The simplest way to measure return on investment for an offshore water treatment system is to determine whether using the system actually reduces the risk of paying a fine for violating water pollution laws. This has typically been done through laboratory tests—required by regulators—on periodically collected samples of treated water.
But increasingly, water testing systems are being installed on production platforms offering constant updates of the effectiveness of the water treatment systems. The argument for them is that what flows out of oil fields changes constantly, with surges and slugs dense with hydrocarbons. An unnoticed surge or slug can cause a sharp increase in the oil level in the treated water that is disposed overboard. Without quick adjustments, these excursions can create a telltale sheen around a platform, which can lead to trouble.
“There is the dreaded sheen,” said Sandy Rintoul, executive vice president of Wilks Enterprise, which was recently acquired by Spectro. “If there is a sheen on the water, watch out. The helicopters will see you pretty soon.”
Wilks sells tabletop devices, used on platforms for periodic processed water quality checks that have been used for decades. It now faces multiple competitors in a niche where new testing methods are for sale. If done properly, those tests can indicate how a platform will fare when tested for regulatory compliance.
“They (platform crews) typically use it at least once a day. You see some do it four times a day. If something is going on with the system and there is an issue, they could grab samples every hour,” said Rintoul.
A small but growing number of platforms have installed constant monitoring systems. The future of this option will depend on convincing operators that there is a favorable return on investment in monitoring systems that cost many times more than periodic checks.
There was keen interest at the annual meeting of the Produced Water Society, which spent one day at its 3-day annual Produced Water Seminar, held 14–16 January in Galveston, Texas, for presentations and debate on the value and effectiveness of continuous monitoring and its future.
At the meeting, an employee of a water treatment company asked an engineer from a major oil company what it would take to convince operators of the value of smarter water treatment systems.
The answer was: “It is hard to prove how much you can save when you do not know the problem you will solve.”
One answer came from MyCelx, a young company that sells equipment for water polishing, which reduces the oil content at the last stage of treatment. Also called tertiary treatment, this step is often taken when there is an upset pushing up oil levels of water from the primary and secondary treatment systems.
A case study conducted by MyCelx covered 2 years’ experience on a deepwater facility in the US Gulf of Mexico where the company observed 10 to 12 upsets a year, some lasting for days.
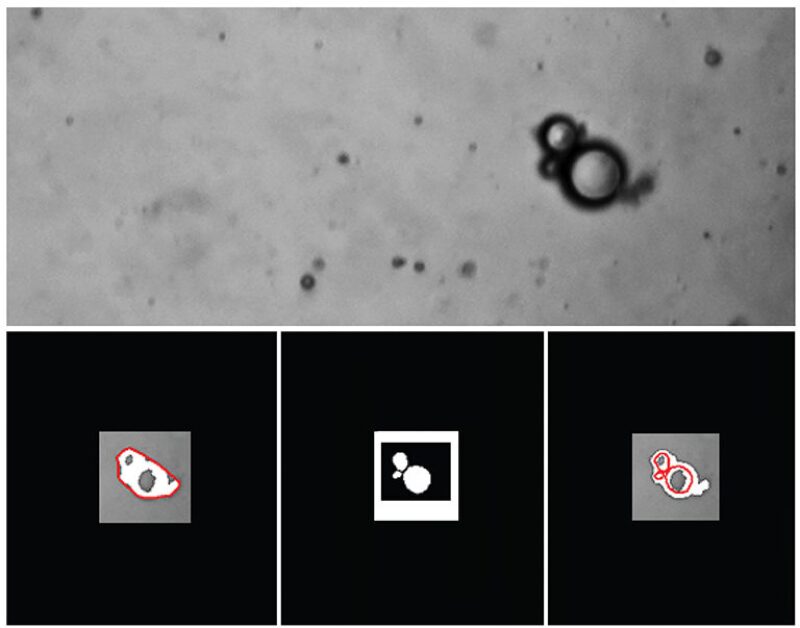
“The problem is there are short, intense, intermittent upsets” caused by variable production rates and slugging from wells, said Lance Rodeman, regional manager of technical services at MyCelx. For operating processing systems in the Gulf of Mexico, “it is a crucible, because the systems are visible, highly regulated, and there is a lot of scrutiny out there.”
