The beasts of burden in the US shale sector are the pressure pumping units that takes the theory of hydraulic fracturing and put it into practice. Yet, for much of the past 2 decades, these high-horsepower machines have seen relatively scant technological advancement.
Then the industry downturn happened. Hundreds of older units were scuttled. Profit margins for what was left were squeezed as tight as ever. Budgets to invest in new, unproven technologies were scarce.
Modernizers from various corners of the industry rose to challenge the idea that pressure pumping technology is stagnate, or simply “dumb iron.” For the past couple of years, this crusade has been led by the largest pressure pumping firms in the US by horsepower, Halliburton and Schlumberger. Both have introduced fracturing fleets that, by automating key manual tasks, are accelerating completion times and improving machine reliability.
But they are not the lone innovators. On the other end of the spectrum are five lesser-known technology developers, most of them startups. Their new software and hardware products reveal that wherever you look on a fracturing spread, there are costs to trim and new efficiencies to be gained.
Evolution Well Services
The problem: Stimulating an unconventional reservoir requires a lot of horsepower, which means burning a lot of diesel fuel. Even a small spread consumes around 9,500 gallons of diesel each day, costing near $30,000. Additionally, diesel-powered pumps dictate the construction of large and expensive well pads. As a rule, a single fleet needs up to three times the area of a drilling rig.
The solution: Based in The Woodlands, Texas, this startup uses 100% natural gas-burning turbine generators to feed its custom-designed hydraulic fracturing pumps.
These electrically powered pressure pumps, known as “e-fleets,” leverage the price arbitrage between diesel fuel and natural gas. Because of the high consumption rate of the machinery, the delta translates into quick and scalable savings.
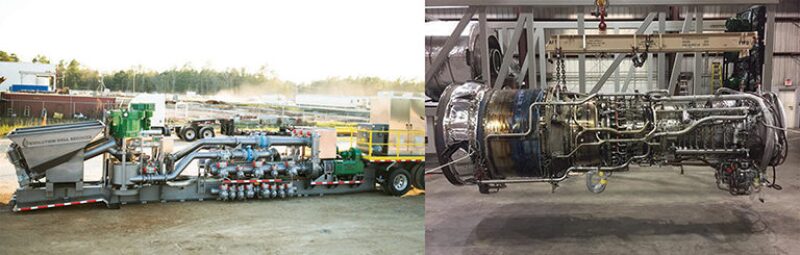
“On a monthly basis, that fuel substitution represents somewhere between $1 to $1.5 million—and that gets everybody’s attention,” said Ben Bodishbaugh, chief executive officer of Evolution.
Realizing such savings does require that a well site be near a ready supply of natural gas, which may be the e-fleets’ biggest limiter. Evolution points out that its system was designed to deliver the best economics by using unprocessed or lightly processed field gas that can be piped directly to the pad from producing wells or associated gas systems, which could help operators dial back flaring.
The firm deployed its first e-fleet in 2016 and has since expanded to six fleets. Each one consists of eight pumping units compared with conventional fleets in the US that range in size from 20–25 units.
“We have more horsepower in a smaller package,” said Bodishbaugh, adding that while large conventional pumps max out at 2,500 horsepower, the upper limit for an Evolution system is 7,000. “By utilizing electric motors as the prime movers of our equipment, we can achieve a much higher power density than with a diesel engine or hydraulics.”
The knock-on effect of having a slimmer capital profile is that it takes fewer people to complete each well. Evolution crews consist of 12 people—half the sector average. And unlike most completions sites, this crew spends almost all of its time within the relative safety and comfort of one of the company’s data trailers. From there, personnel can control the pumps remotely.
A leaner fleet may not be a big selling point for operators in the wide-open spaces of Texas. But it is for those working amid the rolling hills of West Virginia or Ohio where leveling out a pad site large enough for a completions spread costs around $2 million.
Removing diesel from the equation also reduces traffic on the pad since a constant stream of refueling trucks is no longer needed. Evolution argues that piping natural gas into its turbines enhances the safety of the worksite since the shale sector has a history of diesel fuel leaks, some that led to serious fires.
Operators may be attracted to e-fleets for a few other reasons still. Increasingly, North American operators are responding to climate change concerns with initiatives to reduce emissions. Gas turbines do not equate to zero emissions, but Evolution calculates its technologies have prevented more than 300 tons of CO2 that would have otherwise been released using conventional pumps.
KCF Technologies
The problem: As a result of their intense power, pressure-pumping units are subjected to as much wear and tear as any other piece of oilfield equipment, making onsite failures common.
