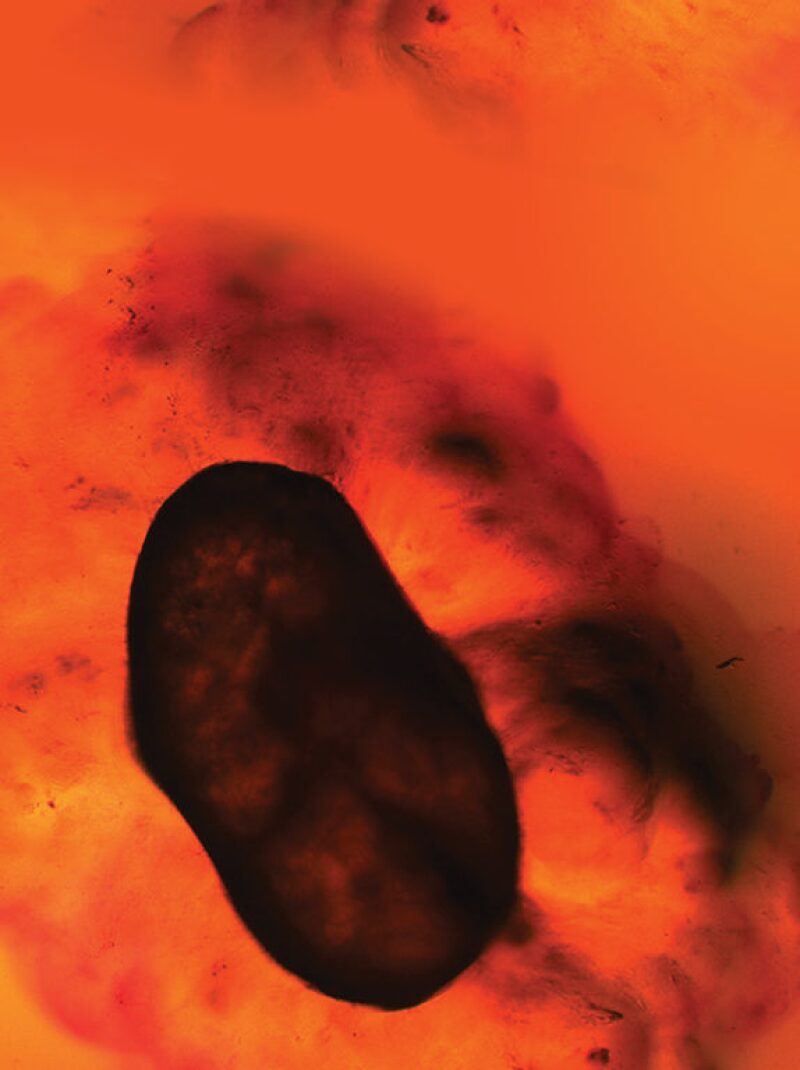
The rapid shift to unconventional oil exploration and production has made creating and maintaining better pathways for hydrocarbon flow a priority. That requires bigger bits of sand or ceramic, made stronger to maintain openings longer, and lighter, so it can be pumped further into formations using less horsepower.
Delivering larger concentrations of bigger proppant requires viscous fracturing fluids. Some of this can be described as a return to conventional formulas, but the biggest category used now in US fracturing is hybrids—a range of options being tried to increase oil yields.
With current methods often leaving more than 90% of the oil behind in unconventional formations, there’s a powerful motivation to seek out new and improved methods to ensure greater fracture conductivity.
At the SPE Hydraulic Fracturing Technology Conference in February the buzz was around a totally different approach to keeping dense particles suspended in water. Rather than putting polymer gels in water to make it more viscous, each bit of sand or ceramic is given a coating that rapidly expands in water to about 5 times its original size.
The combination, called self-suspending proppant (SSP), is far less dense than its proppant core, but this is not like putting on a life jacket. When SSP is added to water, the result looks like a murky slurry, and feels like water. This is because SSP behaves differently than untreated proppant. When SSP is in water, each grain of polymer-coated proppant expands so it has much greater volume with far less density than the grain of proppant alone. Because of its properties, SSP takes up more space in water and also makes the water appear more viscous. Also, because SSP’s density is less than that of untreated proppant—but still greater than the density of water—its settling rate is dramatically less than untreated proppant, said Robert Mahoney, vice president in charge of research and development at Soane Energy, the chemical maker developing SSP in partnership with Marathon Oil.
He describes SSP under magnification as looking like a pile of fish eggs each with a dark spot in the middle surrounded by a clear layer.
