Air drilling has become popular in the Marcellus and Utica shale reservoirs because of its higher rate of penetration (ROP) and less resulting formation damage. A unique drilling system incorporating the use of downhole mud motors, electromagnetic (EM) measurement-while-drilling (MWD), and air hammers has been specifically designed and ruggedized to address downhole shock and vibration encountered in air drilling. Use of this system has resulted in significant reduction of nonproductive time (NPT).
Introduction
While seeking alternatives to increase ROP and reduce drilling costs, a few operators in the northeastern US implemented batch-drilling practices from pad locations. This provides an attractive alternative by allowing multiple wells to share the same surface location, effectively reducing footprint and environmental impact. Common well design uses streamlined well construction, where low-cost rigs can drill the tophole sections and larger, more-expensive rigs drill the curve and lateral sections. The typical well plan incorporates surface, intermediate, curve, and lateral sections that, combined, may exceed 18,000 ft. The lateral sections are the most critical and range between 2,000 and 8,000 ft, depending on formation and well geometry. The goal for close-proximity-well design is to minimize well-to-well interference and maximize reservoir exposure.
Air drilling provides a significant decrease in hydrostatic pressure over common mud types, resulting in an increased ROP. Additionally, significantly better hole cleaning can be achieved because of the high air velocities used to drill the well. Finally, mud- and cuttings-handling costs can be reduced because there are no chemicals to absorb and no cuttings-cleaning requirements on virgin formations. Early tests of this application proved it to be a viable option for the Marcellus and the Utica fields. Initially, hammer bits were used for air drilling, but significant challenges involving directional control emerged as well-plan trajectories became more advanced. The development of ruggedized mud motors and MWD tools capable of handling these challenges, and the use of specialized fluid-control systems, eventually allowed more-conventional bottomhole assemblies (BHAs) to be successful when used for air drilling.
Types of Fluid Regimes
Drilling fluid and its circulation system are used to clean the borehole, stabilize rock, control pressures, and enhance drilling rates in all phases of a drilling program. Drilling fluids allow for sufficient cooling, lubrication, cuttings removal, and adequate transference of hydraulic energy to the bit and other downhole tools. Though rheology varies, circulation systems focus on operating under specific pressure ranges in relation to formation and reservoir pore pressures. Fig. 1 above illustraters how various fluid systems are applied over the range of formation-pore-pressure gradients. Types of fluid regimes include the following, and are discussed in greater detail in the complete paper:
- Overbalanced drilling
- Managed-pressure drilling
- Underbalanced drilling
- Two-phase and foam drilling
- Misting and dry-air drilling
Why Use an Air-Drilling System?
Directional drilling in a dry-air application is widely used in the northeastern US for tophole sections of wells. The benefits previously discussed become compounded as the batch-drilling process becomes more commonplace. The reduction in drilling days, drilling-fluid costs, and cuttings-handling expenses makes batch drilling with air economically more viable.
The simplest application of conventional air drilling is used for nondirectional applications and involves nothing more than a tricone or polycrystalline-diamond-cutter (PDC) bit. Other straight-hole or nondirectional applications use downhole air hammers or straight-housing air motors. These nondirectional assemblies can be run in several different BHA configurations, ranging from a semistabilized to a fully stabilized or slick configuration. The most common method of straight-hole air drilling is to stack the BHA with additional drill collars to create a heavy vertical hanging effect that helps maintain a vertical wellbore.
A motorized air-hammer BHA configuration is not used as widely but is equally effective. This configuration consists of an air hammer positioned at the end of a bent air motor. This BHA is run with an EM MWD tool and a shock sub. An air-bypass sub is used in this configuration to divert a certain percentage of air above the motor, preventing overspinning. This added governor aids in hammer control and increases the longevity of a hammer bit. While directional control is possible in this configuration, care must be taken when selecting not only the bit-to-bend distance but also the bend angle of the motor. Too much angle does inhibit the flat-striking impact of the hammer and can cause damage to the hammer bit, shortening its life. In addition to maintaining a vertical hole, the heavy BHA mentioned previously maintains a downward impact of the air hammer, preventing the BHA from bouncing.
