The steam-assisted-gravity-drainage (SAGD) process along with an efficient steam-use process can reduce production costs and increase the oil-recovery rate. The use of real-time downhole monitoring is an effective approach to achieve this optimization. The use of downhole distributed-temperature sensing (DTS) and array-temperature sensing by use of fiber-optic technology has led to instrumented wells that enable data access on a real-time basis, leading to better control of operations, and to optimizing the steam process. Also, fiber-optic technology enables measuring pressure and temperature over the same fiber and in close proximity along the wellbore.
Introduction
At reservoir conditions, bitumen is essentially immobile, and recovery of these highly viscous fluids requires viscosity reduction, often by applying heat. The SAGD process is an effective recovery method for heavy oil and bitumen. The SAGD process typically uses two parallel horizontal wells that normally are separated vertically by approximately 5 m. The top well is the steam injector, and the bottom well is the producer. As steam is injected, a steam chamber will grow around and above the injection well. Despite its effectiveness, the SAGD process has many economic risks including a high initial investment for constructing the surface facilities and uncertainties related to product prices.
Displacement efficiency is a critical factor in controlling oil recovery from the steam chamber, and, although increased volumetric sweep is beneficial, the chamber-growth rate greatly affects the rate at which the displacement efficiency increases in the steam chamber. Increasing the volume of the steam chamber too quickly may decrease the effectiveness of the SAGD process.
Uniform distribution of steam along the entire length of the wellbore could lead to a more-uniform steam-chamber growth, making the entire length of the well productive and developing optimum performance of a SAGD well pair. Traditionally, the SAGD injection well is completed with dual injection strings (one injection string ending at the heel and the other injection string ending at the toe) and the production well is completed with a slotted liner, as shown in Fig. 1. Steam distribution along the well is governed by different factors. The most important factors include pressure in the injector and producer wells, fluid-flow regime, fluid velocity, wellbore trajectory, and heat loss along the length of the wellbore. A new well/injector configuration is proposed that includes steam diverters, inflow-control devices, centralizers, fiber-optic pressure gauges, a fiber-optic DTS system, and control lines. An intermediate configuration could be the traditional dual string with the addition of temperature and pressure measurement by use of fiber-optic technology to help control the shape of the steam chamber.
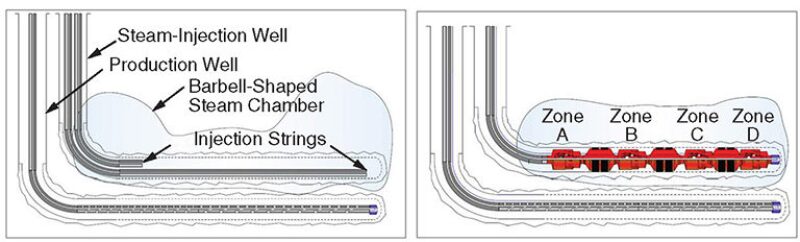
Fiber-Optic Array-Temperature Measurement
The temperature-measurement technique is based on fiber-Bragg-grating (FBG) technology in which discrete Bragg-point sensors are distributed along a single optical fiber. These FBG sensors and the associated fiber, housed in the downhole capillary string, reflect a wavelength of light that shifts in response to variations in temperature or strain.
A broadband source illuminates the multiple FBG sensors, and the reflected light wave is received at the source where the temperature and pressure readings are calculated and stored. The system provides continuous temperature measurements at definable points along the length of the fiber-optic cable. The FBG-array platform allows integration of cable-health and diagnostic sensors along the same sensing fiber, which enables remote assessment of system health and aging.
Thermal Analysis
In the SAGD process, pressure and temperature monitoring provides a reference to the heat-transfer process in the reservoir and a reference to the steam displacement into the reservoir along the completion. Initially, only thermocouples were used to determine the top of the steam chamber; however, thermocouple spacing can limit the ability to determine the steam-rise rate. Fig. 2 shows the resolution of the thermal profiling in the 1170- to 1290-m section near the toe of a well and with only two thermocouples. The increase in temperature is not captured as it is with the fiber-optic system. The number of temperature-data points along the horizontal axis (i.e., spatial resolution) is critical to fully understand the dynamics inside the wellbore during the shut-in periods. Fiber-optic DTS provides much higher resolution than traditional thermocouples, enabling better analysis of the temperature-falloff data. It is important to mention that an understanding of the dynamics inside the wellbore is necessary during the shut-in periods and during any period of the SAGD operation. The use of a limited number of thermocouples restricts the understanding of the wellbore, and, thus, having 1-m resolution may be a safe option; but the fiber-optic-array method with 40 temperature-sensing points and one pressure-measurement point, providing 15- to 25-m spacing, presents an alternative solution with sufficient resolution.
