Drilling, completion, production, and general surveillance are all areas that benefit greatly from remote real-time analysis. However, several challenges to remote services exist, including communications issues, fear of job loss, and working outside one’s comfort zone. What is considered an important development goal for a business might be regarded as a threat to an individual, leading to reduced development within remote services.
Remote-Operations Business Model
A remote-operations business model removes geographic location and physical distance in all phases of oilfield-service delivery. It reduces the cost of delivering services, increases geographic reach, and improves safety. Remote operations, in essence, are real-time workflows that integrate personnel at rigsites and at assembly and maintenance and overhaul (AMO) facilities; at remote operations centers; or at real-time operational centers (RTOCs) anywhere in the world.
Remote operations are the acquisition of sensor data from rigsite equipment and instruments, and the transmission and processing of those data from remote locations. Monitoring, alarm, or advisory services are delivered in real time with global delivery models, increasing the capability to move work from the point of service to another location, where it can be performed more safely, more quickly, and at a lower cost.
Infrastructure, while critical, is only an enabler. The true sources of efficiency and competitive advantage come from the organizational redeployment of the workforce and the re-engineering of workflows. Providing on-demand expertise enables service providers to deploy new technology faster and deliver high-end services in areas with few local qualified resources. Customers also benefit from bundled services, which require the integration of different disciplines and expertise that may be in short supply.
The Digital Oil Field
Improved connectivity through radio link, fiber optics, and satellite systems has opened a new world of opportunities for operation optimization. Real-time operations monitoring occurs from any office, accessing data streams through Web portals. New downhole tools and software have been developed on the basis of these new abilities, and new service levels have resulted, leading to new and interesting jobs, improved well placement, high service quality, and reduced nonproductive time (NPT).
Some of the most important contributions to drilling analysis include real-time services as a function of new downhole tool technology, improved telemetry, and fast access to near-real-time downhole data; oilfield standardization for data aggregation and transfer (WITS/ WITSML/PRODML); and new engineering software.
In the early stages, most real-time monitoring was used only by field personnel. However, as real-time data were displayed in the service-provider were conducted remotely in newly developed remote operations centers or in both parties’ offices. Field personnel were remanned, and field job functions were integrated through specialized cross-training programs.
A 24/7 operations cycle was implemented for key services in the operations centers; specific field functions that were conducted in front of a PC were physically reallocated from the field to the remote center. The model provided the means of reducing the number of field personnel significantly [especially for drilling services, where measurement-while-drilling (MWD)/logging-while-drilling (LWD) and surface-logging services could be conducted remotely].
The idea behind the model was to reduce personnel at the rigsite and to transfer the job tasks to a remote operations center. Fig. 1 shows the change in personnel needed in the traditional work model compared with multiple rigs with remote personnel, and the reduction in personnel that need to be transported to any rigsite. The increased support level is also illustrated, and the expertise level within the support organization is also enhanced.
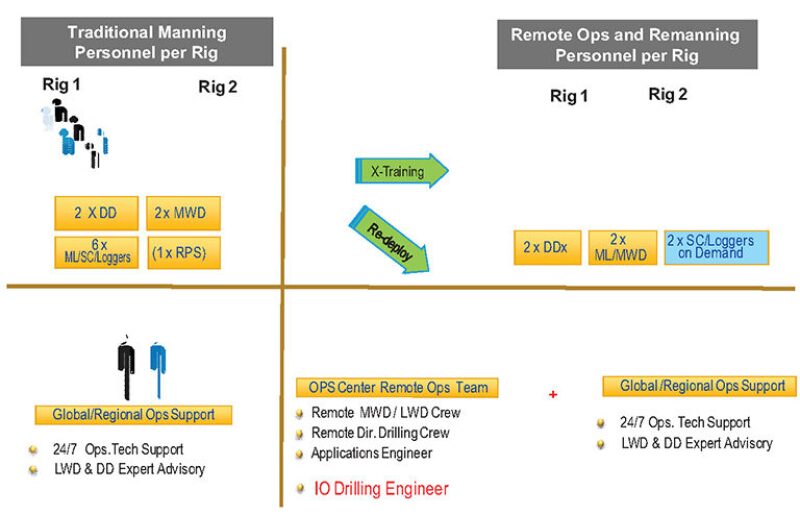
Remote Real-Time Analysis
The connectivity, real-time data display, and reliable communication flow of fully equipped remote operations centers and RTOCs set the stage for the future of remote services. Important areas exist in which oil companies and service providers can improve their operations significantly, such as prejob planning and drilling execution.
