To maintain zonal isolation throughout the life of a high-pressure/high-temperature (HP/HT) well, the cement sheath must perform reliably at temperatures that can exceed 315°C. Weighting materials have largely been assumed to be inert with respect to set Portland cement; however, the present study reveals that this assumption may be false in HP/HT environments in which well temperature exceeds 260°C. Some weighting agents may react with the set Portland cement, causing strength loss and increased permeability. Fortunately, this effect can be prevented, and the set-cement integrity can be preserved.
Experimental Procedures
Cement Blends. Five solid cement blends were prepared; their compositions are presented in Table 1. The blends were formulated according to the engineered-particle-size concept, wherein the volumes of coarse, medium, and fine particles are optimized to maximize the packing volume fraction (PVF). An increase in the PVF reduces the amount of mix fluid required to prepare a stable and pumpable slurry, and it increases the strength and reduces the permeability of the set cement.
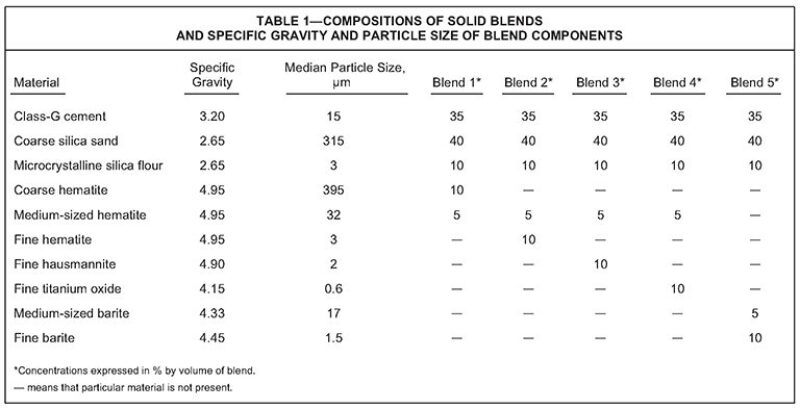
The five blends contained 50% by volume of blend (BVOB) silica, which is sufficient to allow formation of the calcium silicate hydrate mineral xonotlite [Ca6Si6O17(OH)2] upon curing at temperatures above approximately 160°C. The weighting-agent concentration was held constant at 15% BVOB.
The slurries were prepared according to the recommended American Petroleum Institute (API) procedure.
Strength. The five slurries were placed in an ultrasonic cement analyzer (UCA) fitted with a dual-cylinder high-pressure pump that provided pulseless metering. They were cured at a final temperature and pressure of 302°C and 122 MPa, respectively, for periods of up to 100 days. Two additional tests were conducted at 274 and 288°C at a final pressure of 122 MPa.
It should be kept in mind that the UCA does not provide absolute strength values at such elevated temperatures because the transit time increases significantly during the heating period; therefore, one should consider strength trends vs. time. When possible, the cured-cement samples were crushed with a hydraulic press to obtain an accurate compressive strength. The recommended API procedure was followed.
Permeability. When possible, water-permeability measurements were performed on 5.08-cm-long, 2.54-cm-diameter cement cores with a liquid permeameter operating at a confining stress of 2.76 MPa.
X-Ray Diffraction (XRD) and Scanning Electron Microscopy (SEM). Crystalline structure and phase analysis were determined by performing wide-angle XRD experiments. The cured cement was ground to a fine powder (<325 mesh), dried with acetone, and dried again with ethyl ether.
The microstructure of the cured cements was examined with SEM, and elemental X-ray microanalyses were performed with an energy dispersive spectrometer. Before examination, a thin layer of gold was deposited on the cement surfaces.
Results
Blend 1. The cement slurry contained coarse and medium hematite, and the slurry density was 2275 kg/m3. The UCA data (Fig. 1) revealed that the cement strength reached a maximum value after approximately 6 days of curing at 302°C and 122 MPa. Then, it underwent a slow but minimal strength decrease until the test was terminated at 19 days.