Over the next year Marathon Oil will be testing it on a series of wells to see if replacing fluid thickened by gels with individually coated particles will deliver more proppant into the formation where it can maintain flow pathways for better results.
“All the data we have so far is very encouraging,” said Phil Snider, senior technical consultant for Marathon Oil. “What we have found out so far is we can make it and transport it to a location; get it pumped and get it in place in the formation effectively.” One positive sign is little sand is coming back, and another is the polymer coating is breaking into its component chemicals as it is designed to do.
Based on early results it might provide a lower-cost way to deliver more sand or ceramics into a formation using polymer coatings that in laboratory tests appear to break down without leaving a residue behind, which could lower production.
Coating the proppant could reduce or eliminate the cost of gel used in fluids, the water and horsepower needed to pump the jobs, and might offer a delivery vehicle for new treatments, such as slow release of chemicals to fight scale buildup.
But all those are secondary measures. “Everyone wants reduced-cost fracs,” Mahoney said. “But in the end the big payback is from increased production.”
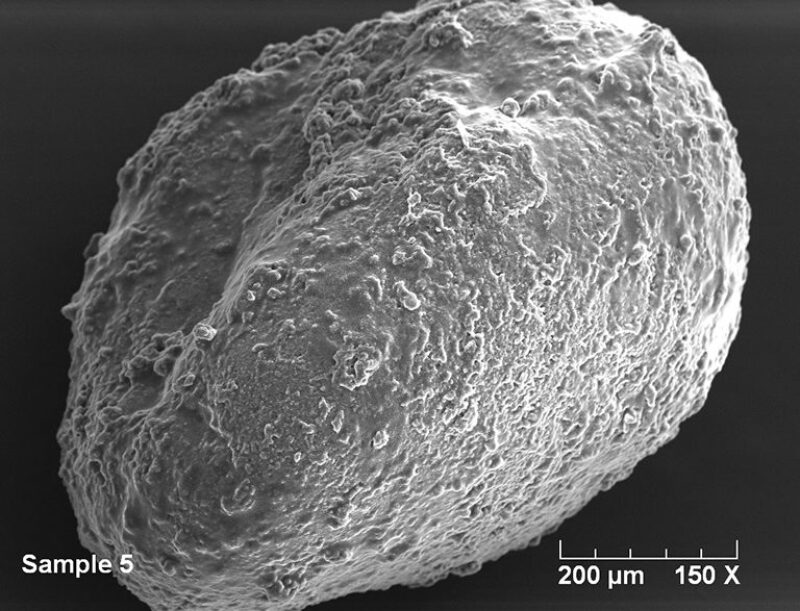
Pumping Possibilities
At the 2011 SPE fracturing conference, when Mark Franki was asked what was new in fracturing, he said he was once again able to be particular about the proppant he used to fracture wells.
Industry supplies of proppant became tight because the surge in shale exploration transformed the proppant business. The volume of sand and ceramics used now to prop open fractures is 15 times what it was in 2005, said Terry Palisch, director of petroleum engineering at Carbo.
Two years ago sand producers were catching up, but it took longer for makers of ceramics to build the factories they needed to meet the demand.
For small operators—Franki is an engineer for a small Texas company, Mentano Energy—short supplies meant taking what was available, even if it meant mixing a variety of sizes of sand to get enough to do the job. “We overlooked a lot of things that in the past would have been unacceptable,” said Franki.
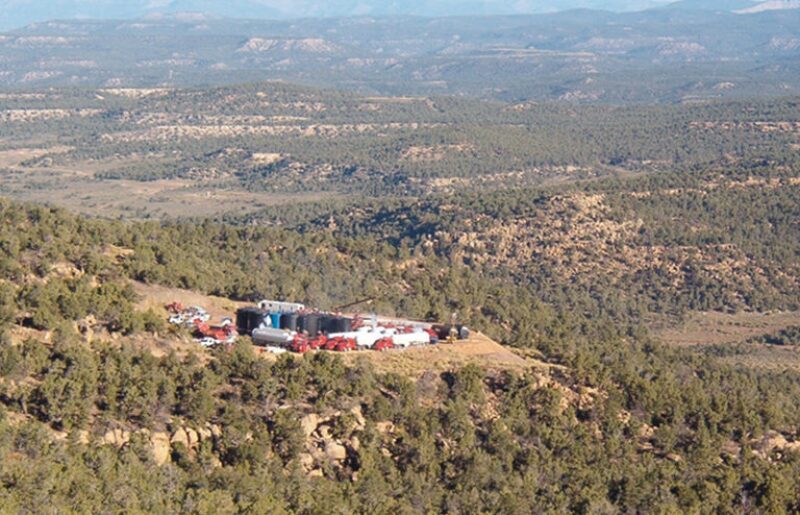
Now supplies are more than adequate and with more competition companies are rolling out new options promising better performance to maintain their share of a market where greater oil production is the measure of success.
