In this study, a fit-for-purpose electrical submersible pump (ESP) load-bearing power cable was deployed inside the production tubing of a sour oil well for an extended period of service. Project economics required the power-cable metallurgy to survive long-term exposure reliably for up to 15% hydrogen sulfide (H2S) and high-salinity production fluids. Laboratory tests simulating varying sour well and extended galvanic corrosion conditions have been performed to determine the adequacy of the selected armor metallurgy in downhole corrosive environments.
Introduction
In recent years, various types of load-bearing power cable-deployed ESP (CDESP) systems have been introduced, eliminating the need to install or remove a conventional ESP along with the completion and reducing ESP changeover time by more than 80%. More recently, live-well CDESP systems have been developed and tested to eliminate the need for a well-kill operation.
The most-critical and costly component of such a system is the load-bearing power cable. The cable has the dual purpose of conveyance and long-term powering-up of the ESP. In a conventional artificial lift operation, the ESP is conveyed using the production tubing with a non-load-bearing power cable strapped to the outside of the tubing.
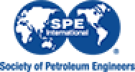