Technology that can analyze visual data with unprecedented speed and accuracy is emerging as a powerful and potentially transformational tool for the industry.
Artificial intelligence (AI), machine learning, and computer vision are a trio of technologies that, when combined, make it possible to interpret images and videos to identity patterns that can be used in many ways.
In the oil patch, a supermajor conducted a proof of concept using computer vision to assess hole-cleaning efficiency during well construction, a university developed a workflow for analyzing drill-bit wear to improve drilling parameters, and companies are using the technology to enhance worker safety through real-time monitoring of personal protective equipment (PPE) and the identification of potential hazards.
Assessing Hole Cleaning
A 3-month proof of concept trial has shown computer vision can assess the quality of hole cleaning during well construction, although some details need to be refined before the technique can be widely deployed.
SPE 220985 describes assessing the effectiveness of hole cleaning at five Permian Basin wells by using an image analysis model combined with a remotely monitored and autonomous camera system to measure the recovery rate of drilled cuttings.
During a session at SPE’s 2024 Annual Technical Conference and Exhibition in September, Shekhar V. Gosavi, principal borehole management engineer at ExxonMobil, said that as of the time of writing the paper, most of the quantitative measures of hole cleaning using the traditional approach were still in the “art” phase with the accuracy of measurements varying by plus or minus 20%.
“That’s not acceptable,” he said.
But the proof of concept did indicate that an optical camera can, under the right conditions, measure the volume of cuttings returned to the shaker (Fig. 1), he said. Once refined, real‑time cuttings-returns analysis using computer vision could enable increased drilling speed and lower risks.
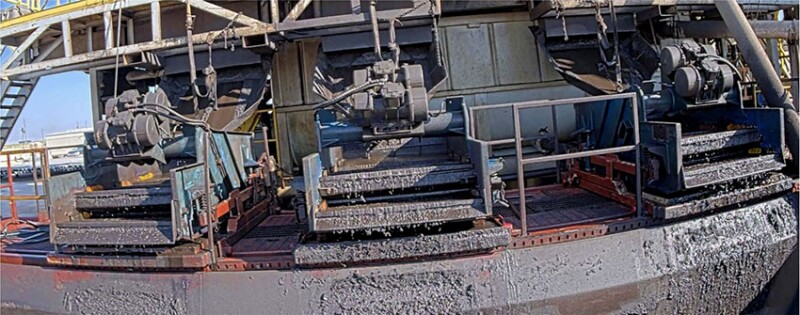
According to the paper, the “technology has the potential to significantly reduce the nonproductive time associated with circulating and mitigating packoff events, effectively addressing inadequacies in current cuttings-transport modeling and hole‑cleaning practices.”
Prior to the trials, the vendor, DrillDocs, worked with a team at The University of Tulsa Drilling Research Projects to validate the image analysis model against a cuttings-transport model developed at the university. DrillDocs engaged BlackHawk Datacom to provide technical support during mobilization, ensuring that the system was installed by experienced personnel with minimal impact on active drilling operations.
To conduct the trials, ExxonMobil installed an explosion-proof optical camera with onboard image analysis software near the shale shaker, turning the shaker into a source of digital information.
Other elements included network infrastructure and a server for data processing, storage, and visualization.
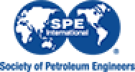