Back in 2011, Mentano was also part of industry shift to exploring for oil in a range of formations once ignored because the quality of the reservoir is so poor. The number of rigs in the US targeting oil has since surged from 808 in February 2011 to 1,414 in March 2013, while those after gas dropped from 911 to 407 in that time frame, according to the Baker Hughes Rotary Rig Count.
An analysis of more than 3,000 wells in the oil-rich Bakken formation by Baker Hughes underlined the importance of the fluids and proppants used in fracturing. While the top variable when comparing well productivity was the location, just behind were the volume of fracturing fluid used, the use of coarse (larger-sized) proppant, and the concentration of proppant.
To deliver the heavier load needed for producing oil, and the gas, whose flow complicates the conductivity equation, the makeup of the fracturing fluids has moved to mixes with cross-linked gels added to prevent the heavier proppant from settling in transit.
The changes are evident in the disclosures on the FracFocus website, which was created to reveal what things are going into wells during fracturing. An analysis of that data by an energy data firm, PacWest Consulting, showed that the number of slickwater fractures—mixes of water and a friction reducer, known as slickwater fractures—went down from 46% of all the fractures in early 2011 to 24% in the third quarter of 2012.
In third-quarter 2012, the remaining fracturing jobs were a mixture of those considered conventional (34%) and others that combine old and new approaches, classified by petroleum engineers at PacWest as hybric fractures (around 40%). Using water with a minimum of additives for fracturing generally creates longer, planar fractures and saves on the cost of chemicals and pumping. Conventional fluids are said to transport sand more effectively but create shorter fracs that finger into the reservoir.
There has been nearly a decade of variations on the hybrid theme, with papers going back to one in 2004 by Mukul Sharma, a professor at The University of Texas at Austin.
The most recent variation, presented at the conference by Sahil Malhotra, a graduate student with Sharma, made a case for alternate slug fracturing. It uses water to transport proppant followed by gelled fluids to push it in, and the steps are repeated.
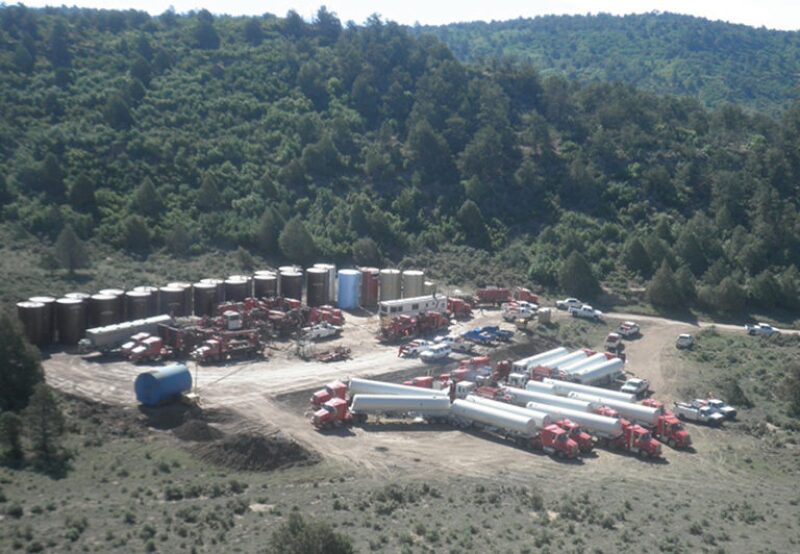
The benefits claimed were a good summary of what the industry is seeking: longer fracture lengths, lower pumping power, better control of fluid leaking off into the formation, and reducing the risk the proppant will not get into the formation due to screenout at the wellbore.
Based on experience, fracturing methods are evolving. Darren Schmidt, a technical advisor at Statoil, said many operators are making fracturing jobs more complex to make them more effective.
A lot of things are being tried. The FracFocus database shows a spate of slickwater fracturing jobs in the Bakken this year—8% of those reported in the fall of 2012 compared to 1% during the same quarter the year before—in a basin where 55% of the fractures are conventional.
It is hard to settle an argument about what works in the ground because little testing has been done with rock from the formations to see what happens after the fracture.
