Mixed carbonate-/sulfide-scale problems have been reported when water is produced from carbonate reservoirs. This study presents interactions of lead sulfide and zinc sulfide coprecipitating with calcite. The relationship between bulk precipitation and deposition on a metal surface of the mixed carbonate/sulfide scales was examined when the mixed scales began to nucleate, agglomerate, and grow. The nature of these mixed crystals may indicate that mixed sulfide scales tend to prefer forming in solution rather than adhering to metal surfaces in protected zones. Thus, the mixed sulfide scale may be controlled in one zone but be unprotected in other regions.
Introduction
Carbonate reservoirs contain approximately 60% of the world’s remaining oil and gas reserves. Scale precipitation during oil and gas production is costly. Conventional scales, such as sulfate and carbonate, are well-known and have been researched and reported extensively. Sulfide scales are less studied, and their effect on conventional scales (formation and inhibition) is relatively unknown.
The effects of carbonate/sulfide coprecipitation in bulk solution and on metal surfaces are presented. Sulfide was coprecipitated with barium sulfate (BaSO4), and the effects on formation and inhibition of the BaSO4 crystals were monitored. The relationship between bulk precipitation and surface deposition of the mixed carbonate/sulfide scales was examined also. Both carbonate- and sulfide-scale problems have been reported when water is produced from carbonate reservoirs, and the use of scale inhibitors to control this problem is relatively common.
Experiments
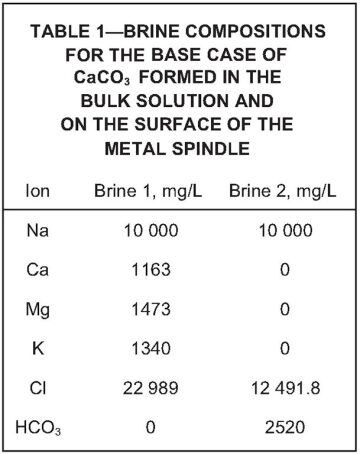
Experiments were carried out in a 500‑mL acrylic-glass vessel at 20°C with a magnetic stirrer to accelerate bulk precipitation. Calcium carbonate (CaCO3) was precipitated spontaneously by mixing 150 mL of a base brine with 150 mL of a second brine containing a bicarbonate. The composition varied according to the sulfide scale being formed in association with the CaCO3 scale. The influence of lead sulfate and zinc sulfate (PbS and ZnS, respectively) on CaCO3 bulk precipitation and surface deposition was studied. The acrylic-glass vessel was built to simulate the formation of CaCO3-scale deposition by carbon dioxide (CO2) loss. The principle is that, as CO2 is lost from supersaturated brine, CaCO3 scale will form in the bulk solution and on the metal surface of the spindle. The spindle is nonrotating, so a magnetic stirrer was used to accelerate scale formation on the surface of the spindle in the dynamic beaker test. CaCO3 scales were deposited on the active surface of the stainless steel. During the experiments, an insulating tape around the electrode ensured that only the end surface was the electrochemically active surface. Deposition occurred on the active surface of the electrode, which was the only surface analyzed with the environmental scanning electron microscope (ESEM). As the experiments progressed, the pH of the solution was allowed to increase (i.e., CO2 degassing proceeded). The composition of the final scaling solution varied, depending on the brine composition used for the experiments.
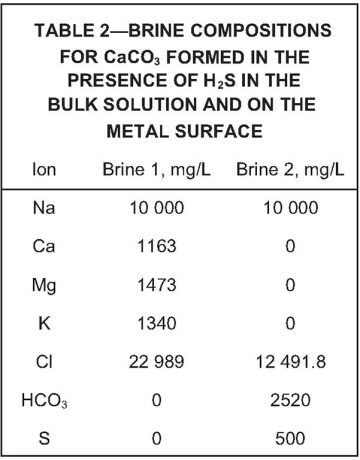
Brine Compositions. Table 1 shows the brine composition for the base case of CaCO3 formed in the bulk solution and on the surface of the metal spindle. Table 2 details the brine composition for CaCO3 formed in the presence of hydrogen sulfide (H2S), both in bulk and on the metal surface. This was the base case used to determine the influence of H2S on the formation of CaCO3. The complete paper contains tables with brine compositions used in the other experiments.
