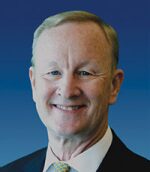
Quality is a measurement of excellence that is often difficult to quantify. Providers of quality products and services command premium prices. Brand names we associate with quality inspire positive thoughts. They are names we trust to deliver what we expect of them—safely, reliably, and with flawless performance.
Quality is a perceptual, conditional, and somewhat subjective attribute that is understood differently by different people. In business, engineering, and manufacturing, quality is fitness for purpose. It has a pragmatic interpretation as the superiority of something. That something may be a product or service. It may also be a process, personnel, management, or an entire enterprise—a brand.
While our industry strives to strengthen quality and reliability standards worldwide, the general public has a very negative perception of the industry’s performance. They do not think “quality” when they consider our performance or contributions to society.
Why do so many people feel so negatively about the industry responsible for powering the modern world? It provides jobs and improves living standards. For more than 7 billion people on our planet, every measure of quality of life, from gross domestic product per capita and infant mortality, to education levels and access to clean water, is correlated to the consumption of modern fuels, in particular oil and gas. There is no doubt that it is a vital resource that has improved people’s lives more than any other energy source.
A growing proportion of society now wants the lifestyle that oil and gas provide without our industry. Why? The short answer: trust. People do not trust oil companies. Perhaps they are cynical about gasoline prices. They do not trust what they perceive as an environmental polluter and source of greenhouse gases. They do not trust us to operate safely. The rise of vocal activist groups has exacerbated the situation, but we are not without blame. There have been industry incidents that caused loss of lives and damage to the environment. We did not always respond satisfactorily. Modern telecommunications, especially the Internet and social media, spread bad news universally, instantaneously, and continuously.
In my March column, I wrote about social license to operate, deemed to exist when a project—or an industry—has ongoing support and trust from the community. Gaining that support and trust requires that we not only meet, but exceed, society’s perceived basic requirements for safety, environmental stewardship, and social responsibility. We must deliver the affordable energy that society expects of us, and we must deliver it reliably, safely, and with flawless performance. Quality is not a luxury; it is essential.
The Role of Standards
The value of standards to quality has been apparent at least since the Industrial Revolution. Sir Joseph Whitworth, a Victorian mechanical engineer, campaigned for conformity and consistency in nuts and bolts in 1841. This made manufacturing safer, more efficient, and more economical in his native Britain and eventually, internationally. We in the oil and gas industry have applied similar logic to develop standards that have imparted benefits in areas ranging from the manufacture of tubular goods, fittings and flanges, to cost, performance, and reliability; global trade and international operations; health, safety, and environment (HSE); sustainability; intellectual property; global trade; competition and antitrust; knowledge sharing and transfer; the needs of specific groups in society; and the development of indigenous capacity and technology transfer to developing countries.
“If you control an industry’s standards, you control that industry lock, stock, and ledger,” wrote W. Edwards Deming in his book, Out of the Crisis. The crisis in this case was the economic struggle of the developed countries of North America and Western Europe in the late 1970s and early 1980s to keep pace in the face of stiff competition from Japan’s ability to produce high-quality goods at competitive cost. Ironically, Japan’s economic rise following World War II was founded on the ideas taught by Deming, an American engineer, statistician, professor, author, and management consultant.
Japan became the second-largest economy in the world by managing processes. Deming saw that the concepts of statistical control of processes could be applied not only to manufacturing processes, but also to the processes by which enterprises are led and managed.
“Costs go down and productivity goes up as improvement of quality is accomplished by better management of design, engineering, and testing, and by improvement of processes,” he said.
After a series of lectures in Japan in 1950, a number of Japanese manufacturers applied his techniques widely and experienced previously unheard-of levels of quality and productivity. The improved quality and lower cost created new international demand for Japanese products.
Business terms and concepts, such as continuous improvement, quality control, and total quality management, came about through Deming’s teachings. He warned that management’s failure to plan for the future would bring about loss of market, which brings about loss of jobs. He also counseled that management must be judged not only by the quarterly dividend, but also by innovative plans to stay in business, protect investment, ensure future dividends, and provide more jobs through improved products and services.
Donald E. Purcell, a recognized expert in globalization, international standardization, and strategic standards education initiatives, compared global standards to DNA as the basic building blocks for all technology and economic systems. They underpin expectations that platforms, systems, and equipment will be safe, reliable, and fit for purpose. If quality is the destination, standardization drives the improved performance, improved safety, improved reliability, and reduced costs needed to reach it.
Leading standards bodies for the oil and gas industry include the American Petroleum Institute (API), International Association of Oil & Gas Producers (IOGP), International Association of Drilling Contractors (IADC), and Bureau Veritas. Government agencies often promulgate regulations or voluntary programs that become de facto standards as well.
To enhance quality, it is critical that throughout the enterprise, employees at all levels embrace training and obtain all qualifications required to do their jobs properly, and we support these efforts with a broad, and expanding, range of training programs. During periods of low prices, training is often sacrificed. Inevitably, this risks quality in design, manufacturing, and implementation. In the same way Stop Work Orders are implemented when conditions are unsafe, everyone should be encouraged and empowered to take action and speak up if they see something that does not comply with appropriate standards, processes, and procedures. It is vital to participate in quality standards such as API Q2, the specification developed in 2010 to ensure that service providers implement quality controls at the facility level, based on identifying, assessing, and managing risk. Similarly, quality can be improved by applying ISO/TS 29001:2007: Quality System Requirements for the Petroleum, Petrochemical, and Natural Gas Industries, and industry tools such as Six Sigma. While standards and processes are important, it is ultimately the culture of an organization that will deliver quality.
Moving Forward
Quality has expanded from meeting basic manufacturing standards to managing risk at all levels of an organization and in all operating environments. We have learned from past incidents that moving the industry toward safer, more reliable operations requires that all aspects of quality programs be interrelated, interdependent, and consistent. Standards such as API Q2, which support procedural controls, guidelines, risk mitigation, and other aspects of quality, will help our industry reduce risk and ensure safe, trouble-free operations on the broadest scale possible.
For individual companies, quality is a prerequisite for staying in business, protecting return on investment, and providing more jobs. For our industry, it is a prerequisite for gaining and retaining our social license to operate.