In the past year lab tests were conducted in an industry study on samples of rock gathered from a test well in the Bakken, using various proppants and fluids. The goal was to see how various combinations of the three are likely to affect the flow of hydrocarbons in tests simulating underground pressures and temperatures.
The study, by the North Dakota Energy and Environment Research Center, with funding from government and industry sources, looked at variables ranging from how different fluids affect rock hardness to whether ceramic proppants are likely to outperform sand.
It found water could significantly reduce the strength of reservoir rock—the average loss was around 50%—which could allow the weight of the rock above the wellbore to embed the proppant, blocking hydrocarbon flow. Gelled diesel had the least effect on the rock, but it is out of favor as the industry seeks out environmentally benign fluids for drilling and completing wells.
The tests simulated the effect of the fluids and pressure on proppants. It found the strength of the ceramics were least affected by the fluids tested. Crush tests showed sand was more likely to break apart, and the fine particles created that way could reduce the conductivity of fractures. Ceramic proppant performed best in conductivity testing, followed by resin-coated sand.
“There are orders of magnitude difference in the conductivity under stress of sand and ceramic proppants,” said Schmidt, who delivered a paper on the study.
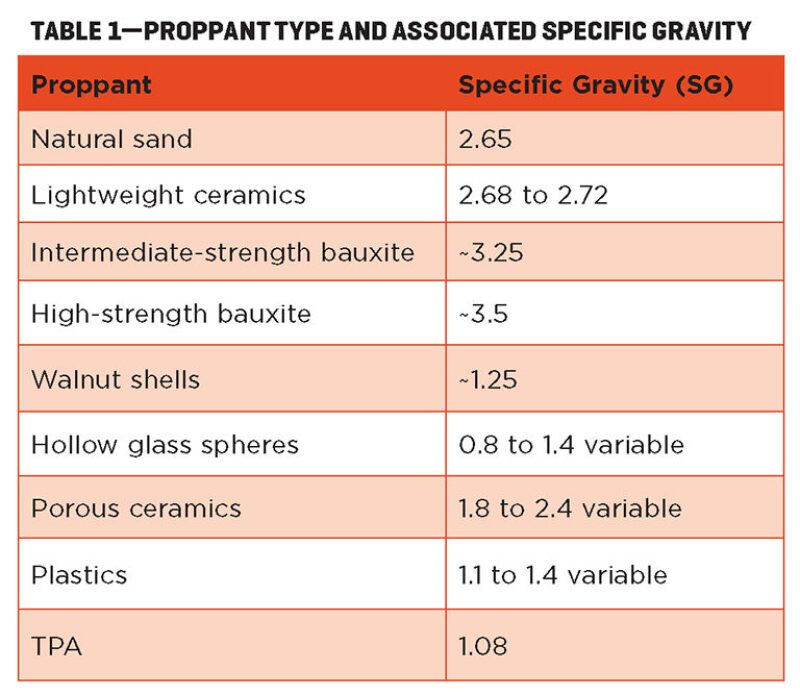
Proppant Problem Solving
Proppant makers are bringing out new products that are lighter, stronger, do more, and come in a different shape.
For extreme offshore wells that are in water depths of more than 30,000 ft, Carbo has tested an ultrastrong bauxite ceramic capable of withstanding up to 20,000 psi of closing pressure in formations, such as the Lower Tertiary in the deep waters of the Gulf of Mexico.
The company has little to add about what it can do while it gears up to produce it on a commercial scale, said Palisch of Carbo.
After a long quiet period, Oxane is expected to finally begin talking about the results of field tests on its OxBall proppant, which was developed using nanotech materials developed at Rice University that it says are far stronger by weight than competing ceramic proppants.
The details will be in papers to be released later this year said Mark Mack, vice president of engineering at Oxane, who offered a short comment: “In a 20-well study, we have documented a 20% improvement in 12-month production simply by replacing standard intermediate strength proppant with OxBall. In many North American tight oil/oil shale plays, an improvement of less than 5% would justify the additional cost of upgrading to an advanced ceramic proppant.”
And the company said an improved version that is lighter and offers the same strength is expected later this year, he said.
For wells with performance problems, like scale buildup, Carbo has released a porous proppant, Scaleguard. It is an early example of an industry trend toward using proppant as a delivery device. The advantage of this approach is a chemically infused ceramic can slowly release a chemical over time. Treatments delivered in fracturing fluids will flow out of the well in the days after the job, Palisch said.
Schlumberger has a new ceramic proppant shaped like rods. It is designed to act like tiny columns, providing a more conductive pathway near the wellbore. The sharp-edged shape is designed to create a proppant pack that remains in place, significantly reducing the amount of proppant that flows back in field tests.
