A subsea water-treatment system designed to leverage space availability, steady temperatures, lower bacteria levels, and other natural benefits of the seabed environment was successfully installed during pilot testing at the Ekofisk field offshore Norway. After several phases of testing, a full-scale water-treatment module was built and installed, and at the time the complete paper was written, the pilot had moved into the long-term testing phase to determine the system’s viability under North Sea field conditions. According to the author, if the system succeeds, it could drive a major change in injection-water management offshore.
Introduction
The Ekofisk field was originally developed with pressure depletion as the primary drive mechanism. After several decades of production, significant resources are still in place. Limited gas injection and comprehensive water injection have contributed to a substantial increase in oil recovery. Large-scale water injection began in 1987, and has been extended in several phases. Water displacement of the oil has been successful, and the recoverable resources have been adjusted correspondingly upward from the original 17% to an estimated final recovery factor of greater than 50%.
An important factor in the success of a waterflood project is the quality of the injected water. In worst-case scenarios, poor water quality can cause plugging and reservoir souring. Water quality is greatly affected by contaminants such as suspended solids, corrosion products, scale, and bacteria. Controlling corrosion and disinfection of biomass are two major challenges associated with waterflood. The two challenges are linked because oxidants are required to reduce bacterial activities that could lead to microbial-induced corrosion, but the oxidants also promote corrosion.
Joint-Industry Project (JIP) Results
Development of the injection-water treatment system described in the paper began in 2004. Det Norske Veritas’ recommended practice for qualification of new technology has been used throughout the development process. On the basis of successful experimental testing that demonstrated proof of the concept, a JIP supported by several oil and gas majors was launched in 2009. A prototype was built and tested in 65 m of water depth in Oslofjorden, a sheltered environment in a fjord, to verify the water-treatment module’s performance and reliability through seasonal variations in real offshore conditions. Results demonstrated that the treatment method, which combined various electrolysis approaches, provided very good water quality, in many aspects superior to that achieved by topside seawater-treatment plants.
With proof of concept demonstrated, a full-scale production unit was designed, built, and began pilot testing in a new JIP. The test was carried out in Fognafjorden on the Norwegian western coast offshore Tau, in 220 m of water. The main objectives were to:
- Qualify the subsea water-treatment module according to API Technology Readiness Level (TRL) 6
- Achieve a water-quality-disinfection level at least corresponding to the current practice at typical topside treatment facilities
The water-treatment module was stress-tested at various capacities as well as at the nominal design capacity of 40,000 B/D, and met API TRL 6 requirements. Third-party surveillance of water quality showed a consistent free chlorine level, promising disinfection capabilities, and substantial particle settlement within the treatment module.
On the basis of this performance, a pilot test was scheduled at Ekofisk field. The primary objective was to verify the system’s performance and reliability, demonstrating its ability to reliably clean and deliver injection water in a harsh offshore environment and in a live field situation. The test was planned to cover both summer and winter months to demonstrate that acceptable water quality can be sustained through seasonal variations.
The secondary objective of the pilot test, ongoing at the time of the paper’s writing, was to observe the wellbore and reservoir effects of injecting treated seawater from the subsea treatment unit. Results from this test were projected to become available during the second half of 2019.
Treatment System Technology and Operation
The complete paper discusses traditional oxidizing biocide use in the industry and then describes principles and operation of the subsea water-treatment module. Water is chlorinated at the inlet of the module by electrochlorination as it is transferred into a large compartment, where the water is afforded a long residence time to allow the chlorine reaction to take place. Disinfected water exiting the large compartment then flows through a secondary electrolysis treatment cell called the hydroxyl radical generator. Hydroxyl radicals are very strong oxidizing agents that are known to destruct organic contaminants in water. With enough hydroxy molecules, hydroxyl radicals have the potential to completely oxidize organic compounds dissolved in water to CO2 and H2O.
Solids removal is the other key capability of the treatment process. Gravity, together with low velocities and laminar flow, maximizes Stokes’ law, or the principle of drag force exerted on objects in a viscous fluid. Inclined plates within the large compartment allow for efficient particle settling, because particles have less drag force along these plates and are therefore settling into the lower part of the treatment module.
The unique property of electrolysis is the ability to produce oxidants directly from the seawater, which means that no liquid chemicals need to be added. The combination of electrolysis- and gravity-based solids-removal processes provides a net result of very good water quality using minimal amounts of energy with a system that has no moving parts.
