Editor’s note: This is the first in a series of four reports with highlights from the Hydraulic Fracturing Test Site in the Permian Basin.
A chance to see what hydraulic fracturing really looks like in the Permian Basin drew overflow crowds for the first reports of what was learned at the Hydraulic Fracturing Test Site 1.
The featured attraction in the 13 technical papers presented over two mornings at the Unconventional Resources Technology Conference (URTeC) was 600 ft of rock fractured in late 2015 near wells in the upper and middle Wolfcamp. Those core samples spawned a mind-boggling array of observations about the rock, proppant, natural and hydraulic fractures, and how it all interacts.
In the more than 2 years since the samples were gathered, the sections of core have been meticulously analyzed by teams of experts. More than 700 fractures were categorized based on whether each one was created by nature, hydraulic force, or the stress of drilling the slant well. And the majority of the 400 stages pumped were studied using tracers and/or monitored using advanced diagnostics.
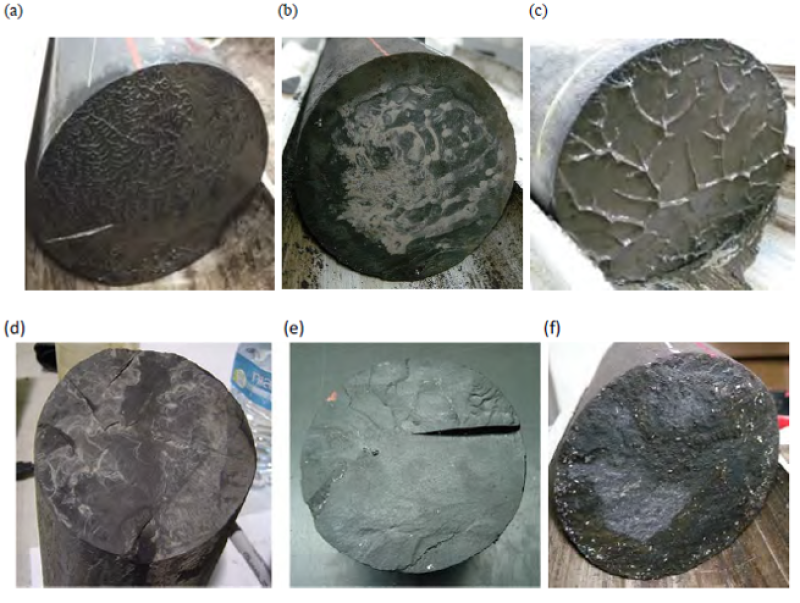
The density and distribution of the fractures were measured as the scientists worked to understand how natural and hydraulic fractures interact. The bits of sand, calcite, and drilling mud found in and around the rock was collected and sorted. Automated imaging and painstaking manual examinations were used to measure the size, shape, and translucence of each grain, in order to identify and quantify the grains.
The “incredible complexity” observed was “far beyond what current simulations can model and predict,” said Jordan Ciezobka, manager for research and development for the Gas Technology Institute (GTI), which managed the federal grant supporting test site 1 and is planning Hydraulic Fracturing Test Site 2 (URTeC 2937168).
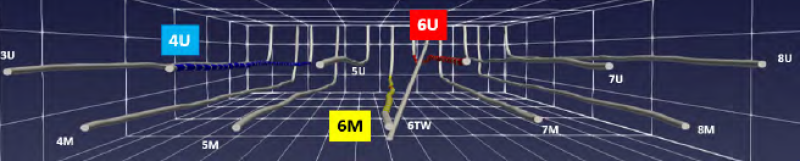
Ciezobka predicted that findings from the first Permian test site hosted by Laredo Petroleum in the Midland Basin, would be studied for years to come. The public-private partnership is just beginning to deliver the delayed reports of what it learned from the $25 million research project. Federal funding for the project requires the partnership to ultimately disclose its results, with data releases beginning later this year. The lag time rewards companies that supported the project with a long first look.
