This paper presents the development of Sapinhoá field, covering the fast-track transition and decision-making process, from appraisal to conceptual and basic engineering of the Sapinhoá pilot project and on to its subsequent execution, highlighting the challenges, lessons learned, and results. Even though, at the time, several uncertainties about developing presalt areas were present, a fast-track strategy was chosen. A pilot project was seen as a means to provide valuable information for the remaining development of Sapinhoá and other fields in the presalt cluster.
Introduction
The Sapinhoá field is in Block BM-S-9 at the central portion of the Santos Basin (Fig. 1). The water depth is approximately 2140 m, and reservoir depth lies between 5000 and 6000 m, with salt-layer thickness up to 2 m.
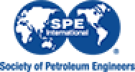