Contrary to popular imagination, which favors John Wayne stereotypes heroically rescuing the oil industry with wrench and hammer, the oilfield is a place of exquisite engineering, the match of anything on Earth, a marvel of innovation at the biggest and smallest scales.
The office-block sized blowout preventers on the ocean floor or the minute geopositioning electronics inside a logging while drilling (LWD) tool both are designed to operate perfectly within exacting environmental specifications. Almost every aspect of upstream exploitation is the result of exhaustively leveraging the glorious value chain of math, science, and engineering.
Along this trajectory, failure is met more often than success, as ideas and developments are tried out and eventually fine-tuned until something begins to work reliably. The journey is not for the faint-hearted. Whether it be one obsessive individual or a team with an equal desire to win, both energy and imagination must be sustained at every hurdle, to force progress and eventual success. This is as valid for the glamorous game-changing innovation as it is for a leap-of-faith improvement to existing technological practice.
Since the 1980s, our industry has experienced a technology renaissance all along this innovation spectrum— the oil price volatility in this modern era of our industry certainly focused minds on doing things more efficiently at less cost. As a celebration of these years of technical innovation, we now make so bold as to list perhaps 10 of the most significant contributions.
No doubt it is foolhardy to propose such a list because we all have an opinion on what should be on it. Nevertheless, there is surely enough common ground to guarantee some degree of objectivity. What may be objectionable is limiting the number to 10. Within that constraint, however, just the intellectual and practical bravado displayed surely merits all 10 to be included.
1981: Horizontal Wells Increase Production
The Soviet Union pioneered horizontal wells in the late 1960s only to turn its back on furthering the development of the practice in favor of vertical wells that were easier and faster to drill. But the mantle was picked up by Jacques Bosio, a drilling engineer with French oil company Elf Aquitaine, which needed horizontal drilling to intersect fractures and increase production from a karst reservoir found off the Italian coast, the Rospo Mare field.
In 1981, for twice the cost of a vertical well, horizontal drilling was sanctioned. The first well would bring in 3,000 B/D—more than 20 times its offset vertical well. By the mid-1980s, horizontal drilling was seeing wider adoption as a way to target thin oil and gas reservoirs in Texas, the Middle East, and the North Sea. Operators had known about these skinny hydrocarbon-bearing layers for years—now they had a way to contact them with enough surface area to make money. Bosio would go on to become the first SPE President from outside the US, in 1993.
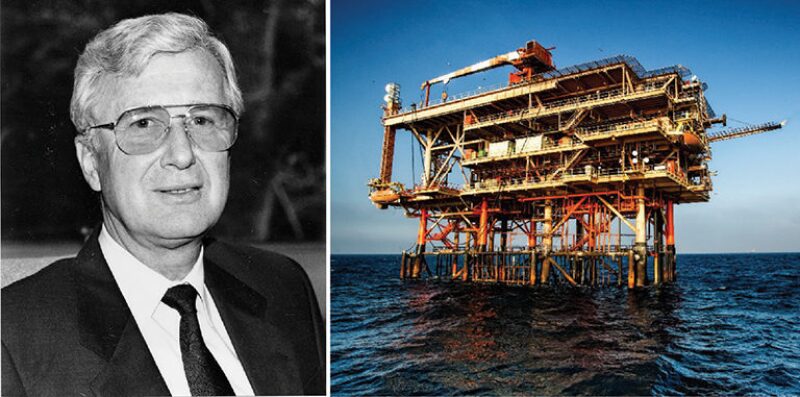
1982: The Topdrive Improves Efficiency, Begins Drilling Automation
George Boyadjieff, an aerospace engineer, spent much of his career with Varco International challenging himself to find a better way to turn to the right. His early innovations led to the iron roughneck in the mid-1970s, a notable development in its own right.
Other advances came to the drill floor to accelerate the rate of penetration, such as the power swivel, but although this saved time, pipe handling and tripping remained a bottleneck.
Contracted to help with the design of two new jack-up rigs, Boyadjieff was aware of these issues and conceived a machine that would hang from the derrick’s traveling block and drill 90-ft-long stands of drill pipe vs. the 30-ft-stands used with the power swivels. In 1982, Varco released the realization of this idea as the topdrive. By decade’s end, it would be in use on most of the industry’s large rigs and is now ubiquitous.
