During a protracted period of depressed prices in E&P, the customer focus for service companies and suppliers shifts to finding ways to reduce the cost of producing a barrel of oil.
Step one in the process was meeting the demand by operators to discount services and supplies to maintain customers in a shrinking market. Last year, cost cuts were quick, often substantial, and not likely to be repeated this year.
“There is a limit to that (discounting) where you begin losing capability,” said Ethan Phillips, a partner for Bain & Co., who recently did a report on changing opportunities for oilfield service and supply companies. “The easy stuff, cutting capacity and pricing, came quickly. Now service and equipment companies are looking to that next stage, which is: How can we collaborate with our customers to look for ways to shave costs, promote new development, and gain efficiency?” he said.
Optimization used to be associated with maximizing production. Now it must offer a way to profitably produce, even from higher-cost reservoirs.
“The conversation has changed,” said David Deaton, chief advisor in production solutions for Halliburton’s Landmark Software and Services. “For the more nimble operating companies, it is a call to action to streamline processes and improve efficiencies.”
An example of that was a producer that lowered the cost of heavy oil production by testing how production held up when steam injection was reduced, and discovered that reducing one of its most expensive inputs had a negligible impact on oil production, making it an attractive tradeoff.
“Even though efficiency is a continuous goal, operators may not have considered reducing the steam plant output, as long as they could produce any amount of oil at USD 100/bbl with a profit,” Deaton said.
There is an increased focus on reducing production costs because drilling for more oil is simply too expensive, particularly if it is heavy oil. To limit costs, service company customers want to get more value from the equipment, software, and data they own. Better measurement and analytics can be an attractive option, but only if it can be managed by the operations and engineering staff, which has seen its workload grow as companies have cut staff, Deaton said.
Next Steps
The industry cannot afford to abandon exploration and development because it needs to make up for the natural decline in older wells, so new approaches are required. An obvious target is deepwater development, where the average cost per barrel is even higher than shale plays onshore and major cost overruns have been common.
There have been early examples in the North Sea and Gulf of Mexico, where projects are being engineered to simplify designs. Complexity and over-customization are on the list of things causing blown budgets and timelines. Phillips said the options include more modest designs for production systems, limiting modifications of the components used, and buying systems in the form of standardized modules designed by the supplier.
The financial constraints require more widespread use of management approaches, such as designs based on a specific price point, rather than setting the cost based on the design, and zero-based budgeting where the full cost must be justified rather than the cost beyond a benchmark level.
Data Insights
Operators are looking for ways to get more value from available hardware and information. An example of that is finding ways to get more out of the data flowing from operations.
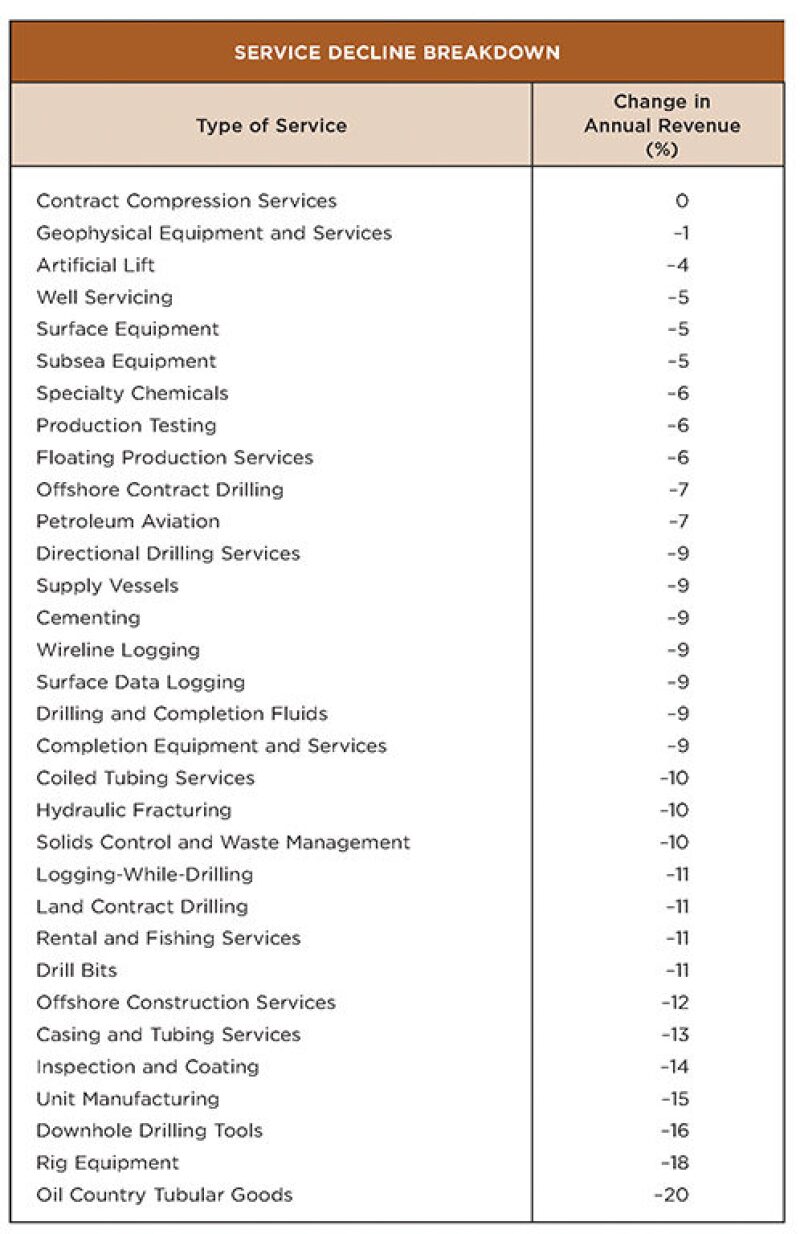
For example, systems that sift through data flowing from pumps seek trends or anomalies that may point to opportunities to increase efficiency or avoid costly failures, said Deaton, who is the technical advisory council chair for the SPE Petroleum Data-Driven Analytics Technical Section. Pattern recognition software can be used to seek out ways to reduce downtime and operating costs on a limited budget.
Over time, the goal is to create accessible databases from isolated spreadsheets, which can offer workers access to information that will help them be more productive, such as knowing in advance what is likely wrong with a pump and what parts will be required to fix it. Getting that information into the hands of field workers requires organizational changes to ensure staffers see the value of the tools, know how to use them, and have the resources available to address problems.
“Automating the data activities and applications in this way will lead to more efficient use of engineers’ time, less time searching for tools and data, and therefore reduced nonproductive time,” Deaton said. “The staff can be more effective in looking for and applying more optimization opportunities …(which) is also called for in these times of reduced operations and engineering staff.”