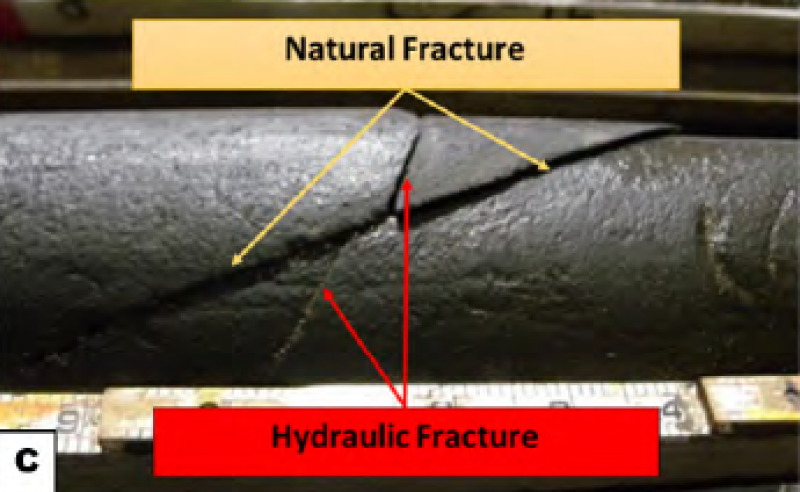
Cause and Effect?
Completion engineers in the room those two mornings likely left wanting more. With one exception, the talks avoided mentions of the ultimate measure of what works, production. What they did do was challenge widely held mental images of fracturing.
For one, fracture height is overrated. While microseismic testing indicated that fractures grew up about a 1,000 ft, the height of the propped fractures—the fractures most likely to produce oil and gas—was about 30 ft.
Proppant distribution was sporadic. While there were thick fractures full of sand inside, a paper describing fracturing (URTeC 2902624) said that only three of them were found among hundreds of propped fractures. And all of those were found in the upper Wolfcamp.
While the fractured lateral in the Middle Wolfcamp was further from the slant well—135 ft versus 90 ft from the nearest stage—the middle Wolfcamp core has a lot more proppant than the upper Wolfcamp core (URTeC 2902364).”
The sand grains collected tended to be extremely fine, many one-half to one-third the size of the grains that would just fit through a 100 mesh screen. Samples from the core tended to be mostly made up of those tiny particles. The three proppant packs were the exception, with a lot of bigger grains.
While crushing could turn large gains of sand into small ones, close examination showed that the tiny bits of sand were generally smooth and rounded, not the jagged shapes created by crushing. Nor did researchers find particles embedded in the fracture faces.
Fractures expose many different faces. Some are smooth, others rough. They did not appear to be the simple fractures growing out in opposite directions, known as bi-wings, which are widely assumed in modeling. After looking at hundreds of examples, Julia Gale, a senior research scientist for the Bureau of Economic Geology at the University of Texas at Austin, said, “we are not dealing with planar bi-wing things.”
Payoff for Pulsations
The papers also suggested the industry consider pumping jobs differently. In his paper, Ciezobka offered some production results of the sessions in a short report on a test of a fracturing method that used sharp variations in the pumping rate to increase production. “The rapid changes in the fluid flow, or a rate pulse, temporarily produce a pressure pulse of hundreds of thousands of pounds per square inch.”
A well fractured using the variable rate method delivered 20% gains on average over four other wells on the pad where a steady pump pressure was used, said Ciezobka, who is listed as the co-inventor on a patent held by GTI.
The variable rate well “clearly outperformed four adjacent wells with the same or higher proppant loading, in both initial production rate and cumulative production after 24 months,” according to the paper.
Meanwhile, on the URTeC exhibit floor, there was a booth promoting Hydraulic Fracture Test Site 2, which is being hosted by Shell and Anadarko Petroleum and will begin work later this year on Anadarko acreage in the Delaware basin.
