A pressure pulse, known as a water hammer, can occur immediately after water-injection wells are shut in for emergency or operational reasons. Large pressure pulses may cause wellbore-integrity problems such as sandface failure and sand production. This paper proposes a new work flow to simulate water-hammer events, the resulting wellbore failure, and sand production in water injectors.
Introduction
For water-injection wells handling high injection rates, water-hammer signatures are observed when water injection is stopped. Designing water injectors and deciding how quickly or slowly to shut in wells requires careful attention.
×
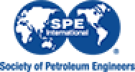
Continue Reading with SPE Membership
SPE Members: Please sign in at the top of the page for access to this member-exclusive content. If you are not a member and you find JPT content valuable, we encourage you to become a part of the SPE member community to gain full access.