Results
Base Case (CaCO3-Crystal Formation). To investigate the influence of sulfide coprecipitation with CaCO3, it was important to establish a base case of precipitated CaCO3 crystals in bulk and on the active metal surface. Bulk CaCO3 precipitation was carried out with the brine compositions in Table 1. Fig. 1 shows an ESEM image with corresponding energy-dispersive-analysis X-ray (EDAX) elemental quantifications for the CaCO3 crystals that formed on the active metal surface. Notice the classic trigonal rhombohedral crystal shape of calcite. Crystals that formed on the metal surface at 24 hours were 10 to 20 µm in size and covered the whole metal surface. Fig. 2 shows the CaCO3 crystals that formed in the bulk solution. In the bulk solution, the size of the crystals in the precipitate was less than 5 µm.
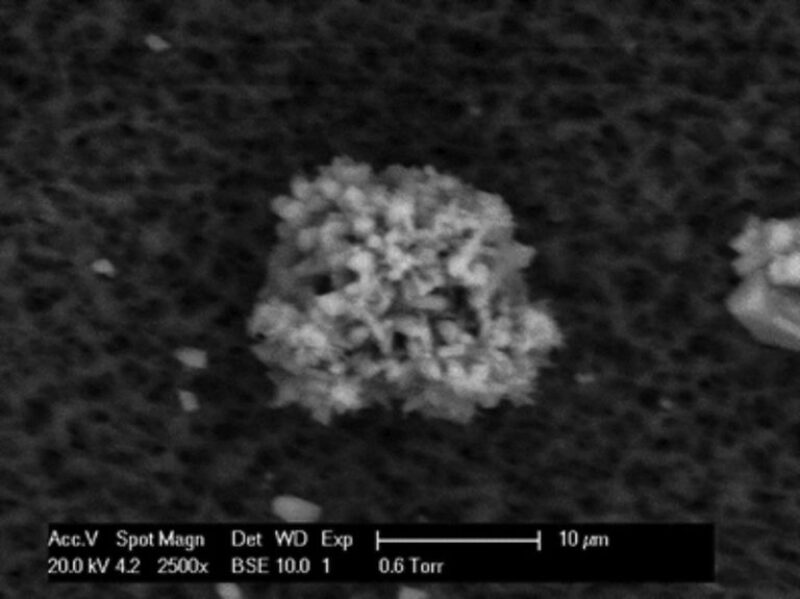
Fig. 3 and Fig. 4 show CaCO3 crystals deposited on the metal surface and precipitated in the bulk solution after 2 hours, respectively. Fig. 3 shows fewer crystals deposited on the metal surface, but the crystals are of similar size and shape. Crystals that formed in the bulk solution (Fig. 4) aggregated as a CaCO3 mass. The experiment showed that the precipitate formed in the bulk solution was different from the deposit formed on the metal surface.
