Flow assurance in subsea oil and gas fields often presents significant challenges. Every field has its own combination of difficulties, and no universal process or system can be used to mitigate these. Detailed knowledge across a broad range of competencies, therefore, is required to find solutions that can minimize the risk of not getting the hydrocarbons safely to the process facilities.
Many subsea fields that are being developed today are long tiebacks, taking advantage of existing offshore infrastructure or producing directly to shore. These developments must deal with the long-distance transport of hydrocarbons in deep cold water, commonly increasing the risk of hydrate formation and wax deposition, for example. In addition, large elevation changes from deep water to surface and topographical challenges along the pipeline can create flow-regime effects that can hinder production.
The loss of temperature in a long subsea pipeline also creates challenges for fields that produce heavy oil because the oil viscosity in some cases increases dramatically at low temperatures, in addition to effective viscosities increasing because of oil and water emulsions. Other phenomena such as scale deposition, foaming, sand production, erosion, and corrosion must be considered and dealt with as well.
Various smart-technology innovations for subsea oil and gas production contribute to reducing the risk of these flow-assurance issues. Some of them are described in this month’s selected SPE papers.
A good example is as follows: When wells start to produce water, the operator needs to understand where the water is coming from and quantify volumes in order to start a mitigation program to avoid hydrate formation. This is one of the reasons why subsea multiphase flowmeters have become an essential feature in all new subsea fields.
The most common remedy for flow-assurance problems is probably the use of chemical additives. A sensor technology that can directly determine the ratio between produced water and chemicals such as monoethylene glycol has been recently introduced in subsea production systems. This measurement enables the optimization of chemical-injection rates, thereby contributing to significant savings in capital expenditure (reduced design margins) and operational expenditure (reduced overdosage margins).
Another effective way to prevent hydrates and wax is to keep the process temperature above critical limits by applying active flowline heating. New technologies for highly reliable and efficient subsea electrically heat-traced flowlines have recently been qualified, industrialized, and installed.
Technologies as described here can play an important role in future subsea field developments. The recommended readings for this feature date back further back in time than usual, but are relevant to the theme of this year’s main selections.
This Month’s Technical Papers
New Monoethylene-Glycol Sensor Validated by Flow Loop Under Hydrate-Forming Conditions
Early Production Life of Wheatstone Project Offshore Australia Yields Key Lessons
Subsea-Systems Innovations Improve Heavy-Oil Production in Ultradeep Water
Recommended Additional Reading
OTC 29232 Real-Time Subsea Hydrate Management in the World’s Longest Subsea Tieback by Christophe Vielliard, OneSubsea, a Schlumberger Company, et al.
OTC 31078 Electrically Heated Trace Flowline on the Ærfugl Project—A Journey From Product Qualification to Offshore Campaign by Guy Mencarelli, Subsea 7, et al.
SPE 195784 A New Flow-Assurance Strategy for the Vega Asset: Managing Hydrate and Integrity Risks on a Long Multiphase Flowline of a Norwegian Subsea Asset by Stephan Hatscher, Wintershall Norge, et al.
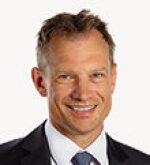
Birger Velle Hanssen, SPE, is the global sales manager for subsea multiphase flowmeters at OneSubsea, a Schlumberger company, a position he assumed in 2018. Previously, he was product manager for subsea boosting and compression. Hanssen has more than 30 years of experience in subsea technology, covering a wide range of competencies, including mechanical design, product development, sales, and management. He has presented papers at various SPE conferences on subsea processing technologies. Hanssen holds a master’s degree in mechanical engineering from the Norwegian University of Science and Technology and is an active member of SPE. He is a member of the JPT Editorial Review Committee and can be reached at bhanssen@slb.com.