The positive feelings experienced by those in the upstream oil and gas industry during 2018 faded into a familiar uneasiness in 2019.
Commodity prices declined last year and share prices continued their half-decade-long fall in yet another reminder of the uncertainty that comes with working in the industry. While the previous 2 years were seen as a recovery from a generational oil-price downturn, last year marked a wholesale shift in how operators approach the business. A movement toward financial discipline over growth has impacted work all the way down the supply chain and affected every aspect of the upstream space, particularly in North America.
The goal for the industry is to ensure more stability in the business and operations amid the typical fluctuations in commodity prices. This will come with better efficiencies and lower costs, which will be accelerated by the application of new technologies and work flows. It will also come against the backdrop of a drive toward sustainability, with the industry working to eliminate its environmental impact to ensure its long-term survival.
To meet these challenges in the coming years, it is unanimous among SPE technical directors—each of whom has their own unique perspective forged from decades of work experience in their discipline—that the traditionally fragmented industry must become more integrated and collaborative. A primary solution to breaking down those barriers: the continued evolution and adoption of digital technologies.
Here, the six directors share their outlooks for the next several years for the disciplines they lead: Data Science and Engineering Analytics (formerly Management and Information); Drilling; Completions; Health, Safety, Environment, and Sustainability; Production and Facilities; and Reservoir.
Birol Dindoruk, Data Science and Engineering Analytics (formerly Management and Information)
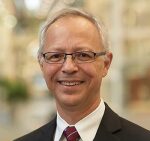
Digital and data-driven technologies now pervade the industry, and the transformation will be reflected in the impending split of Management and Information: Management will have its own discipline and Information will become Data Science and Engineering Analytics (DSEA). Dindoruk, previously director of Management and Information, will serve as director of DSEA.
The creation of DSEA comes as these technologies rapidly evolve. The move seeks to aid adoption across the industry by promoting learning and discussion among engineers, petrotechnical professionals, and data scientists, each of whom will need to ensure their skills and knowledge advance with their changing roles.
In the near-term future, Dindoruk expects more standardization of data as the industry continues to cull more structured or legacy data. Sensor data will be scaled down and commoditized to ensure broader uptake, leading to bigger digital exhaust, which will bring new challenges in managing and using that volume of data. Computational techniques will become more hybrid and data driven. And virtual experimentation will emerge as a new domain.
In a more specific example of things to come, Dindoruk believes integrated field management will resemble an artificial nervous system in which the nerves will be the Internet of Things and sensors and central nervous system will be the computational power with domain-related checks and balances. “And we will have the option to have that brain talk to other brains—and the other brains might even be our competitor because it’s going to drive the synergies for both entities,” he said. Collaboration will be a primary outcome and facilitator of the industry’s digital transformation.
Work flows will be more consolidated and integrated, a departure from the current status quo according to discipline, de-facto norms dictated by software, or the way things have always been done, he said. Organizations will have to break down traditional work flow-deadline mandated “compartments” through a fundamental change in their culture while addressing contrasting views of how digital technologies will affect employees’ work: Will those technologies solve every problem, or will they take away my job? The answer to both, Dindoruk said, is “no.”
That is because the one thing machines lack is human creativity. “I’m not afraid of machines because they are not creative—at least for the foreseeable future,” he said. When it comes to the next enabling technology, “somebody will imagine that.”
As it stands now, petrotechnical software is not integrated enough, and that will need to improve. He noted that when he runs a reservoir simulator, “it has no idea what the drilling people did, but in fact, it may have very important information in it that I can use to my advantage. But even if I want to, I can’t do it today, at least in a just-in-time basis.” Dindoruk believes “data will bring that dimensionality into the picture and force classical software makers, or the school of thought as a whole, to comply.”
The education of engineers and petrotechnical professionals will progress in that universities will ensure students graduate knowing how to select and utilize the right digital tools to improve work in their field of study, he said. But it is even more important for students to learn how to ask the right questions when attempting to solve a problem, which in turn will enable them to properly leverage the digital tools at their disposal.
Digital transformation notwithstanding, industry professionals can never forget about the underlying principles of science, which are timeless. After all, those professionals “are still going to be the ones driving the process,” Dindoruk said.