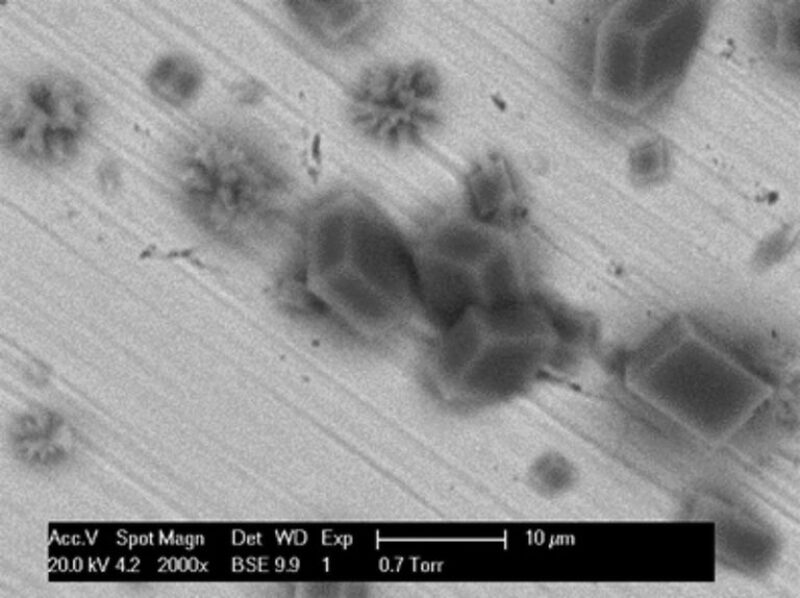
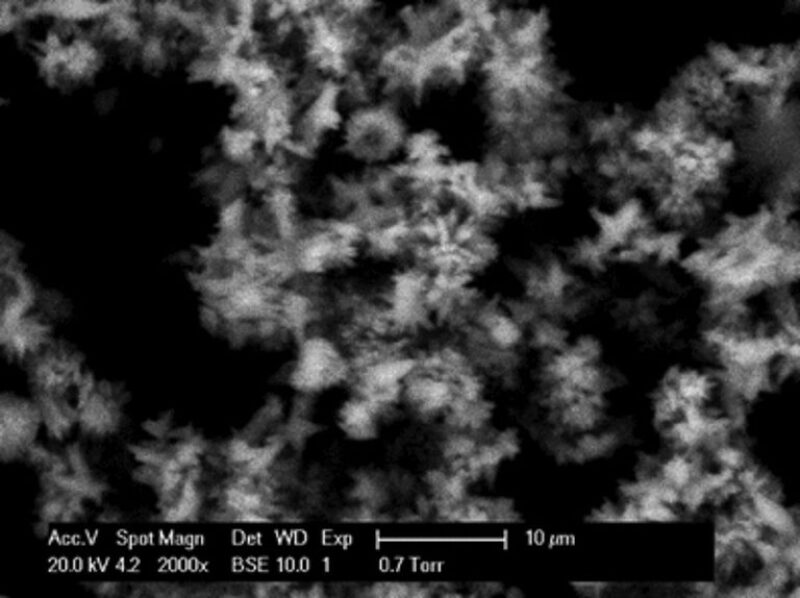
CaCO3 Coprecipitation With ZnS. The CaCO3 crystals deposited on the active metal surface when coprecipitated with ZnS varied in size but were fully formed undistorted CaCO3 crystals. Fewer crystals formed on the metal surface than in the base case at 24 hours. EDAX data indicated that the crystals were CaCO3. Fig. 5 shows CaCO3 crystals that formed in the bulk solution, with elongated crystals in a fused mass. The EDAX data indicated that CaCO3 crystals and ZnS were mixed in the scale in the bulk phase. However, ZnS was not identified on the metal surface. Although both scales (CaCO3 and ZnS) form, there must be a difference in the degree of adhesion of these minerals to the metal surface.
