The quality or quantity of oilfield water is often a problem: There may be inadequate quantities, excessive quantities, or it is not the right kind of water for its intended use. Using less water in oilfield operations is commendable and promotes conservation. Recovering spent fracturing water and formation water for reuse as fracturing makeup water is even better because the practice is sustainable and applaudable.
The volume of spent fracturing fluid returning as flowback varies from basin to basin, from less than 15% in the Eagle Ford Shale to up to 40% in the Permian Basin and Bakken Shale. While the percentage of recovered fracturing water may not change, the overall volume recovered is on the rise (Boschee 2014). Formation water recovered during production operations is highest in the liquids-play basins, and is expected to continue to rise as more wells are completed and produced. Given the large volumes of produced water available, and the large volume of water used in fracturing applications, the highest and best use of produced water is as fracturing makeup water. Unfortunately, the quality of produced water generally requires specialized treatment to make it suitable for use in fracturing fluid, and the volumes of water to be treated are out-of-sync with the quantities required for fracturing.
Metcalf & Eddy (2003) wrote that “determining wastewater flowrates and constituent mass loadings are a fundamental step in initiating the conceptual process design of wastewater treatment facilities.” The authors add, “… the product of constituent concentration and flowrate is necessary to determine the capacity and operational characteristics of the treatment facilities… to ensure the treatment objectives are met.” In summation, reliable flow rate and water quality data are necessary to ensure the delivery of requisite water quality.
Fresh water used as fracturing makeup water typically has total dissolved solids (TDS) ranging from as low as 500 mg/L to 30,000 mg/L. For comparison, a 2% potassium chloride solution = 20,000 mg/L, and seawater = 30,000 mg/L. As a result, flowback may not only have a TDS as low as the fracturing water itself, but may contain up to 300,000 mg/L+ TDS, as spent fracturing and formation water combine.
Monitoring of the daily variation in TDS becomes more complex when the TDS not only increases from day to day in the flowback water, but low-TDS spikes also occur in the flowback water that otherwise has an upward-trending TDS. Add to that the not-so-unusual situation when the water to be treated comes from multiple wells and is offloaded into 500-bbl fracturing tanks, such that no two tanks have the same water quality. Taking into account each of these variables, reliable water quality data for operational consideration appears elusive.
The water quality data and the target water quality that might be needed as fracturing makeup water vary widely for a slickwater fluid vs. a zirconium crosslinked carboxymethyl hydroxypropyl guar (CMHPG) fluid. Generally, crosslinked fracturing fluids are more sensitive to certain attributes of water quality than the suite of polyacrylamides used in slickwater fluids.
With inconsistent inlet water quality being the rule rather than the exception, sizing and operational considerations of the treatment system components must vary accordingly to make the most economic sense. Not only will one size not fit all, but operational considerations must be connected to the treatment objectives. High in-situ boron content can be a problem for borate crosslinked fracturing fluids, but is not as great a problem for a low-pH zirconium crosslinked carboxymethyl cellulose.
Acquiring reliable data on untreated water, in-process water, and treated stored water is further complicated by the method of transport and operations that require treatment to occur in real time. Water stored in 80 fracturing tanks, instead of one 40,000-bbl aboveground storage tank (AST) is more challenging to maintain operationally and assure the consistent quality of treated water. The process of collecting and analyzing samples from 80 fracturing tanks requires significantly more time than evaluating four or five samples from a continuous-content storage unit, whether it is a pit or an AST.
Large-volume surface storage provides a means by which more heterogeneous untreated water can be homogenized before treatment. Although a more consistent treated water quality can be achieved by improving the consistency of the incoming raw water, treated water can and does vary. It changes with time and may change as treated water is drawn from the tank or pit, and freshly treated water is added. Changes in treated water alkalinity, pH, dissolved iron, oxidation-reduction potential, free available chlorine, dissolved oxygen, bacteria numbers, and biocide residuals may occur as the time between treatment and use is lengthened. Changes in just one of these attributes may have a profound effect on guar hydration or crosslinked fluid stability.
To treat the water and then forget about it is not adequate. Remember, the mission that Metcalf & Eddy emphasized was to “… ensure that the treatment objectives are met.”
Additionally, treatment flow rate has a direct relationship to volume. If a water treatment facility is expected to treat a certain volume per day, delivery of half of this volume per day means that the plant operation time will be proportionally reduced if the flow rate is kept as initially planned. Conversely, if the flow rate is reduced to extend the length of plant operations to the original plan, then mixing times, contact times, and retention times of the water in the treatment facility are doubled. These changes affect the water quality. Even in the cases resulting in improved water quality, this is a deviation from the treatment objective, and the treatment cost per barrel will likely increase substantially when the throughput is halved. If all costs are fixed, the treatment cost will double.
Whether stemming from sourcing, transportation, storage, treatment, or disposal, there are operational challenges attending every attribute of water reconditioning and recycling. With great strides continually being made in oilfield water treatment technologies, one of the biggest impediments to universal oilfield water reuse is water storage.
Storage issues are associated with the process at nearly every step and affect the economics of water reuse. Enough water can be accumulated, if there is adequate storage capacity; flow rates to fill pipelines or transports can be accommodated, if there is adequate storage; and treatment processes can be designed and implemented, if there is sufficient storage to feed the plant.
If untreated, water cannot be collected and stored in sufficient quantities to justify mobilization/demobilization and the daily treatment costs, thus treatment does not occur. If the volume of treated storage is insufficient for the intended application, for example, as fracturing makeup water, then the number of opportunities to treat for that application is reduced.