Some of the hardest problems to deal with are caused by the vibration and cavitation generated as the pumps are running full bore during the stimulation of a horizontal well. But because standard units are not equipped to detect such movements, critical components can break apart suddenly and without warning, leading to nonproductive time and safety risks.
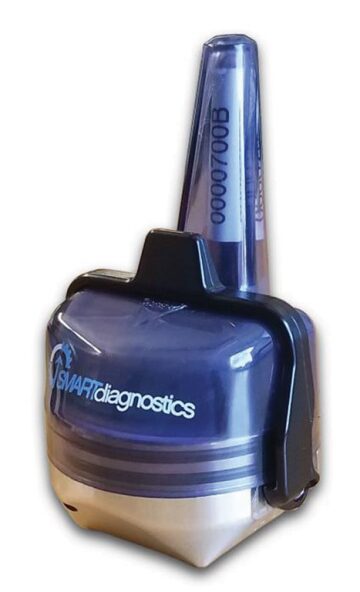
The solution: KCF Technologies has developed vibration sensors that attach to several components of a pumping unit. The firm analyzes the data from its headquarters and, when issues are detected, its technicians alert field crews if a pumping unit should be proactively taken out of service for maintenance. Historically, the industry has not monitored fracturing equipment in this way.
KCF’s entry into the unconventional scene is built on 30 years of industrial vibration research and US military contracts. The company’s sensor technology has been deployed on helicopters and nuclear submarines.
In the past few years, the firm has seen its monitoring technology used on 90 fracturing fleets across the US. US Well Services, which has KCF sensors on all its fleets, found in the first 6 months of using them that it reduced nonproductive time to 19 minutes a day.
According to KCF, coupling its sensor technology with a centralized monitoring center has resulted in an 80% reduction in unplanned downtime due to machine failures. “That means 80% of the dangerous fires—both figuratively and literally—that would have started, never did,” said Ben Lawrence, the vice president of KCF.
Lawrence added that some clients are using the vibration data to optimize how they run the pumps to extend their service life, sometimes up to 40%. Pressure pumpers are also selecting more durable parts and are working with their suppliers to redesign other components to last longer.
The biggest impact that KCF’s technology has had on any single component is on what is known as a fluid end. The firm’s research concluded that fluid end cavitation is the most undiagnosed cause of failure in the hydraulic fracturing sector.
Weighing as much as a car and costing between $50,000 and $80,000, fluid ends are where the slurry of water and sand undergoes a rapid pressurization from about 100 psi to 10,000 psi.
“It’s an incredibly violent process,” explained Lawrence. “And when your plumbing is not correct on that fluid end, what happens is you get air inside that giant hunk of steel—the fluid end—instead of just water and sand.” This scenario can lead to a sudden release of energy, resulting in severe and fatiguing cavitation.
Failures come as these steel blocks eventually crack open, releasing a geyser of pressurized fluids, or send a rod flying into the air. Moreover, the cavitation that begins in a fluid end can ripple forward and backwards into the pumping unit, causing further damage to other components. But with dedicated sensors, and real-time feedback, pump operators know which of their units are acting up and can prevent disruptions in a treatment schedule by shifting pressures to standby units.
EKU Powerdrives
The problem: Diesel-powered pressure pumping tractor-trailers are started and shut down manually. But since their hydraulic might must be ready to ramp up any time, all engines are left running for hours in between each frac stage.
While the practice saves time and reduces operational complexity, the idle time may account for half of an engine’s running hours, counting against its service life and warranty. Idling also burns between 8–22 gallons of fuel per hour, depending on the engine type.
The solution: EKU Powerdrives built an automated control system that shuts down a pumping unit whenever it is not needed to pump. Only when the data van demands pressure are units automatically started, resulting in a 90% reduction of idle running time. Looked at another way, a pumping unit using this system should complete twice as many fracturing stages over its life.
