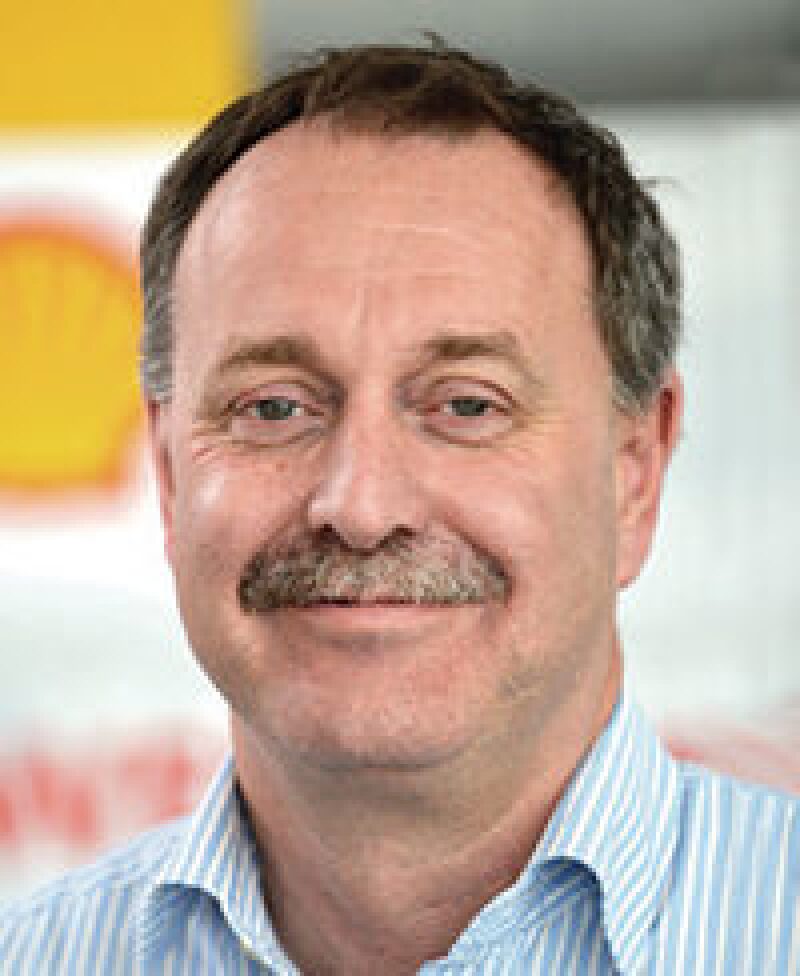
Stuart Clayton is the vice president of hydrocarbon recovery technologies at Shell’s innovation, research, and development organization based in the Netherlands, a position he has held since 2011. His research and development responsibilities are focused on subsurface technology development and include improved and enhanced hydrocarbon recovery systems, reservoir surveillance and smart fields, computational modeling, storage and containment, rock and fluid sciences, and emerging technologies.
Describe the energy production and consumption in the Middle East.
Energy demand in the Middle East is expected to increase by 60% by 2035. Despite the fact that the Middle East holds more than 40% of the global oil and gas reserves, meeting local and global future energy demands will be a major challenge.
It is evident that the global energy system will go through a major transition this century. Shell expects the global energy supply mix to evolve significantly in the decades ahead, with gas, the cleanest burning fossil fuel, becoming more widely used for power generation. While we expect renewables such as wind, solar, and biofuels to play an increasingly important role, oil and gas will be vital to meet the considerable expected increases in energy demand. Building a sustainable energy future is a complex challenge. Irrespective of how long the transition will last, technology innovation will be a crucial driver and will play a vital role to facilitate the transition.
It is imperative for our industry that we maximize the economic ultimate recovery from our existing fields. With the global average field recovery from waterflooding currently being around 35%, leaving from 60% to 70% of the oil in place is a very large opportunity. However, many current and future development opportunities are dominated by complex improved oil recovery (IOR) and enhanced oil recovery (EOR) projects, challenging fluids (heavy oil and sour gas), challenging reservoirs (tight formations, deep reservoirs, high temperature and high pressure), or challenging environmental settings (deep water and Arctic).
Shell has been deeply committed to EOR technology deployment for more than 40 years, throughout the time that EOR has been featured on the industry agenda. In-depth knowledge and an extensive tool box of proven and novel recovery technology solutions are the result.
The Middle East is an important region for Shell and we are proud of the many long-standing partnerships we have established. We have worked with Petroleum Development Oman (PDO) for many decades. Our relationship with the UAE dates back more than 75 years. We are also involved in major projects elsewhere in the region: in Qatar, Saudi Arabia, Kuwait, Egypt, and Iraq.
What is the recovery rate at Shell’s operated fields worldwide and which recovery techniques are used?
