The significant effect of human errors on the operation of industrial processes calls for improved methodologies and tools to train both control-room and field operators. Common operator-training simulators (OTSs) meet almost exclusively the training needs of control-room operators. As for field operators, little has been carried out to improve their training level. The paper presents and discusses a solution for immersive training of industrial operators that allows experiencing the multifaceted scenarios of real-plant operations.
Introduction
Although in recent years some causes of industrial accidents have been mitigated, the overall number of accidents per year is growing. Human error is one of the main reasons for accidents in all industries, including the process industry. Process safety is still a relatively young and underdeveloped field, for both research and academia. In recent decades, the chemical industry has faced numerous accidents, from near misses to major disasters. Unfortunately, in that domain, compared with other fields such as aviation and medicine, there is a lesser focus on safety aspects. Contribution of human error to industrial accidents is reported to be in the range of 60 to 80%. A timely response to the incident/accident can reduce the escalation of the incident/accident itself and limit possible damage. Even an abnormal shutdown can result in significant financial losses to the industry. In addition, restart procedures are inherently hazardous and time consuming. Therefore, approaching industrial safety in terms of operator-performance improvement is one viable way to overcome, or at least reduce, the number and effect of accidents. The authors have designed a plant simulator (PS) as a training and performance-assessment tool implemented in a virtual environment.
Human Error and Industrial Operators
The authors are concerned with minimizing accidents and abnormal situations that may result from human errors by fostering the adoption of the PS paradigm. Situation awareness (SA) is the term used to describe, as a whole, the degree of understanding, the consciousness, and the decision-making capacity of people involved in specific activities within specific environments. The widely accepted three-level model of SA, consisting of perception, comprehension, and projection levels, is considered to be one of the best means of characterizing SA (this model is discussed in the complete paper).
The authors propose a specific definition of SA specifically tailored to industrial operators: Industrial situation awareness refers to the deep comprehension and understanding of the variables of process safety—plant structure, interconnections, layout, equipment characteristics, the nature of alarms, sequences of operations, short- and long-term risks, intervention sequences, cause-and-effect chains, and consequences of error.
The understanding of these issues gives one the capability to anticipate their effects, which will occur in the process/plant/equipment, as a consequence of either remote or in-the-field/manual actions.
PS
The proposed engineering solution consists of coupling a conventional OTS with an immersive virtual environment (IVE) that simulates the field in all its facets including spatial (or 3D) sound. Such a solution couples two distinct dynamic software tools: a real-time dynamic process simulator and a real-time dynamic accident simulator. The former simulates the dynamic evolution of the process inside the process units and the pipe network but is not able to describe what happens outside of the equipment. The latter receives information about the possible releases, outflows, emissions, and leakages from the process simulator and calculates in real time the accident evolution. The dynamic accident simulator also quantifies the effects of the accident on the surrounding equipment, and on the involved operators. To close the interaction loop, the process simulator receives as input data the quantities determined by the accident simulator (e.g., thermal fluxes) and determines their effect on the process variables accordingly. In short, the communication between the two simulators is bidirectional because they are mutually influential. The core benefit of this solution, which is also a breakthrough with respect to available training solutions, is that the data exchanged between the process simulator and the accident simulator allow for the following:
- Tracking the dynamic evolution of the process when an accident occurs
- Quantifying the possible effect on and damage to the structures and the equipment
- Quantifying the potential injuries that might be suffered by field operators in real life
The PS is presented as a suitable solution to educate and train operators and to assess their performance in carrying out both cognitive and manually related tasks. However, in attempting to identify a precedence hierarchy, the authors propose that the PS is better suited to test and enhance decision-making-related capabilities than to improve precision and accuracy of manual skills. This is certainly not because of inherent limitations of virtual reality (VR) itself but because of its state of development. Actually, when field operators were immersed in the PS, the concern was that operators would have found it easier to perform their activity in VR, thus making the PS risky to use for decision making because the results of experiments would have been optimistic instead of being conservative. However, when operators were asked to comment upon their feeling in coping with difficult tasks in the IVE, their reply was prompt and firm: Performing tasks in VR is much more difficult because the senses of smell and touch are not involved. (For a discussion of the characteristics and capabilities of VR and augmented-reality training, please see the complete paper.)
Methodology
Training. Another field in which operator training and assessment are of paramount importance is worker replacement, given the aging workforce at most industrial sites. A viable means of training new and unskilled crews is a common need in process industries. This is also a means to keep process knowledge inside the plant by minimizing the losses caused by the retirement of expert workers. These issues call for new means and new perspectives in training operators by use of reproducible and effective tools. The repeatability of training allows the achievement of a standardized approach to operator formation and the administration of well-accepted and validated procedures. For a discussion of the training section of the PS, please see the complete paper.
Performance Assessment. Training procedure and performance assessment are two distinct but interconnected features of the PS. If the operator assessment is not meant to test the real understanding and skill improvement achieved by the training session, training will not achieve its potential.
