Different artificial lift technologies have been used for decades to dewater coalbed methane (CBM) wells to reduce hydrostatic pressure and release the gas for production. Among the newest is the electric submersible pump (ESP) using progressive cavity pump (PCP) technology, known as an ESPCP (Fig. 1).
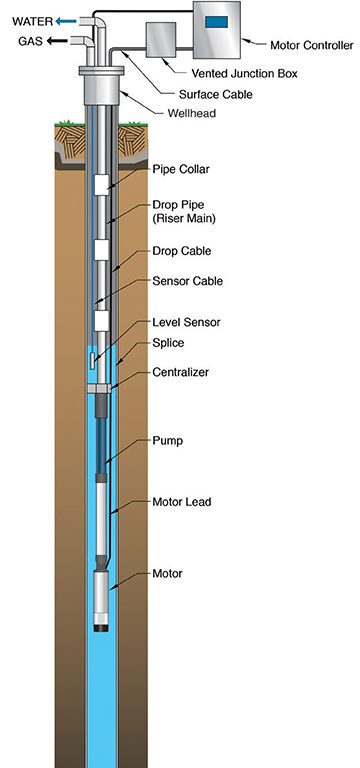
Close coupling between a PCP and a submersible electric motor enable these units to run more quietly, pump more, and last longer. And because of their lower profile above ground, submersible pumps lend themselves to gas operations near residential areas and other locations where aesthetics and quiet operation are a priority.
Dewatering CBM wells can be difficult because coal seams typically lie far below the groundwater level, often at depths greater than 2,000 ft. Conventional centrifugal water-well pumps and standard oilfield ESPs struggle at typical flow rates of wells of 250 B/D or less.
To overcome this, some operators overspeed a centrifugal pump, which requires start and stop cycles to avoid overpumping. Such operation is inefficient and shortens pump and motor life. In addition, most centrifugal pumps that operate in this range tend to have small flow passages and become easily clogged. A different style of pump is required to operate these “low and slow” wells efficiently. The ESPCP, which combines the benefits of the ESP and the PCP (Fig. 2 above), meets this need.
PCP Systems
A PCP transfers fluid by advancing it through a sequence of fixed-shaped, discrete cavities, as the rotor is turned. This leads to the volumetric flow rate being directly proportional to the rate of rotation, and to low levels of shearing being applied to the pumped fluid. The individual pump cavities are tapered toward their ends and overlap in the axial direction with neighboring cavities so at any given instant, multiple cavities are open and discharging fluid. This makes for smooth fluid flow, with no pulsing action.
Because the rotor is well sealed within the cavity walls, the pump is effective at low flow rates from significant depths. The pump’s lack of shearing action also makes it good for pumping fluids that contain fracturing sand, coal fines, or even large particles, typically present in CBM dewatering applications.
Also typical are varying levels of gas and varying flow rates, which the PCP’s smooth and uniform operation is able to handle more easily. Additionally, the high pump efficiency helps to keep the power requirements modest at low flow rates. Franklin Electric has found that power levels for its ESPCP systems can be as low as 600 W to 3 kW to maintain desired water levels at depths of 900 ft to 1,300 ft.
PCP systems have traditionally used aboveground motors with long drive shafts, but this can pose problems. The motors are noisy and if used near residential areas are often considered visually objectionable. If the well has a horizontal design, the drive shaft approach requires mechanical support such as bushings or bearings to negotiate the curve built into the well path. These will wear out, which increases operational costs.
Submersible PCP Systems
A better approach is to use a submersible PCP that directly couples the motor to the pump. There are several advantages to this tight coupling. No gearbox is involved, eliminating a source of reliability problems. The pump also responds more rapidly to changes initiated from the controls. With a topside motor, the torque transmitted through a shaft possibly thousands of feet long causes a lag between changes in motor revolutions per minute (RPM) and changes in pump RPM. By placing the motor downhole with the pump, a change in the pump can be instantaneously detected in the motor.
Another advantage is that placing the motor downhole enables a heavy-duty check valve to be set atop the unit to prevent debris from settling into the pump while it is turned off. As long as the PCP and pipe diameter selected enable a sufficient operating flow rate, sand that settles on the check valve will be driven upward to the surface when the motor starts again. On a traditional PCP driven by shaft from a surface motor, the pump must be pulled to dislodge the debris, thereby increasing operating cost and nonproductive time.
Because of smooth on/off pump operation, prevention of debris settling, and the close coupling of the motor and the pump, a very tight level of control of the water level in the well is possible. A control unit on the surface is connected electrically to the pump motor underground, and a downhole level sensor can be mounted in the well and connected to the control unit. Mounting this sensor is easier and can be done more reliably because of the reduced tubing size and reduced vibration that result from eliminating the drive shaft.
The ESPCP needs a pumping control system, which includes a variable frequency drive to control motor speed and a graphical user interface (GUI) through which installers and operators can adjust pumping parameters. The GUI is web-based and device independent, using common terminology. The interface screen is highly intuitive, allowing virtually every aspect of pump operation to be adjusted to achieve maximum efficiency and enabling critical production parameters, such as gas concentration, to be monitored.
Fourteen ESPCP systems are being used by a mid-sized energy company operating in the northwestern United States in low-producing CBM recovery wells down to depths of 3,300 ft. The systems replaced were ESPs that were subject to clogging and frequent shutdowns because of sand, coal fines, paraffin, and salt accumulating in the pump and motor. The first ESPCP installed has operated for 16 months without clogging and the rate of methane recovery from the well has doubled.