Large storage tanks are a means by which untreated water can be accumulated to help regulate the flow rate to a treatment facility, as well as to enhance smoothing of the variability of the untreated water quality to make treatment easier to manage. Large storage tanks are also a means by which treated water can accumulate as a homogeneous water source, which in turn provides for a more consistent fracturing fluid at the wellsite (Fig. 1).
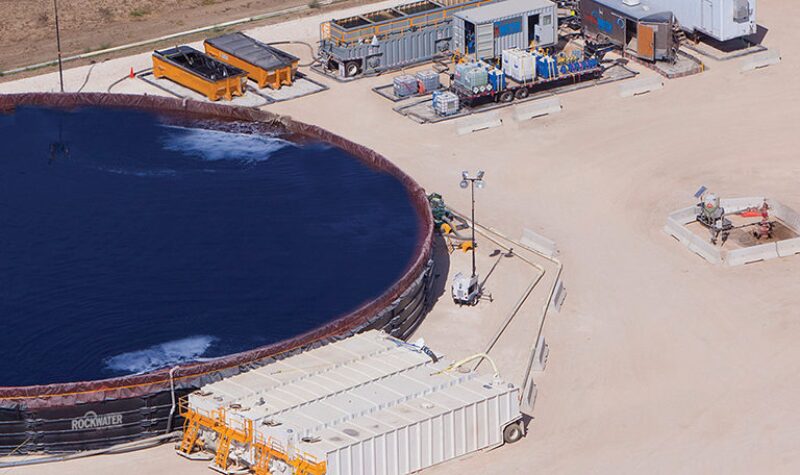
Fracturing tanks and in-ground pits have been the historical solutions to storage problems and continue to be used in many operations. More recent alternatives include the use of ASTs and closed-loop fluid handling systems. Fracturing tanks are fairly well-standardized at 500 bbl, and ASTs are available in multiple sizes, ranging from 4,000 bbl to 40,000 bbl. In-ground pits can be built to hold much more water than ASTs, but some states (Colorado, North Dakota, Oklahoma, Pennsylvania, Utah, and Wyoming) are moving away from in-ground impoundments. The smaller footprint required by ASTs is desired for some operations. For example, a 40,000-bbl AST covers about 20,000 ft2, whereas the same volume would require 80 fracturing tanks, covering about 36,000 ft2. The efficiency of water transfer operations may be improved by reducing the number of failure points with fewer connections and valves. The use of ASTs can reduce the truck traffic, (e.g., a 40,000-bbl AST requires from 4 to 12 tractor-trailers to hold the ancillary equipment required for setup vs. the 80 fracturing tanks requiring 80 tractor-trailers). A 40,000-bbl AST can be set up in from 8 to 10 hr. To set up an equivalent capacity of 80 fracturing tanks in 10 hr, it would require one fracturing tank to be placed every 7½ minutes.
In many cases, operators are using ASTs to store produced water because of the savings in cost for produced water recycling operations. Costs associated with transporting water are high and can be reduced in some regions by incorporating ASTs into a water management program (Fig. 2). Regulatory agencies are looking to the industry to provide improved technologies to reduce costs without compromising the health, safety, and environment of their constituencies. The Colorado Oil and Gas Conservation Commission (COGCC) and the Wyoming Oil and Gas Conservation Commission have been working to obtain approval for ASTs as storage tanks for untreated produced and treated produced water. Although both groups recognize the benefits of using ASTs, the facts do not outweigh their concerns about safety issues and potential cleanup, if there is a catastrophic failure of an AST holding produced water.
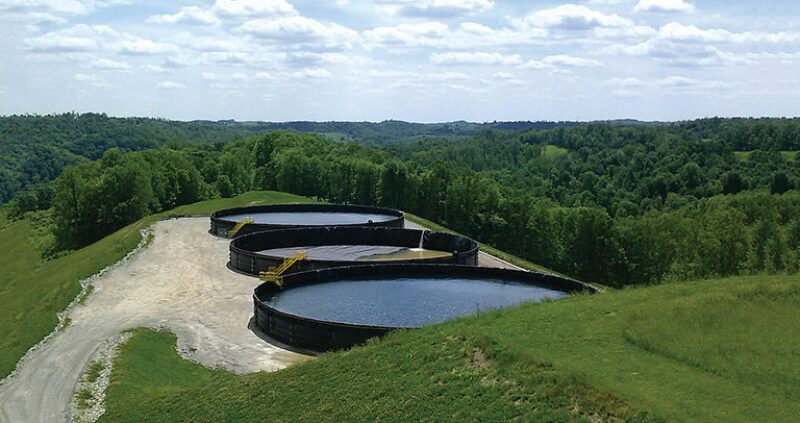
David Nightingale, executive vice president of water management at Rockwater Energy Solutions, in Houston, reported that his team has approached COGCC with a solution that showed how a liner failure could be isolated to reduce the risk of a catastrophic tank failure. Progress is being made in Colorado, Wyoming, and other states toward the use of ASTs for produced water storage. If the concept is approved and commercialized, it could change the landscape of oilfield water storage and improve the economics for water reuse. OGF
For Further Reading
Boschee, P. Produced and Flowback Water Recycling and Reuse: Economics, Limitations, and Technology. Oil and Gas Fac. 3 (1): 16-21.
Tchobanoglous, G., Burton, F.L., and Stensel, H.D. ed. 2003. Wastewater Engineering: Treatment and Reuse, 4th edition (Metcalf & Eddy). Boston, Massachusetts: McGraw-Hill.
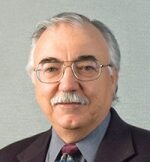
David Harry is a senior technology fellow at Rockwater Energy Solutions, where his main interest is recycling produced water for reuse as fracturing water. He has been a member of SPE since 1980, and can be reached at dharry@rockwaterenergy.com.