SPE’s recent Liquids-Rich Basins Conference rewarded attendees with far-reaching insight into how to economically exploit liquids-rich plays. Based on the theme “New Technology for Old Plays,” SPE held the conference in Midland, Texas, from 11 to 12 September. The 29 speakers explored a wide range of topics and points of view from macro to detailed perspectives, centered on strategic thinking; current understanding of reservoir characteristics; proper application of completion, stimulation, and production techniques and tactics; and case histories.
This is the third year the conference has been presented. Almost 300 attendees gathered at the Midland Convention Center to listen to four technical sessions—each with three speakers—each day; interact with four Knowledge-Sharing Poster speakers who presented during four half-hour breaks; hear a keynote speaker at Thursday’s luncheon; and investigate the offerings of more than 20 exhibitors.
Two training courses were also given—a 2-day course Monday and Tuesday, 9 and 10 September, titled “Modern Production Data Analysis for Unconventional Reservoirs”; and a 1-day course Friday, 13 September, titled “An Overview of Microseismic Imaging of Hydraulic Fracturing.”
Thinking Strategically
The first session highlighted commercial and financial interests in oil resource plays and price pressures imposed by limited transportation in the areas of rapid development.
Crude and Liquids Growth in the US
Dave Pursell, managing director of Tudor Pickering Holt, kicked off the conference with his presentation, “US Crude Oil Production Growth and the Impact on Price Differentials… or Get Me off This Rock!” “‘Liquids-rich’ is my least favorite term,” he said. “It’s as accurate as calling a dog a non-cat.”
Basically, he said further, what people are talking about is natural-gas liquids (NGLs): “If it’s crude, they’re going to say it.”
When considering the question of why Brent crude is at USD 110/bbl, he said, “Risk premium is the last possible answer before the shoulder shrug.” He assured the audience that global crude fundamentals are fine, with crude inventories pointing to a balanced global market and global refined inventories below 10-year norms.
The big story is taking place in the US.
While US crude production has grown from around 7 million B/D in 2005 to around 9 million B/D in 2012, non-US, non-Organization of Petroleum Exporting Countries’ (OPEC) crude production during the same period has remained fairly stagnant at around 44 million B/D. Organisation for Economic Cooperation and Development (OECD) countries’ demand, which hovered at around 50 million B/D from 2000 to 2007, has tapered down to around 46 million B/D in 2012 and non-OECD demand has grown precipitously from less than 30 million B/D in 2000 to close to 45 million B/D in 2012.
“When considering global growth,” said Pursell, “it is really important to note that the only real growth in crude production is happening in the US.” He cited the resource triangle (Fig. 1), which illustrates that smaller volumes of high- to medium-quality resources are in hard-to-find but easy-to-produce conventional reservoirs and larger volumes of easy-to-find but hard-to–produce resources are found in unconventional reservoirs. Higher resource prices, along with improved technology, enable production of unconventionals.
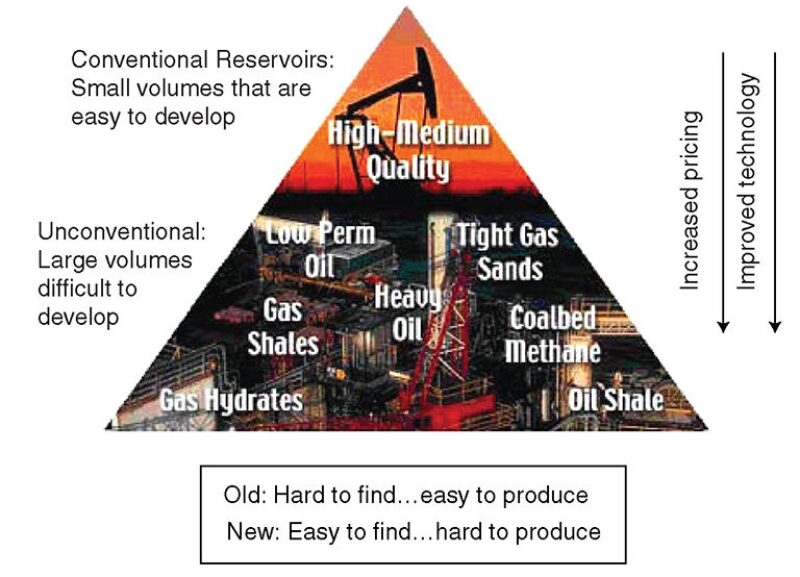
US onshore oil production is driving growth in the US, with production steady at around 3.0 million B/D from 2005 through the latter half of 2010, then skyrocketing to well over 5.5 million B/D by the first part of this year. Driving growth in 2013 is oil supply emanating from the Eagle Ford and Bakken shales, with significant contribution from Permian Basin plays. The US Gulf of Mexico represents only a tiny sliver of overall US oil supply growth.
US NGL production follows a similar growth pattern, taking off in the latter part of 2009 from a relatively steady 1.8 million B/D to close to 2.6 million B/D so far in 2013.
Pursell pointed in particular to projected growth in Marcellus and Utica condensate and NGLs. In the Marcellus, “NGL production is expected to ramp up materially over the coming years,” he said, “as operators focus rigs in the wet gas portion of southwest Pennsylvania and West Virginia and processing/takeaway capacity comes on stream.” In Ohio’s Utica, Pursell projected, “Processing bottlenecks have constrained NGL growth but larger facilities are ramping up capacity this year and next, unlocking significant growth potential.”
Following the presentation, a questioner asked “With the price of natural gas so cheap, why is there not a drive to convert cars to gas?” Pursell acknowledged, “The holy grail for gas demand is vehicles,” and that the key to unlocking this potential is using vehicles in fleets that run on compressed natural gas (CNG). He predicts it will be “a long haul to get there.”
