Digitally enabled collaboration between operators and service companies is driving significant improvements in process safety in the upstream oil and gas industry. However, drilling contractors generally have been considered only the owners of the systems that generate part of the surface drilling data and, as such, have not been engaged in the development of real-time analytics tools. The role of a real-time operations center (RTOC) with a drilling contractor is itself a new factor. This paper explains how an ultradeepwater drilling contractor is applying real-time analytics and machine learning to leverage its RTOC to improve process safety and performance.
Introduction
The increasing availability of digital drilling data and the emergence of reliable communication between offshore rigs and well operators’ offices enabled a proliferation of RTOCs in the 2000s, spawning a collaborative environment between well operators and service companies that enabled enhanced support and optimized use of expert resources to improve process safety and operational efficiency.
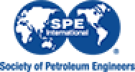