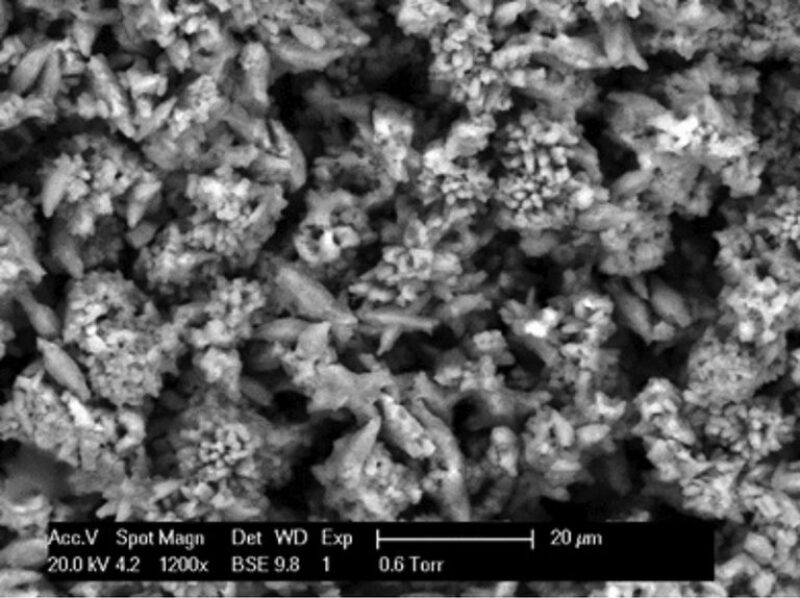
CaCO3 Coprecipitation With PbS. Fig. 6 shows the CaCO3 crystals deposited on the active metal surface when coprecipitated with PbS. The CaCO3 crystals are distorted, with most crystals appearing to be quite thin, and projecting outward; some crystals formed bunched together, giving a flower-petal appearance. Crystals that formed in the bulk solution were fully formed CaCO3 crystals mixed with, perhaps, PbCO3 (not confirmed). The CaCO3 crystals showed a rhombohedral shape, and EDAX data indicated the presence of CaCO3. In the bulk solution, PbS formed spontaneously as the brines were mixed. The scales appeared as a brown gritty mix in the bulk solution. The low solubility of the PbS may have enhanced the full formation of the crystals by a heterogeneous precipitation process. This was the only experiment in the study in which fully formed PbS crystals were found in the bulk solution.
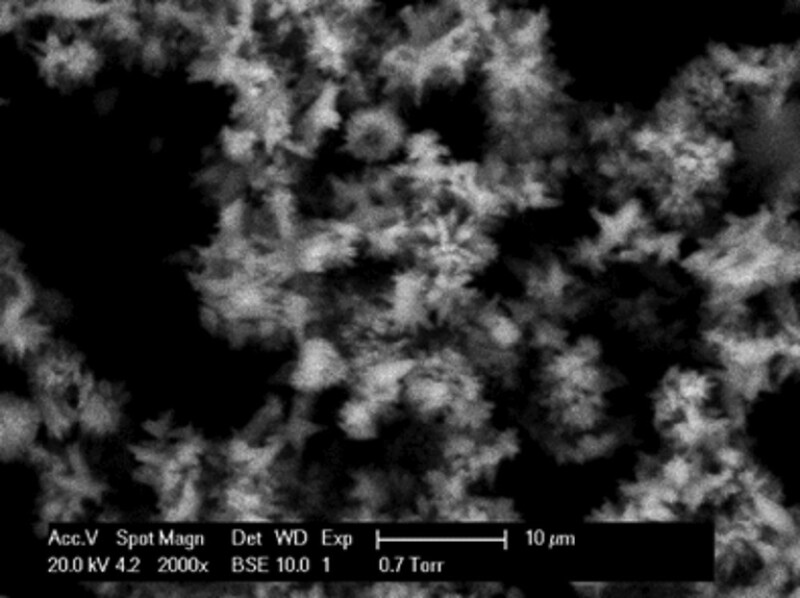
CaCO3 Coprecipitation With Sulfide Scales in the Presence of Scale Inhibitor. Inhibited CaCO3-deposition experiments were performed with a polymeric scale inhibitor (SI)—polyphosphino carboxylic acid (PPCA)—with initial PPCA concentrations of 3, 1, and 0.5 ppm in the mixed brines. A base-case experiment with Brine 2 in Table 1 indicated that at 3 ppm, no CaCO3 was formed in the brine or on the surface of the metal. However, as the SI concentration was reduced, tiny spots of CaCO3 crystals formed at 1 ppm, but they had an unusual appearance, probably because of the SI. Fig. 7 shows crystals formed on the metal surface in the presence of 1-ppm PPCA. Fig. 8 shows the metal surface with CaCO3 when 0.5 ppm of SI was used; the CaCO3 crystals appeared to be in the nucleation stage and not in the same quantity as for the base case. EDAX data confirmed that the CaCO3 crystals were in an early stage of formation.