When asked whether the industry should be lobbying to export US crude, he replied, “I am confident that won’t happen anytime soon, for political reasons. But,” he added, “we’re just happy we’re getting LNG exports.”
The Pros and Cons of Vertical Integration
Mary S. Van Domelen, senior engineering advisor at Performance Technologies, an affiliate of Chesapeake Energy, spoke on the “Pros and Cons of Vertical Integration”—particularly focusing on fracturing equipment mainly in upstream exploration and production companies. In her talk, she considered the impact such vertical integration has on service and material costs, access to services, and technology offerings.
Van Domelen pointed out that vertically integrated oil and gas companies are nothing new and find their roots in Standard Oil, whose grip on oil production, transport, refining, and marketing was deemed too dominating and was broken up after a 41-year history, in 1911, when the US Supreme Court ruled that Standard was an illegal monopoly. Nonetheless, a number of vertically integrated oil companies subsequently arose, drawing the attention of economists from the 1950s through the 1990s. It was not until the early 2000s—mainly starting in 2010—that vertical integration involving fracturing began.
She cited 10 oil and gas companies that have formed fracturing-related business units: Chesapeake (Performance Technologies), Pioneer Natural Resources (Pioneer Pumping Services), Encana (Bayou Well Services), Endeavour International (Advanced Stimulation Technologies), Lewis Energy (Falcon Completion Services), Liberty Resources (Liberty Oilfield Services), Southwestern Energy (WSN Well Services), Richland Resources (Manek Energy Pressure Pumping), Triangle Petroleum (RockPile Energy Services), and Oasis Petroleum (Oasis Well Services).
Van Domelen listed the benefits that accrued to Pioneer, which captured margins due to secured access to cost–effective fracturing services. Pioneer is able to deploy crews when and where they are needed in various unconventional plays. With, for example, 27 rigs running in the Permian Basin’s Spraberry, “it makes sense for them,” she said. “They don’t have to compete for fracturing dates.”
She reminded the audience that fracturing costs can be one-third of the well cost. Thus, Pioneer is able to buffer fracturing supply and demand price drivers; assure continuity of supply for proppant, chemicals, and equipment; and capture margins otherwise lost to third-party suppliers.
Van Domelen then focused on the benefits gained by Encana Haynesville and Performance Technologies through simplified planning and safe and efficient operations. With “one customer/one service company,” having a dedicated fracturing service assured early entry into the companies’ planning process which led to operational efficiency, cost reductions, and minimized environmental footprint. A limited chemical portfolio is required, she pointed out, and environmental targets are clear.
A third benefit of vertical integration centered on a company’s ability to align common drivers for success. Van Domelen emphasized, “Ownership drives toward ‘best-in-class’ quality, retention of high-quality human assets, and maximized production.” Liberty Oilfield Services, for example, was established because the operator had a unique approach to fracture design and benefited from the intellectual capital of principals who were seasoned industry professionals. With RockPile, Triangle has greater control over its largest cost center and has the ongoing benefit of two spreads that are fully operational 24 hours a day.
An important fourth benefit is the assurance of confidentiality. Vertically integrated companies do not have to give outside service companies access to reservoir data and production results, are assured that fracturing techniques will not be shared with other operators, and can retain high-quality human assets.
Van Domelen summed up the pros and cons of vertical integration:
- One operating company—Pro: High utilization, efficient operations. Con: Limited exposure to new ideas.
- Training programs—Pro: Focused on parent company. Con: Fewer resources available.
- Career progression—Pro: Possibility to move to parent company. Con: Opportunities may be limited.
- Research budgets—Pro: Joint research with parent company. Con: A vertically integrated fracture company has a smaller budget.
Multiwell Facility Optimization
Tyler Farley, project engineer at Halker Consulting, spoke on “Multiwell Facility Optimization in Unconventional Plays.” She pointed to several reasons—including cost savings—multiwell facilities make sense: single, optimal location of physical point of well management and maintenance; significant reduction in time and travel needed to monitor and maintain multiple sites; elimination of redundant equipment through consolidation; increased emissions control and secondary capture through single point of emissions; and decrease in truck traffic.
However, there are several challenges. Exponential production increases, with the changeover from vertical to horizontal wells and multiwell pads, vastly increase the risk to well stakeholders and drive the need for increased safety and risk management. The complexity of facility design therefore increases. “Onshore facilities,” stated Farley, “are quickly adopting offshore characteristics.”
Major hazardous incidents can occur when there are flaws or failures within design, construction, and operations defensive barriers. The barriers, which are intended to provide layers of protection, develop vulnerabilities because perhaps a multiwell facility is
- Not designed to best practices or industry standards, when process hazard analyses are not conducted highlighting unforeseen design flaws
- Installed or welded improperly, or pressure and leak tests have not been performed
- Operationally unfit because personnel are inadequately trained, change management fails, or no mechanical integrity program and standard operating procedures are in place
The US Occupational Safety and Health Administration 1910 safety standards and best practices do not explicitly regulate onshore production facilities. However, Farley asked, “Horizontal facilities have the potential to produce just as much as an offshore platform, so why not use similar standards?”
She said, “When used in a fit-for-purpose way, many offshore safety standards are completely applicable onshore. Simply applying an API [American Petroleum Institute] 14C checklist to an onshore facility provides a minimum level of safety for common upset conditions in a process.”
While companies are still determining the best methods to optimize well production in Bakken, Utica, Marcellus, Permian, and Eagle Ford unconventional plays, Farley said, “Equipment, facilities, and infrastructure are what’s bottlenecking production.”
Focusing on the engineering design process allows companies to identify problems and solutions to them that best suit companies’ goals and needs, as well as work out bugs and improve upon designs once lessons have been learned. “Engineering solutions safely maximize profit,” she said.