The most-common and -reliable air directional BHA is a bent-housing air motor with a tricone or PDC bit. This BHA is used with an EM MWD system set above the motor, with a shock sub set between it and the motor.
Air-Drilling System
An EM MWD telemetry system offers several advantages over standard mud-pulse-telemetry systems and is the preferred method of transmitting data from a downhole tool to surface during underbalanced operations. The key advantage over mud-pulse tools is that the EM MWD system can be used with compressible fluids such as aerated liquids or air. However, the use of air as a drilling fluid is particularly challenging for any MWD tool or mud motor because of the extreme levels of axial and crossaxial vibrations generated by the lack of a liquid fluid regime.
A few operators recognized the potential benefit of drilling with dry air to increase ROP in the area. But because of congested pads with a great number of wells, the need for directional measurement and control was recognized. Unfortunately, these early adaptors experienced a high number of failures when drilling with MWD and mud motors because of the harsh air-drilling environment.
To mitigate damaging vibration effects, studies were conducted to identify BHA changes and operational practices to improve reliability of the air-drilling system. A number of common operational practices were identified as exacerbating lateral shocks and vibration. Implemented procedures limited off-bottom rotation, initiated staging compressors, and stopped the practice of drilling off weight on bit. While differences were seen between BHA configurations, it became best practice to remove all string stabilizers and use a ¼-in. undergauge stabilizer on a bent-housing motor with a bend setting no greater than 1.5°. Unfortunately, the effect on service reliability was not as substantial as anticipated. As such, a new system was required to withstand these conditions and operate without failures downhole. This upgrade included a modified air-drilling motor, a ruggedized EM MWD tool, a shock sub, and, in certain instances, a fluid-bypass sub.
The EM MWD tool was ruggedized by introducing more-robust electronics and alternatively designed shock absorbers, to mitigate vibration. The MWD mounting technique was converted to hold the tool in tension while using redesigned centralizers that allowed other parts of the tool to move with the vibration instead of trying to eliminate it. The placement of the centralizers was modeled and engineered to eliminate drilling harmonics that could cause damage to the MWD tool. The antenna of the EM tool was re-engineered to withstand the high levels of vibration generated by the air injection. The overall length was increased by a factor greater than four to dampen damaging vibration successfully and prevent vibration concentration on critical, small-cross-section parts. The high-rate lithium batteries were laboratory tested extensively and then modified to operate in this environment.
The drilling motor was modified for the air environment by making modifications that successfully reduced the necessary lubrication for the bearing pack. With the changes, the motor requires only 5 gal/hr of oil to extend its operating life successfully. Additionally, a series of self-lubricating dynamic sleeves was incorporated to support side loading and reinforce the bearing pack, leading to added longevity and better performance.
A shock sub was designed and used as a vibration dampener within the BHA. The new design is able to absorb a large quantity of both axial and lateral vibrations generated by the mud motor. The tool successfully dampens high-frequency vibration that induces excessive shock to the MWD electronics and sensors.
When air hammers are employed, a bypass sub is used to minimize the amount of air pumped through the BHA. This bypass sub helps protect the hammer bits, which are sensitive to the higher air-flow rates required for successful hole cleaning.
Once the engineering phase of the project was completed, field trials were initiated. The new system has since drilled more than 400,000 ft with a success rate exceeding 98%.
Early Case Study
An operator was drilling a series of wells near Washington County in southwestern Pennsylvania. The target reservoir was the Marcellus shale. Because this is a populated area, drilling surface locations have to be as small as possible. In order to make drilling economical, as many wells as possible needed to be drilled on a single pad. The case-study pad was designed to drill up to nine complex 3D wells (see Fig. 2).