Test Setup and Injection-Well-Selection Criteria
The pilot test rig-up is divided between two installations, the jackup rig, West Linus, and the wellhead platform Ekofisk Zulu. The water-treatment module is placed at the seabed approximately 70 m south of the platform (Fig. 1). An 8-in. flowline is pulled from the water-treatment module to a water-lift pump located in the leg of West Linus. This pump lifts the treated seawater up to the main deck, where the treated water can be sampled for analysis and further distributed to either Ekofisk Zulu for injection or dumped back into the sea.
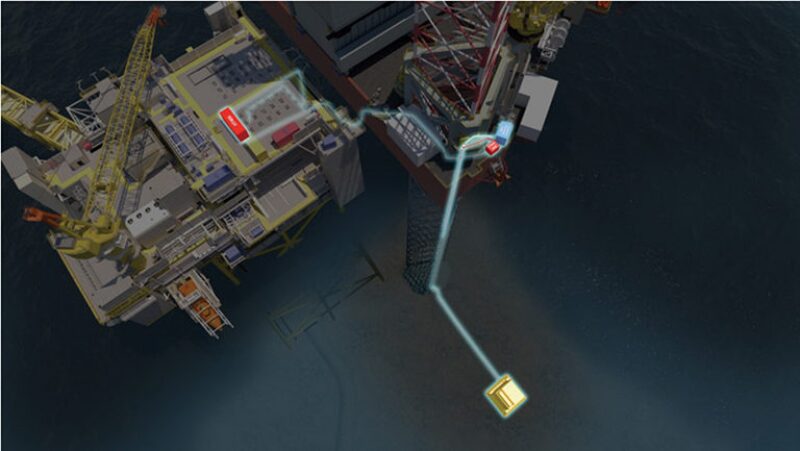
A risk assessment was run to find a suitable well for injecting water into the Ekofisk reservoir. Tree and tubing corrosion, reservoir souring, and loss of injection were considered. Because the pilot test was to make use of an existing well with 13Cr tubulars, corrosivity of seawater was identified as a potential risk. Crevice corrosion is always expected in various degrees on the basis of the materials involved—simply nature’s way of reversing an unnatural process back to a lower energy state. Length of service during the test period is short (9 months) and the resulting risk was deemed acceptable.
Reservoir souring is a process in which a previously sweet oil field begins to produce fluids containing hydrogen sulfide generated by microbiological activity. It typically occurs in reservoirs flooded by seawater for pressure maintenance because of insufficient disinfection of the seawater injected. Close monitoring of disinfection efficiency and particle levels was prescribed.
Water quality has a major influence on the injectivity of injection wells. Poor injection-water quality can compromise effective injectivity of even high-quality formations. Solids-particle damage depends on particle size of the solids and the average pore-throat diameter of the formation. If the particles are larger than the average pore-throat diameter of the formation, they cannot penetrate the pores. As a result, permeability of the formation around the wellbore can be reduced—and, with it, injectivity. Pressure buildup and injection rates will be monitored during the test period.
Data and Results for Commissioning Phase
The lowermost tray of the water-treatment module was the first element to be installed and was placed directly on the seabed. It was followed by the large stillroom, then the treatment unit (the top piece that contains all the equipment that requires periodic maintenance).
Overall, installation was considered a success. However, a few improvements were suggested.
- Allow for higher weather tolerance on the various elements during installation.
- Use additional weights where needed to withstand environmental loads.
- Evaluate higher weights on the lowermost tray.
- Locking-system handling should be improved to be easier to handle by remotely operated vehicle.
- Altered design on the tray and stillroom might improve scouring effect.
During the commissioning phase, establishing stable flow rates through the module and a stable chlorine concentration at the sample point was important. Oxidant demand is normally higher after initial startup or prolonged shut-ins because of the overall higher presence of organics. Hence, the commissioning phase was considered completed when flow was constant and excess oxidant levels were stable.
Conclusions From Commissioning Phase
- It is possible to install a water-treatment system directly at the seabed.
- Limited data are available, but the system has demonstrated high reliability.
- Although current results are within expectations, conclusions from the pilot test and injection into the Ekofisk reservoir cannot be drawn until more data become available and the injection test has been concluded.
- The project has recently moved into the long-term testing phase.
This article, written by JPT Technology Editor Judy Feder, contains highlights of paper OTC 29552, “Subsea Water Treatment Pilot Testing at the Ekofisk Field in the North Sea,” by Eirik Dirdal, National Oilwell Varco, prepared for the 2019 Offshore Technology Conference, 6–9 May, Houston. The paper has not been peer reviewed. Copyright 2019 Offshore Technology Conference. Reproduced by permission.