Performance improved markedly in the second year when the rig went from doing periodic sampling to continuous monitoring of the oil levels in the treated water. Rodeman said the payoff came in several forms:
- Reduced costs for tertiary treatment because the constant water quality data gave operators the confidence to turn on the system only when needed. Systems created to remove really small droplets (less than 5 microns) use a media that must be removed and treated after a certain amount of use. Continuous monitoring halved that expense by limiting the use of water-polishing equipment.
- Offering clues pointing to the cause of water quality problems. There were short periods of poor oil/water separation that could be connected to a chemical used to prevent hydrate formation when flow in the riser was stopped. The operator is now seeking an alternative chemical.
- Providing operators with a constant awareness of water quality gives them a sense of ownership in consistently treating the water by allowing quick reactions to changes in quality.
“The response time went from hours to seconds,” reducing the cost of tertiary treatment needed to a fraction of what it had been, Rodeman said.
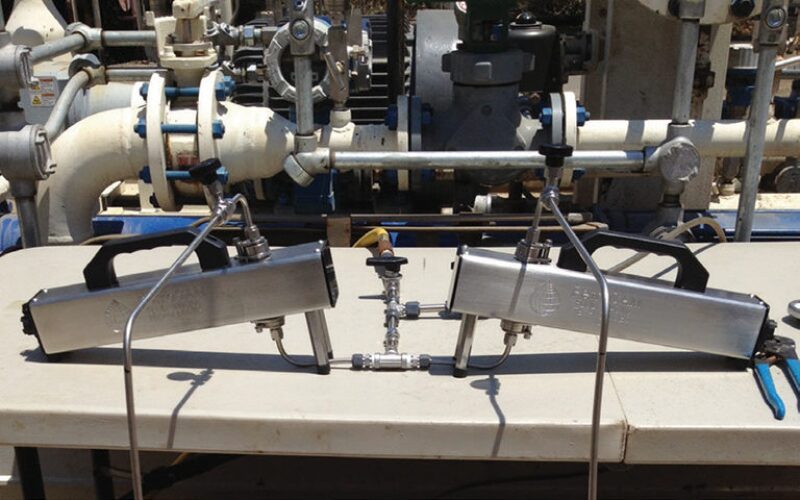
The Value of Vigilance
Those selling constant monitoring equipment say value comes from improved operations.
“The data is important for the whole process of water treatment and disposal, and reuse,” said Rick Gaskin, director of Jorin. He is one of the founders of the company that sells particle analyzers that take pictures of thousands of bits of solids, droplets, and bubbles, and then measures, identifies, and quantifies them at a phenomenal rate. The process is sometimes called dynamic image analysis to differentiate it from a previous generation of machines that measured only particle size.
Over time, the regulatory limits on the amount of oil in disposed water are getting tighter, and there is greater regulatory scrutiny as well. In the United States, the Macondo disaster in 2010 led to the creation of a new agency regulating offshore oil production with the goal of tighter supervision. Its stricter approach has motivated some operators to invest in system upgrades, said Frank Richerand, whose company, Enviro-Tech Systems, sells and engineers constant monitoring systems and other offshore water treatment equipment. His pitch is: “Tighter standards are inevitable, so why not ensure the system is working right with real-time monitoring?”
Constant monitoring is used on a significant number of locations: Enviro-Tech said it has installed them on more than 120 and Jorin on more than 200. Sales of periodic monitors indicate the monitoring market is far larger. Rintoul said it has sold 3,500 of its benchtop analyzers for periodic tests, and competitors add to that total.
Case studies presented at the seminar showed how operators used continuous monitoring systems to detect problems, react more quickly to upsets, and troubleshoot other issues. In the future, feedback from continuous monitoring will be an essential part of automated water treatment control systems, which are now being tested.
This early automation effort points to the challenge faced by those selling continuous monitoring: The value of what they sell depends on whether users find uses for the data.
Richerand said one objection comes from those who feel the added data, which is available online to authorized users, is like “big brother looking over your shoulder.” His response is it gives them early warning of a mechanical problem that needs fixing before it becomes a discharge problem noted by regulators.