The reservoirs of our operated fields vary in complexity and the projects are in various stages of field development. Hence, the recovery rates vary significantly from 10% to 70%.
We are using several recovery technologies, and our research takes us beyond the traditional boundaries of recovery techniques: primary depletion, water injection-based recovery technologies (waterflooding, low-salinity flooding, polymer, surfactant, and water-soluble solvents), gas-based technologies (water-alternating-gas injection, gas/oil gravity drainage, miscible gas injection, high-pressure contaminated gas [carbon dioxide/hydrogen sulfide] injection, and foam), and thermal applications (steam, steam foam, solvent steam, and steam-assisted gravity drainage in fractured reservoirs). We are also looking at the chemical polymers that function effectively in high-salinity, high-temperature environments.
We drive technology with a combination of expertise and determination to see effective technologies tested, demonstrated, and deployed. The technology development process covers all scales, from laboratory tests to full-field commercial application. These steps involve careful interpretation of the reservoir volume and design of each program and includes the use of detailed simulation models as well as thorough field trialing. The initial step is to conduct phase behavior studies, which is followed by corefloods and single-well tests that lead to commercial field deployment. Our scientists and experts provide experimental work, analysis, and support for the deployment process. A vital part of this is working with the field and reservoir engineers to understand what they need.
The development of alkaline/surfactant/polymer (ASP) flooding technology illustrates the development stages. The technology has the potential to recover up to 30% of oil at a carbon dioxide (CO2) footprint that is lower compared with, for example, thermal EOR. We are well on the way to bringing this technology from the laboratory to the field.
Supported by Shell Technology Oman, PDO identified significant target oil volumes for ASP flooding and carried out a sequence of single-well pilots in three fields, sandstone and carbonate, to assess the flooding potential of tailor-made chemical formulations under real subsurface conditions and to quantify the benefits of full-field ASP development.
An extensive design process followed, including the optimization of chemical phase behaviors in test-tube and coreflood experiments. The key chemicals and flow properties of an ASP flood were captured to calibrate a comprehensive reservoir simulation model. The model was used to evaluate PDO’s single-well pilots and showed how these results were used to design a pattern-flood pilot.
In Russia, working with our joint venture company Salym Petroleum Development (SPD), we have been conducting a series of laboratory and field tests in the Salym field. These have been completed with impressive results. The use of the ASP technology in a single-well tracer test showed the displacement of 90% of oil left in the formation after conventional waterflooding.
SPD is now building a pilot plant. The wells have been drilled and cemented, and the construction of the facilities is progressing. With the results from the pilot plant, the chemical cocktail will be fine-tuned and the full-field reservoir simulation will be updated. This process will aid the optimization and commercialization of ASP on a larger scale.
Maximizing recovery from mature fields presents complex technical challenges. Operators must take into account factors such as reservoir depth, oil density, and viscosity. Each formation is unique: there is no one-fits-all EOR solution. Every EOR method has specific strengths or weaknesses and different areas of technical applicability. However, commercial factors such as the cost of the proposed IOR/EOR scheme and the relative balance between capital and operating expenditures must also be considered. Making a strong and realistic business case for the application of EOR is a crucial part of the process.
Describe your water-soluble solvents for EOR applications.
We are examining the idea of using water-soluble solvent for EOR applications to enhance a conventional waterflood. The solvent swells the oil and decreases its viscosity. Because the solvent is water-soluble, it can be back-recovered from the reservoir. At the separation facilities, hydrocarbons are extracted and sent for refining and the water produced from the reservoir is divided into its key components for subsequent reinjection.
The result is a significantly higher ultimate oil recovery compared with the conventional waterflood and accelerated oil production. The technology can be applied in reservoirs that are too hot, tight, or saline for more conventional types of EOR. The overall findings of the work show that the technology can increase oil recovery from both carbonate and clastic cores by 10% to 15% on top of the waterflood.
What is the recovery rate you are targeting with research and development (R&D) projects?
Our aim is to increase our recovery over the entire portfolio globally by an average of 5%. To meet this target, we will have to extract more oil from a broad variety of reservoirs while simultaneously reducing unit costs and energy use.
In addition to more challenging reservoirs and more complex field developments, the business environment is driving changes that include working in more environmentally sensitive areas, and increasing governmental regulation that requires enhanced capability in the monitoring of containment (i.e., reservoir, well, and surface system integrity).
Given this increasing complexity, it is critical to form a better understanding of the subsurface for better decision making over the life cycle of fields in order to
- optimize technical integrity and preserve our license to operate
- optimize field performance and maximize economic recovery
To make our recovery technologies deliver, we focus on wells, reservoir, and facility management, which rely on modern information technology and data acquisition and management. It helps to improve asset value by assisting in the efficient assembly and processing of data into information to enable well-informed decision making in a timely manner.