The higher cost of the rod-shaped proppant relative to traditional spheres, was offset by production gains and better proppant flowback control in field tests, said Alejandro Peña, well production services chemistry and materials portfolio manager at Schlumberger.
And there is a growing array of ultralightweight proppants designed to reduce the weight, volume, and pumping power needed to deliver proppant.
In a Tight Zone
Ultralightweight proppant made it possible for Energen Resources to complete four wells in a national forest in New Mexico on drillsites so small the phrase “frac spread” was not a good description.
The solution was a proppant developed by Halliburton and produced by Sabic, called MonoProp made out of thermo plastic alloy. It reduced the amount of proppant needed for each well to an average of nearly 31,000 lb, compared to an average of 296,000 lb for five comparable wells elsewhere in the Pictured Cliffs tight gas formation, according to a paper on the project.
“If we had to do it the conventional way we would not have been able to do the project,” said Patricio Sanchez, senior district engineer at Energen, which has operations in the Black Warrior basin of Alabama, the Permian Basin in west Texas, and the San Juan basin in New Mexico and Colorado.
Switching to lower-weight proppant reduced the number of containers needed to deliver it from 15 to one, and also reduced the pumping capacity needed for the nitrogen foam job done by Halliburton. The proppant, whose density is among the lowest in its class, can be pumped at 25 bbl per minute, compared to 50 bbl per minute with sand. That helps to control fracture height growth and to keep the job more in the zone, Sanchez said.
A paper presented by Halliburton and Energen Resources at this year’s fracturing conference concluded that using the ultralightweight proppant may have added to production as well.
The proppant was chosen after comparison test with other competitors. It was able to stand up to the closure pressure in the shallow formation, as well as to the production chemicals the company planned to use, Sanchez said.
The results of the four gas wells were compared to five wells drilled into the same formation and fractured using 20/40 mesh sand. By far the best producing well was drilled by Energen, while the two worst were in the control group fractured using conventional materials in what he said was a better reservoir. The other six wells were tightly bunched.
Sanchez was pleased because “we compared it to wells in a better reservoir, and actually ours performed better.”
A Q&A with George KingGeorge King, global technology consultant at Apache Corp., has written and spoken extensively about advances in unconventional oil and gas exploration and production technology. He offers his thoughts on whether the industry is likely to try some unconventional approaches to improve recoveries. Do you think there is a greater willingness to try new things?In about the same proportion as the rest of the human species, only the young and the curious are open to new ideas, but when new ideas have a strong economic drive, the uptake is much better. We are led by our wallets. Self-suspending proppant and other similar things that have the potential to sharply raise production will be tried by leaders, who will take the lumps and bruises while the rest follow when it is proved a success. What is their motivation?The unconventional oil and gas zones, which, to date, have only produced about 1 to 3% of total technically recoverable reserves (in unconventional plays). The driver here is stronger because of the reserve picture. Unconventional oil recoveries have risen to 3 to 5%; 5 to 8% is on the horizon, but we aren’t there yet. Yes, without advances in technology we could leave 90% behind. That’s a really large target for technology to shoot at. Will that sway decision makers?When enough dollars dance in front of an oilman, even the older ones will try new stuff. For more, see a replay of George King’s recent online lecture, Tight Oil Approaches and Technology Gaps—What Works, What Hasn’t Yet at http://www.spe.org/dl/video.php. |
Proppant Placement?
There is more than 50 years of mathematical work on how fluids and gases flow through fractures. But a lot of questions remain for debate.
In a keynote speech at this year’s fracturing conference on conductivity, Bruce Meyer of Meyer and Associates offered an overview, running through a forest of formulas dating back to the 1960s.
But there are still differences among experts on the importance of proppant. His conclusion was: “If you go out and do not pump proppant, I do not think you will do as well.”
Arguments about what proppant does are hard to resolve because of uncertainty about where it goes. At the fracturing conference booth for MicroSeismic, a company named after the approach it uses to monitor fracturing work, one the most-asked questions was: Where did my proppant go downhole?
And there are theories that one reason fracture performance varies so widely is because some spots get more proppant than others.
To help shed light on the subject Halliburton did a study simulating the flow of sand through a row of three perforations along a wellbore using an above-ground flow loop. The goal was to answer the question: Can differences in the amount of proppant help explain wide production differences observed within wells?
The answer was, the distribution varies. Heavier sand and ceramics tended to flow into the last of the three openings on the test loop, possibly because its momentum carried it farther than the fluid. Smaller grains were more likely to flow out the first. Adding gel to make the fluid more viscous evened out the distribution.