Rintoul has heard similar concerns about data gathering. Some question why Wilks’ new model is designed to easily connect to the Internet so results can be monitored and stored. The value of data-driven operational analysis, such as being able to compare test results to see if any worker is consistently off the average, depends on one’s point of view. “None of these things work unless people onboard [a platform] buy into them,” Rintoul said, adding that some people seek meaning in the data while others “walk by and see a number.”
“If you think it has given you valuable alerts, you will like it,” she said.
Costly Education
For Jay Cooke, offshore drilling and completion manager at Helis Oil & Gas, the value of testing was not immediately apparent.
Water quality had become an issue after the company restarted production on a shallow-water platform off the Louisiana coast that replaced one destroyed by Hurricane Katrina in 2005, said Cooke, who told his story at the seminar.
The problem was a surge in the cost of maintaining the four injection wells used to dispose of water processed on the platform. Helis was paying USD 1 million every 3 months for backflushing to allow continued water injection. Before the hurricane, that was done every 9 to 12 months.
The cause of the injection blockages was not revealed by periodic checks of the water processed by an oil-skimming unit and a water-polishing unit. The results were in line with the design specifications. But when Helis ran the processed water through an oil-removing filter, it clogged in 30 minutes.
This costly quandary led the company to seek advice from Enviro-Tech, which advised Helis to try continuous monitoring. Those tests showed large variations in what flowed out of the 87-well Black Bay field that had been missed by tests using “grab samples.”
The periodic test results using a long-accepted lab test, the Millipore test, failed to reflect the slugs and surges there, Cooke said. “At its best, a Millipore is a snapshot,” he said. “The empirical data told us we had terrible water.”
Using what they learned about how changing production levels affected the treated water quality, Helis has reduced its maintenance expense back to what it had been prior to the hurricane. For Cooke, the lesson was: “If we had gone to real-time testing earlier, we could have gone for the best bang for our buck earlier.”

Using Feedback
When looking to improve the performance of a new produced-water system design, Mark Wolf, product line manager of process technology at National Oilwell Varco (NOV), used sophisticated continuous particle analysis to determine its performance.
He turned to the process using mass imaging and computer sorting to test the idea that certain processing steps—a hydrocyclone used for sand removal and a progressing cavity pump—would measurably increase the size of the oil droplets, thus improving the effectiveness of an oil/water separator.
The analysis did allow NOV to improve the design, and provide objective data to clients showing the process caused changes that aided treatment. But the makeup of many of those pictured particles remained an open question.
In his presentation at the meeting on using particle analysis for the first time, Wolf said the size data was a good indicator that oil droplets were coalescing at certain steps, but “I do not trust it” to measure oil and solids levels, when there are so many hard-to-identify composite particles made up of oil, solids, and other things. Still it was valuable to know that he was observing what are known as agglomerations rather than big solids, he said.
Since then, the makers of the device have been working on programs they say can identify when oil and solids are stuck together, along with things such as algae and gas, and estimate how much of an agglomeration is oil and how much is solid.
Enviro-Tech has developed an automated water processing system using continuous feedback to guide it, which has been field tested. Enviro-Tech reported at the meeting on a test of its Smart Water Discharge system on a platform off the coast of southern California, where the operator faced intense scrutiny from the public and regulators.
The system combined the standard elements of industrial automation: a programmable logic controller guided by an algorithm that used an artificial neural network to learn how to manage chemical use while minimizing excursions.
The result was the control system worked dependably over the 3-month period, but more work is needed on the water treatment method used, which required too frequent changes of the membranes used to polish the water due to the asphaltene in the water, Richerand said.
The company is now working on a different membrane to solve its water treatment problem and seeking other places to use the automated system. “We do believe it works,” Richerand said, adding “We believe this is the way of the future.”
In Water Monitoring, Nothing Is Perfect
Constant water quality monitoring is good at highlighting changes in produced water quality, and also shows how hard it is to precisely measure the exact makeup of water from oil wells.
Inside each barrel of produced water is a mix of hydrocarbons, solids, dissolved solids, microorganisms, and minerals that varies over time. If samples from the same bucket of water were tested multiple times, even by onshore laboratories, results are likely to vary, often significantly.