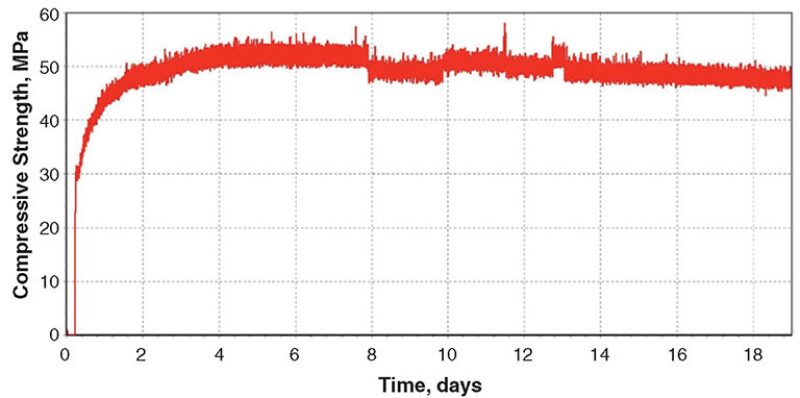
The cement sample was then removed from the UCA, and a core was prepared for compressive-strength and permeability measurements. The compressive strength was 29.7 MPa, and the water permeability was 0.011 md.
XRD analysis showed that the set cement was composed mainly of xonotlite, quartz (SiO2), and hematite.
Blend 2. This blend was compositionally similar to Blend 1; however, the coarse hematite was replaced by fine hematite. The slurry density was 2275 kg/m3. The UCA chart (Fig. 2) showed that, as in Blend 1, maximum strength was achieved after 6 days of curing. However, unlike in Blend 1, significant strength loss occurred during the remainder of a 52-day curing period at 302°C and 122 MPa.
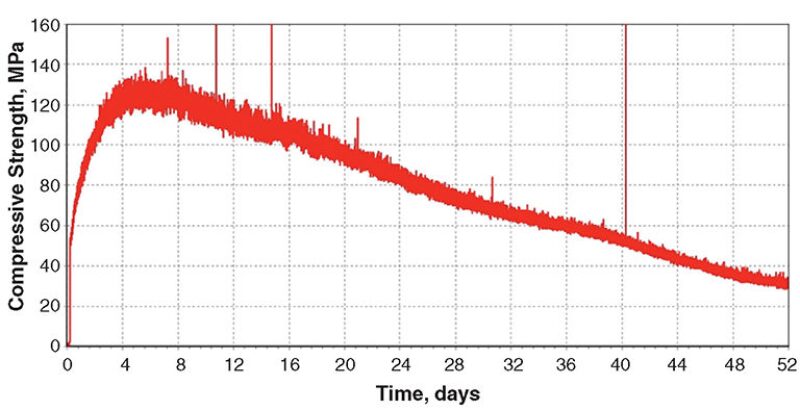
A second sample of Blend-2 slurry was cured at 302°C and 122 MPa; however, the test was terminated after 6 days to obtain a sample of the set cement when it was close to its maximum strength. At Day 6, the compressive strength and water permeability were 27.4 MPa and 0.007 md, respectively. After curing for 52 days, the compressive strength had reduced to 12.2 MPa and the water permeability had increased to 0.15 md.
XRD analysis of the 6-day sample gave results similar to those of Blend 1—xonotlite, quartz, and hematite. However, the 52-day sample revealed a different composition—andradite (Ca3Fe2Si3O12) and quartz, with minor amounts of xonotlite and hematite—indicating that the hematite had reacted with the xonotlite.
Blend 3. In Blend 3, the coarse hematite was replaced by an equal volume of fine hausmannite. The slurry density was 2275 kg/m3. The set cement reached a maximum strength value (Fig. 3) after approximately 5 days of curing at 302°C and 122 MPa; then, it steadily declined to a plateau value at 16 days. The UCA test was terminated at 20 days.