Achieving superior drilling performance requires more than merely selecting the appropriate drill bit and bottomhole assembly (BHA); recommendations often relate to all aspects of the drilling operation. Drill-bit design, BHA setup, and the analysis of borehole geometry vs. formation zones, hole cleaning vs. pressure, and fluid and vibration patterns all form the drilling environment.
The drilling-optimization adviser has a wide range of knowledge about drilling practices, but without the correct rock-property analysis, that knowledge is insignificant. Measurements must be accurate and timely to ensure that adequate changes are made as necessary. Verifying measurements is the first step in automated drilling—the input parameters must be correct.
Remote automated drilling-advisory service, which recognizes potential drilling problems before they occur, is an additional tool for the drilling adviser/ engineer. The adviser/engineer provides their best operational advice on the basis of continual real-time surveillance and interpretation of all available data in addition to the automated decision support from the case-based reasoning software. This integrated solution, built on the premise that similar problems have similar solutions, delivers constant surveillance, interpretation, and advice within a collaborative environment to reduce uncertainty, minimize NPT, increase safety, and enhance efficiency.
Case-based reasoning software automatically identifies events and trends. When the system identifies a potential problem, it is brought to the attention of the drilling adviser/engineer. The best course of action is determined and necessary personnel are notified with recommendations for correction. Fig. 2 depicts the case-based reasoning workflow.
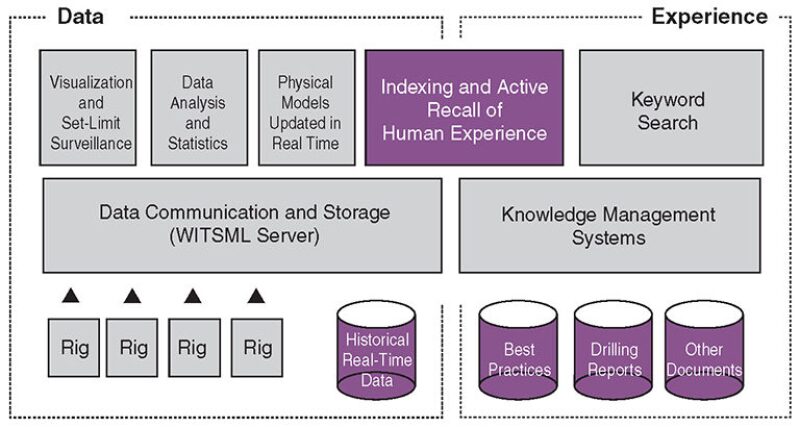
In addition to the remote drilling-advisory services, there are a number of other tasks that can be conducted remotely. In this context, it is important to mention real-time pressure or equivalent-circulating-density management, pore-pressure prediction, and wellbore stability as tasks that can be performed continually from a remote operations center or clients’ RTOCs. Collecting and analyzing borehole cuttings and evaluating possible cavings are tasks that must be performed at the wellsite. Proper use of photography and scales enables the caving evaluation to be performed remotely, thus delivering a more advanced scan of the caving.
Real-time data are also extremely important in the planning phase for reviewing, improving, developing, and following up on field-specific best drilling practices. All available data, including real-time drilling-fluid parameters, are used in this type of analysis, predicting situations at any well depth with current parameters. Advice is given to help avoid stuck pipes, lost circulation, and hole collapse, and to stay within predetermined operational envelopes.
Continuous operation monitoring is required during tripping in and out, where running speeds are estimated on the basis of analysis of available real-time and historical data. The reaction of adjusting the mud-weight window up or down is dependent on the mode of failure interpreted from 1D geomechanical analysis. By integrating drilling experiences, the geomechanical model can be calibrated, providing an optimized geomechanical analysis.
Reservoir navigation is another concern that has moved from the field to remote operations centers without problems. The reservoir-navigation supervisor primarily works from the client’s office; reservoir-navigation engineers perform continuous drilling-progress and LWD-log-response analysis, updating the Earth model while drilling. When there are recurring differences between the premodeled expected physical properties of the reservoir and the actual observed measurements, the objective is to ensure that changes made are kept to a minimum to maintain consistency with other data.