David Reid, Drilling
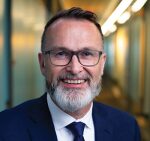
Drillers have dramatically reduced the number of days it takes to drill a well, even as wells have gotten longer and more geologically challenging. But that does not mean the industry is drilling better wells.
“We’ve been learning how to drill wells faster, but we’ve not been learning how to measure performance or adjust to geology,” said Reid. “The focus on speed specifically in the shale markets has been cost driven.”
Getting in the way of achieving more accurate and more productive wells has been the industry’s traditionally siloed nature and struggle to develop effective models on the fly with live data. Drilling will have to become better connected to other parts of the upstream process, with more collaboration across disciplines. For this to happen, better data will be needed to foster stronger connectivity. Drillers are still figuring out how to “close the loop” on data so that models learn and correct as the bit cuts through the rock.
“This journey needs better alignment between groups who have seen their tasks as somewhat separate,” Reid said. “We are reaching a time for holistic drilling systems of data. The journey is really beginning now.”
The automation of drilling components and systems will continue to change the way people work, making it critical for employees to remain adaptable. While the transition to automation “is still early, I think you’re going to see a central person doing most of the work” traditionally performed by multiple specialists on the rig, he said. “So the driller will have to become a more advanced process operator.” Replacing some of the traditional drilling roles are data science jobs, which Reid describes as “better jobs for humans.”
Beyond the drilling cabin and the office, the day-rate contracting model has come under scrutiny as drilling companies continually improve performance but receive little financial reward. “If we drill faster, we make less money,” Reid said, adding that he advocates for a performance-based contract model.
“Current day-rate models are crushing the supply chain into nonfunctioning businesses that must go out of business or consolidate,” he said. “The path out of that is better alignment.” One contracting trend, he noted, involves large service companies integrating well services into a total well delivery project, resulting in better efficiencies and lower costs.
Lower costs remain imperative to a sustained offshore rebound. Reid believes the industry’s learnings in shale “will become a more global phenomenon” offshore and internationally. For example, push-button drilling was recently implemented by an international oil company as it discovered a bounty of oil that is expected to lead to several new developments.
Terry Palisch, Completions
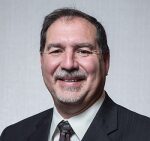
As the unconventional revolution has evolved, figuring out how to maximize contact with hydrocarbon-bearing rock in the subsurface has been a primary directive for operators. But, as well spacing has become tighter, the growing number of newer wells, or child wells, drilled around older wells, or parent wells, in many cases has resulted in lower-than-expected productivity.
In the unconventional space, said Palisch, “the big question now is, how do we maximize the amount of recovery when we drill these child wells?” A hot topic at recent SPE conferences and forums, measures being taken to mitigate parent-child interactions include preloading the parent well to “pressure it up” before fracturing the child wells. Possible solutions for child wells include diversion technology to help optimize fracture propagation.
Ultimately, the industry will need a better understanding of the production mechanism of unconventional wells. “It’s not the same as in a conventional well where it’s just plain Darcy flow through a matrix,” he said. And the industry is “not going to solve these completions challenges with just completions engineers,” Palisch said. “This is a cross-discipline issue, and our biggest companion in this is reservoir engineers.”
Another persistent hurdle faced by those in the discipline has to do with casing deformation in multistage fractured wells, he said. This involves portions of the well casing becoming constricted, preventing a well from flowing at an optimal level. In the worst cases, entire portions of the lateral are lost.
As with the parent-child challenge, the movement to understand and solve the casing failure issue is early. Currently the industry is trying to learn where the problems are happening: Are they in the lateral? Are they in the uphole section? Could better cement help? And are they a regional phenomenon? To date, failures have been reported in China, Argentina, and North America.
Palisch noted an inquiry on SPE Connect about a year ago in which a member asked if anyone else was having the problem, “and over a hundred people responded, ‘Yes.’” That implies that perhaps there is now enough experience with casing failures to where engineers can come together and study why it keeps occurring. It too should involve multiple disciplines, incorporating completions, drilling, and geomechanics, he said.
The industry as a whole for too long has relied on the “bigger hammer approach,” he said, where it grew production merely by drilling more wells and pumping bigger fracs. Now, as the unconventional space matures, both problems and solutions are becoming more complex.
