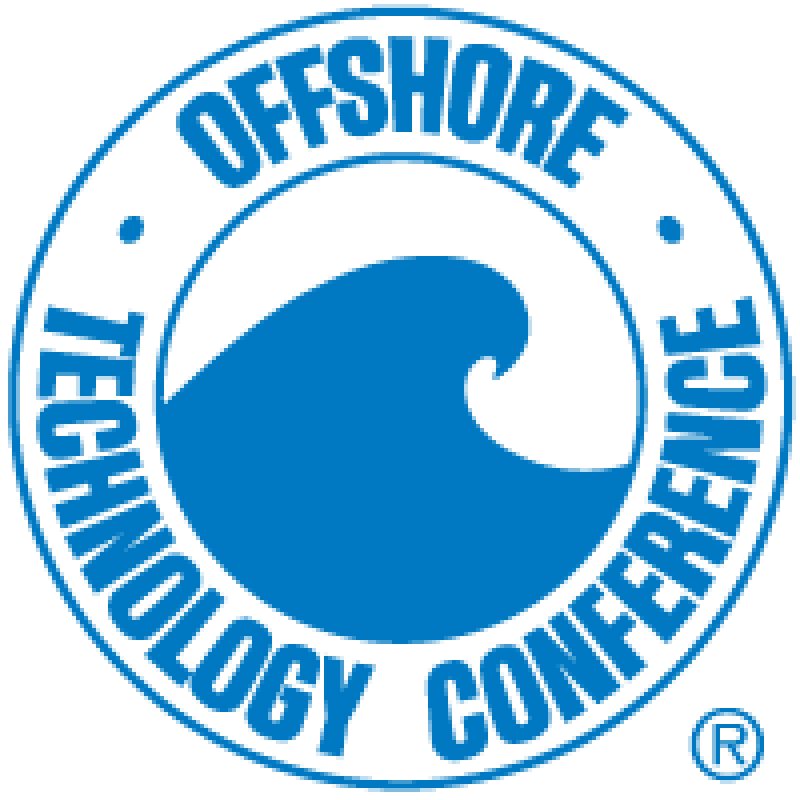
Complexity is the central challenge of executing deepwater major capital projects, and the industry must find ways to reduce it for future projects to be viable, Chevron’s General Manager of Facilities Engineering Mick Kraly told a luncheon audience Tuesday at the Offshore Technology Conference in Houston. “Major Capital Projects Yesterday, Today, and Tomorrow: Is There a Need for Change?” was his topic.
Kraly said that companies must prove capable of finding, developing, and maintaining the competencies needed to carry out these projects and overcoming various performance gaps that have become increasingly evident. The industry must commit to increasing standardization across multiple projects, come together to address major technological challenges, and take full advantage of joint industry projects (JIPs) and the work of industry committees, he said.
Deepwater projects are inherently complex because of the increased reservoir recovery necessary to justify their economics. “We’ve got to have the ability to do further technology deployments to be successful,” Kraly said. Projects involve seafloor pumps, may also use in-well and electrical submersible pumps, and can incorporate waterflooding, which may be followed by enhanced oil recovery. “Each of these adds a layer of complexity,” he said.
Performance Gaps
Kraly presented a major consultant’s analysis of a large number of deepwater installations that showed widespread performance gaps in the industry’s project executions in the areas of meeting schedules, keeping within budgeted costs, and attaining targeted startup production. Only 18% of projects met both their schedule and cost goals, and a mere 8% met schedule, cost, and production attainment goals.
“If we don’t change, obviously in this low-price environment many projects are not going to be viable,” Kraly said.
At the same time, the necessary technical capabilities for these major projects are not always available to the extent desired. “All across that value chain of the project, we’re finding that we lack the depth of really having the competencies that we need,” Kraly said.
Chevron is addressing these needs internally with a focus on three areas:
- Preservation of project materials from purchase through final installation.
- Shifting the management of single-point inspections to an in-house responsibility and redefining the meaning and scope of these inspections.
- Quality management of engineering, procurement, and construction (EPC) contractors, expanding the level of it, and shifting it upward in the project cycle to bring more of it into the front-end engineering phase.
Standardization
Increasing the industry standardization of future projects is critical to their successful execution, Kraly said. “We try to simplify processes, workflow processes as well as engineering standards as well as executional standards,” he said. “We are challenging ourselves to stop doing this on an ad-hoc basis and actually implement these as part of our overall work stream. We have to take advantage of standardization in the ability to deliver things more repeatedly as well as more cost-effectively.”
Kraly also said that companies should leverage the work of JIPs and industry committees and that these are good avenues for elevating the discussion of standardization.
He recommended that companies across the upstream industry and regulators work together to enable the industry to move forward, and cited high-pressure/high-temperature (HP/HT) technology as an area that could benefit especially from such initiative.
‘Let’s Do This Together’
Recent discoveries in the Gulf of Mexico present downhole environments that will exceed the current 15,000-psi limits of wellheads, casing lines, and blowout preventers, and new HP/HT technologies must be developed and qualified to operate in 20,000-psi settings. International oil companies, EPC contractors, suppliers, and regulators are sounding the same message for this need.
“Let’s do this together,” Kraly said. “Let’s just make sure that we have these controls and standards and qualifications. Let’s make sure that the 20,000-psi opportunities are done in the best way.”
During a question period after his talk, Kraly said that Chevron is re-establishing a central engineering organization that will do all project work before the front-end engineering and design (FEED) phase.
“We see the need to have very solid, very good engineering documents going into the FEED,” Kraly said. Analysis has shown that installation and technology problems on a number of projects “have been rooted in actions going into the FEED,” he said.
Joel Parshall is the Features Editor for the Journal of Petroleum Technology.