And after the series of tests, the friction of the flow had cut deeply into the hardware used to connect the three diverter lines on the flow loop even though the pumping rate used—up to 14 bbl per minute—was a fraction of what is pumped in a well.
When asked about why the lower pressure was used, the paper presenter, Freddy Crespo, an applications engineer at the Halliburton Technology Center, said higher pressures were not an option because of the limits of the test setup, adding: “If you go to higher flow rates it will explode.”
A Surprise Answer to an Old Question
Back when supplies of guar were tight, Marathon Oil asked a high-tech chemical company if it could create a substitute for the plant product used to thicken fluids used for fracturing, and it was also looking for an option that transported proppant more efficiently.
The company, Soane Energy, came back with an unexpected way to keep dense particles from settling in water.
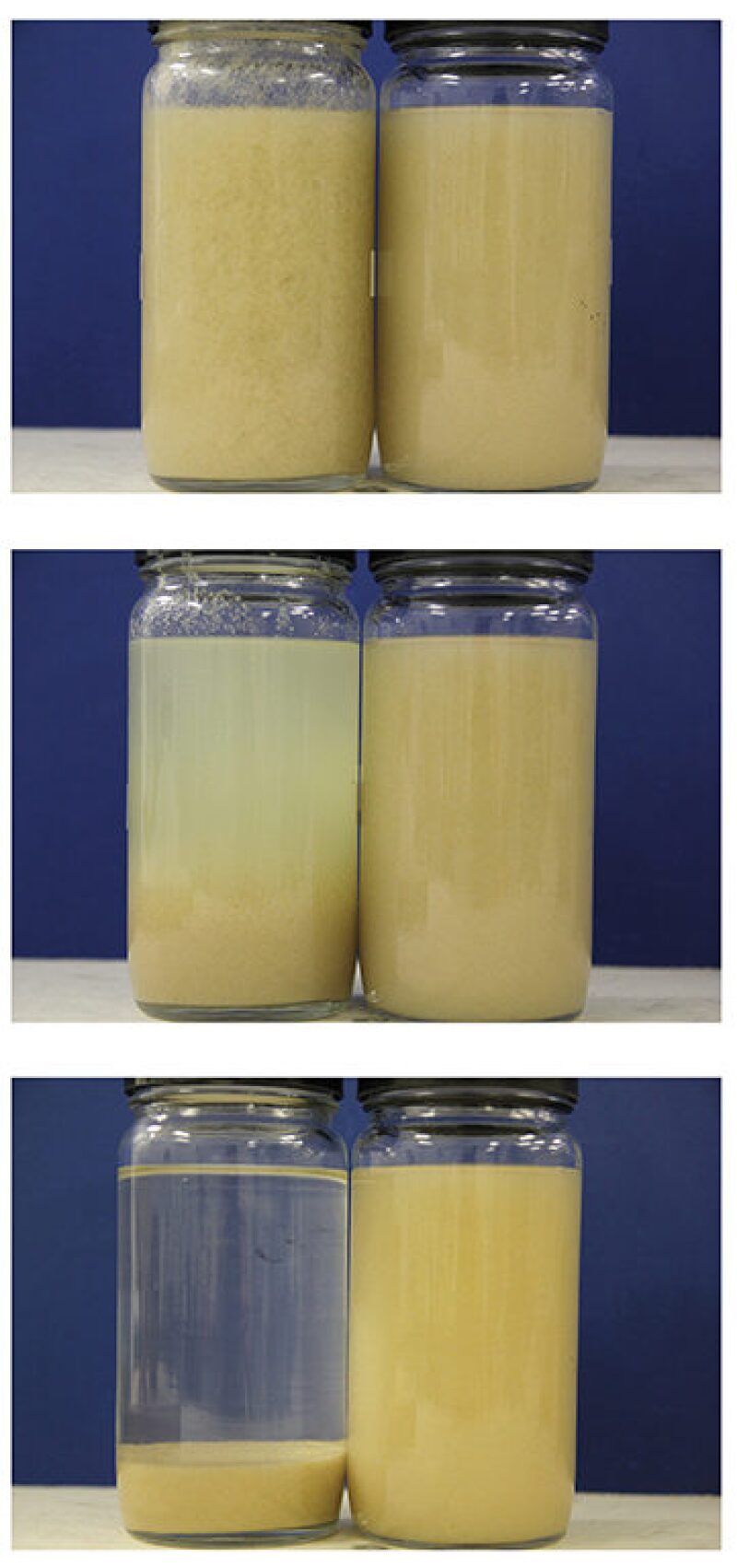
In the oil business this has long been done by mixing water and a gel, most often made from guar, creating a viscous fluid able to carry bits of sand or ceramic through a well on to fracture the formation.
