The complete paper describes a recent directional coiled-tubing drilling (DCTD) job completed for an independent operator in the Appalachian Basin. The objective was to access target zones identified as adjacent to a recently drilled vertical well using a lateral sidetrack. The project was ultimately successful in that a dry hole was re-entered and sidetracked to create a productive well.
The Economic Equation
The target of the project was to define drilling efficiency in terms of cost per production rate. This measure takes the initial production into account and ties together the ability of the driller to make hole in the direction required with the ability to select a productive part of the formation.
Recognizing that each stage of well construction can affect another, a multidisciplinary approach was adopted that included input from geology, geophysics, reservoir engineering, and drilling and completions engineering.
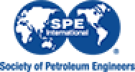