“We’ve upped the completions intensity over the last 4 or 5 years, leading to dramatic increases in our production and productivity. But we’re still looking at recovery factors that are in the 10% or less range,” he said. “And the question is, can we as an industry continue to just drill more and more wells on tighter and tighter spacing, pumping more and more water and more and more proppant?”
In other words, is that approach sustainable in an era where environmental concerns are heightened and investors are put off by the industry’s traditional lack of capital discipline?
But the industry is continuing to make the most of its current knowledge and resources and has done a good job of adapting and applying learnings as it goes. “In the end, we’re still making more production, we’re still depleting the reservoir,” Palisch said. “We’re just trying to figure out how do we go from 10 to 15% recovery” in a sustainable manner.
Johana Dunlop, Health, Safety, Environment, and Sustainability
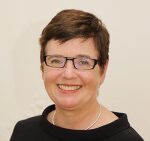
The industry’s purpose moving forward should be to continue providing reliable, affordable energy to the world while striving for “effectively zero negative impact,” said Dunlop. This means the industry should decarbonize its products and promote conservation. However, because of its fragmented nature, the industry cannot answer the question, “Are we doing enough fast enough in relation to the scale and urgency of the challenges?”
As the originator of the SPE Gaia Summit, Dunlop is part of a movement that seeks to mobilize more than 250,000 people around the industry through professional associations in an effort to ensure “that oil and gas is on the right side of history,” she said. Delegates at the summit, held in June, explored difficult questions about the industry’s role in the coming years, including, “How do we accelerate a transformation of our own industry?”
The first challenge is establishing a unified front—or overcoming the inherently fragmented nature of the industry, which consists of many different moving parts: different disciplines, different business units, different companies, different countries, and different cultures. Sustainability should be addressed at major industry events where there is a captive but diverse audience of industry participants. SPE events serve as excellent venues to enable safe, collective engagement given that it is a trusted and respected organization globally, Dunlop said.
Those events can facilitate an open dialogue where people can learn from each other. “We can host the rational middle, where people can come and congregate and they can have completely divergent points of view,” she said. “SPE is extraordinarily well placed to play a pivotal role and to address parts of the big picture that are not addressed by others,” Dunlop said.
In the end, however, actions speak louder than words. “Let people think what they want to think,” she said. “We will change what they say about us when they see our performance, when we decarbonize to the point where the production of our products and their combustion by consumers and industry are no longer a risk to the planet.”
This includes an end to flaring and venting, which are both harmful to the environment and wasteful. In an example of how operators are reducing the negative impacts of their work while also improving efficiencies, Occidental Petroleum’s Oxy Low Carbon Ventures invests in carbon capture technology that can supply CO2 for enhanced oil recovery injection in the Permian Basin, she noted.
Countless startups are also working to find ways to monetize CO2. Operators are enlisting drone-mounted sensors to detect, localize, and measure fugitive gas emissions. Broader application of these methods and technologies will go a long way toward achieving the ultimate goal of “effectively zero,” Dunlop said.
Bob Pearson, Production and Facilities
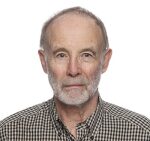
In the production and facilities discipline, Pearson said, unconventionals and deep water continue to face major challenges going forward in an environment of low and unpredictable product pricing. As a result, field development planning will continue to focus on “driving down costs and driving up reliability and predictability,” he said.
Pearson believes part of the solution is for the various subsectors to tackle these challenges collaboratively through jointly funded research and development projects and the exchange of technologies.
While advances in digital automation and fiber applications are transferrable, a number of downhole completion and service tools will eventually find much broader application, particularly in light of advances via coiled tubing in extended-reach wells and smaller-sized downhole tractors. Downhole sensors and controls are under development for both unconventionals and deep water as well as for conventional applications. For example, inflow-control device concepts are being applied to steam distribution in unconventional thermal operations and conventional waterfloods.
However, the transfer of technologies is not limited to this industry segment. The upstream space as a whole can learn from the refining and petrochemical businesses, for example, which have mastered fully automated process controls. “Just imagine what this could do for real-time voidage replacement management in [enhanced oil recovery] projects,” he said. The production and facilities discipline will continue to strive to apply state-of-the-art industrial engineering in a factory approach to operations, automating as much as possible and reducing operating expenses and safety and environmental risks.
