Advances in drilling and reaming with casing or liners (DwC, DwL, RwC, and RwL) are yielding unprecedented capabilities in well design and construction. These innovations reflect the continued evolution of a versatile system of technologies that has grown in two decades from a tool to improve efficiency and mitigate drilling hazards to a system enabling advanced wellbore construction.
Advancing the Technology
Modern DwC involves a suite of capabilities for drilling and reaming with either the primary string or liner. The concept has a long history. In the 1950s, the production sections of wells were drilled using tubing that was ultimately cemented in the hole without recovering the bit. Slimhole coring technology from the mining industry was tried in the 1990s in an effort to improve exploration efficiency.
Over the next decade, DwC technology and versatility grew. In addition to eliminating nonproductive time (NPT) tripping drillpipe out of the hole and the associated wellbore problems, DwC emerged as an effective means of proactively mitigating wellbore instability, lost circulation, and pressure transition issues.
The introduction of an integrated casing drive system in the early 2000s enabled the safe and efficient rotation, reciprocation, and circulation of the casing, which led to other benefits such as ensuring high-integrity cementing and zonal isolation. Advances in casing bit design began to resolve the inherent challenge of durability vs. subsequent drillout.
With growing wellbore complexity and challenges, DwC technology evolved from discrete hazard mitigation to a larger capability well plan optimization. Greater capability advanced the end objective from solving an immediate problem to constructing a high-integrity wellbore—as designed and to the total depth (TD). The latest innovations continue this wellbore construction advance on multiple fronts.
Strengthening the Wellbore
Plastering has been one of the more intriguing and elusive benefits of DwC techniques. The so-called smear effect crushes cuttings against the formation to form a barrier to circulation losses and enhance wellbore stability. But achieving it on a regular, predictable basis has been difficult. Plastering occurs in some wells but not in others.
A greater understanding of this process is providing the means to produce and accelerate wellbore plastering reliably, thus substantially strengthening the wellbore. The first field application of the process is planned. Research has shown that the key to plastering is the concurrence of the formation’s permeability and fracture matrix with a wide range of particle sizes in the annulus. If these factors do not correspond, plastering does not occur.
The main variables are the range of particle sizes and the speed of achieving an optimal size distribution. While grinding in the casing wellbore annulus can reduce cuttings to a wide range of size over time, the delay in achieving the appropriate distribution allows time for problems to develop. Early achievement of the optimal particle distribution is critical to success.
In addition, and critical to the calculation, this optimal size distribution may never occur if left to natural processes. There are many factors that influence plaster formation, and they create a complex equation for success. Mud type—water, oil, or synthetic—along with rock type and bit selection can all affect particle formation and distribution. The size of the annulus between the hole and the casing contributes many variables to the equation, including annular velocity and the time that cuttings are exposed to annular grinding.
Achieving a much higher probability of plastering and accelerating the process have been essential to establishing an effective plastering capability. Based on research into particle size, creation, and distribution, proprietary software has been developed to create an optimal blend of application-specific wellbore strengthening materials (Fig. 1). The blend of materials is added to the drilling fluid before penetrating the lost circulation zone.