“That said, though,” continued Farley, “with all the best facilities money can buy, if there is nowhere to put product, costs and profit can be greatly impacted.” In many fields, therefore, underdeveloped infrastructure needs to be addressed. “Improved infrastructure will have the greatest impact on crude pricing,” she said, “in areas like the Rockies and Midwest, where the cost of shipping is greater due to underdeveloped pipelines and few refineries.”
Farley ended her presentation by saying, “Operating multiwell facilities is still in its infancy. However, please remember that these facilities we work in and around every day have the potential to be very dangerous and unpredictable.”
She recommended that companies invest the upfront capital in sound and safe facility engineering. This in turn will mean “Operators can get ahead of the crowd in increasing their return on investment while ensuring the product remains in the pipe.”
Drilling and Completions
This session’s three speakers explored current techniques, geomechanics, tubulars and downhole equipment, support issues such as fluids and proppant, and logistics.
Developing the Bone Spring in New Mexico
Mitch Abahusayn of K&M Technology Group spoke on “Islands in New Mexico? Surface Area Restrictions Drive Land Islands and Extended-Reach Wells to Develop the Bone Spring.” He explained that New Mexico has been primarily known for its potash mining—basically water-soluble potassium (sylvite) used mostly for fertilizer. “It is a great resource,” he said. “And the state provides the US with 80% of its potash. However, as it is mined from 1,500-ft depths, it restricts access to Permian Basin formations such as the Bone Spring below it.”
The solution Abahusayn pointed to is to drill extended-reach wells, from total vertical depths of around 10,000 ft with laterals to 10,000 ft or more (Fig. 2), from a surface location outside the potash area in order to access the unexploited formations.
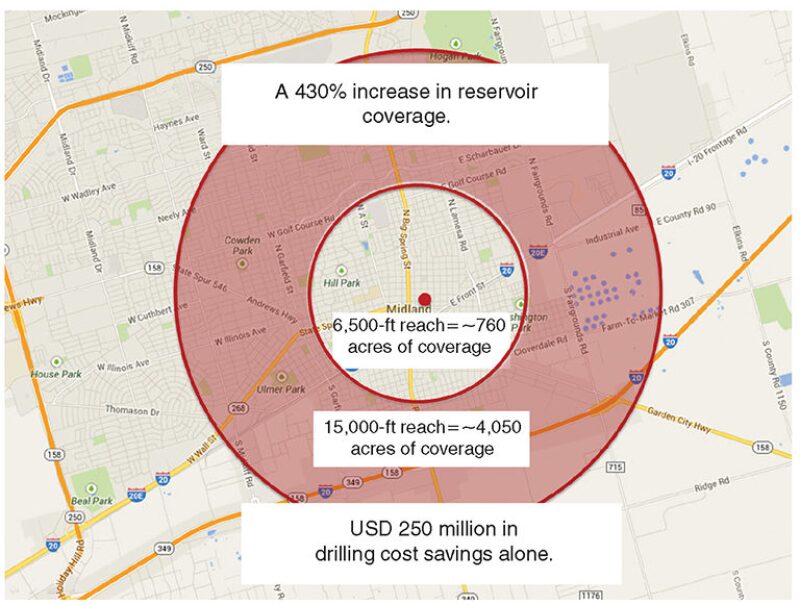
“The technical bottleneck,” he said, “is drag, drag, and drag.”
The challenges include rapid decline in weight when 7-in. casing enters the horizontal, difficulty slide drilling in the 6⅛-in. hole, and lack of weight when running 4½-in. liner. Diagnosing the bottleneck requires torque and drag software. Is the problem just drag overcoming weight in the vertical section; problems with buckling, which can take two forms—sinusoidal (snaky) and helical (coiled)—and is often misdiagnosed; or a combination? It is apparent that high friction and drag limit drilling longer wells. One can either attempt to reduce the friction or accept high friction and design around it.
Abahusayn said two effective ways of reducing drag are reduction of the weight of the pipe laying on the low side of the hole and rotation. Conventional casing runs the risk of not reaching bottom. Therefore, utilizing buoyancy assist to reduce the weight of the bottom 4,500 ft of casing [for example, using 9-pounds-per-foot (ppf) pipe vs. 26-ppf pipe] would be recommended. In the 6⅛-in. section, reaming to bottom will be required. Also, rotating the drillstring, he said, “is the only way to alleviate drag across the entire lateral.”
In the transition from “designing for success to optimization,” Abahusayn predicts potential future bottlenecks would be the torque limit of the 4-in. high-torque drillpipe and limits in equivalent circulating density as reach is extended.
Horizontal Wells and Produced Water Recycling
“Horizontal wells are exciting!” exclaimed the next speaker, Rob Clark of ConocoPhillips. “They’ve reinvigorated the oil and gas industry, allowing us to reach formerly inaccessible zones we knew were there.” His topic was “Horizontal Well Completions for Accessing Tight Liquids-Rich Reservoirs and Produced Water Recycle for Hydraulic Fracturing.”
However, he cautioned that one cannot effectively stimulate open hole. Lined completions should thus be considered one of the tools of the trade. In stimulation design, he said, “Plan, plan, and plan again. Consider all the questions that need to be asked.” These include all the bits of information regarding reservoir, rock, and fracture properties. For a fracture model, he recommends a 3D simulator.
The volumes of water required for hydraulic fracturing appear massive. However, according to Clark, even with several thousand unconventional wells being fractured in the US each year, the oil and gas industry uses less than 1% of all water used by industries. The push to recycle water stems from the desire to reduce or eliminate truck traffic. “A very good solution,” stated Clark, “is large, above-ground water storage tanks. These offer an alternative to earthen pits.” A big proponent of recycling, he said that storage tanks can eliminate an estimated 342 trucks annually from the road.
