This column was written in mid-February before the pandemic declaration and work from home mandates.
Success is neither magical nor mysterious. Success is the natural consequence of consistently applying the basic fundamentals.
This month’s column is dedicated to technology evaluation, an area where I have spent the majority of my career. For at least 2 decades, I have been approached almost weekly by either one of my engineers or an inventor who has found the “next best thing that will revolutionize our industry.” While I have been a champion for innovation and technology development, I have also applied critical thinking in forming my opinion of such claims. The first questions I always ask myself are: “Do I need this new technology?” and “Do I understand the root cause of the problem well enough to determine if applying existing technology and accepted practices cannot solve it?” To adequately answer these questions, a good understanding of the fundamentals, such as fluid or mechanical dynamics, is often needed. Is this new tool or method genuinely innovative, or has it been born out of engineering ignorance?
Being ignorant is not so much a shame, as being unwilling to learn.
For context, let me provide an example. The downhole rod-driven reciprocating pump has existed since the late 1800s (Beckwith 2014). For a century, the design practices for determining the optimal tolerance between the downhole plunger and barrel were theoretical equations and often used rules of thumb. Too large of a tolerance would lead to excess fluid slippage and decreasing efficiency of the pump. Too tight of a tolerance could lead to rod buckling and the inability to handle particulates such as sand. As an industry, we typically erred on the side of caution toward tighter tolerances, and many “gadgets” were invented to prolong the life of the downhole rods and pumps and to counter issues caused by this design practice. It wasn’t until the late 1990s when a group of operators in the Permian Basin began to question the validity of the existing equations and design philosophies.
These Permian operators collectively funded research at Texas Tech University to understand the dynamics of the fluid slippage between a plunger and barrel under a variety of conditions. Through intensive research and experimentation of the fundamentals, they were able to develop a new equation, later named the Patterson Equation, which proved that larger tolerances did not lead to excess slippage (Nickens et al. 2005). The gained understanding of these previously accepted fundamentals had significant implications throughout the industry. Operators began to increase their plunger and barrel tolerances in their designs, and they no longer needed gadgets. As a result, the run life of the downhole equipment increased considerably. The value gained by those operating companies collaborating with the university far exceeded their original investment. However, the industry was the greatest benefactor of the publication of the research.
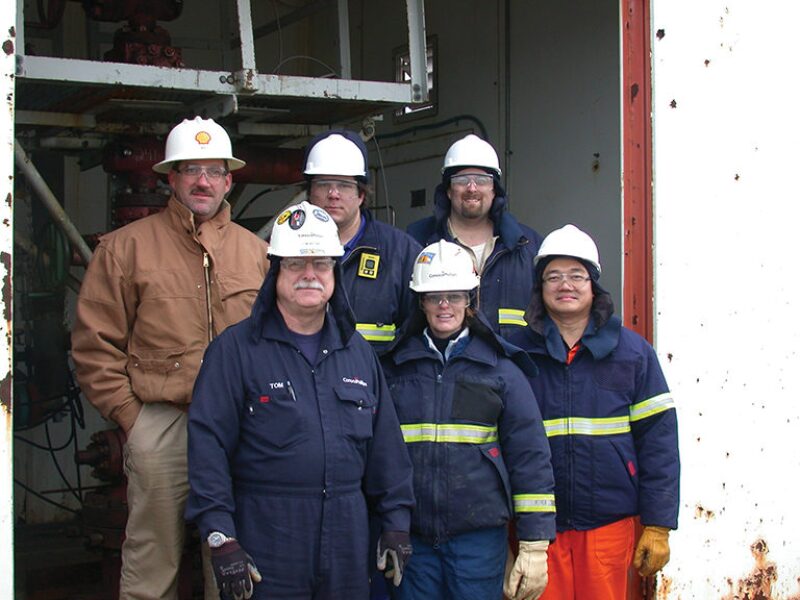
There are more examples I could cite from my own experience, ranging from gas-lift valves to flow-control devices, and I know that my SPE colleagues could reference other cases as well. These gadgets that I keep referring to are what I like to call “bandage technology,” which is a technology that appears to provide a solution but doesn’t address the root cause of the problem. Many field-level challenges can be overcome with the application of basic fundamentals. There are situations when a quick solution is needed to reduce downtime, for example, but in most cases, bandage technology should only be treated as a temporary solution. The installation of unnecessary components can also lead to other negatives, such as increasing costs and raising the overall complexity of the system.