The potential pitfalls for water testing methods and what is being done to improve them were on the agenda when the Produced Water Society discussed online monitoring at its annual seminar, held 14–16 January in Galveston, Texas.
Most continuous testing devices for oil in water rely on one of the following two testing methods:
- Florescence uses ultraviolet light to excite hydrocarbon molecules. The intensity of what is emitted can be measured to estimate the oil present.
- Particle analysis uses microscopically magnified pictures of thousands of particles in a sample that are sorted based on their size and shape to estimate the volume and size of oil, solids, and microorganisms present.
Each has its limits. Not all hydrocarbons fluoresce—aromatic molecules do, but aliphatic ones do not. To fill in that blank, other test methods are used to establish a ratio between hydrocarbon types that is used to statistically estimate the total content. But that has to be periodically checked on platforms processing production from varying combinations of wells.
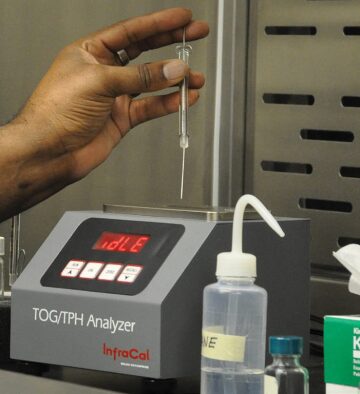
Particle analyzers are marvels when it comes to rapidly sorting particles based on pre-set parameters, representing a step up from the days when particle analyzers could only measure size. But there are bits that defy categorization. Droplets can be stuck together, with tiny solids of sand—and the image further muddied by algae—making it hard to categorize or measure the components. New software is being developed to look for oil droplets and gas bubbles tucked in what are called agglomerations.
Makers of particle analyzers, such as Jorin and Fluid Imaging Technologies, are working on new interpretation software that analyzes complex particles, spotting and measuring oil droplets, even when they are tucked into an agglomeration.
The software seeks out arcs, which are the distinctive rounded edges of a droplet, and calculates the volume of the whole by that part, said Steve Bowen, sales manager at Fluid Imaging. That particle analyzer “is now being integrated with software for testing.”
Online testing devices can be thrown off by a dirty window. Continuous imaging machines have viewing ports allowing sensitive instruments to safely view dirty water flowing through a sample tube. If nothing is done to clean it, over time, a viewing port will develop a film that distorts the measurements or makes them impossible.
Keeping these windows clean has been a major challenge for analyzer designers. They have created systems with mechanical wipers, automatic dispensers for cleaning chemicals, and ultrasonic cleaners. This feature has become a point of intense competition among sellers of continuous analyzers, with claims and counterclaims among those at the Produced Water Society seminar about which cleaning approach is most reliable and which requires the least attention by platform crews.
The ideal is a machine that maintains itself. It would eliminate the problems created by crew members who fail to follow cleaning routines, allowing a film to develop that can distort readings. And it will be essential in the future as the industry begins to move water processing units to the ocean floor, where they will need to work for years without any attention.
All the testing methods depend on the care and judgment of those caring for the machines on a platform. That is a significant variable in real-world performance, said Colin Tyrie, a consultant who has tested the performance of online water testing devices.
“They are in the difficult position of not knowing how to make sure operators take care of their equipment,” said Tyrie, who as secretary of the Produced Water Society has organized the annual seminar for years.
Details Matter
To ensure accuracy, results from real-time tests are checked against results from periodic tests. Advocates for constant monitoring remind users that the only number that matters to regulators is the one that comes from laboratory tests of water samples grabbed periodically.
Frank Richerand, whose company, Enviro-Tech Systems, sells real-time monitors, said they are good indicators of water quality, but not the final word. When a system is first installed, “the first thing is, [platform crews] all start to love it. They rely on it too heavily,” he said, adding that the critical measure remains the grab sample for the laboratory tests required by regulators.
Companies in the online testing business also sell devices for periodic tests. But there is still the risk of operator error.
One of the most common periodic tests uses infrared to measure oil volumes by calculating how much of the light is adsorbed by the hydrocarbon. Because light also adsorbs infrared, the method requires removing the oil from the water using a solvent. Seemingly small matters, such as poorly cleaned glassware, dirty solvent, or how long a sample is shaken can alter the result and even small variations can be significant when a 5-ppm swing can push the result past the limit set by regulators. Variations are also a fact of life in the required lab tests.