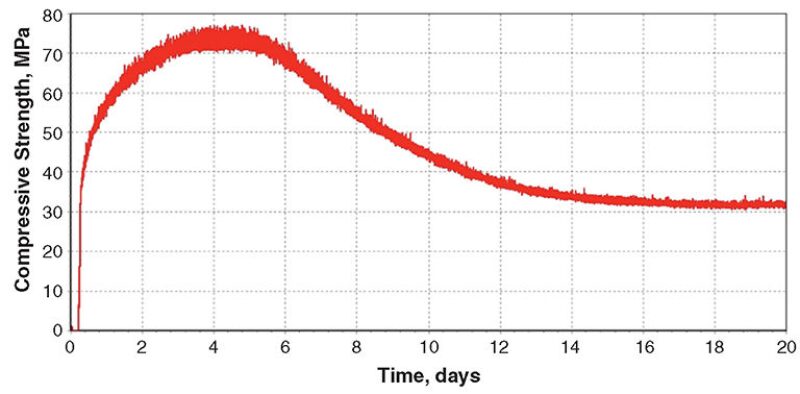
After removal from the UCA, the compressive strength and water permeability were measured—20.6 MPa and 0.77 md, respectively. XRD analysis showed that the cement matrix was composed mostly of johannsenite (CaMnSi2O6). There were minor amounts of xonotlite, quartz, and hematite present and a trace amount of hausmannite. Johannsenite is the product of a reaction between xonotlite, quartz, and hausmannite.
These results show that johannsenite is more stable than xonotlite at 302°C and 122 MPa.
SEM analysis revealed a less-compact microstructure than that seen in Blend 1.
Two additional UCA tests of the Blend-3 formulation were performed at lower temperatures—288 and 274°C. The pressure was maintained at 122 MPa.
At 288°C, the maximum strength was attained after 15 days of curing, as opposed to 5 days at 302°C. At 274°C, a 28‑day curing period was required to achieve maximum strength. In both cases, the strength declined to a plateau level.
XRD analysis of the sample cured at 288°C revealed that johannsenite was still the major phase but was not as abundant as in the sample cured at 302°C. The minor phases were xonotlite, quartz, hausmannite, and hematite. In the sample cured at 274°C, the cement matrix was predominantly xonotlite, quartz, hausmannite, and hematite, with a trace amount of johannsenite.
Blend 4. Titanium oxide has a specific gravity of 4.15 and could possibly be used as a weighting material. The Blend‑4 cement slurry containing fine titanium oxide and medium hematite was cured in the UCA at 302°C and 122 MPa. The slurry density was 2235 kg/m3. As shown in Fig. 4, maximum strength was attained after 8 days of curing, followed by a significant strength decline until approximately 36 days.
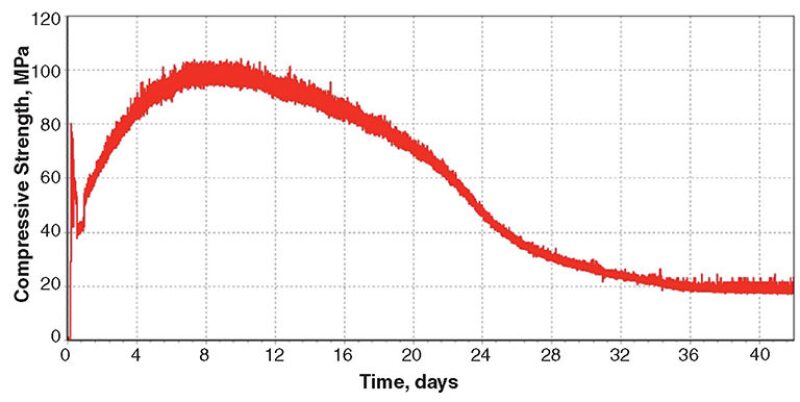
XRD analysis showed that the cement matrix was mainly composed of titanite (CaTiSiO5) and quartz. Xonotlite and titanium oxide were not detected.
Blend 5. This blend contained fine and medium barite. The density of the cement slurry was 2225 kg/m3. The UCA data (Fig. 5) show that maximum strength was attained after 6 days of curing at 302°C and 122 MPa. Very little strength loss was observed over a 25-day period, after which the test was terminated.