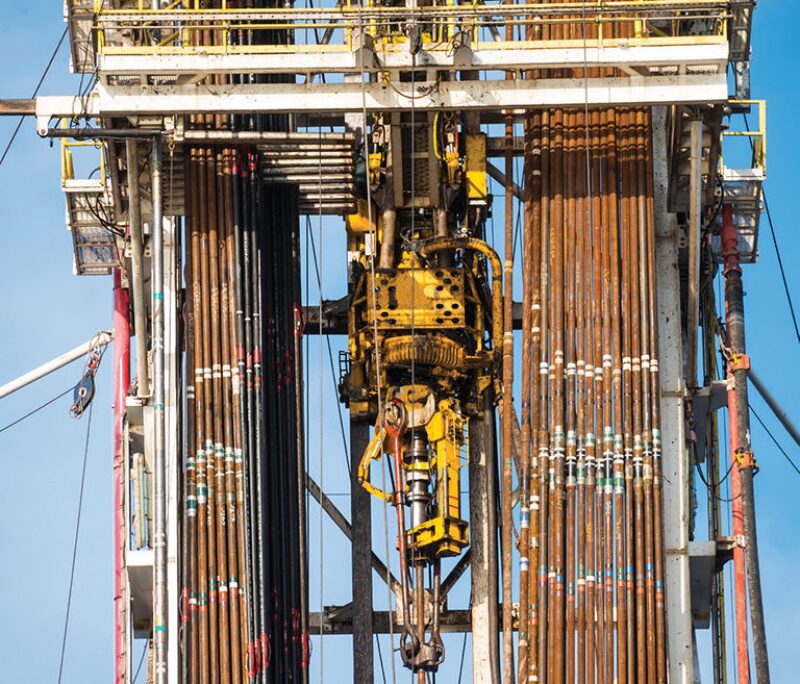
1983: Reservoir Simulation Enables Field-Wide Reservoir Development

Efforts to simulate the production of a reservoir had been under way since the early 1950s but a push by the United Kingdom’s government helped bring it to the fore. The UK Department of Energy needed to predict the future of the country’s North Sea reserves and found a theoretical physicist in the nuclear industry, Ian Cheshire, who could help.
In 1977, Cheshire and his team would release a new simulation software that presented the reservoir in three dimensions and with multiphase flow. He would later be hired by a London-based group, Exploration Consultants Limited (ECL), to perfect his simulation software for the oil industry.
His crowning achievement was released in 1983 as ECLIPSE—short for ECL’s Implicit Program for Simulating Everything. ECLIPSE enjoyed widespread adoption because it allowed engineers to alter a reservoir model’s cell sizes to help match unique geometries; in other words, it made things more realistic. ECLIPSE was later acquired by Schlumberger, which notes that the program has been cited in more than 1,500 SPE papers and is used in 70 countries.
1983: Coiled Tubing Gives New Life to Old Wells
Service companies and operators were experimenting with flexible tubing for well interventions but found that the fatigue caused by spooling and unspooling made for a short service life. In early testing, this meant more money was being made on fishing coiled tubing out of wells than from any production improvements they delivered, and operators quickly grew cold on the idea.
Then in 1983, Quality Tubing in Japan began making longer sheets of steel, which meant fewer welds were needed to create a coiled tubing system and, therefore, less points of potential failure. By the 1990s, thanks to continued improvements, coiled tubing became synonymous with workover operations. The technology went on to be an enabling vehicle for a host of downhole technologies and intervention practices.
1985: 3D Seismic Becomes Everyday Tool For Reservoir Engineering
The 2D seismic interpretations that oil and gas companies had been studying for decades left them wanting more. Vertical slices of the subsurface were essential for exploration, but not cut out for reservoir development. For landing wells in reservoir sweet spots, engineers needed a 3D cube of seismic data.
Esso performed the first 3D seismic experiment in 1964 just outside of Houston. After that, a consortium of oil companies and independent efforts fine-tuned the technique. But the computers needed to organize and interpret this new data set were expensive and so large that their use had to be rationed.
Then in the mid-1980s, the decisive development arrived as the industry started using workstations that allowed engineers to study the 3D seismic data from their desks. Pivotal players on the software and acquisition side included Sun Microsystems, Landmark Graphics, GeoQuest Systems, and the Geco seismic company. As more operators adopted their technologies, major projects would never move forward without 3D seismic. By repeating 3D seismic surveys over time, a technique called 4D seismic even became possible to monitor fluid movement in the reservoir.