Soane’s approach was: “We can coat every sand grain,” said Phil Snider, senior technical consultant for Marathon Oil. The proppant problem was on the list of problems in need of better solutions that Snider and his partner on the project, Steve Baumgartner, also a senior technical consultant at the company, were working on.
The result of that exchange is called self-suspending proppant (SSP). Each grain is given a polymer coating that expands to about 5 times its size when combined with water. The combination reduces the density of the pairing, which alone would reduce settling. The key to keeping it suspended, though, is the expanded size of the coating, which fills the space keeping the heavy bits in suspension.
The inspiration for this was the chia seed, which has gained a bit of notoriety as an eye-catching addition to trendy drinks. The seed remains suspended indefinitely because it is covered by a layer of material that expands by readily absorbing water.
“When you put one in water it swells like crazy,” said Robert Mahoney, the vice president of research and development for Soane, who still has a murky glass full of the seeds, which inspired the development team, which then had to find a polymer that acted like that in water and attach it to the various materials used as proppant.
The offbeat inspiration is not out of line at one of the many companies founded by David Soane, a former professor at the University of California Berkeley turned entrepreneur. His ventures are in many industries but have a common thread; they use innovative material science techniques to make and attach coatings. One of the best known is a treatment to make fabrics stain resistant, known as NanoTex.
To explain SSP’s potential, Mahoney points to a lab test using an 8-in. tall cylinder, called a vertical flow column. Various mixtures are pumped in to see if they separate while rising. While the SSP, with sand inside, flows over the top, the water thickened with linear gel leaves the sand behind.
It is too early to say if SSP will do as well in the ground. But Snider said the early results are promising. After lab tests indicating it could do what was needed in a well, Marathon started trying it out by fracturing individual horizontal well stages, and steadily adding more of them. By mid-February it had done half the stages of a lateral and a full well test was completed in early March.
The cautious buildup was designed to observe the performance of a product that did not fit into the measures of performance of proppants or fluids because this coated proppant fills both roles.
One early concern was whether the coating would keep the proppant from entering fractures, but there has been no sign that is a problem. Snider said the gel and proppant combination is able to squeeze into tight spaces because its outer layer deforms to fit in. They have observed that the amount of proppant flowing back after fracturing has been minimal, and the polymer coating is breaking down as designed.
The coating is designed to break into its component parts when it reaches bottomhole temperature. This process can be enhanced by pumping a chemical breaker, and higher salinity water can also break the polymer.
Those conditions are likely around the time the fluid reaches the end of its trip in the wellbore and is about to enter the hot formation.
Making sure the SSP coating breaks down is critical because its creators want to avoid a problem commonly blamed on gels—production-reducing residues left in the formation. Based on the lab testing, Mahoney said SSP is different because “it is not just a polymer (molecule) coiling and uncoiling”; it is breaking into component parts that flow out with the produced water from the well.
Over the next year Marathon will be trying to answer the key question: Can SSP increase oilwell production? It plans to do a series of comparison tests in areas with fairly uniform geology. “The number of wells tested will depend on the how the first few turn out,” Snider said.
The coating is being done by CRS, a proppant company brought in to figure out how to apply Soane’s invention to millions of pounds of sand. So far, changes have been made to ensure SSP flows as smoothly as the highest-quality sands, which is not easy to do when handling a coating that reacts with water.
And Snider said the experience highlighted the benefits of going outside the industry when looking for help. “There is an advantage getting some tech assistance from someone who has no knowledge of how we do things,” he said. “They are not constrained by conventional thinking.”
A Proppant Pill for Ailing Wells
In the 1980s Claude Cooke had an idea for a low-cost way to improve the output of underperforming wells.
But it took decades to find the materials he needed to turn that idea into a treatment, called SqueezeFrac, being produced by a startup company called EnerPol.
While doing hydraulic fracturing research for what is now Exxon Mobil Corp. he noticed there were a lot of fracture treatments where pressure tests showed much larger than expected results, suggesting a high-pressure shot of sand likely cleared out damage near the wellbore.
It strongly suggested there is a reward for fracturing older wells, but the cost of doing that would exceed the likely gains at many of those wells. Cooke said he saw “a need for a much less aggressive and expensive method to remove near wellbore damage.”
