After nearly 4 decades of work, Björn Paulsson has created a system using fiber optic seismic receivers so sensitive that he said it will be able to create much more accurate, detailed seismic images with features too small to be seen now, detect the sounds of fracturing never heard before, and stand up to temperatures exceeding 300°C and pressures of more than 30,000 psi.
But he needs USD 12 million from companies interested in using it in their wells, which is nearly equal to the financial backing he has received from the United States Department of Energy (DOE) to get to this stage.
Paulsson and the DOE’s Research Partnership to Secure Energy for America (RPSEA) were organizing a meeting in late May seeking the support of oil companies to develop a full-scale version of the system he describes as “more than an order of magnitude better than what we can do now. This is not a small step up, it is a huge step.”
The plan is to build a system that can place 200 fiber optic seismic sensors, each of which has three channels (3C) allowing it to detect the direction of incoming signals along three axes, deep in a 30,000-ft deep well. There would be a receiver every 50 ft covered by a metal housing capable of standing up to the extreme pressures found in wells in the ultradeepwater US Gulf of Mexico, and clamped tightly onto a drilling pipe that can deliver it to the end of a long horizontal well.
Winning industry support will require convincing experts in geophysical exploration that it is possible to get a lot more out of seismic imaging, and microseismic monitoring, using high-capacity, high-fidelity receivers located deep in a well.
Fiber optic lines have been used as digital acoustic sensors for seismic testing, but the experience has been limited. One of the few companies to do so is Silixa, which markets distributed fiber optic sensing to the energy industry. It has a handful of customers and about 3 years of field work using fiber to record seismic signals.
“When we looked at it first, it was a collaboration with Chevron and Statoil. The initial hope was when we look at the data, maybe we can see some seismic signal,” said Mahmoud Farhadiroushan, chief executive officer of Silixa. “When we did it, we got a clear seismic signal from (surface to) the fiber optic lines in the wellbore, and could see it shot by shot.”
Since then, the companies have shown that it is possible to do seismic imaging using data recorded across multiple wellbores and working on ways to track the movement of water and oil in places such as Saudi Arabia, where conditions make seismic testing using geophones on the surface difficult to useless.
“When people saw this 3 years ago, this was new. I think it has just been a mind shift,” Farhadiroushan said. “We are now seeing commercial projects moving forward making use of this new technology for seismic and other applications.”
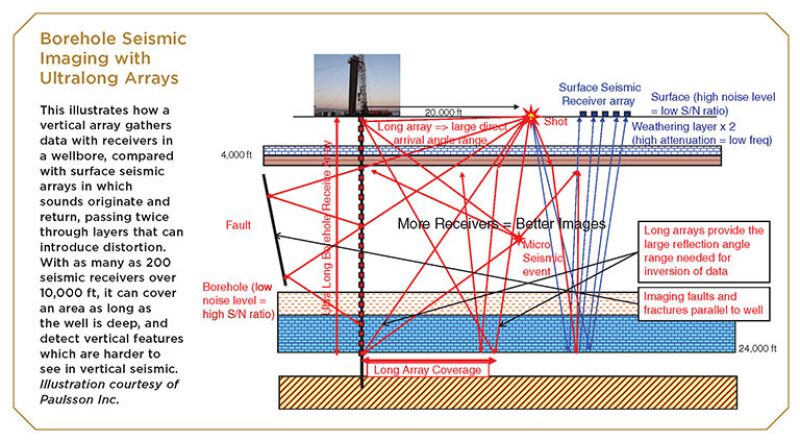
The users are still limited to major international operators with large commitments to technology development—for example, BP has worked with both Paulsson and Silixa—and while the two approaches rely on digital optical sensing, the companies are seeking different roles in exploration and production (E&P).
Silixa is using seismic data gathering to add value to permanent installations that also use optical sensing to track temperatures, pressures, and fluid flows in a producing well. Paulsson has developed a tool designed to create extraordinarily detailed and accurate images that will guide costly developments by better defining reservoirs and geological features within them.
