The use of moored, oceangoing “smart” buoys that can harvest energy from waves could be an efficient and economic means of supplying electric power for various offshore oil and gas operations, including well trees, monitoring systems, and autonomous underwater vehicles (AUVs). Potentially, such technology could reduce, or in some cases eliminate, the use of diesel-powered generators on offshore facilities.
The PowerBuoy (Fig. 1), developed by Ocean Power Technologies (OPT), is new to the oil industry but has been used for a number of years in the defense and utility sectors. The autonomous buoy system consists of a surface float, a spar containing a power takeoff (PTO), a battery system, and a heave plate that constrains the spar’s motions. The system is capable of delivering energy from a few kilowatts to several hundred kilowatts, with future evolution planned to deliver even more power.
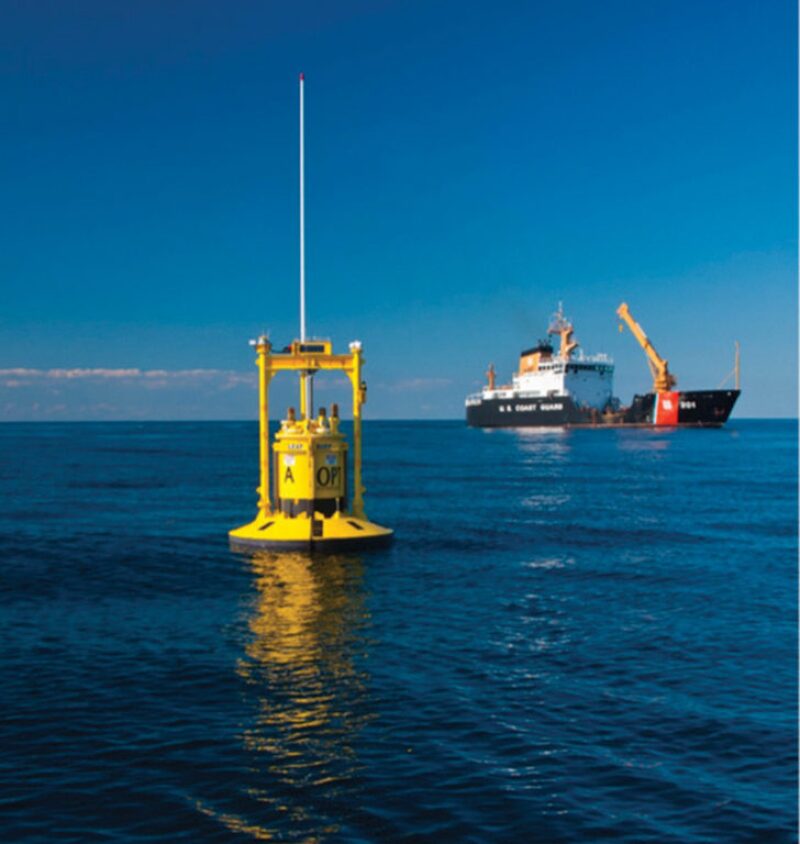
The process begins with the rising and falling of waves, and the resultant mechanical stroking is converted by a specially designed PTO to drive an electric generator. This power is transmitted to external equipment by means of an underwater power cable or directly to payloads integrated into the structure itself. Continuous power is then available with the option of larger, timed power bursts.
Advanced internal control systems continuously monitor the various subsystems and the surrounding environment and optimize performance of those systems with data transmitted to shore in real time, providing health and status updates on itself and its attached payloads. With this information, the operator gains a high level of control. Depending on the model of the buoy, the system is designed to need no maintenance for up to 3 years, providing potential savings in operating and life cycle expenses compared with existing power generation alternatives.
Advanced control algorithms have been developed that actively assess oncoming waves to tune the internal PTO dynamically to ensure that it extracts maximum power. In the event of especially large oncoming waves, the buoy will automatically protect itself by locking the float and PTO subsystems and continuing to supply electric power to its payloads by means of the embedded energy storage system (i.e., batteries). The power management system of the buoy manages the state of charge of the battery to ensure efficient overall system operation and to preserve battery life.
US Navy Project Case Study
OPT established the Littoral Expeditionary Autonomous PowerBuoy (APB) (LEAP) project after being approached by the US Navy, which was trying to increase the coastal monitoring and security surveillance capability of its high-frequency (HF) radar network.
To extend the offshore range of the coastal radar system, an APB-350 unit designed by OPT was deployed approximately 22 miles of the US east coast. The HF antenna was mounted on the top of the buoy to transform a monostatic shore-based network by enabling it to operate in a bistatic mode for improved performance.
Among the Navy’s specifications for the LEAP project were:
- Uninterrupted power supplied to the HF radar payload and to communications systems
- Ability to remain on station in all ocean conditions
- Mechanical, electrical, and mooring systems capable of surviving defined extreme ocean conditions
- Dimensions suited to deployment by a US Coast Guard cutter vessel (transportable in a standard ISO 12m shipping container)
- Deployment for a long period
- Autonomous operation without a constant need for on-site monitoring and maintenance
These requirements guided the design and testing of the APB-350 buoy system, including its electrical, mechanical, and mooring subsystems.