The use of recycled water dovetails with future completions technologies, including multipad field development; simultaneous operations; simultaneous, sequential, and so-called “zipper” fracturing; the use of lower-viscosity fluids; the use of more fracturing stages; using shorter laterals; and using ultralong laterals.
In asking the question, “What can we do with horizontal wells?” Clark gave a Bakken development scenario in which a lot of different horizons were targeted. If the well is planned enough in advance, one can be assured of obtaining enough produced water to use in fracturing; a certain density of wells would be needed for enough produced water. Using produced water assures better compatibility with the formation, he said. And less volume of fracturing chemicals is needed when using the water capacity that is there.
He pointed out that one does not have to get drinking-quality water, and that using a simple filtration system would be adequate. He predicted that sliding sleeves will predominate in the future. In addition, various types of dissolvable balls used with hydraulic fracturing are affordable and more reliable, said Clark.
Drilling Geomechanics in the Wolfcamp
“Operators have serious problems drilling horizontal wells in the Wolfcamp and Cline formations in west Texas,” said the next speaker, Goke Akinniranye, of K&M Technology Group. His topic was “A New Approach to Using Drilling Geomechanics to Solve Complex Horizontal Drilling Problems: A Wolfcamp Case Study.”
His conclusion was that the majority of problems are due to wellbore stability issues. Using the synergy generated by a combination of drilling engineering and geomechanics is the best way to identify root causes of problems and make recommendations, he said. In planning a well, when drilling engineering also works with geomechanics, correct calculation of allowable damage before roof collapse becomes high-risk can be determined using risk-based rock mechanics. “This gives drillers a ‘severity of failure,’” said Akinniranye, “when wellbore stability modeling is performed.”
Integrated Monitoring Methods
Various technologies for evaluating reservoir, formation, and microseismic fracture events were examined next.
Distributed Temperature Sensing and Fracture Diagnosis
Kyle Friehauf, senior completions engineer at ConocoPhillips, talked about the use of distributed temperature sensing (DTS) as a way to get information about fractures. In reviewing more traditional methods of fracture identification, he mentioned radioactive proppant tracers; various non-unique solutions such as step-down tests (pressure diagnostics), microseismic, fracture modeling, and production modeling; and permanent DTS, which can determine residual fracture cooling over a significant amount of time.
The key, he said, is to keep an accurate time log from fracture time in order to diagnose the fractures. “It warms back faster where it’s not at the fracture clusters,” said Friehauf. “If a perforating cluster didn’t have a fracture, its temperature would be closer to borehole temperature.”
According to Friehauf, “Using temperature to identify hydraulic fractures is an old idea.”
The new idea centers around the long amount of time that residual cooling effects remain. “We can wait a lot of time and still get the same information,” he said. “Even after producing the well, we can still get fracture information.”
This approach, he pointed out, can be used in a liquids-rich environment, and a permanent system will answer a lot more questions. “Right now, however,” Friehauf stated, “the interpretation data is not there. We’ll be doing more things with the data in the future.”
Well Performance in the Lower Eagle Ford
Using data generated in four wells drilled in the Lower Eagle Ford in south Texas, Paul McGeer of Marathon Oil looked at how fault systems affect well performance. The reason for the analysis, he said, was that the wells’ 90-day cumulative production was only 50% compared to other local wells. They wanted to understand why.
Marathon tested using microseismic on two of the wells and a chemical tracer on the other two wells—with all tests telling the same story. In well performance, it appears, the orientation of the wellbore is critical. Having it perpendicular to the fault appears to be important. A key question to ask, he said, is “If you cross over a fault, will your stresses remain the same?”
One will not always have the luxury of large amounts of data like that generated about the four wells Marathon studied, said McGeer. But one should always keep in mind, “Are you propping fractures that are open anyway?” he said.
Microseismic Volume
Shawn Maxwell of Schlumberger Canada discussed “Microseismic Volume: Stimulated, Propped, or Effective?” In microseismic hydraulic fracture interpretation, he said, one must consider the following:
- Fracture geometry
- Microseismic deformation, including fracture orientation and mode of failure
- Determining the fracture deformation
- Determining what portion of the fracture is effective, in terms of well performance/production, reservoir drainage, and well spacing
Maxwell presented simulated reservoir volumes based on a dual-porosity model. “You’re always going to overstate the microseismic volume,” he said. “The holy grail is, even with an incomplete picture, to get an understanding of where the proppant is settling within that.”
He emphasized, “Microseismic provides geometry (location and mechanism), but microseismic does not detect all deformation.”
However, proposed Maxwell, “Microseismic calibration of the geomechanical deformation during hydraulic fracturing can be used to assess the fracture effectiveness.” This is achieved by using microseismic deformation to calibrate the corresponding component of geomechanical deformation. “Geomechanics can then be used to simulate the aseismic deformation,” he said. “This enables reservoir simulation and optimization of well performance.”
Play by Play
A total of six presenters in sessions 4 and 5 of the conference provided introductions to developing new liquids-rich plays, with a focus on issues related to effective exploitation.
The Wolfberry
Greg Hinterlong of Chevron talked about the Wolfberry—a commingling of the Spraberry and Wolfcamp formations in the Midland basin, which is part of the Permian Basin. The Spraberry was discovered in 1943, with commercial drilling beginning in 1948 and commercial production reached in January 1949.
To add background to Hinterlong’s presentation, in the February 2013 issue of JPT one can find a series of articles titled “Tight Resources, Promising Economics: The Permian Basin Continues Yielding Liquid Riches,” which addresses in considerable detail the history and current status of the Spraberry trend and the various Wolfcamp plays. In addition, in that article several SPE papers are discussed that follow the development of the use of hydraulic or acid fracturing and both vertical and horizontal drilling of these trends.
