I work in a technology company with lots of creative and innovative people who regularly use internal networks to share ideas and challenge the status quo of the key themes and focus areas of our business. We use these internal networks to gain consensus on difficult issues, propagate new initiatives, or share important things we have learned.
SPE Connect provides the same opportunities with its Technical Communities, which are groups of professionals aligned by common technical interests. Meeting in an electronic community, SPE members can share information, ideas, and documents, discuss topics of interest, and answer questions posed by other community members.
I belong to the projects and facilities technical community, the production discipline community, my local SPE section community, and two technical sections—Separations Technology and Water Handling and Management.
The communities are valuable resources with discussion boards and a broad range of topics covered, but the technical sections have piqued my interest as skilled practitioners use these “communities of practice” to focus on specific challenges in the production of oil and gas.
Technical sections are virtual communities that focus on a specific technical area and use a blend of meetings, webinars, publications, and blogs to pursue improved understanding of a given topic. They can be the springboard for SPE forums, technology workshops, conference themes/tracks, and collaborative industry projects. They offer a single global venue for engineers with a particular interest to build knowledge and develop industry-impacting solutions.
The Separations Technology Technical Section is flourishing with more than 500 members and a couple of SPE Annual Technical Conference and Exhibition events under its belt. The Water Handling and Management Technical Section is a more recently formed community, but already has more than 300 members and a core group of the industry’s best driving things forward. SPE launched the Flow Assurance Technical Section in January, which I will also join.
My bias is that separations, flow assurance, and water management are the core areas for effective facilities design and successful operations. You may argue with this prioritization and have your own favorites—such as project management, design for reliability, process control, or others—but this triumvirate of capabilities is essential to take reservoir fluids and deliver export quality oil and gas and has been key in the major capital projects and assets that I have been involved with throughout my career.
When we do well in the three core areas, oil or gas production is good, operating costs are low, and optimization is the focus. When we get it wrong, we see production curtailment/constraints, excessive chemical usage, poor injectivity, noncompliance with discharge limits, and a focus on troubleshooting and “putting out fires.”
Looking at some recent papers in OnePetro reinforces the thought that there is value to be realized in improving our capabilities in these areas. I, for one, am looking forward to the resources offered by the Flow Assurance Technical Section and encourage all facilities engineers to join and become active in the Flow Assurance, Separations Technology, and Water Handling and Management Technical Sections.
Modular Production Facilities Components
The topic of modularization has been part of the dialogue in the facilities world for a long time. Early work in seafloor processing and compact topsides processing used the concept as a basis of design, but the “design one, build many” philosophy has not yet matured to deliver the plug-and-play architectures conceived in the early 90s.
More recently, an article by Hart et al. (2013) highlighted the value proposition to major capital projects around modularization and cost efficiency, focusing on standardized modular designs that can lower unit cost, enable faster delivery times, and be reusable.
Again, this is not new, but with facilities becoming more costly (and seemingly complex), the argument for modularization becomes stronger. In my opinion, however, capital cost is only part of the picture.
Fully configurable, modular, standardized production system components can be assembled to create optimum facilities architectures for the full life cycle of the field. The goal is to maximize oil recovery by elimination of facilities constraints.
Ideally, I would like a catalog of modular production facilities components that could be assembled into an early phase architecture that is optimum for oil continuous phase production, then is modified simply for higher water cut production, and reconfigured again, if boosting/artificial lift/improved oil recovery is required in the final stages of field life. I want fluid based architecture flexibility and the ability to deliver an optimized facilities configuration based on reservoir deliverability.
This may seem overly complicated, but is it? For example, what if the only reconfigurations were at a fixed gas/liquid ratio and the oil/water phase inversion point? In a standardized, modular world, efficient reconfigurations would become routine, and facilities engineers would have an effective solution to the inherent uncertainty of full field life facilities design.
As an industry, we are some distance away from this vision, but we have made progress with individual component technologies, such as hydrocyclones. The challenge lies on both sides of the ledger—equipment and technology. We need suppliers and end users to buy into the concept, develop modular designs, and agree to standardization of interfaces.
In essence, this is a political, and not a technological, challenge. It may be that our projects, facilities, and construction technical sections can take this on, bring the industry together, and deliver my concept of a modular production systems catalog.
Reference
Hart, J., Phaf, N., and Vermeltfoort, K. 2013. Saving Time and Money on Major Projects. McKinsey&Company, http://www.mckinsey.com/insights/energy_resources_materials/saving_time_and_money_on_major_projects.
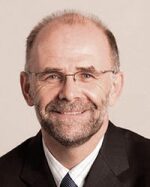
Paul S. Jones is the subsea unit manager at Chevron and a past SPE technical director of Projects, Facilities, and Construction. He is a member of the Editorial Board of Oil and Gas Facilities.