Emphasis on identifying more-efficient subsea boosting solutions has led to a number of initiatives in the industry. A new multiphase-pump technology has been developed that will expand the operation envelope for subsea boosting and create better opportunities for more-effective offshore-field development. A parallel, and equally important, advance has been the development of a new heavy-duty 6-MW subsea motor.
Introduction
In 2011, a decision was made to abandon twin-screw technology because of the low sand-handling resistance and limited differential-pressure generation with multiphase fluids that these pumps had demonstrated during in-house testing. Thus, a development project was initiated.
Multiphase-Pump-Development Project
For this development project, the main target was to increase pump performance in the following ways:
- From 4,000 to 6,000 rev/min
- From 3 to 6 MW
- From 500 to 1,000 actual m3/h
- From 50- to 150-bar differential pressure at 70% gas-volume fraction (GVF)
Reaching these targets would require design of a new motor to operate at higher speeds at twice the power.
Multiphase-Pump Technology
It was evident from recent experience that the pump design had to use the rotodynamic principle (dynamic energy transfer to the liquid) and not the positive-displacement principle.
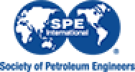