After considering optimal well spacing, Hinterlong discussed when horizontal wells would be the best choice:
- When the number of pay zones is reduced
- When the recovery factor or drainage area for the target zone is very low
- When other pay zones have already been depleted through historical production
Once the decision has been made to drill horizontally, several factors need to be considered:
- Where to land the horizontal, considering highest HIP, mechanical properties, and total organic carbon content
- How much could be left behind or stranded below the zone
- The effect of previous production on depleting portions of the interval
- Direction of the horizontal path
Hinterlong shared the following insight: “Because the hydraulic fracture propagation length will vary with each zone based on the mechanical properties, a map view picture of the drainage radius can give a very misleading impression of the recovery. In areas where this variation is extreme, the drilling of horizontal wells to an area with vertical wells in pattern could lead to improved recovery from the interval.”
He pointed out, “Exceptional lateral length (7,000+ ft) has had limited application in the Midland basin mostly due to mineral ownership issues. A few examples are being watched closely.”
“Originally envisioned as a vertical well play,” concluded Hinterlong, “the [expanded Spraberry/Wolfberry] trend now is toward a combination of vertical and horizontal wells in proximity, maximizing the recovery from this highly stratified reservoir.”
He cautioned attendees by quoting Bryant Fulk, a geologist at Chevron, “Geology sets the ceiling but stimulation sets the floor. You don’t get P90 rates from a P10 reservoir, but you can get P10 rates from a P90 reservoir.”
The Bakken and Eagle Ford
The next speaker, Bob Shelley, petroleum engineer at StrataGen, presented the topic “Completions Optimization in Liquids-Rich Plays: Bakken and Eagle Ford Case Histories.” “Completion and fracture optimization requires a predictive model,” he stated.
He referenced SPE paper 133985 in a discussion of two very different modeling processes—discrete and single-well (data-driven) modeling. In discrete modeling, one’s assumptions totally dictate the results; in data-driven modeling, one quantifies through experience and integrates data. The latter approach is more flexible on data requirements and can be adapted to use available data, according to Shelley.
He explained the benefits of using the data-driven predictive neural network modeling process in several Bakken and Eagle Ford wells. Shelley showed the effects of a Bakken model on a number of best practices. These effects were largely positive, both on controllable completion and fracture parameters—such as number of fracture treatments, proppant, staging method and perforating, treatment type, lateral length, and treatment volume—and on noncontrollable reservoir-related parameters—such as butane, total gas, methane, and drilling mud weight. Use of the model substantively affected an optimized new well completion, exceeding production expectations, and reducing completion and fracturing cost by USD 2 million. He presented similar models for Eagle Ford oil and gas wells.
Shelley concluded, “Contact and conductivity are the primary controllable drivers that affect production from liquids-rich shale plays.” He added, “There is useful information for completion optimization that can be readily measured during drilling operations. These include geochemical, light/heavy ratio, gas wetness, gas, rate of penetration, mud weight, and many other parameters.
He cautioned, “A completion/fracture in liquids-rich shale requires a different fracture design than for shale gas.”
The Bone Spring Play
Josh Walker of Chesapeake Energy spoke next on the Bone Spring play in the Texas Bend, covering the story of the company’s Bone Spring fracture design—from initial plan to lessons learned.
Chesapeake was targeting three main sand bodies—the B, D, and Wolfcamp, each 12 to 15 ft thick—separated by 60 to 80 ft of shale. “All indications were that the shale should be a significant contributor,” said Walker. “But we were wrong. It turned out we were just in a really good area.”
The debate centered around the question, “What and when is the shale contributing?”
In resolving the debate through trial and error, there were some key lessons learned:
- Go big first. See what the well is capable of producing. You cannot risk killing a play due to cost concerns on well #1.
- Go small early. (But don’t go too small or they’ll underperform.) Make the design changes dramatic—you need definitive results.
- Realize that you might be wrong, and be OK with it. Don’t try to get the results that justify your initial theory.
The Upper Avalon
Jan Schmidt, project reservoir advisor at Anadarko Petroleum, spoke about “Upper Avalon Spacing and Completion Design Evolution.” Schmidt described Anadarko’s Avalon spacing tests at 500 ft, 700 ft, 1,420 ft (Fig. 3). After extensive analysis of the tests, Anadarko found that with 1,420-ft spacing, there was no evident production interference and the wells were the best producers in the field.
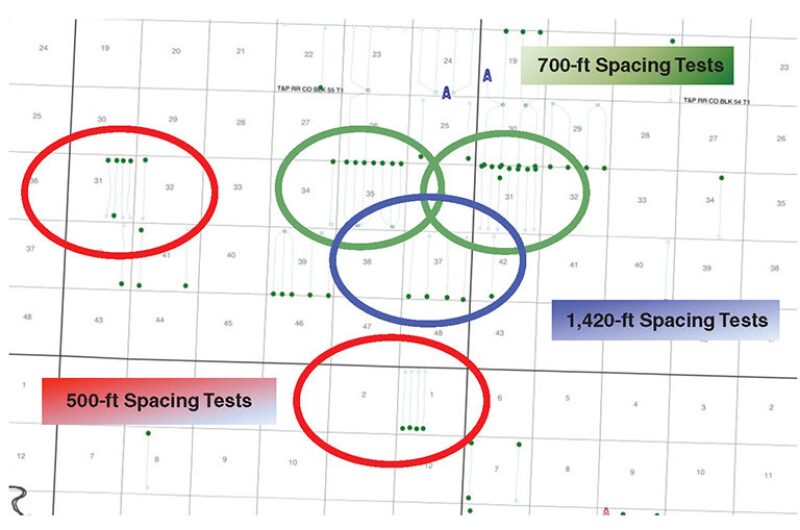
Schmidt pointed out several observations resulting from the spacing tests:
- Completion size affects spacing.