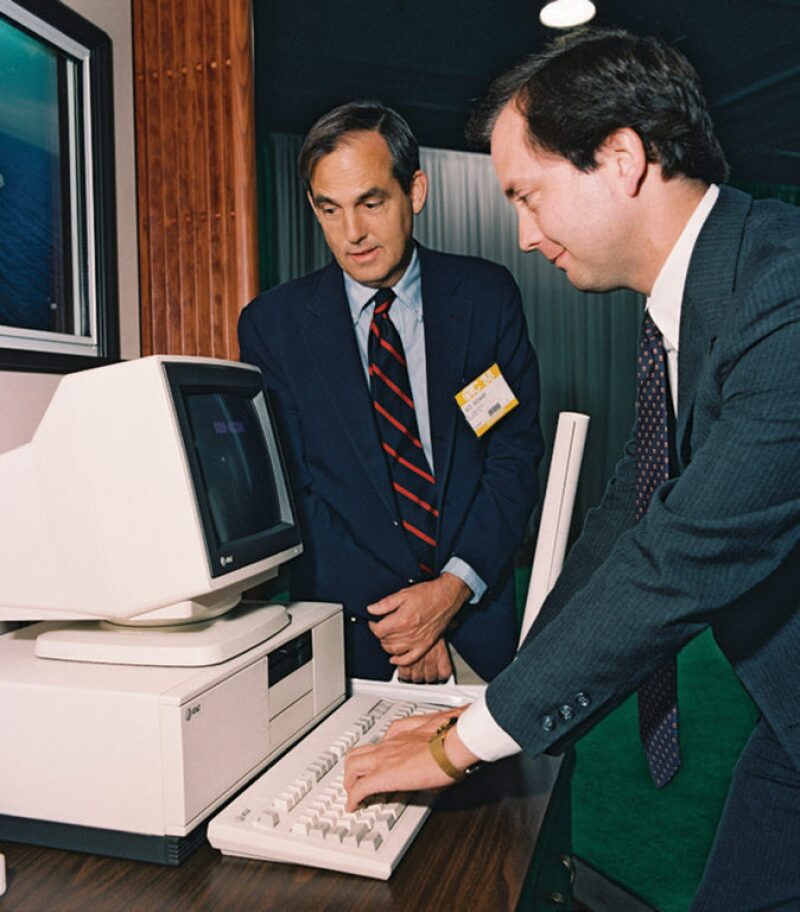
1985: MWD and LWD Guarantee the Future of Horizontal Wells
The commercialization of measurement-while-drilling (MWD) suffered from years of setbacks that included the limitations of electronics, telemetry, and industry trust. But by the early 1980s these issues started to break down and MWD would see wider use by directional drillers interested in knowing where their bits were headed.
The next step was to see if well logs could be run in a similar fashion. This innovation would become logging-while-drilling (LWD) and it promised engineers a way to evaluate formations without waiting for wireline to be run. In 1985, Sperry Sun led the market with its first LWD tool and the SPE paper it shared about the innovation pushed others to follow.
Wireline survived the introduction of LWD, but operators now had an ability to log in horizontal wells too tough to access with wireline, and even see ahead of and around the bit. This dramatically increased the odds of targeting not just the reservoir, but its most productive sweet spots.
1989: Third-Generation Wireline Formation Testing Gives A Taste of the Reservoir
Since the 1920s, engineers had some understanding that testing the formation prior to producing a well had value. Innovation here started with tools that measured reservoir pressure and flow. This led to the first buildup and drawdown tests developed in the 1950s that gave clues to a formation’s permeability. Building on this, a method was soon developed to establish the distance from the wellbore to sealing faults and other reservoir structures. Schlumberger jumped in by 1955 and made it possible to do some of this testing with wireline instead of drill pipe.
Wireline testing, however, could not reliably capture uncontaminated reservoir fluids. There was no way to control the influx of drilling mud and mud filtrate. A group of the service company’s Houston-based engineers led the breakthrough. They simply packaged into the downhole tool a way of monitoring production so you could be sure the sample was pure reservoir fluid. Brought to market in 1989, their modular dynamics formation tester combined many other technical features and bolstered the industry’s ability to certify reserves.
1990: Engineering Enters the Deepwater Era
The offshore sector had been inching into deeper waters from the late 1940s using drill ships and fixed-leg production facilities. But with more deposits waiting to be tapped in deeper waters, companies would need to invest in the development of floating production systems, especially ones that could handle the worst that the open seas had to offer.