The reservoir there is significantly different from the Midland Basin home of Test Site 1. Results from the first site “will establish the foundation for investigating EOR techniques, which we plan to investigate” in the second site, Ciezobka said. This second phase of the Delaware Basin project will inject natural gas into the wells in hopes of recovering an added 2-4% of the oil in place, according to the test site webpage.
Proppant Packed or Not
Large fractures packed full of sand do exist. In the cored rock from the fracturing test site there were fractures from 0.5-1 cm thick full of proppant. They were fine examples of the large breaks in the rock propped open with sand.
In 600 ft of core, researchers found three big fractures packed with sand among hundreds of propped fractures, most of which were smaller. The breaks examined held from 1.3 pounds of particles to a fraction of an ounce of sand, drilling mud, and bits of calcite and pyrite from the formation, said Debotyam Maity, a senior engineer at GTI, whose presentation covered the analysis of the sludge of sand and other particles found around the depressurized core (URTeC 2902364).
What they observed resisted orderly categorization. Maity’s paper also noted that “the proppant seems to show sudden jumps and drops with some core samples showing no proppant and some showing a lot.” Differences were ascribed to “geology/fracture or stress related variations.” Hydraulic fracturing interacted with natural fractures in many ways.
“They are certainly reactivating natural fractures” and there is proppant down in there, said Sara Elliott, a research scientist associate from the Bureau of Economic Geology for the University of Texas. The paper (URTeC 2902629) covered the painstaking job of extracting and measuring particles found in fractures. To begin with, researchers had to develop a method allow them to get all of what was there, including particles that escaped the depressurized core, clean it, sort it and record where samples were collected.
It was “one of first attempts at physical collecting and quantifying injected proppant from a parted fracture break from a stimulated reservoir,” said Elliott.
The total volume of proppant found in middle Wolfcamp fractures was a lot higher than in the upper Wolfcamp, where researchers observed five times more fractures including natural fractures. “The upper Wolfcamp hydraulic fracture should show a lot more interaction with natural fractures, providing more opportunities for the proppant to screen out locally due to a reduction of fluid momentum/carrying capacity of the fracturing fluid,” Maity wrote.
Other concentrations of proppant were found at fractures in seams between layers of rock with contrasting properties. “We find that almost all of the high proppant concentration zones appear close to carbonate bed boundaries or where there is a significant change in stress/brittleness,” Maity said. These included complex fractures at the intersection of beds of carbonate with contrasting rock properties.
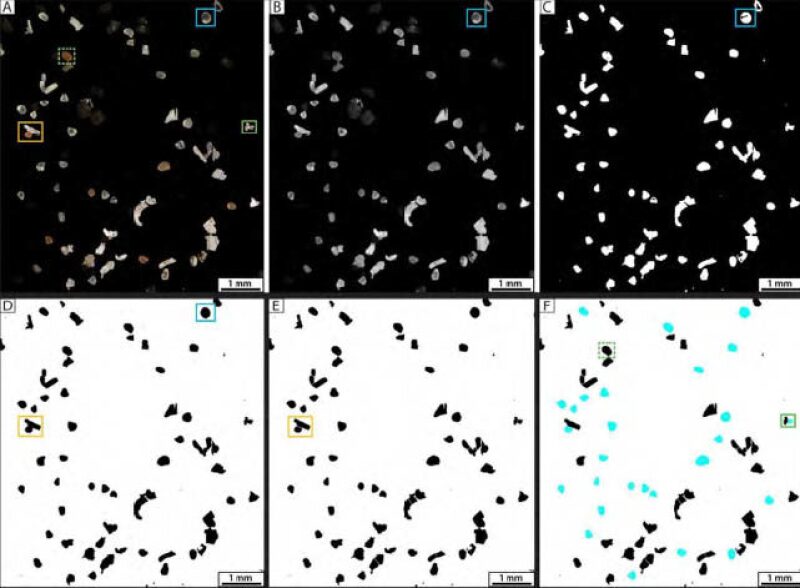