Learn the fundamentals of the game and stick to them. Band-Aid remedies never last.
I was fortunate to work in this industry during a time when companies (operators and manufacturers) funded research and testing programs to understand fundamentals and validate the performance and operating envelope of technology. Sadly, I have seen these types of research programs and consortia dwindle in recent years. Who now is researching the fundamentals we must use in our industry? Who is supposed to be doing this research, and, more importantly, who should be funding it?
The biggest issue I see is the apparent lack of interest by some operating companies to understand these fundamentals. Several years ago, I approached an asset manager with a research proposal to better understand the performance of unconventional completion designs. I was told that he did not care why Completion A outperformed Completion B in the first 3 months and that the initial production data were all that he needed. I have also witnessed operating companies applying pressure to manufacturers to commercialize technology that has not been fully validated and understood.
C-FER Technologies, located in Edmonton, Alberta, is where I have historically gone to perform validation testing and experiments to understand the fundamentals of artificial lift equipment. I reached out to their managing director, Dr. Francisco Alhanati, to see what trends they are experiencing with the commissioning of research and testing.
He stated, “We have noticed a decrease in demand for new technology validation testing since the industry downturn in late 2014. This is consistent with the decrease in overall capital investment from operators, in particular those associated with new field developments or existing field production capacity expansions. That said, there has been significant work being commissioned to qualify and evaluate technologies with the potential to improve operational efficiency and equipment reliability, reduce operational costs, and address environmental concerns.”
I find comfort in Dr. Alhanati's observations that investments in technology evaluations are beginning to trend upward. However, there also appears to be a global perception that data science alone will solve our industry’s biggest challenges. There is increased pressure on the petroleum engineering academia to add data science courses, which could come at the expense of longstanding fundamental engineering courses. It is my opinion that data science will undoubtedly help our existing technology to be more efficient and reliable, but it cannot replace fundamental R&D. Dr. Alhanati shares a similar opinion: “From our perspective, the industry is learning that a pure ‘data-driven’ approach has a poor chance to succeed, for a variety of reasons, and you need to bring some subject-matter expertise and engineering understanding of the application and the equipment to improve such a chance (even if it is just to help classify/label the data and assess its quality). In some cases, you may need some full-scale testing, with full control of the influential variables, to validate your models of how things really work.”
There will be no silver bullet. Rather it will be a combination of technologies.
As a professional technical society, what role can SPE play to strengthen our understanding of the fundamentals and their dissemination throughout the membership? Arriving at viable solutions will involve collaboration between companies, academia, and research institutions, as well as disciplines and industries outside of oil and gas.
The high level of facilitation and coordination required is an area of strength for our society, and we need to capitalize on that. At the same time, we need to educate our members, especially our young professionals, on the importance of learning the technical fundamentals. We must realize that there is no magic solution or silver bullet that could ever replace them.
References
Beckwith, R. 2014. Legends of Artificial Lift—Part 1. J Pet Technol 66 (10): pp. 101–107. 1014-0101-JPT.
Nickens, H., Lea, J.F., Cox, J.C., et al. 2005. Downhole Beam Pump Operation: Slippage and Buckling Forces Transmitted to the Rod String. J Can Pet Technol 44 (5): pp. 56–61. PETSOC-05-05-05.
The Research and Development Technical Section will be reviewing SPE’s five grand challenges that our industry needs to overcome. What additional technical challenges do you think we as an industry must focus research on? Please send your response to president@spe.org. To hear Shauna’s President’s Column via podcast, please go to www.spe.org/en/podcasts.