- Denser spacing may lead to rate acceleration.
- Pressure surveys and microseismic improve understanding of inter-well communication.
- Based on early observations, optimal spacing appears to be between 700 and 1,400 ft.
Regarding Avalon completion evolution and fracture design, Schmidt discussed some completion tests. The tests resulted in several observations:
- Bigger is better—up to a point.
- Higher sand concentrations improve economic ultimate recovery (EUR).
- A higher number of stages indicate better overall EUR.
- An optimal fracture design is achieved when economic indicators are maximized.
“The Avalon continues to evolve,” concluded Schmidt. “Future spacing tests will likely tend towards 1,000 ft. Larger slickwater fracture jobs have yielded the best results. We seek cost optimization while retaining well performance.”The Lower Marmaton, Anadarko Basin
Chris Jamerson, drilling engineer at Apache, presented on a “Lower Marmaton Sand Case Study.” In filling out its acreage position in the Anadarko basin, Apache closed its purchase of 254,000 net mineral acres in Oklahoma from Cordillera on 1 May 2012. One of the key formations targeted in that acreage was the Lower Marmaton, located below the Oswego and above the Granite Wash at a depth of around 9,300 ft. Several wells had previously been drilled in the area—for wildly differing costs, from USD 4.2 million to USD 13.7 million.
Jamerson was handed a rig and told to go to the area and investigate. He had a week. “Something was going on with the previous wells,” he said. In investigating the previous well designs, they discovered evidence of small flat, sharp shards of shale in one well and stuck casing in another. Apache did an analysis to come up with the optimal mud weight prediction.
Apache started out by learning lessons on two wells. On the first well—Merrett #1-28HA—they were tripping every other day due to bit wear, but the conservative casing design worked. With a 4,023-ft lateral, it was drilled in 74 days at a cost of USD 7 million. The schedule they had developed for weighting up the mud was established and it worked. Drilling the lateral was often painfully slow, however.
On the second well—Frank #1-34HA—some changes were made, but drilling the 3,450-ft lateral was still slow. It took 87 days at a cost of USD 8 million.
Two more wells were drilled, and results did not improve.
After that, Apache did a major design change. They reduced production casing to 4.5 in., eliminated one casing string, drilled standard sizes, and still saw the need for using high mud weights. They decided to drill 3 ft below the pay zone. The company achieved good results, reducing the average drilling time to 44 days and cost to USD 4.1 million. The wells experienced a 48% reduction in cost with 20% more pay.
Several more challenges lie ahead, such as higher pay zone pressures, the need to reexamine fracturing techniques and workovers, and a possible casing revamp to 5.5-in. production casing. In the wells Apache drilled, after starting with a good plan from Cordillera, a geomechanics review reduced issues with pressure and trajectory, mud weight, and overpressure in the Deese shale. “We had science behind us,” said Jamerson. “But if it’s not in the real world, it doesn’t mean anything.”
The key lessons learned, Jamerson concluded, were: “Overly safe designs lead to slow wells. And cheat and drill to the next pay zone if you can.”
The Wattenberg Field, DJ Basin
Tommy W. Thompson, of Anadarko Petroleum, focused on “Unconventional Play Development and Horizontal Drilling Revitalize a Mature Field (DJ Basin—Wattenberg Field).”
Discovered in 1970, the Wattenberg field currently has more than 15,000 producing vertical wells, developed primarily on 20-acre spacing. Thompson explored a recently emerging opportunity—around 350,000 net acres in the core Wattenberg area, with a 1.0- to 1.5-billion-BOE net resource, the possibility of around 4,000 horizontal well sites, each with an EUR of around 350,000 BOE.
Anadarko considered several key technical questions:
- Well spacing
- Horizontally and vertically, by type curve area
- Importance of steering
- Reservoir quality
- Prioritization within the field
- Productivity drivers
- Role of API gravity, rock quality, faulting
- Completions design
- Stage density, fluid system, packers vs. plug-and-perf, job size
- Wellbore geometry
- Lateral length, azimuth, toe up/toe down, porpoise effect
- Operational efficiencies
- Costs, cycle times, infrastructure
- Simultaneous operations (known as SIMOPS)
- Field operations
- Artificial lift
- Choke management
- Facilities optimization, infrastructure
The formation is highly fractured. Anadarko faced drilling in urban areas—near shopping centers, for example. “We spent a lot of time developing a work plan,” said Thompson. “It’s Colorado. How do we communicate with landowners, state and local government, and municipalities? The things you have to do going into a mature field are just like going into a green field.”
Of particular importance are the advantages of expanding infrastructure. Around 45,000 truck trips were eliminated because 7.5 million bbl of oil has been gathered to date via lease automatic custody transfer (LACT) units and pipeline. Around 230,000 truck trips were eliminated due to reliance on around 50 miles of water distribution pipelines that delivered 30 million bbl of water to date. Around 2,000 offset wells were investigated and around 750 interventions performed to date. There is an ongoing water sampling program (baseline and follow-up).
Two key results are that gas processing capacity is aligned with production growth and oil takeaway capacity is aligned with production growth. Several challenges remain, how-ever, including noise mitigation, traffic, infrastructure, takeaway capacity, visual impact, rig fleet optimization, and cycle time reductions.
Of the continuing operational challenges, Thompson said, “You have to snake wells. The opportunity for a straight wellbore doesn’t exist in this field. If you have no other option, then you try to optimize.”
Artificial Lift
This session addressed multiphase-flow issues and flow assurance, from first production through well mid-life and beyond.
The Life Cycle of a Shale Horizontal Well
Keith Stevens, production engineer at Anadarko, discussed artificial lift in the Wattenberg field. The Niobrara formation, targeted in the Wattenberg, is organically rich, consisting of marine deposits with multiple strata of chalks and marls and minimal water.