Two of the most critical solutions came from a single man. Ed Horton, an engineer and founder of Deep Oil Technologies, is credited with inventing both the tension leg platform (TLP) and the spar. First conceived in the 1970s, Horton’s contributions would become widely adopted for offshore production by the 1990s as companies began drilling wells in depths that exceeded 1,500 ft.
His legacy is perhaps most felt in the Gulf of Mexico where TLPs and spars dominate the deepwater landscape. This includes Shell’s Perdido spar, which set the record in 2010 for the deepest subsea project on the planet. This record was nabbed in 2016 by Shell’s Stones development (also in the Gulf), which is using a Brazilian-born innovation, the floating production storage and offloading unit or FPSO, to produce from wells at depths of 9,500 ft.
1992: Inflow Control Devices For Horizontal Well Production
As companies drilled more horizontal wells and logged them, they realized that production was not evenly distributed along the wellbore. Engineers at Norway’s Norsk Hydro were keen to solve the issue in one of their offshore wells in which 75% of production was contributed by the section closest to the heel. To augment the production profile, they came up with a completion tool called the inflow control device (ICD).
First built in 1992, the ICD used filters and chokes distributed along the length of a horizontal well that could be tailored to optimize production. Others realized the opportunity the ICD represented, including Saudi Aramco, now the biggest user of the technology. For Aramco, the advent of the ICD meant it could economically develop tight formations with multilateral wells that greatly enhance the wellbore’s reservoir contact area.
1997: From Just A Hunch To A Revolution
As one of his gas fields dried up, oilman George Mitchell was inspired to find a way to produce from ultra-tight rocks called the Barnett Shale. On the shoulders of government-funded research and recent advances in MWD/LWD, Mitchell and his engineers seized on the idea that they might be able to do this by combining horizontal drilling with hydraulic fracturing.
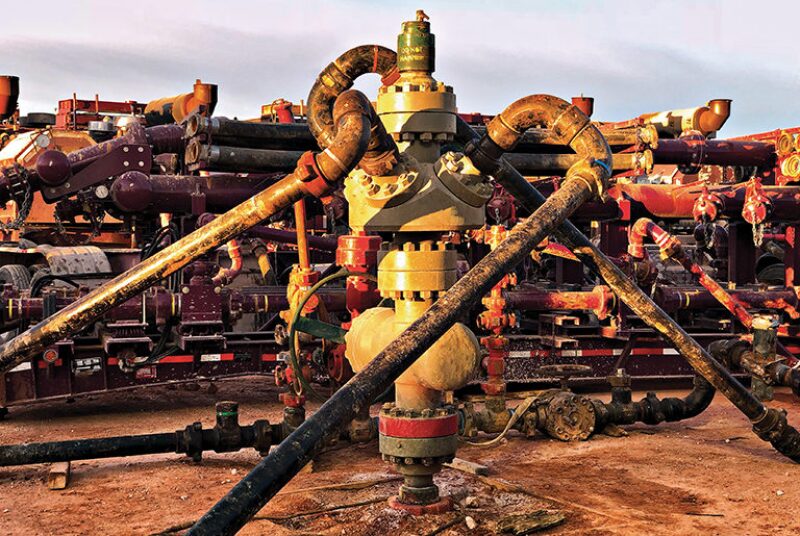
The first of their trial wellbores was drilled and fractured in 1991, but many attempts failed to unlock acceptable quantities of gas. Then in 1997, Nick Steinsberger, a petroleum engineer working for Mitchell, earned his entry into the history books with an accidental discovery. Inadvertently blending gel into the fracturing fluids resulted in a more watery mix than had been previously used. This appeared to do the job.
The technique would become known as a “slickwater frac” and it enabled Mitchell Energy to double its overall gas production. The company was sold to Devon Energy in 2002 and a few years later headlines would report that the shale revolution had been born. In the next decade, contrary to historical trends, the US became the largest combined producer of oil and gas. The tandem of hydraulic fracturing and horizontal drilling is now used globally as programs of varying maturity are under way in Canada, Argentina, China, and Saudi Arabia.
![]() | Henry Edmundson is the director of R9 Energy Consultants based in Cambridge, England. He spent 45 years with Schlumberger where he was the founding editor of the Oilfield Review and latterly global director of the company’s petroleum technologists. The entries in this list are based on excerpts taken from Edmundson’s book, Groundbreakers: The Story of Oilfield Technology and the People Who Made It Happen, which he co-authored with Mark Mau and published in 2015. |