A common method of performance assessment is the use of the direct contribution of the trainer. According to the authors, human judgment can be flawed because it is based on subjective impressions that can vary significantly even within the same day. Such a biased judgment may vary as a function of both the trainers and the trainees. Thus, it would be highly desirable to ground operator assessment on a reliable, repeatable, and automatic tool that is completely neutral and avoids any subjectivity, a tool that meets the following prerequisites: consistency, quantitative assessment, repeatability, and neutrality. To satisfy the neutrality criterion, the assessment procedure should be automatic and should avoid questionnaires and consequent analysis and correction from examiners. Therefore, advanced tools for operator training call for an automatic procedure to assess the training degree of operators. This assessment should be implemented in a computer program capable not only of evaluating the performance of operators but also of registering, storing, and analyzing the actions taken and decisions made by the operators during the training session. In short, the assessment procedure should become an algorithm to be implemented in a computer program by means of an automatic procedure.
The authors designed and developed a software tool for the assessment of industrial operators. This tool measures and records in real time a set of process and accident variables, actions, decisions, and time intervals coming from the process and accident simulators and from the human/machine interface of the IVE, and it determines/evaluates the performance indicators and key performance indices required to quantify the training level and situation awareness of the operator. The additional benefit of this tool is the inherent flexibility that allows making the necessary modifications and adjustments according to the needs of the involved plant subsections.
The performance-assessment algorithm is capable of storing all the actions performed by the operator during the given scenario, evaluating the correctness of those actions, and weighing each action on the basis of a well-defined hierarchy and a relative weighing technique. Fig. 1 shows a schematic of the authors’ algorithm for an example briefly explained in the complete paper and for that of the catalyst-injection procedure of a polymerization process. The right-hand portion of the figure shows how the algorithm takes into account operator-performance indicators based on relevant human factors, key performance indicators (KPIs) based on process understanding and given situations, and the quantity/quality of help requested by the operator.
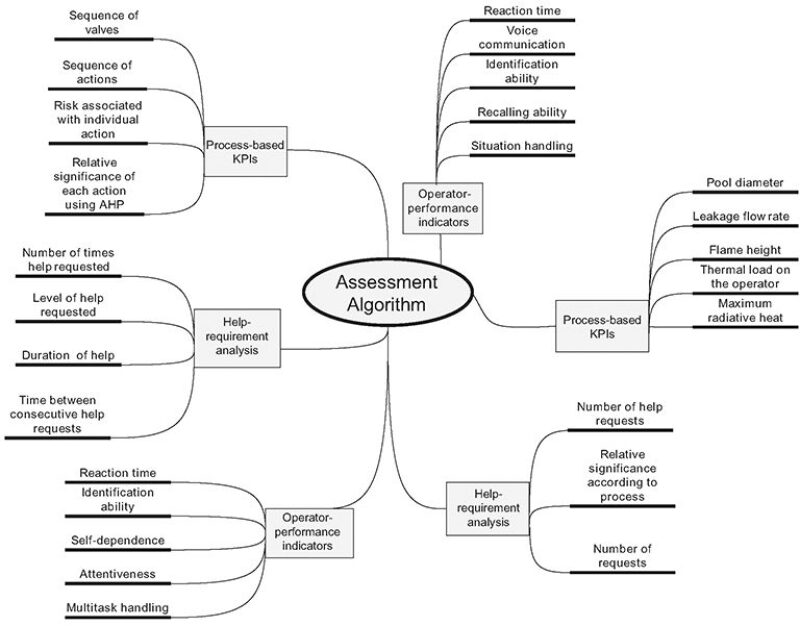
Application Cases of PS. As previously discussed, the coupling of a dynamic process simulator with a dynamic accident simulator allows description of the evolution of a large number of processes and plants in real time. The availability of an IVE and some human/machine interfaces to interact with the PS allows experimentation with immersive and realistic training sessions. For a detailed description of two application cases of the PS, please see the complete paper.
Conclusion
The PS has demonstrated efficiency in improving overall process safety by strengthening the understanding, situation awareness, responsiveness, and decision making of industrial operators. The assessment of the operators was presented and discussed through the introduction of an ad hoc software tool capable of producing automatic, reproducible, and unbiased evaluations of the performance of the trainee(s) on the basis of a multidimensional set of KPIs. A range of promising future research activities can be envisioned. The positive influence exerted by the PS on the operator’s performance in the case of a virtually simulated accident scenario was investigated and tested recently. By focusing on advances in areas such as training, knowledge improvement, situation awareness, and performance assessment (because this topic has been overlooked in the process industry), many abnormal situations and incidents or accidents can be prevented. Work is currently under way regarding the following: implementation of the PS for different applications, experiments with real-plant operators, the effect of training on SA, and possible improvement of the PS with the help of experimental studies and user feedback.
This article, written by JPT Technology Editor Chris Carpenter, contains highlights of paper SPE 164992, “A Plant Simulator To Enhance the Process Safety of Industrial Operators,” by Davide Manca, Simone Colombo, and Salman Nazir, Politecnico di Milano, prepared for the 2013 SPE European HSE Conference and Exhibition, London, 16–18 April. The paper has not been peer reviewed.