High-pressure/high-temperature (HP/HT) environments in offshore gas fields with a significant presence of carbon dioxide (CO2) and hydrogen sulfide (H2S) in the full well stream demand the use of corrosion-resistant alloy (CRA) pipelines. This pipeline system comprises a metallurgically bonded CRA layer, produced by roll bonding and known as metallurgical cladded pipe (MCP), and a mechanically expanded and fitted CRA layer in a backing steel known as mechanical lined pipe (MLP). The complete paper outlines specific issues, mitigation steps, and lessons learned during the development phase of the CRA pipeline.
Pipeline System and Materials
To achieve the lowest life-cycle cost, CRA pipeline designed to handle a maximum partial pressure of 18 bar of CO2 and 13 mbar of H2S at a maximum temperature of 150°C was selected for an offshore gas field. The pipeline system consists of two types of CRA line pipe, MCP and MLP. The pipeline system is divided into Zone 1 and Zone 2. The areas of application of MLP and MCP are summarized in Table 1.
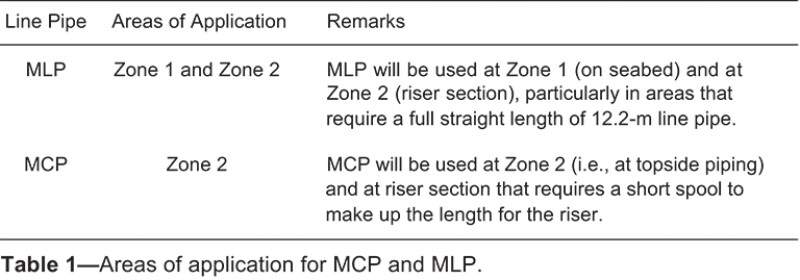
MLP Challenges
The MLP challenges experienced are subdivided in the complete paper according to the development phase of the pipeline during which they were experienced (i.e., during the manufacturing or installation stages).
Undulation Appearance on the Internal Surface of the MLP. Undulation, in this context, refers to a wavy appearance of the internal surface of the CRA pipe, which was found after the mechanical expansion process. Fig.
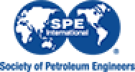