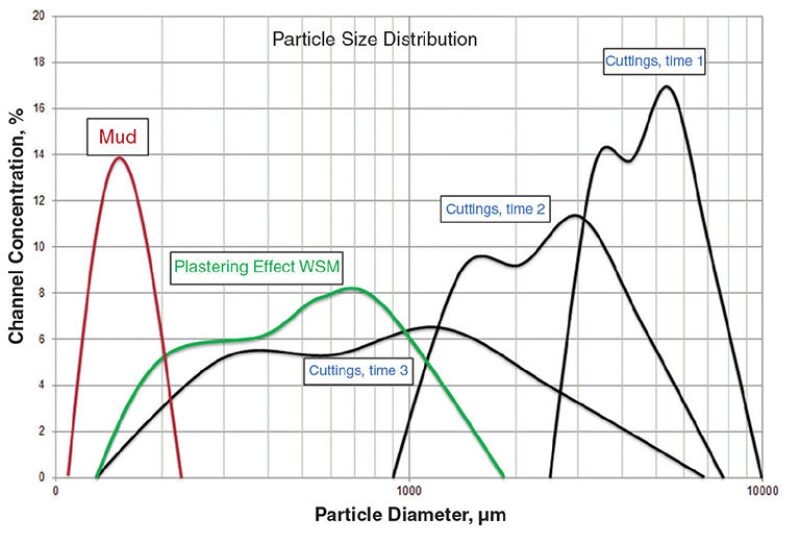
The theoretical strengthening mechanism has three levels. First, the casing rotation on the wellbore wall repairs the imperfections of the borehole such as microcracks and small fissures, therefore helping restore the original integrity. This process is thought to be responsible for the strengthening benefits observed while drilling impermeable shales, in which conventional wellbore strengthening methods are not applicable. Second, in lost circulation scenarios caused by fracture propagation, the available particle size distribution from the added blend and ground cuttings are plastered into the induced fractures, helping to isolate the pressure to the tip and arrest the fracture growth. The propped fractures increase the tangential stress around the wellbore wall. Third, continuous rotation of the casing heals the fractures, and the plastered filter cake reduces the permeability at the compacted near-wellbore zone, providing an effective stress in the wellbore vicinity.
Wellbore strengthening increases the fracture gradient, enabling a wider mud weight window to reduce the loss of circulation and the potential for well control events, and can eliminate the need for a contingency string to mitigate a problem zone.
Combining Forces
Advances in DwL wellbore construction include its integration with managed pressure drilling (MPD) capabilities for wellbore pressure management. The union is another reminder that complex well construction challenges require more than a simple technology fix.
MPD controls wellbore pressure through management of annular backpressure in a closed loop drilling system. The effect is dynamic control of equivalent circulating density (ECD) in contrast to conventional systems that depend on changes in mud weight.
MPD is commonly performed with drillpipe. This necessitates tripping the pipe and running casing, which can result in surge and swab pressures and prolonged wellbore exposure. DwL provides the solution to tripping, and when combined with MPD provides a highly effective means of drilling and casing problem wells. Lower density fluids can be used with MPD, allowing the ECD to maintain sufficient overbalance to contain pressured reservoirs while mitigating wellbore instability in unstable shale formations. Furthermore, MPD allows the application of surface backpressure while making connections, which compensates for the loss of annular friction pressure during drilling.
In slot recovery operations offshore South America, the use of the integrated capabilities is planned for drilling and running casing through weaker sand and shale sequences at hole angles requiring mud weights exceeding the anticipated fracture gradient. Impetus for the program came from sidetrack problems with the original wells that resulted in 281 days of NPT.
A collaborative engineering process using the operator’s basis of design led to the combination of MPD and RwL to drill and case the difficult 12½-in. and 9½-in. hole sections. Once drilled, the application of surface backpressure during liner-running operations is planned for maintaining wellbore stability and safely reaming the 9⅝-in. and 7⅝-in. drilling liners to TD.
Solving the Bit Conundrum
Drilling with casing bits continues to be a key enabling technology for DwC applications. The bit challenge is inherent because the bit must be tough enough to drill the rock and yet be drilled out with the same type of bit that drills the next section, without the process damaging the new bit. Risk of damaging the drillout polycrystalline diamond compact (PDC) bit has been a primary constraint in increasing the durability of drillable bits.
Recent design innovations are achieving much faster drillout times with PDC casing bits designed for drilling in medium to medium-hard formations with unconfined compressive strengths of up to 15,000 psi. The new bits have an average drillout time of less than 20 minutes, compared with steel alloy casing bit drillout times of 125 minutes.
The Weatherford Defyer DPA casing bit provides a cutting structure comparable to conventional PDC bits with an average of 80% less steel in the drillout path, compared with full steel alloy casing bits. As a result, drillout times are significantly reduced. In a study of multiple bit runs, the casing bit was drilled and the hole section reached TD in a single run. Cutters on the PDC drillout bits remained in good condition.