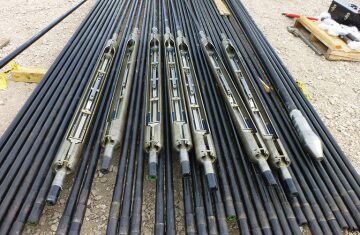
The combination of the fiber used as a distributed acoustic sensor that records seismic signals every meter, and seismic sensors able to pick up a far higher range of sounds, and identify the incoming direction, will help create a more accurate velocity model. This model is a precise measure of the time it takes for sound to travel through to various depths in a formation, which is critical when estimating the depth of features shown in a seismic image.
System Hardware
- Up to 200 sensor pods holding fiber optic seismic sensors spaced every 50 ft up to 10,000 ft.
- Fiber optic cable is protected by ¼-in. tubing.
- The 15 fiber optic lines are protected by ¼ in tubing.
- All seismic components are protected from pressure by Inconel steel and assembled in advance.
- Drillpipe (S135 steel) is used to deploy the sensors into the wellbore.
- Each seismic sensor is capable of separating the direction of incoming sound waves along three axes.
- The fiber used in the fiber optic seismic system (80 µm with polyimide coating) is capable of operating at 350°C.
- Laser light sent from the surface. No electric power required in the well.
- The system weighs 5.4 lb/ft. Tapered drill pipe, which is thicker and stronger higher in the well, will be used to support the weight of the entire system.
The technical specifications set Paulsson’s system apart, but its future depends on answering the economic questions: Can this unique data-gathering device create images that will reward users with greater production, better drilling locations, and more accurate production estimates to avoid costly mistakes when designing production facilities?
The appeal of borehole seismic has been the same since Paulsson started working in the late 1970s: Signals travel from the surface to receivers in the ground without the distortion added when echoes travel back to the surface. This creates clearer images by avoiding materials that add noise, such as the thick layers of salt or unconsolidated sands found above some of the largest oil fields. The angle of arrival of the signals gives it a better look at vertical features, such as faults dividing reservoirs, which range from hard to impossible to see on surface seismic.
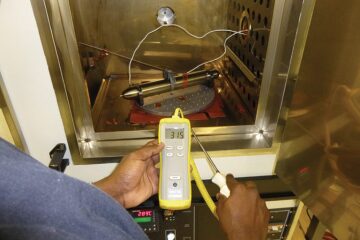
The biggest problem in putting standard seismic receivers in a hole is the heat, which limits how deep the electronic devices can be used. Paulsson’s system can be used in the ultradeepwater US Gulf of Mexico, such as the Lower Tertiary. There the potential reserves are huge, but the extreme cost of drilling wells puts a premium on accurate reservoir models, and the harsh conditions mean traditional coil geophones are not an option.
In-well seismic testing looks costly, until it is compared with well costs exceeding USD 100 million, or the risk of building a production platform costing more than USD 1 billion that is designed to process far more than the field produces.
Inaccurate reservoir estimates are a costly problem facing E&P companies. A 2008 study funded by RPSEA found that all the reservoir estimates used to develop projects in the Gulf of Mexico were wrong based on the actual production, said Bill Head, ultradeepwater project manager at RPSEA, who is advising Paulsson on the project.
“We have some companies that are good at it, but the majority of companies are way off. They drill too many wells or did not drill enough,” Head said. “If we can decrease the cloud of uncertainty, we are doing great. This tool will help do that. It will help us understand reservoirs better.”
Paulsson expects the borehole seismic studies will be used to produce better reservoir models to guide development plans.
“You drill a discovery well and there is plenty of time before development drilling begins to do in-well seismic to gather better information about the reservoir,” Paulsson said. The combination of fiber optic lines and 3C fiber sensors can create a more accurate velocity model. The data gathered in the well can be used to reprocess previous seismic to ensure more accurate reservoir models, which will be used by E&P companies to make big decisions, such as picking drilling locations.
Paulsson’s OptiSeis system’s potential is based, in large part, on its ability to gather more data over a far wider range of wavelengths using accelerometers built using fiber optics rather than standard geophones. Fiber has the added advantage of being able to function in ultradeep wells where the temperatures are too high for electronic devices.