Our current focus is on developing and implementing improved 4D seismic methods, next-generation sensors and systems for areal and in-well monitoring, in particular, integrated fiber-optic solutions for real-time well, reservoir, and pipeline surveillance for use both onshore and offshore. We have forged partnerships with technology providers such as Baker Hughes, QinetiQ/OptaSense, Sonardyne, CGG, Smart Fibres, and FairfieldNodal and have long-term relationships with universities and research institutes such as TNO (an independent research organization in The Hague) and Delft University of Technology (TU Delft).
What are the technologies being researched to achieve the targeted recovery increase?
I have mentioned ASP and solvents. Another is low-salinity waterflooding (LSF). A large proportion of the world’s oil and gas resources is contained in carbonate rocks. The behavior of carbonate reservoirs is very different from sandstone reservoirs. Our laboratory has recently identified the fundamental controlling mechanism for LSF in carbonates. The breakthrough was based on a combination of expertise in carbonate reservoirs, a dedicated in-house EOR research group that specifically targets carbonates, and collaboration with leading university teams.
It is estimated that LSF can improve oil recovery by up to 6% oil initially in place. Being a natural extension of conventional waterflooding, LSF is easier to implement than other EOR methods. However, the process of screening, designing, and executing LSF projects requires an increased operator competence and management focus compared with conventional waterflooding. To accelerate the deployment effort and standardize the facilities design, integrated technology teams collaborate closely with our R&D and asset teams.
The screening of fields to determine which EOR technologies are suitable for a field and the screening of the chemicals (surfactants, polymers, or planned water quality) to suit a field is crucial to the success of EOR programs. By screening and optimizing the chemical cocktail in the laboratory, we give ourselves the best chance of increasing the recovery factor in the field. We are working closely with the teams in the field because there will always be a difference between what can be achieved in the laboratory and what is observed in the field where issues such as sweep efficiency and geological complexity will reduce performance.
At Shell, we are currently in different stages of deployment around the world and across the whole spectrum of waterflooding projects, from the rejuvenation of brownfields to greenfield developments (offshore and onshore). The LSF deployment effort is combined with the screening of other EOR technologies to identify where LSF may be able to unlock additional value by creating the appropriate conditions for subsequent chemical flooding as part of the full-field development.
Companies in the Middle East are looking at nanotechnology as a solution to achieve maximum oil recovery. Are you conducting research in this technology?
Shell already uses nanotechnology, for example, as catalysts to speed up chemical reactions and in coatings to help stop corrosion of pipes.
We have a nanotechnology laboratory in the United States and are a founding member of the Advanced Energy Consortium, which is an industry consortium set up to facilitate precompetitive research into micro- and nanotechnology materials and sensors. We also partner with the Massachusetts Institute of Technology on projects involving nanotechnology for subsurface applications.
The implications of applying nanotechnology to enhance oil and gas recovery are very exciting. Nanotechnology may help us achieve things that once seemed impossible. The right design of nanoparticles can stabilize foams and emulsions in the reservoir to improve sweep efficiency and recover oil from otherwise bypassed zones.
Foam flooding as a mechanism to EOR has been intensively studied and is the subject of multiple research groups. However, limited stability of surfactant-generated foam in the presence of oil and the low chemical stability of surfactants in the high-temperature and high-salinity conditions of an oil reservoir are among the reasons for foam EOR not being widely applied in the field.
Our recent studies with the TU Delft suggest that synthesized nanoparticles with altered surface properties can aid foam generation and increase foam stability in porous media. Both sandstone and carbonate rocks have been evaluated. We have focused on a silica-based nanoparticle that is available in large quantities and can be processed economically without separate surface treatment. This gives it the potential to become a practical solution in the field.
What is your long-term strategy for EOR deployment?
For an international oil company, the way we innovate and develop technology has changed substantially over the past 10 years. The global innovation footprint is large and diverse. The challenges and solutions for enabling the energy industry to tap into that global technology development, much of which is occurring in academia, are varied and need significant effort to leverage the richness of what is available.
We operate a global “open innovation” strategy for our technology developments and collaborate with our business partners, universities and research institutes, suppliers, and customers. Innovation is not only about new technologies and new processes, but it is also about new ways of thinking to create value. There are two keys to success. One is the integrated and speedy technology delivery from development in the laboratory through to deployment in the field, and the other is having a clear understanding of current and future business needs, and the technologies that respond best to them.
In the current oil price environment, we are challenged. We drive innovation based on the premise of value; this includes value creation with clearly affordable technologies to enable increased competitiveness and direct contributions to Shell’s businesses and bottom line. Right from the start of technology innovation projects, there is a need to focus on how we can commercialize new technologies.Working collaboratively is key. External R&D institutes and technology innovators, such as academia, play an increasingly important part in our innovation efforts. How we deliver that while keeping a focus on the value, requires continued close, sustained long-term relationships and deep collaboration, plus a systematic approach to ensure that connectivity is maintained.