Prejob modeling is required to provide road maps for what can be expected during section drilling, where real-time data and subsequent analysis dictate the well path to be drilled. Discrepancies between a prejob Earth model and projections being made on the basis of real-time data can immediately halt the drilling process; a thorough analysis of the real-time data and the model determines future actions. In some instances, the model is altered, and drilling commences. In other cases, the discrepancy is accepted or leads to sidetracking, and new well profiles must be drilled. The process is labor intensive and requires a clear and streamlined communications plan.
In production, significant achievements have been made in optimizing electrical submersible pumps (ESPs), such as improving pump life cycles and detecting scaling and other problems. Production is controlled remotely from an operations center, where thousands of pumps are monitored and operation sequences are analyzed simultaneously on the basis of real-time data. The automatic analytics determine the ESP’s condition, and appropriate action is taken. Automatic chemical injection of, for example, scale inhibitors is also conducted remotely. The automated analytics and alarms provided by the software enable repair and workover field crews to be established in a controlled atmosphere.
The latest addition to the remote-operations domain is the situational-awareness and operational-visualization system, which triggers specific workflows to be followed. The system integrates data, visual feeds, and audio channels, providing operations traceability. The system engages all operations participants, providing a comprehensive view for coordinating actions and responses. It also contains recall and replay functions of all information sources for after-action review. All acquired data are stored in a black box at the rigsite in case of an unexpected event, and are also displayed in real time in a continuously manned RTOC or operations center. Fig. 3 shows one possible remote-operations-center layout. Visual information from the wellsite is shown through cameras, and sound is transmitted through open-communication channels, avoiding phone calls as much as possible. The circle is completed in the operational environment, giving feedback to the real-time operations crew.
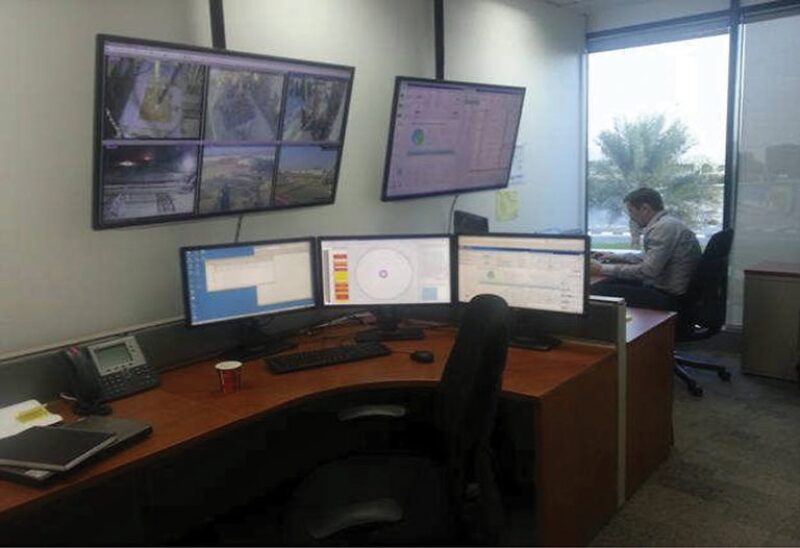
Benefits and Challenges
For more than a decade, remote operations have been implemented in the oil and gas industry, with significant progress made through workflow and process design, enabling remote monitoring, execution, and control.
Drilling contractors have swiftly implemented automation, with manual work being replaced by machines and smart software. In the service industry, remote subject-matter experts have replaced field engineers. These initiatives have contributed significantly to reducing operational cost and have improved service quality and reduced NPT.
The challenge, however, is the human capital—the individual reaction to continuous change and where jobs are being moved. Human nature resists change and prefers the known, and therefore change processes are sometimes impeded by a workforce comfortable with the status quo. Key personnel that would be the preferred candidates for remote positions often prefer rotation cycles in the field. Therefore, intense management focus is required to cause the workforce to commit to the newly developed operations model. Communication and workforce inclusion in all stages of the pre-engineering process are key factors to success.
This article, written by JPT Technology Editor Chris Carpenter, contains highlights of paper IPTC 16999, “Remote Real-Time Analysis—A Game Changer for Remote Operations Centers,” by Erland Saeverhagen, Arve Thorsen, Jan Ove Dagestad, Nic Spanovic, and Kate Cannon, SPE, Baker Hughes, prepared for the 2013 International Petroleum Technology Conference, Beijing, 26–28 March. The paper has not been peer reviewed.