With vertical beginnings in the 1970s, a lot of pads, which use smaller, low-profile equipment, were drilled, posing complexities for artificial lift. Anadarko added the Niobrara in the 1990s, and in the 2000s, refractured and redrilled horizontal wells, putting the infrastructure to the test. “We were pushing the pumping units to the limits for gas,” said Stevens. “After 4 months, the wells started decreasing in productivity. Finding the transition before it happens will help in cash flow.”
Anadarko decided to use plunger lift, which, in a high-pressure scenario, said Stevens, can be used continuously with minimal offtime, can increase oil production, and can optimize the speed to get maximal plunger efficiency. “We were using gas to effectively offload our oil,” he said.
After installing the first pumping unit about a year and a half ago, gas production is the biggest issue. A pumping unit gas anchor, consisting of a dip tube inside of tubing set below the pump intake, motivates the gas to travel to the lower-pressure annulus. A pumping unit gas separator was also installed to separate gas and liquid. Also, a hydraulic rod pump was installed. “Tighter tolerances in the pump help,” said Stevens. “We need a little more experience, but the surface equipment is safer and looks better.”
“Gas separation poses the biggest issues to rod pumping in the Wattenberg area,” concluded Stevens. “Sand wearing out the inside of the pumps is the biggest problem. It’s a gas field that’s becoming an oil field.”
ESP Design and Operation in the Permian Basin
In discussing electric submersible pumps (ESPs), Caleb Conrad of Baker Hughes emphasized, “The bottom line reason for operational changes in artificial lift strategy is to improve recovery.” In horizontal plays, he pointed to a possible production strategy. First, install a large ESP (2,500 or more B/D) above the kickoff point (KOP); this maximizes early production and cash flow. Second, install a small ESP (500 or less B/D) below the KOP; this achieves the lowest bottomhole pressure.
The company conducted a 3-year net present value comparison between an ESP just installed above the KOP, the ESP mixed installation (above and below the KOP), and rod lift. The first two options performed markedly better than rod lift; and the second option performed noticeably better than option one. “If the lateral section is worth it,” said Conrad, “one should look at the cost analysis.”
“The critical technical component,” he explained, “is the temperature/pressure sensor at the bottom of the ESP on top of the motor.”
In vertical plays, such as Wolfberry, Wolffork, and Bone Spring recompletes, perforated intervals can reach 3,000 ft or more as different formations are targeted. Setting the ESP artificial lift at greater depth—say, at 8,700 ft (Middle Wolfcamp) rather than 6,700 ft (Upper Spraberry)—can produce considerably improved production, moving from 10 B/D to 500 or more B/D, with sustained production over 100 B/D.
Conrad cautioned that one should develop a strong chemical program and monitor residuals. He strongly recommends using direct chemical treatment at the ESP using capillary tubing (CT line). “It is not uncommon for ESPs to scale up in a week due to commingling of reservoir fluids if not treated properly,” he said.
He concluded that ESPs improve economics by providing higher initial production rates, have proven capable of handling high gas rates, and are capable of operating below the perforations. Effective chemical treatment is a must, Conrad said, and in horizontal wells, sand separation is a must.
Horizontal Well Deliquification and Liquid Loading Implications
Omar Soto, senior petroleum engineer at BP, introduced his topic by giving a brief history of horizontal drilling. “The first recorded true horizontal oil well, drilled near Texon, Texas, was completed in 1929,” according to Soto. “Another was drilled in 1944 in the Franklin heavy oil field, Venango County, Pennsylvania, at a depth of 500 ft. China tried horizontal drilling as early as 1957, and later the Soviet Union tried the technique. Generally, however, little practical applications occurred until the early 1980s, by which time the advent of improved downhole drilling motors and the invention of other necessary supporting equipment, materials, and technologies, particularly downhole telemetry equipment, had brought some kinds of applications within the imaginable realm of commercial viability.”
In asking the question, “Are we drilling more complicated wells?” Soto pointed out that wells are demanding more and more technology to drain ultimate reserves, and that conventional artificial-lift methods have to evolve to meet well completion and production targets.
“Flow regime is very important,” he said. “In horizontal wells, flow pattern prediction is key.”
At the University of Tulsa (TU), the TU Fluid Flow Projects (TUFFP) operates as a cooperative industry-university research group supported by several oil and gas production, consulting, and service member companies, and government agencies. TUFFP’s mission is to conduct applied research and develop solutions for problems encountered by the member companies pertaining to multiphase fluid flow in pipes. TUFFP has a flow patterns prediction model. According to Soto, some real-world wells were set up. An important aspect was the strategy for deliquification. First, surveillance of physical changes in the lateral needed to be set up, then the plunger lift and gas lift were implemented. Production logging tools were deployed using coiled tubing.
“Water deliquification in the lateral is all about velocity,” said Soto. He discussed several experiences deliquifying horizontals in the Woodford and Eagle Ford, and the Anadarko basin.
In his conclusions, he emphasized, “The differential in elevation from toe to heel in toe-down wells makes the difference regarding liquids movement. Toe-up vs. toe-down may not be important for now, but the elevation from toe to heel could be the answer as to how the well will behave.”
Keynote Talk: Even Wimps Can Double Well Productivity
Mike Vincent, a consulting engineer with Insight Consulting, gave a provocative and extensively researched keynote presentation at the conference luncheon held Thursday. He cited several SPE papers in his pursuit of the question: What really happens downhole with induced fractures?
He concluded that hydraulic fracturing is the premier way to touch rock. But, he said, “We look like heroes even with poorly designed fractures.” Are the fractures optimized? “Not even close,” he said. “Perhaps 90% of the created fracture volume is ineffective?”
