Human error can be defined as an action or behavior that unintentionally results in an undesirable or unwanted condition or leads a task or system outside of acceptable limits or established standards. An error-free workplace is not possible. The average worker will make anywhere from 10 to 12 errors per hour. These errors, however, will not necessarily lead to an injury or quality defect and are considered to be part of normal operations.
Employee Experience vs.
×
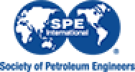
Continue Reading with SPE Membership
SPE Members: Please sign in at the top of the page for access to this member-exclusive content. If you are not a member and you find JPT content valuable, we encourage you to become a part of the SPE member community to gain full access.