Miscible injectant (MI) has been used at Prudhoe Bay and its satellite fields for more than 30 years. This paper provides an overview of all enhanced-oil-recovery (EOR) projects in the Greater Prudhoe Bay (GPB) region and presents the process and methodology for MI allocation to these projects and to individual injection patterns. A new approach is used to determine the amount of MI allocated to each project on the basis of predicted marginal MI use per barrel of EOR oil.
Introduction
The MI-gas EOR process at Prudhoe Bay began in late 1982. In late 1986, the Central Gas Facility (CGF) began operation, enabling the first field-scale EOR project, the Prudhoe Bay Miscible Gas Project (PBMGP), to start in early 1987. Since then, the PBMGP has expanded to more than 170 injection patterns in the main field of Prudhoe Bay. Fig.
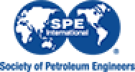