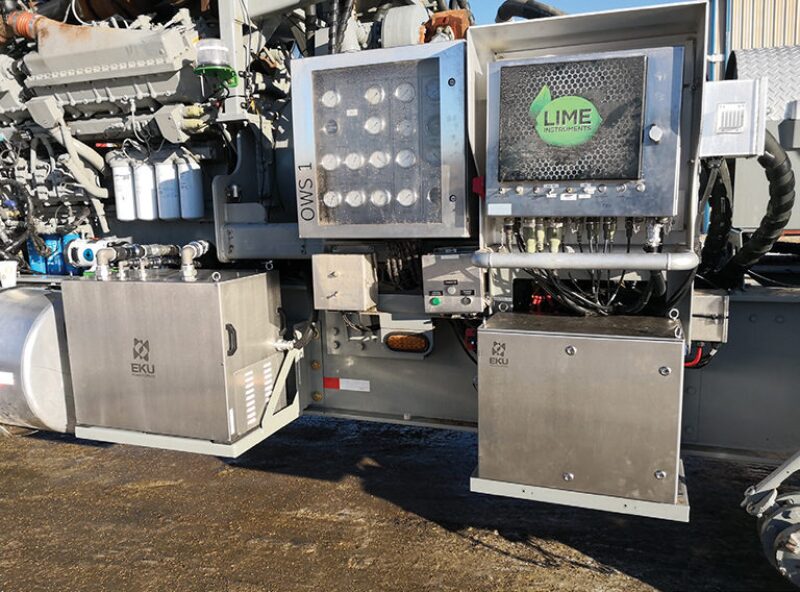
The emerging technology is a combination of newly designed hardware and software. Developed in Germany, the system has found its home as a bolt-on addition to more than 70 pressure pumping units in the US.
Before he focused on making pressure pumping more efficient, Edward Eichstetter, cofounder and chief executive officer of EKU, worked on the control systems that manage battery usage in hybrid and electric vehicles. While a college student in Stuttgart, Germany in 2012, he met the firm’s two other founders during a project that delivered the world’s fastest accelerating electric car.
By 2015, the trio started EKU to address the lack of control system technology in industrial vehicles. Their first target would be the US pressure pumping market.
Eichstetter said high-end electric vehicles and luxury cars that cost around $100,000 might have more than 100 control systems connected to everything from the engine and brakes to the power windows and entertainment system. “But when you buy a frac pump, you pay $1.5 million and you have three controllers on it,” he said. “If you install our system, you go from three to eight.”
The bolt-on has delivered other ancillary benefits:
- Preventative maintenance can be deferred from every 2 months to 4 months.
- Battery units are prevented from draining prematurely, resulting in zero battery replacements.
- Reduced idling lowers refueling requirements.
IOT-eq
The problem: Operators and service companies are looking for ways to move data from the sensors on fracturing equipment into their headquarters where they can be run through analytics or machine learning programs to improve completion designs. However, the digital trend has revealed a major bottleneck: older generations of fracturing fleets in use today were not built to store, transmit, or process high-resolution data.
The solution: Thanks to the proliferation of software programming talent, building a control system for multimillion-dollar machines from scratch is easier and cheaper than ever. IOT-eq was founded in 2016 to seize upon this converging technological sweet spot.
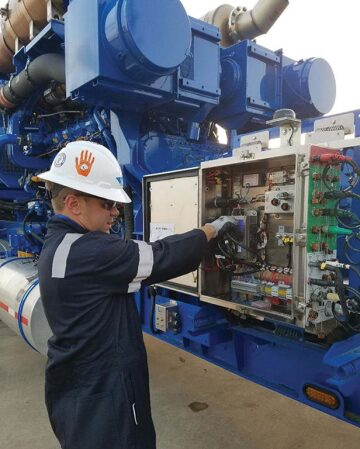
The startup developed its own field communications system, known as a gateway, to move large volumes of data via the expanding cellular networks being built to cover remote oilfields found across the US. It has also focused on creating new software and computers to do more with the data onsite.
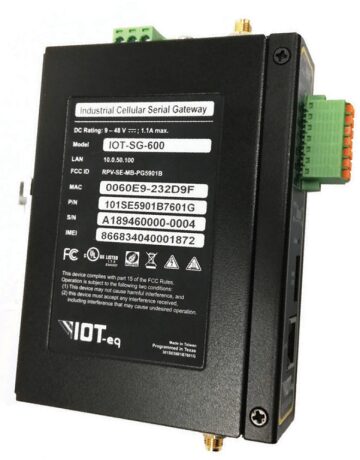
While their steel frames remain useful, these older fleets often run on computers designed by equipment manufacturers that do not meet the needs of big data initiatives. “They did such a great job designing these systems 10 or 15 years ago that they have lasted this long—but when you don’t update that frequently, then you’re basically at a point 10 years down the road where everything is obsolete,” said Jay Hunt, the director of sales and refurbishing at IOT-eq.
Service companies feeling this problem are sending pumping units and data vans to IOT-eq’s facility outside of Houston where they are updated with new and easily programmable control systems. Out are the suitcase-sized computers that are costly to reprogram and troubleshoot. In are lower-cost, more capable computers about the size of a football.