The use of the HF radar on the buoy resulted in a major improvement in the resolution and tracking of vessels, with detection ranges doubled. This helped reduce spurious alarms and improve the management of the offshore monitoring and security surveillance.
Beyond its communications ability, the robustness of the buoy was tested, including mechanical, electrical, and mooring components. The structure successfully withstood Hurricane Irene, which passed just west of the deployment site. The buoy remained on station despite 29.5-ft significant wave height generated by the storm over 48 hours.
However, more notable was that the system remained fully operational throughout to provide power to the payload. A post-hurricane inspection of the structure and mooring revealed no damage. This highlights the technology’s capabilities that could be transferrable to the extreme conditions of the offshore energy sector, such as deepwater and ultradeepwater environments.
In the program’s next phase, starting in July 2013, a passive acoustic monitor for subsea vessel tracking was added to the system.
Oil and Gas Applications
OPT has developed a range of potential applications for the oil and gas industry, including:
- AUV garages that perform permanent infield monitoring or inspection of assets
- The control of electric trees for field injection of CO2 and water
- Environmental monitoring before and after the deployment of offshore drilling and production assets
- Real-time, on-site field monitoring and sensing systems for 4D reservoir analysis and preseismic and post-seismic deployment surveys
- Security cordons for offshore developments, in which the buoy serves as a host for surveillance equipment that can track vessels and aircraft and potentially provide early threat warnings (Fig. 2 above)
- Temporary navigational markers for surface and submerged structures
- Diesel power replacement, using the larger PowerBuoy 40 (PB40) system
Three of these applications—AUV garages, the control of electric trees, and diesel power replacement—align particularly with current needs in offshore operations.
Prepositioned AUV Networks
Applying the technology as a persistent power source for prepositioned AUV systems alongside AUV garages could enable fast and cost-effective power delivery. Used in this way, the buoy system can hold an advantage over ship-centric AUV systems, especially with the wide areas covered by typical oil and gas fields and the increasingly remote locations being developed.
AUV performance is hampered by the vehicle’s need to resurface for recharging, for mission programming, and for uploading post-mission data. Doing so is particularly difficult in sea states higher than 2. Using an AUV garage removes these limitations by providing an in-situ charging point and enabling two-way communication between the device and its control point without the need to resurface.
Thus, the operator can address minor maintenance issues quickly from the desktop, requiring fewer staff members, and more time is available for addressing major problems that may arise, reducing the risk of production outages.
The technology provides ample power for AUV functions and could be scaled up to support larger work vehicles. The system is equipped with a number of on-board communication capabilities, including satellite (Iridium), HF, and Wi-Fi. The stable spar buoy can also accommodate the specialized antennas required to support high-bandwidth systems such as the very small aperture terminal systems used in the Gulf of Mexico.
Electric Tree Power and Control
Electric trees offer the potential for improved control system response and increased reliability compared with similar hydraulically controlled systems. Using the buoy as a power source and control hub potentially avoids a complex and costly subsea umbilical installation.
Currently, electric wellheads obtain power through connections with remote surface infrastructure. Use of the buoy system potentially can lower power delivery cost while maintaining equivalent reliability and safety levels.
To use the buoy system, it must have sufficient power and a margin of safety to provide safe and reliable operation of the electric tree. The tree is mainly a low-power system that operates on a fraction of the power used by a subsea pump. The subsea control module has no moving parts, and intermittent bursts of high power are needed to operate valves.
Changing the power source to the tree does not increase safety concerns. Nonetheless, because the buoy is on the surface, there is some added risk compared with that of a submerged cable. However, up-to-date navigational aids mounted on the buoy and its marked location on marine charts mitigate that risk.
The buoy continuously transmits a “health check” status to operators to alert them of incidents or failures. The buoy is designed to include a high-integrity shutdown mechanism. To ensure that a communications failure does not lead to a buoy power failure, the buoy has a failsafe closure signal that will be transmitted to the tree if a reset signal is not received from the control center within every 4-hour period.
Diesel Power Replacement
Diesel generators are the most common source of electrical power in the offshore operations market, but their use comes at a price for the fuel and its delivery to the facility. To meet the needs of an unstaffed platform with PowerBuoy technology requires the PB40 system. The system, which delivers 40 kW of power and can be scaled up to deliver 80kW, is being prepared for a trial off the north coast of Spain as part of the Waveport project funded through European Commission’s FP-7 research and development program.
The buoy system can connect to a platform’s uninterruptable power supply by means of an underwater cable to supply power that will support diesel generators and thereby significantly reduce operational costs. The resulting dual power source
- Greatly reduces diesel generator use and fuel consumption, extending generator life.
- Reduces maintenance and the associated staff needs, transportation, and operational downtime.
- Increases the redundancy and enhances the safety of the power system.
- Reduces the environmental impact of platform operations.
As the technology evolves, larger systems being planned could further reduce or eliminate diesel generator use and reduce capital and operating expense, which could especially benefit marginal production facilities.