Cost reductions will also come through more efficient energy usage and fuel substitution. “More and more equipment are likely to be powered by LNG, CNG, and renewables where there is a cost advantage to their use,” Pearson said. This is already happening in sunny West Texas, where Occidental Petroleum recently started up a 16-MW solar facility to power its enhanced oil recovery operations in the Permian Basin. The LNG Canada project under development in British Columbia will utilize hydropower to reduce emissions and increase throughput.
But, “It’s not so much the technology,” he said. “It’s the way in which we work that is changing. We’re going to have to work much more collaboratively not only within the industry but also with other industries and stakeholders.”
As with other industries that are heavily reliant on large engineering and construction projects, delivering new megaprojects on time and within budget remains a persistent hurdle for the upstream space. Here, Pearson sees an opportunity to learn from the military. “We’ve already latched on to that in unconventional operations with former military people managing logistics and helping to optimize the supply chain,” he said.
“I also see a lot of megaprojects being broken down into smaller, more manageable projects instead of continuing the trend of making contracting and project management processes more complicated,” Pearson added.
The upstream space is increasingly employing advanced project engineering processes to better execute large-scale projects. “Some of the best project managers that I have worked for had limited experience in the upstream oil and gas business,” Pearson said. “The digital age will allow for much more sophisticated scheduling and risk analysis, which hopefully could lead to more sophisticated approaches to project risk mitigation,” he said.
Erdal Ozkan, Reservoir
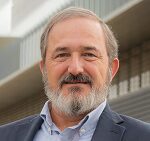
Ozkan believes the reservoir discipline within SPE and outside the Society could benefit from some updating. That is because many of the technologies and concepts commonly put to practice in the discipline were developed during bygone eras of exploration and production.
“The fundamental knowledge, the fundamental approach to this discipline has not changed much, despite the fact that the subject reservoirs and expected results are much different” from those eras, Ozkan said. In the past, “we had the luxury of dealing with more permeable, more homogeneous types of formations in more forgiving economic conditions. Today, we are dealing with a lot of complexities in these reservoirs—not only technical but also economic, environmental, and social—especially in light of what we have learned from unconventionals.”
When it comes to reservoir technologies, the industry had “neglected the unconventional side for quite some time because it was always about drilling and completions,” Ozkan said. Now that cash flow has shrunk and the treadmill of drilling and completing wells has slowed, the reservoir discipline is getting more attention. More emphasis is being placed on recovery factors as companies try to squeeze more out of each existing well rather than making new ones. For this approach to be successful, however, the industry needs to further improve its understanding of the unconventional reservoir.
Enhanced oil recovery (EOR) has long been touted as a potential game-changer for increasing recovery factors, but the large-scale application has been mostly hampered by economics.
Unconventionals seem to provide a new horizon for EOR technologies, as initial trials in the lab and in the field have been encouraging. Ozkan expects more development in this area as larger companies utilize their resources to improve and implement these technologies economically. He added that there is motivation to use CO2 as an EOR agent given carbon capture efforts, and there is an abundance of gas, particularly associated gas in the Permian Basin, that can also be repurposed into an EOR agent.
On the conventional side, the global industry still stands to learn from the unconventional skills and knowledge gained over the past 20 years in North America, which could lead to increased application of horizontal drilling and hydraulic fracturing in tight carbonate reservoirs. “We will see some updating of our conventional reservoir concepts and technologies in light of our new experience in the unconventional fields,” he said.
For the discipline as a whole, the focus in the coming years will shift to studying phenomena at a smaller scale—all the way down to the pore—to improve understanding of the reservoir at a larger scale. The challenge will then be taking those learnings and expanding them to field scale, incorporating the physics of fluid flow and production via realistic simulations.
Ozkan said there is a lot that reservoir scientists and engineers can learn from other disciplines and other industries, including the application of nanotechnologies, biotechnologies, information technologies, and robotics and automation. “We cannot just continue by reading our papers from OnePetro while missing the benefits of cross-fertilization.”
For now, SPE’s reservoir advisory committee—which consists of 60 subject matter experts from numerous subdisciplines—is working to compose a paper to identify where new concepts can be adopted within the discipline. Ozkan hopes it will ultimately promote “a more dynamic mode of discussion and development.”