The job could be done with a lot less sand, fluid, and horsepower to pump the job, if it were possible to squeeze in a small amount of very viscous fluid and proppant.
His idea was to do that by delivering the sand and proppant in the form of pellets about the size of an M&M that would be pumped into a vertical well. These pellets would dissolve as they warmed after reaching the area in need of treatment. It would be a targeted delivery system reducing the materials and pumping power required.
The concept of a small fracturing job, like a squeeze job for cement repairs, sounded simple enough for Cooke, who was honored by SPE as one of the “Legends of Hydraulic Fracturing” for his role in developing bauxite ceramic proppant.
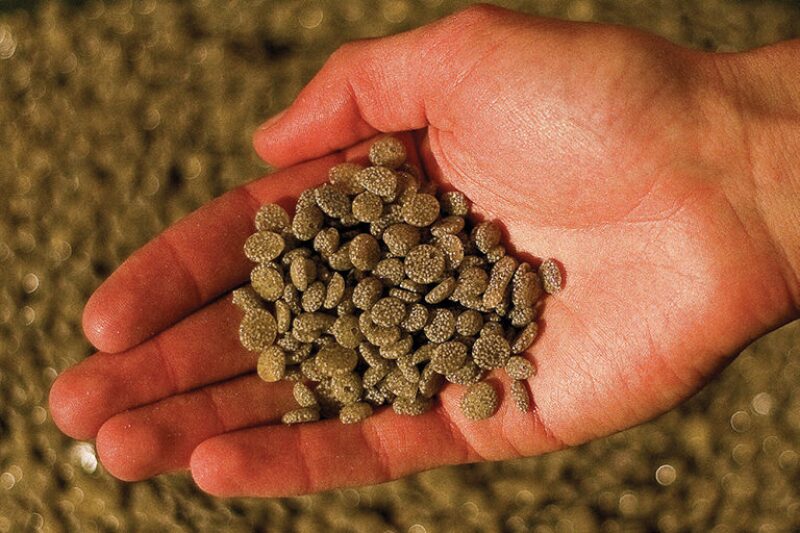
But the project remained on hold for many years because he lacked a low-cost source of a polymer that would degrade as needed—first going from a solid into a thickener for the fluids in the well, and after the job is done breaking down into its component chemicals without leaving a residue. “It had to have a degradable polymer. I knew such things existed but they sold at too high a price,” he said.
That changed when environmental concerns persuaded fast-food chains and others to begin to make clamshell hamburger containers using materials that would biodegrade in a landfill.
It took a while longer to find a company willing to supply what he needed in the amounts required by EnerPol to begin making the pellets and testing the concept. Recently it received a second round of support from the Research Partnership to Secure Energy for America to pay for testing, with a budget of USD 3.4 million.
The treatment has been tried on one well, which became significantly more productive, but unfortunately most of what was produced by that dead well was water rather than oil, Cooke said.
SqueezeFrac is a multistep process. Polymer pellets without proppant are pumped in first, followed by pellets with the proppant. They accumulate over perforations at the bottom of the casing and a gel forms. Then the mixture of gel and sand is squeezed through perforations by pressure at the surface, much like a squeeze cementing operation. Afterwards the polymer degrades in the fracture into an organic acid.
The equipment used is no different than what would be found on a typical fracturing job. It works perfectly well, but Cooke pointed out it is built for jobs many times larger than his, which can be done with a 300-horsepower engine, or less, and would cost about 20% of what a typical fracturing job would. In the future he’d like the see the job pumped using equipment mounted on the back of a pickup truck.
Further Reading
- SPE 163818 Self-Suspending Proppant by R.P. Mahoney,
Soane Energy, et al. - SPE 163815 Case History: Production Results From Partial Monolayer Proppant Fracture Treatments in the Pictured Cliffs Formation Horizontal Wells of San Juan Basin by Muthukumarappan Ramurthy, Halliburton, et al.
- SPE 160206 Hydraulic Fracture Design Optimization in Unconventional Reservoirs—A Case History by Terry T. Palisch, Carbo Ceramics, et al.
- SPE 163849 Investigation of Improved Conductivity and Proppant Applications in the Bakken Formation by Bethany Kurz, Energy & Environmental Research Center, et al.
- SPE 163875 Analysis of U.S. Hydraulic Fracturing Design Trends
by Christopher Robart, PacWest Consulting Partners, et al. - SPE 163852 Application of Multivariate Analysis and Geographic Information Systems Pattern-Recognition Analysis to Production Results in the Bakken Light Tight Oil Play by Randy F. LaFollette, Baker Hughes, et al.