consideration can fall only between the opening date and the 30th month.
Fig. 2 shows the search performance of this initial test with the “pure” GA that did not include any of the engineering guidance or cutoff values described previously. Therefore, all the 107 well interventions, including dependent closing variables, were included. More oil is recovered in the optimal scenario as compared with the base case (no-action scenario). The optimization progress indicates a scattered search that shows little sign of identifying an optimum value. A number of the iterations had values less than, or close to, the base case. This is because the optimizer, trying to explore the search space, has shut zones with a high oil-production rate.
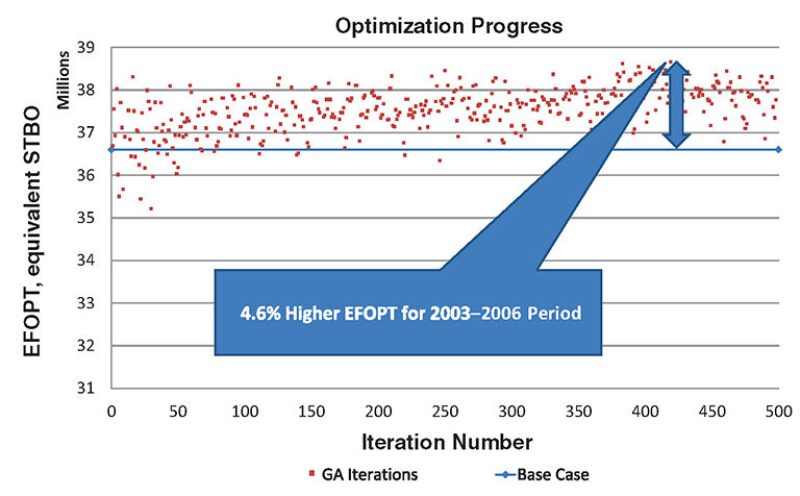
The base-case field-oil-production total (FOPT) for the 3-year period is 36.6 million STB. Optimization shows that the maximum direct cost of workover operations can reach USD 6.9 million, even after inclusion of risk penalties of USD 2.3 million. Note that the total maximum cost (in equivalent stock-tank barrels) of workover operations is equivalent to only 0.8% of the base-case FOPT, which means that the incremental-oil value is far larger than the associated workover costs. Also note that FOPT value for the base case is the no-action scenario that represents continuity of oil production without the risk and cost elements of a workover.
We then added engineering-knowledge-based conditions to “steer” the GA optimizer. The efficiency of the available workstation’s 16 central processing units was maximized by setting the population number to 50 with a replacement factor of 0.28 (i.e., each generation initiates 14 new simulation runs, which could be run in parallel mode on the available high-end, single PC). The crossover rate was set at 0.9, and the mutation rate was 0.05, meaning that 90% of the individuals are combined to generate a new population converging to the optimal point while 5% mutate to ensure a sufficiently wider exploration area.
Over 500 iterations, a maximum of 6.4% higher FOPT is achieved as compared with the base-case scenario. After 700 runs were completed, less than 0.5% variation on the objective functions of the last 14 sets of simulations was seen, and this was deemed an acceptable level of convergence for the optimization. With an average run time of 80 minutes and 14 parallel runs, the whole optimization process took less than 3 days t complete.
The “steered”-GA optimization started with the sampling of 100 points in the search space made up of the potential 44 zones that could be opened or closed. The GA optimization stopped after 32 generations (448 iterations). Analysis showed that the best solutions were the ones that consisted of opening only formations ranked by added value. This can be explained by the field-production constraints, because excess liquid-processing capacity is available and it is always economically advantageous to open new zones if the oil production is sufficient to pay for the risked cost of the workover. This allowed a further reduction in the number of variables by excluding all possible closing operations, leaving only 29 variables to be optimized by the GA. The optimal scenario included 22 well interventions on 13 different wells to open new zones.
This article, written by JPT Technology Editor Chris Carpenter, contains highlights of paper SPE 167818, “Optimal Well-Workover Scheduling: Application of Intelligent-Well Control-Optimization Technology to Conventional Wells,” by Faraj Zarei, SPE, Khafiz Muradov, SPE, and David Davies, SPE, Heriot-Watt University, prepared for the 2014 SPE Intelligent Energy Conference and Exhibition, Utrecht, the Netherlands, 1–3 April. The paper has not been peer reviewed.