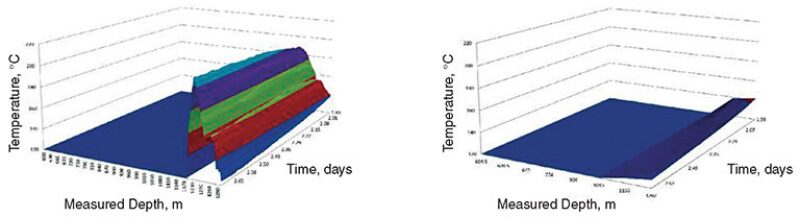
Having a sufficient number of accurate, stable temperature- and pressure-measurement points in both the injector and the producer is essential to optimize SAGD-production systems. A key control variable in SAGD operations is the subcool, which is the temperature difference between the injected steam and the produced fluid. In a horizontal section of 600- to 1000-m length and with heterogeneous geology, the temperature profile is very important and must be measured and controlled to allow a proper subcool value between 15 and 30°C.
Inflow Calculation
It is important to understand the flow distributions of bitumen and water along the horizontal intervals of the reservoir. In a horizontal well, the inflow along the wellbore can vary because the rock characteristics can change along the wellbore, and, in the case of SAGD wells, temperature changes must be included in the process because of the effects on the total contribution. Temperature profiling is extremely important in the case of unconventional reservoirs such as shale, bitumen, and heavy oil where an effective reservoir is generated. In the case of bitumen and heavy oil, steam injection generates the contributing volume of the reservoir and maintains it over time. The contributing-volume size can be modified or adjusted if the correct data are processed at the right time, and correct actions are taken.
Fluid flow is a function of permeability, pressure drop, and viscosity (which is a direct function of the temperature and depends directly on the steam-injection rate). Temperature changes in the producer well can be controlled and adjusted by regulating the injection rate at the heel and the toe of the injector well to maintain a constant temperature profile. The temperature profile in the producing well depends on the steam-injection pressure and rate and on the oil-production rate. If the production rate is too low, a condensate-water level will increase and limit the heat transfer, resulting in less production. If the production rate is too high, steam breakout can result. To avoid these situations, the subcool-effect term is introduced and careful real-time control of this parameter is necessary.
The inflow model used here for horizontal wells is a modified version of the Joshi model that takes into account the changes of temperature and viscosity over time. The composite-inflow model uses 40 inflows that are divided to take the heterogeneity of the wellbore into account. The inflow for this type of well is more dynamic than for a traditional well, and the changes can be controlled by the rate and pressure of the injected steam, which require real-time monitoring.
Production
The three most common artificial-lift systems used in SAGD wells are electrical submersible pumps, progressing-cavity pumps, and gas lift. Although not part of this study, software can be used to optimize these production systems. Real-time monitoring can aid analysis for these systems. Real-time monitoring and alarming capabilities, coupled with integrated analytical and reporting tools, can achieve optimum well performance.
Conclusions
Because of the heterogeneity of the reservoir, a sufficient number of data measurements is required. Acquiring data from 40 thermal points, and at least one pressure-measurement point at the toe of the well, will help define a more-accurate composite-inflow model that varies with temperature. The system output is compatible with various SAGD systems, to enable monitoring and analysis by use of these real-time downhole data. Software enables this data management by exception, with different types of alarms and analysis modules to optimize the system on a real-time basis.
This article, written by Senior Technology Editor Dennis Denney, contains highlights of paper SPE 157923, “Real-Time Optimization of SAGD Wells,” by Luis E. Gonzalez, SPE, Peter Ficocelli, SPE, and Tad Bostick, SPE, Weatherford, prepared for the 2012 SPE Heavy Oil Conference Canada, Calgary, 12–14 June. The paper has not been peer reviewed.