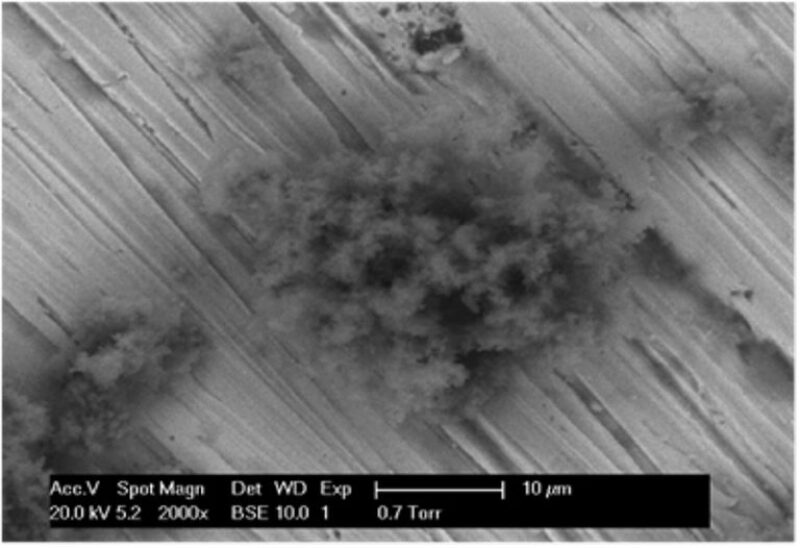
Conclusions
CaCO3 crystals were deposited in bulk solution and on a stainless-steel surface in the absence and presence of sulfide scales of zinc and lead. The coprecipitation process for these scales was similar to field conditions in which CaCO3 scales are deposited on metal surfaces and precipitated in the bulk solution. Sulfide scales have different effects on the type and medium (surface or bulk) of CaCO3-scale deposition. Crystallization was found to be sensitive to changes in the brine chemistry. When CaCO3 was coprecipitated with ZnS, fewer CaCO3 crystals were deposited on the metal surface, while more CaCO3 crystals were mixed with the ZnS flocculent. However, when CaCO3 was coprecipitated with PbS, the CaCO3 that was deposited on the metal surface exhibited distorted-crystal forms (probably a polymorph of those deposited in the base case). The corresponding crystals formed in the bulk were a mix of fully formed CaCO3 (likely) with PbCO3 crystals. This result suggests that the PbS/CaCO3 scaling system may be more difficult to inhibit in bulk solutions than the ZnS/CaCO3 scaling system. The precipitation of CaCO3 crystals in the presence of SI (PPCA in this case) demonstrated that minimum-inhibitor-concentration levels appropriate for the metal surface and the bulk solution may be very different. However, in the presence of sulfide scales, the bulk precipitation was affected less than the metal-surface deposition. This study will aid in designing better scale-treatment programs as more information becomes available regarding which scales occur and where and in what form these mixed scales occur. Such data also will help determine the type of SIs with which to treat different mixed sulfide/carbonate scaling systems.
This article, written by Dennis Denney, contains highlights of paper SPE 168182, “Sulfide Scale Coprecipitation With Calcium Carbonate,” by C. Okocha and K.S. Sorbie, SPE, Heriot-Watt University, prepared for the 2014 SPE International Symposium and Exhibition on Formation Damage Control, Lafayette, Louisiana, 26–28 February. The paper has not been peer reviewed.