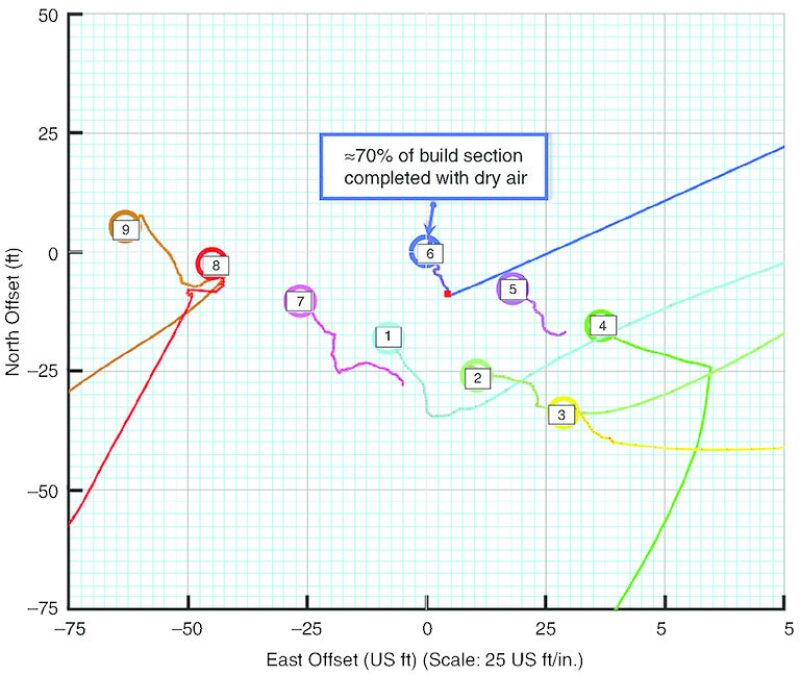
A typical well plan includes drilling from the surface to approximately 800 ft and setting 13⅜-in. casing. From surface casing, a hammer bit without directional measurements is used to drill to approximately 4,500 ft. The directional air-drilling system is used to drill from approximately 4,500 ft to approximately 7,000 ft. Finally, a rotary-steerable tool is used to drill the curve and lateral. Wells typically reach total depth at approximately 14,500 ft.
The first five wells were drilled with a low-angle nudge up to approximately 30°. The significance of Well 6 is that this well used the directional air-drilling system to drill a complex 3D well from 4,600 ft to approximately 7,200 ft with an inclination greater than 62°. Almost 70% of the curve was drilled with the directional air-drilling system. That would not have been possible in an air environment without the use of this system. Previously, the customer would use an expensive rotary-steerable system (RSS) to drill this intermediate section. Once they picked up the RSS, they had to change to a liquid-based drilling system, which increased mud cost and reduced ROP significantly.
Well 6 was drilled with air at a rate of 3,800 scf/m while injecting 22 gal/min of water. The 2,565-ft section was drilled in 34.33 hours. The profile of this well kicked off from 0° at approximately 4,600 ft (measured depth), built a 30° tangent at a 60° azimuth, and then turned to a 340° azimuth while building the curve to 62°. Through this section, the MWD tool was able to remain in its lowest power-transmission setting, maximizing tool-battery life and the potential time the tool can remain downhole. Achieving this amount of build while drilling with air reduced the time spent drilling the curve to less than 12 hours. The average drilling time to build a curve section by use of conventional methods in the Marcellus is between 21 and 26 hours.
This article, written by JPT Technology Editor Chris Carpenter, contains highlights of paper SPE 171024, “Unique System for Underbalanced Drilling by Use of Air in the Marcellus Shale,” by Chris Maranuk, SPE, Ali Rodriguez, SPE, Joe Trapasso, SPE, and Joshua Watson, SPE, Weatherford, prepared for the 2014 SPE Eastern Regional Meeting, Charleston, West Virginia, USA, 21–23 October. The paper has not been peer reviewed.