In the Asia Pacific region, the new bit design was a key to drilling a well with 13⅜-in. casing that is the world’s deepest DwC application. The benefits included high rates of penetration and fast drillout time, while meeting the operator’s directional objective. The bit drilled a total 593 m of medium soft claystone interbedded with sandstone at 43 m/h to 46 m/h. A zone of about 45 m of hard limestone stringers was drilled at a rate of 6 m/h to 36 m/h.
The section’s TD was reached in 16 hours with a hole inclination of 0.24°. Drillout of the DPA bit took approximately 8 minutes using a 12¼-in., 6-blade, 19-mm cutter steel-bodied PDC bit (Fig. 2). The bit was later graded at 2-3-BT-A-X-3-WT-TD after drilling 1188 m to TD.
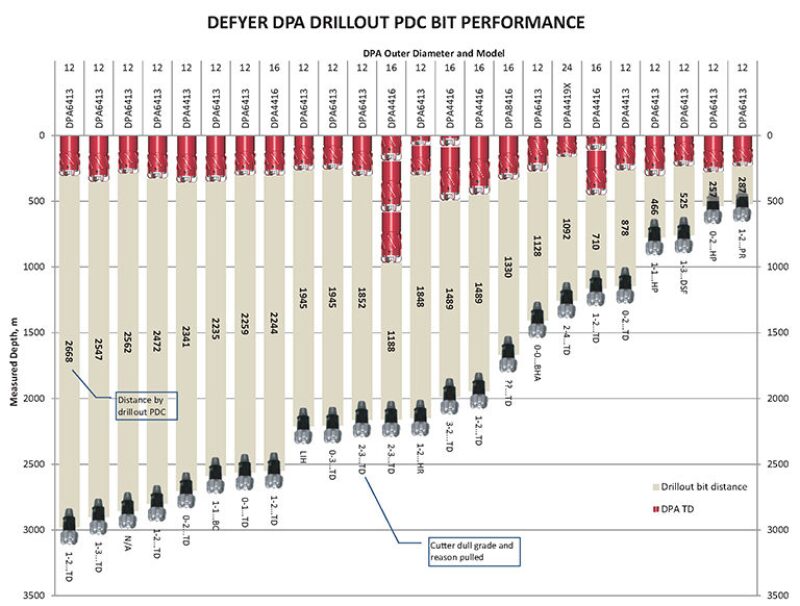
Subsea Solution
In deepwater applications, DwC technology developed specifically for NPT reduction, reduced mud costs, and hazard mitigation is in the final design stages following successful testing. The technology features a retractable shoe joint that allows the high-pressure wellhead housing to be landed safely once the surface section is drilled.
Drilling with casing on wells with surface blowout preventers requires drilling the section to TD with the casing and casing hanger separate. Once on the bottom, the string is pulled back and a joint or two of pipe is laid down. Then a joint with the casing hanger is picked up, made up to the string, run, and cemented. In a subsea application, this would require the casing string to be tripped back to the surface to install the high-pressure wellhead housing, which would negate a key reason for DwC.
The SeaLance DwC system provides a means of drilling to TD, telescoping the string to land the high-pressure wellhead housing, and cementing in a single trip. The system eliminates tripping of the conventional bottomhole assembly and the requirement to pump weighted mud after drilling the hole section. The reduced annulus allows much lower flow rates for transporting cuttings and a significant reduction in mud volumes required to drill the hole section. DwC hazard mitigation benefits address problems including collapsed holes, fluid losses, shallow gas, and rubble zones. In addition, the system facilitates batch setting of wells using a less expensive multipurpose vessel or smaller rig, with a larger rig following to drill each well to TD.
Game-Changing Options
Continued advances across a full scope of DwC, DwL, RwC, and RwL technologies are answering complex wellbore challenges with new methods focused on the larger objectives of wellbore construction. Integrated in the well’s basis of design, these systems provide game-changing options for how wells are planned and constructed.