A critical step in proper design and optimization of any chemical-enhanced-oil-recovery (CEOR) process is appropriate and precise numerical simulations. Addition of chemical species to the material-balance equations, along with finer resolution requirements for CEOR simulations compared with waterfloods, often makes it impractical to run full-field CEOR simulations to the required accuracy. Sector models, by their definition, are naturally suited for modeling of pilots. This paper presents a case study for appropriate simulation of a CEOR pilot.
Introduction
Chemical flooding (polymer flooding, surfactant/polymer flooding, and alkali/surfactant/polymer flooding) has improved significantly over the past decade because of vast research efforts to find practical solutions to specific field applications, improvements in the manufacturing and synthesis of new chemicals, field trials, and implementations by the industry.
Because of the complexity of CEOR and the inherent uncertainties regarding success of a particular CEOR process, extensive evaluations are required before decisions about full-field implementation can be made.
Numerical simulations are critical in CEOR evaluation and provide a realistic performance estimate, assuming that the underlying Earth model is reliable and appropriately calibrated.
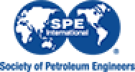