The complete paper describes the development of a smart robotic inspection system for noncontact condition monitoring and fault detection in buried pipelines. Steered by a pipe locator, the smart robot, called an autonomous ground vehicle (AGV), can autonomously track the buried pipeline and simultaneously inspect it externally with a metal magnetic memory (MMM) sensor. The smart robotic system is designed to overcome the shortcomings of both manual external inspection and noninvasive magnetometric diagnosis (NIMD), making pipeline inspection safer, more efficient, and less expensive.
Introduction
Condition monitoring and defect inspection of buried pipelines has been a constant challenge for all oil and gas operations. Maintaining safety and prolonging the service life of ferrous metal pipelines that are exposed to harsh operating environments and damage from corrosion, erosion, and cracking requires regular inspection to diagnose existing or potential defects.
Pipelines can be inspected in two ways: internally and externally.
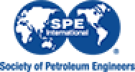