The US Environmental Protection Agency allows up to a 25% error on lab samples. “If you send samples out to several labs, the results can vary,” said Sandy Rintoul, executive vice president of Wilks, a subsidiary of Spectro, echoing an often-repeated observation of those whose reputations depend on these results.
Gathering More Data Faster for Better Water Treatment
For years, David Burnett has been looking for better ways to treat water from shale wells so it can be reused, which has led the Texas A&M professor to a search for real-time water testing devices “offering better quality data sooner.”
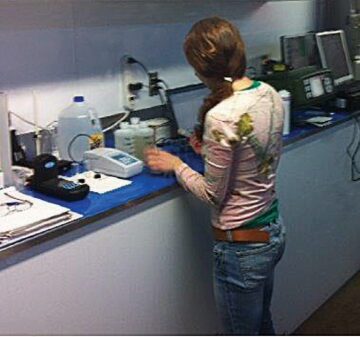
He sees the missing link for creating systems for lower cost onsite treatment of water mixed with oil, microorganisms, solids, and chemicals as the ability to constantly detect changes in what is flowing in and out of the system.
While there is an array of water-testing devices available for offshore producers telling them how much oil is left in water after most of it is removed, testing on land means sending samples off to a laboratory. “Most people fall back on sending samples to a lab and 2 weeks later, they get the result,” Burnett said. “It is hard to design a system that runs automatically without some sort of monitoring.”
The monitoring testing program brings together partners from academia, business, and government. Group members are offering more than USD 900,000 worth of support that will be added to a USD-3.5-million grant from the Research Program to Secure Energy for America (RPSEA) to search for better ways to monitor water quality and air emissions from unconventional exploration.
The project title is “Reducing the Environmental Impact of Gas Shale Development: Advanced Analytical Methods for Air and Stray Gas Emissions and Produced Brine Characterization.”
Increased interest in online monitoring is a response to multiple challenges associated with Burnett’s goal of seeking out and testing available technology to speed adoption of new ways to treat produced water for reuse, which has focused on improved membranes.
“We are trying to set up a network,” Burnett said. “Anyone with a gizmo that measures better, let’s look at it.”
But this will require finding and adapting devices capable of doing the job at a price that is in line with onshore budgets, which are tight compared with offshore operations.
Onshore produced water processing for reuse is competing with water disposal using injection wells, which in Texas costs relatively little. Even a basic, continuous oil/water metering system for an offshore platform will cost more than USD 100,000, including installation, and it monitors water from multiple wells.
Cost is more of an issue onshore. Generally the budget per well for water treatment is far less on land than in the ocean, there are far more wells to track, and the information sought goes beyond what is measured offshore where the focus is on oil concentration.
Those are of interest to Burnett, because small amounts of oil can quickly foul a membrane system, making it a less cost-effective portable treatment option. He would also like to measure all the organic materials present—the total organic content. Organic materials, such as gels flowing back after fracturing, could promote bacteria growth and damage reservoirs by leaving residue.
If the water is treated to near the quality of drinking water, potential users will want to know for sure the process consistently removes toxic chemicals, which are an issue even in very low concentrations.
“It is a tough sell,” Burnett said. “You have got to show numbers. You cannot assume they will believe you.” The portable lab in a trailer Burnett has used to test and publicize new water treatment methods is increasingly being used as a water analytics testing site.
The A&M team is trying out a device from General Electric for measuring total organic content, and a suitcase-sized device developed for the US military by Inficon to detect even small quantities of benzene, toluene, ethylene benzene, and xylene. The presence of even small amounts of those would be a serious problem if treated water was used for watering vegetation or in road construction.
Both devices have performed well when tested, said Carl Vavra, an assistant research scientist at Texas A&M Research Institute, who is working with Burnett on produced-water testing.
But cost is a concern. Burnett said he could afford to buy a used version of the GE devices, which costs USD 30,000 new, but he had to borrow the Inficon unit, because the USD‑150,000 price is beyond his budget.
It is an early-stage search with big obstacles to navigate. Still, looking ahead, Vavra said, “the potential is the sky for inline analysis.”