“What we’re talking about here is smaller, lighter, faster—and then edge computing at the source,” said Hunt. Edge computing describes field computers that can process large chunks of information at the source of collection. After analyzing the data, smaller packets containing the results of the analysis are sent back via the gateway and into the cloud. The point is to reduce storage and transmission costs along with addressing latency issues.
IOT-eq says its edge device churns through 1,000 data points per second from sensors that measure pressure, flow, and fluid density. This information can be used to assess equipment fatigue. Or it can feed the hydraulic fracture and geomechanical models that engineers are running inside the data van, enabling them to rapidly assess stage performance.
To tie its hardware together visually, IOT-eq has taken one more step and created a customizable dashboard for those working onsite and in the office. The software frees users from a locked-down interface—the industry norm—and allows them to focus on whatever data points that they see as most important.
MGB Oilfield Solutions
The problem: A completions spread in North America is a jigsaw puzzle of industrial equipment and machinery—one with too many pieces. As the assembly is brought together, there are systems that serve only temporary uses, such as the tractor-trailers that haul fracturing pumps from well site to well site. After arriving on site, this capital spends most of its time taking up valuable real estate while also imposing unnecessary costs.
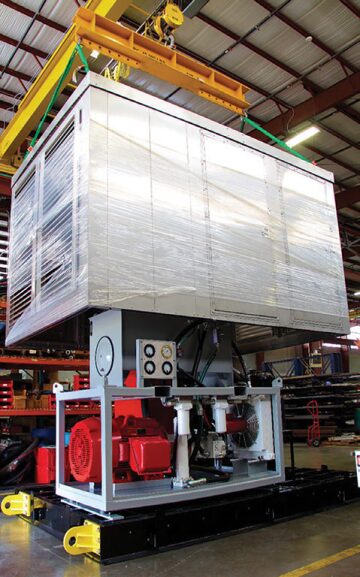
The solution: A multipurpose power system developed by MGB Oilfield Solutions enables companies to decouple tractor-trailers with the pressure pumps, while providing several other support functions. The broader concept is to take independent systems—electric generators, pneumatic air compressors, and hydraulic pressure sources—and replace them with a single source of energy.
With this technology, pumping units can be delivered to a job site and their tractors rerouted for other work elsewhere. This reduces the spread’s headcount and footprint on a pad by up to 35%.
Based on the outskirts of Houston, MGB points out that the personnel who drive the tractor-trailers require commercial driver’s licenses, which thanks to supply and demand, often fetches a wage premium of $1,800 per month. Moving the trailers offsite means drivers can be hired for driving, leaving more room for service providers to hire non-commercial licensed crews for the job of completing wells.
Besides the trailers, this approach to depopulating a crowded job site extends to generator sets and the mechanics’ trucks used to supply compressed air to wireline or pumping crews.
Mark Bishop, the chief executive officer of MGB, was inspired to create this technology package after spending most of his career working on offshore oil and gas projects. In that sector, every minute of nonproductive time is scrutinized, making redundancy a paramount priority.
While the North American fracturing spread is not quite there, “the pendulum is swinging,” said Bishop. “I think mindsets are going to change, but creating redundancy always comes with a cost.” The trick, he added, is to secure redundancy in a cost-effective way.
A single MGB power unit can provide enough electricity or hydraulics for the entire fracturing spread, but for the sake of redundancy, MGB deploys two power units to each site. One powers the left bank of pumps along with the data van, while the other powers the pumps to the right side of the wellhead and the sand conveyer system.
Equipment operators can elect to use the primary drivers on some of their equipment, such as the conveyer belt that has its own engine to move sand from storage and into the blenders. If that engine fails though, the status quo is to activate a standby conveyer belt. MGB’s system presents the opportunity to forgo renting a standby conveyer belt. Instead, the power unit can connect directly to the failed conveyer and provide all the hydraulic power needed to move sand& again.
Similar to the objective of the EKU technology, the MGB unit also connects into the fracturing pumps and enables them to be remotely controlled from the data van. Early field results show that such control over the engines cuts fuel use by up to 40%, while also trimming 85% of the idling that Bishop argues, perhaps counterintuitively, is a major contributor to wear and tear.
He explained: “An engine at idle is more damaging than an engine operating at a full load because you don’t actually have enough pressures and flow within the internal circuitry to effectively lubricate things.”
In addition to its power technology, MGB has produced several other innovations that include a well site lighting system that uses LED technology and is in the midst of developing a new pressure pumping system to compete with legacy models.