While the fiber system is capable of detecting wavelengths from less than 1 Hz to 6,000 Hz in a laboratory, well conditions limit that range. The highest wavelength recorded in a well was 2,000 Hz, Paulsson said. The lower limit is an indication of what sounds make it to the wellbore. The steel, cement, and the rock in the formation attenuate the sound, with losses in the higher wavelengths. When doing seismic testing, it is further reduced by the highest pitch of the sound generated for testing, which tops out at around 1,200 Hz.
That is four times the highest possible wavelength for the geophones and hydrophones in use, but more than 10 times the range typically used for seismic imaging. Even at the bottom end of that range, this could allow four times the resolution, allowing small details to be imaged, Head said.
The ability to record a broader range of wavelengths and pick up sounds too faint to be detected by other seismic receivers also could allow it to greatly increase what can be observed during microseismic imaging onshore, Head said.
It is so sensitive that, in one test, the geophone made by Paulsson detected the sounds of men walking on a nearby highway as well as passing trucks.
Smaller Details
Companies backing in-well seismic are betting that the industry needs to image finer details as it pursues smaller, more complex reservoirs offshore, and to find ways to observe the details that make fracturing and enhanced oil recovery effective onshore.
“If someone is just looking for a feature the size of a mountaintop, you do not need much resolution,” Head said. “If you are looking for a 30-ft thick reservoir and want to know what the fluid properties are, this will be the tool.”
After many years of pushing the idea of gathering more seismic data in wells, Head knows this will not be an easy thing to sell. In-well seismic was invented in the 1930s, but the technique known as vertical seismic profiling (VSP) was not used as a tool by the industry until the late 1960s and early 1970s, he said.
“In the 1980s, lots of companies shot VSP because everybody did it,” Head said. In the 1990s, companies realized they were spending a lot of money on it and making little use of the data. Most were only using it for check shots to help build velocity models, so they quit using it. But he said, “In the last 8 or 9 years, it has been coming back.”
Vertical seismic arrays pick up sound waves coming from above, below, and from the side. Gathering sound data in the ground avoids the distortion added as the sound waves return to the surface, which is a major problem when the reservoir is below the thick layers of salt common off Brazil and in the Gulf of Mexico.
The data has long been gathered with geophones or hydrophones, but the devices require electrical power and can only tolerate so much heat.
The practical limit for traditional coil geophones is from 150°C to 175°C. Heat is not an issue for fiber optics, which require no electric power source—the sensing is done by pulses of laser light sent from the surface. In lab tests, it has performed reliably at temperatures exceeding 300°C, which is well above the maximum temperature in the deepest offshore wells, Paulsson said.
The hardware used to insert the system must be heavy duty. Drillpipe is used rather than wireline because it can push the string into a lateral well and it stretches less. A hydraulic clamping system allows the string on fiber optic cables and seismic sensors in a strong steel (Inconel) pressure protection shell to be put together in advance without using connectors.
“System connections are what lead to failures in the field,” Paulsson said. “We are welding the parts and hard-wiring the fiber.”
A Broader Range
From a data-gathering point of view, this is a quantum leap in volume, which presents a challenge for those doing computer processing that Paulsson likened to the leap from 2D seismic imaging to 3D.
“No one has had to deal with these frequencies before,” Head said. “High resolution is hard on a single channel. Within each of the 3C geophones are three directional receivers, generating an enormous amount of data.”
Where fiber shines is its sensitivity, allowing it to pick up faint sounds over a wide range of frequencies. But at the moment, it is limited by the ability of current software and computer systems used to process the data and to create images.
Higher frequencies come with shorter wavelengths, which could be used to create images with much better spatial resolution showing of finer features. To do so will require processing data sets with an enormous number of data points to find the ones that will yield a usable image, Head said. In contrast, he said, the most common receivers used commercially top out at around 120 Hz, and the top signal generally used for surface seismic is around 60 Hz.