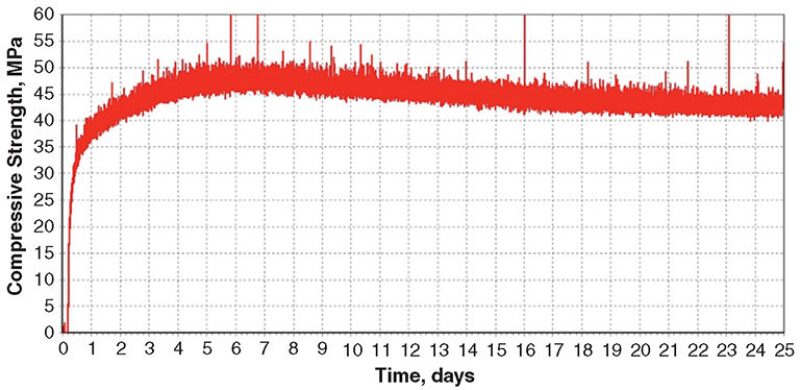
After removal of the cement sample from the UCA, the compressive-strength and water-permeability measurements were 26.0 MPa and 0.008 md, respectively. XRD analysis showed that the cement matrix was composed of xonotlite, quartz, and barite. Apparently, no reactions took place between barite and xonotlite.
Discussion
Blends 1 and 2 contained hematite as the weighting material and were cured under the same conditions. Both blends contained medium hematite; however, Blend 1 also contained coarse hematite and Blend 2 contained fine hematite. During curing in the UCA, Blend 1 exhibited minimal strength loss, whereas Blend 2 lost 76% of its original strength. Xonotlite was the principal phase in the Blend-1 sample, and andradite replaced xonotlite in the Blend-2 sample. A second experiment with Blend 2 showed that, at the time of peak strength in the cement (6 days), xonotlite had not yet reacted with the hematite to form andradite. The difference in behavior between Blend 1 and Blend 2 may be attributable to the higher surface area of hematite in Blend 2, making it more reactive. The results also suggest that Blend 1 might eventually lose significant strength at much longer curing periods. The formation of andradite was also associated with an increase in water permeability. For optimal zonal isolation, water permeability should be less than 0.1 md. Therefore, using hematite as a weighting material may not be appropriate at curing temperatures as high as 302°C.
Blend 3, containing medium hematite and fine hausmannite as the weighting material, displayed significant strength loss and permeability gain when cured at 302°C. The loss is attributed to the conversion of xonotlite to johannsenite. Two additional tests at 288 and 274°C revealed that strength loss was not as severe and less johannsenite had formed.
Blend-4 test results revealed that titanium oxide is not an appropriate weighting material at 302°C. Xonotlite had been fully converted to titanite, resulting in an 80% strength loss during the curing period.
Blend 5, containing a blend of fine and medium barite, performed acceptably at 302°C. Minimal strength loss was observed, possibly because xonotlite became more highly crystalline, and the water permeability was well below the 0.1-md limit. In addition, xonotlite did not react with the barite.
Conclusions
The study demonstrated that iron oxide (hematite), manganese oxide (hausmannite), and titanium oxide are not inert with respect to set Portland cement when cured at 302°C and 122 MPa. Analytical data show that these metal oxides react with xonotlite to form other mineral phases, causing a loss of strength and an increase in water permeability.
In contrast, barite does not react with xonotlite under these conditions. It behaves as a chemically inert filler, thereby preserving the set-cement performance. Consequently, barite is the most appropriate weighting material for thermal cement systems.
This article, written by Editorial Manager Adam Wilson, contains highlights of paper SPE 163544, “Performance of Thermal Cements With Different Weighting Materials,” by Jean-Philippe Caritey, SPE, and Jason Brady, SPE, Schlumberger, prepared for the 2013 SPE/IADC Drilling Conference and Exhibition, Amsterdam, 5–7 March. The paper has not been peer reviewed.