One should infill drill or improve fracture effectiveness, he suggested. “Field results demonstrate there is a large potential to improve well productivity and profitability,” Vincent said.
In the coming revolution, he said, “If we can merely double the productivity and EUR of stimulated wells, there are enormous implications for global reserves.” However, he said, “Merely doubling well productivity via fracture optimization is a cowardly goal.”
Vincent said, “We should instead strive for 5- to 10-fold improvements in EUR, recovering vastly larger reserves per well, reducing required well count, and capturing another level of the resource pyramid.”
One commenter aptly responded to Vincent’s presentation by referring to a central idea of Thomas Kuhn’s 1962 book, The Structure of Scientific Revolutions: “One can be so locked in a paradigm,” paraphrased the commenter, “that it turns out it’s the paradigm that’s wrong.”
Tactics and Equipment
Access to critical services has become challenging for large and small operators alike. In this session, operations strategies were discussed to reduce delays, equipment wear and tear, and how improvements influence performance.
Electrical Power Planning in the Permian Basin
Coleman Lewis, senior energy analyst at Pioneer Natural Resources, presented a number of conclusions at the end of his presentation:
- Congestion is a significant cost factor for many businesses in west Texas, including the oil and gas business.
- Implementation of the competitive renewable energy zone (known as CREZ) lines should help relieve congestion, but the increasing load growth and the inability of utilities to keep pace is a significant issue.
- Congestion revenue rights, which are hedges purchased at Electric Reliability Council of Texas (a nonprofit managing the grid, known colloquially as ERCOT) auctions, are available but are generally only purchased by large companies and are not always the best solution to mitigate congestion exposure risk.
- The best strategy is for companies to report load growth forecasts to the utility companies in order to help them predict where to build new power lines.
Validating Casing Integrity Unconventionally
Sean Canning, global product champion at Halliburton, said that the main challenge was to enable a true casing pressure integrity test and stage fracturing while at the same time improving completion economics in unconventional resources. “This means quicker time to production,” he said, “and reduction of the work required.”
The proposed technology is one tool with a pressure-actuated toe sleeve, a pressure-test sleeve, and a fracture sleeve. Canning pointed out that the technology will validate casing integrity prior to the beginning of the fracture program; its 30-minute time range metering process offers a casing pressure test window; and it is an interventionless means of establishing flow path from the ID of the liner/casing to the reservoir. It has an opening force of more than 25,000 lb.
The tool will work in cemented multistage fracture sleeve completions, openhole multistage fracture sleeve completions, plug-and-perf completions, and zipper-fracture completions. It has a proven design using field-proven technologies. It mitigates risk in that it does not require running, testing, or retrieving the plug; it does not require coiled tubing or wireline toe preparation; and it does not require additional completion equipment to acquire a pre-fracture casing test. Canning said the tool appears to address the challenge he cited at the start of his presentation by eliminating intervention with coiled tubing or wireline and by improving wellbore economics.
Navigating the Proppant Market
Earl R. Freeman, founder and owner of PropTester, Inc., first gave an overview of how the use of proppant has grown since Arkansas River sand was used in 1947 on the first well that was hydraulically fractured to increase well productivity in the Hugoton field, Kansas. Thirty years later, there were three primary sand companies performing 98% of the completions, one ceramic company using sintered bauxite, and two resin-coating companies.
Today, there are 60 sand companies, 90% of which are in North America; 47 ceramic companies, 40 of which are in the Eastern Hemisphere; and 18 resin-coating companies, with 11 in North America and the rest elsewhere. The proppant market has grown from around 10 billion lb in 2003 to around 70 billion lb in 2012 (Fig. 4). Some companies, like Pioneer Natural Resources, have a linear supply chain, providing their own proppant and pumping services.
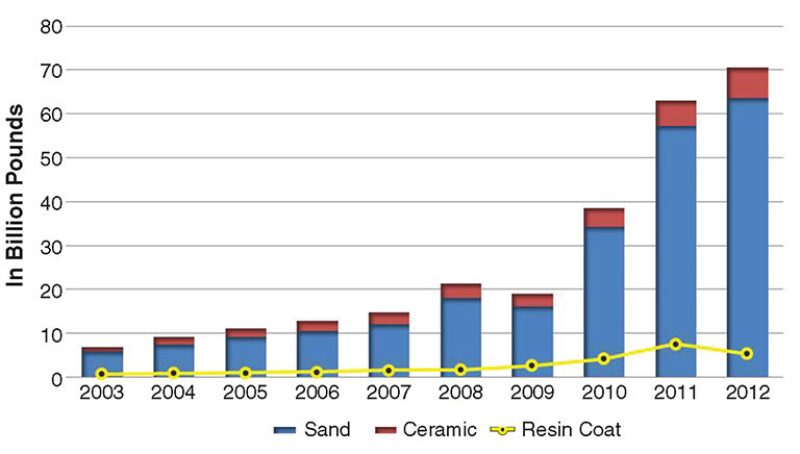
Freeman noted that two key questions need to be answered:
- Is my delivered proppant what I expect in terms of performance and value?
- Does the delivered proppant meet “minimum reservoir requirements” for unrestricted fracture flow capacity?
He pointed to four basic steps to achieve the answers and went into considerable detail in explaining the logistics of each step:
- Test—Apply testing standards.
- Reference—Use reference data.
- Track—Track movement of material through the supply chain; should be able to account for every pound.
- Review—Review the history of the supply chain to make sure we get what we invested in.
Freeman stressed that throughout each stage, one should encounter consistency, with legible shipping documents, minimal substitutions, expected properties, and expected performance.
The future, he said, includes advancements in nanotechnology, resin technology, chemical delivery systems, flowback control systems, placement design and detections, and storage and transportation.