Getting past that upper limit will require more efficient processing. “The software is not designed to handle this sort of data computation,” Head said. Paulsson is working on developing new software to make use of the data gathered by his OptiSeis system, starting with top-end bandwidths around 200 Hz, and rising from there.
“It is going to require a different algorithm. One that is computationally able to handle 16 times the data, with tens of million more data points. For an elaborate survey, it will be much more than tens of millions,” Head said. The systems will also pick up more noise and multiples—duplicate signals that need to be weeded out—on an enormous scale.
The ability to pick up faint sounds could change microseismic analysis, where a common concern is that most of the likely events caused by using hydraulic pressure to fracture rock are not observed.
In a test in a field in Alvin, Texas, three of the fiber optic sensors offered detailed data over a broad bandwidth of the sound created by an explosion of 0.65 g of TNT in a 300-ft deep hole, located 1,200 ft away from the observation well that was more than 900 ft deep.
When measured on the Richter scale, the fiber optic sensors can hear sounds from 2 to 3 magnitudes fainter than the best available microseismic receivers, Paulsson said.
“We can see enormously more,” Head said. “You can see the beginning of a fracture and detect induced seismicity—the sound of the rock accommodating seismic shifts.”
Paulsson’s plan is to build the system in 12 months and then begin using it in the wells of supporting companies that each get one well test per million dollars of support. Head said, “We are just beginning to realize what we can do.”
Fiber Optics Offer Seismic on Demand
A fiber optic cable in a well can be described as a long string of microphones. “You can listen to acoustic signals at every meter on the fiber,” said Mahmoud Farhadiroushan, chief executive officer of Silixa, a company in the United Kingdom selling in-well monitoring systems using fiber optic cable. “If you have 10,000 meters of fiber, you can have 10,000 microphones.”
When compared with a standard geophone used to record the echoes created during seismic testing, a fiber optic line has its limits. Unlike a standard geophone, it is not built to detect the direction of incoming sound waves. But he points out that a permanent installation can offer “seismic on demand,” periodic imaging at a relatively low cost from an installed receiver system without the cost and production interruptions associated with installing a temporary receiver array.
While the data gathered at any single meter on the way is not as rich as what can be gathered using a geophone, there are so many of them. “Meter-by-meter processing offers a high depth of information” from multiple shots coming from a moving source to create seismic images, Farhadiroushan said. While a single strand of fiber cannot detect what direction the sound is coming from, he said a test using fibers in multiple wells can simulate what a geophone can do in that regard.
A Society of Economic Geologists (SEG) paper on a single well test of a BP well on the North Slope of Alaska reported the fiber in the well “successfully recorded seismic signals. The amplitude, frequency, and phase of the digital acoustic seismic (fiber optic) data are very similar to geophone data in the shallow well.” But the report delivered to the SEG annual meeting in 2013 added that the “noise level is about 2 orders of magnitude higher than that of geophone data,” and it suggested the problem could be solved by stacking a number of data sets or using a stronger sound source.
A ¼-in. tube full of fibers attached to the casing, or the production tubing, can measure flows of liquids and gases, and also track pressures and temperatures in the well. Silixa is working to build up a body of evidence to show that an investment in fiber installation and monitoring can deliver multiple streams of data that can be used to improve well performance.
Acoustic monitoring is a recent addition to what fiber can measure. The company uses untreated standard fiber optic cable. At each meter, a small amount of the light is scattered back to beginning of the line where it is analyzed by a device known as an interrogator unit. The device can tell where each reflection comes from by precisely measuring the difference between the departure and arrival times. The strain on the fiber alters the properties of the backscattered light. Changes in the light’s amplitude, frequency, and phase reflect external forces on the fiber, such as sound waves.
It is early days for the technique. Silixa has done “30 to 40 jobs” installing fiber, with much of it used for temperature and pressure sensing. Farhadiroushan said other companies are working in this field. One of them, OptaSense, has worked for several years with Shell on borehole seismic development.
He said he sees a lot of potential for growth because fiber can be used in so many ways, adding: “There are a lot of ways to process the data to extract more information.”