This article highlights key knowledge that was shared at the SPE’s “Collision Avoidance and Well Interceptions Applied Technology Workshop” held in Inverness, United Kingdom, in September. It raised awareness of issues concerning wellbore collisions and interceptions.
Planning to ensure that well collisions do not occur during drilling is a complex and demanding task that is often not given the high priority that it requires in drilling programs. Assumptions are made of the validity and accuracy of historical data that is unfounded. Conversely, planning well interceptions when required in operations such as relief wells/drainage intercept wells requires a sound working knowledge of wellbore-positioning technologies and techniques.
Wellbore interceptions and proximity placement are becoming critical applications for the development of some reservoirs, specifically tar sands and coalbed methane. Wellbore collision avoidance is entering the daily skills requirement of drilling engineers as they plan more infill wells and more cluster (pad) drilling. Ultimately, demonstrating the knowledge of the borehole position during the drilling process is becoming a regulatory requirement that demands greater understanding by the drilling engineering community and drilling/asset managers. Are drilling engineers trained, competent, and adhering to procedures designed to manage the intricacies of wellbore surveying requirements as applied to collision avoidance and well interceptions?
The workshop covered the topic under the headings:
- Survey-database integrity
- Collision-avoidance management
- Practical directional drilling
- Relief-well design
- Interception techniques
The workshop emphasized that wellbore collisions must be treated as high-risk events that must be managed by systematic survey-management procedures. Borehole-position errors are a critical input to subsurface modeling and have a major effect on field economics. Several workshop committee members are also members of the SPE Wellbore Positioning Technical Section (SPE WPTS) that has published two SPE papers on the ellipse of uncertainty error models commonly referred to as the Industry Steering Committee on Wellbore Survey Accuracy (ISCWSA) models.
Summary of the Workshop
Workshop attendees shared and learned about current good practices of the complete management cycle of well-positioning activities. Planning, policies, data management, practical application, and technology were all addressed. This was accomplished during presentations, discussions, and breakout sessions with industry experts. Some in-depth presentations and insightful results were produced, including
- good practice in designing a survey program
- requirements for survey-database management
- managing anticollision risk
- practical insights into relief-well planning and drilling
Planning to ensure that well collisions do not occur during drilling and conversely planning well interceptions, when required in operations such as relief wells and subsurface intercept wells, requires a sound working knowledge of wellbore-positioning technologies and techniques. Over the years there have been numerous incidents involving accidental well collisions, some of which have resulted in major incidents, loss of life, and pollution. The root causes are often traced to human error, inadequate survey practices, software problems, or a lack of integrity in databases.
Major offshore well-control events have captured international media attention. These events endanger workers, pollute the environment and, as a result, cause serious socioeconomic harm, and long-lasting reputational damage to the industry as a whole. A blowout can be initiated by numerous causes, including collision with a live well. In some cases, it is impossible for a blowout to be controlled by surface intervention and so relief wells are required. Relief-well technology is also being used routinely for complicated plug and abandonment operations in which surface access is not possible (e.g., platforms destroyed by hurricanes). Relief wells can be successfully drilled when the target well has correctly selected and managed borehole surveys and the right competences are brought to bear in planning and executing the relief well. There are instances where a lack of adequate surveys in the target well, due to poor or inadequate survey practices during normal drilling operations, lead to a low probability of quick and successful relief-well intercepts.
Database integrity is paramount to managing the known subsurface positions of wellbores. The quality, accuracy, and application of these surveys are critical to subsurface modeling, collision avoidance in clustered well locations, and relief-well interceptions. The knowledge exists to develop the correct procedures, based on good practices, in all operating companies managing such data. Borehole-ranging devices are available for use under multiple circumstances to identify casings (and a bottomhole assembly [BHA]) in an adjacent well and define its relative position for both avoidance and interception.
The content of this paper reflects the information and opinions given at the workshop.
Risk Factors Controlled by Wellbore Surveying
Wellbore Collisions—An Escalating Risk for Operators. The likelihood of wellbore collisions is rising steadily in oil and gas drilling because of the drive to maximize the number of wells from a given surface location, whether onshore or offshore. The major operators drilling from close proximity surface locations on offshore platforms have developed risk-management techniques that mitigate major events. However, onshore operators have rapidly transitioned into a similar proximity situation requiring a radical change to their operating procedures. Unintentional wellbore collisions represent a major risk that the industry needs to be aware of and understand the consequences. There are two key reasons for collisions risks not being highlighted:
- Most well engineers have not experienced what happens when the casing string of an adjacent well is hit. The common thinking is that the bit/drillstring will “bounce” off the other well. Evidence from investigations of wells that have been hit during the course of drilling repeatedly show severe damage with long sections of multiple casing strings being cut away.
- Incidents that have occurred are not published since most companies are unwilling to share their failure incidents. Furthermore, it is the consensus that these incidents are on the increase as a result of the rapid rise of cluster drilling.
The common theme of wellbore collisions is that they are most likely to occur at shallow depths, where the greatest well density exists; this situation provides the opportunity for a shallow well to encounter the pressure regime of a deep reservoir without the ability of hydrostatic pressure or formation strength to contain it. Evidence shows that collisions involving rotating drill bits create extensive damage to multiple casing strings, thereby resulting in a loss of integrity and loss of pressure control in their impacted well. Essentially, wells involved in a collision suffer substantial damage and cannot be assured of their integrity. Well collisions are high-consequence events.
These events must be avoided through management of their probability of occurrence. This probability is determined solely by the wellbore survey uncertainty in the wells and the uncertainty in the relative survey position of their surface wellheads. The drilling and surveying community makes the case that unintentional wellbore collisions represent a major risk. The probability of these events occurring can be significantly reduced through applying good practices to borehole surveys and borehole-survey data.
Management—Do They Ask The Right Questions About Borehole Surveying? Accurate wellbore surveys are critical. Initially they are required to steer a borehole away from adjacent wells and to hit the target. During the drilling process, they are also required to determine the position of the well with sufficient accuracy to enable the drilling of a relief well in the event that loss of well control occurs, and also to enable updating of the subsurface model.
There are four key steps to ensure that the risks are managed:
- Documentation: Is the process written? Is it clear? Is it correct?
- Accountability: Who is responsible? Do they know the probability and impact of collisions, the position requirement for a successful relief well, and the position requirement to minimize reservoir uncertainty and reservoir-model interpretation errors?
- Competence: Are the people analyzing the risks properly trained? Do they have the right skills and right understanding?
- Assurance: How does management know that execution follows the plan?
Performance standards should be reviewed every year, and gaps should be honestly and frankly assessed. Organizations should repeatedly challenge themselves by asking how close is the operation to being “systematic and in control”? The gap analysis then drives the following year’s plan, leading to year-on-year continuous improvement and maintenance of risk management for wellbore positions. When a risk is identified, such as potential collision with another well, processes and requirements can be put in place to reduce and mitigate this risk. It is important to ensure that planning is systematic to avoid the impact of assessed risks and ensure operations remain in control of the well-drilling process.
The issue of potential collisions tends to be downplayed by our industry. Few people are aware of the consequences and catastrophic results that can occur from collisions and, as a result, kept awake by this at night. Discussions generally center on estimating probabilities of collisions and bouncing off casing, but this often does not highlight the consequences of a collision. Addressing the problem in terms of eliminating major accidents adds seriousness to the discussion that supports the classification of wellbore collisions as a major process-safety risk.
Consequences of inadequate borehole surveys are enormous. Often the immediate cost effect is used to rationalize the type of survey tool and the frequency of surveying. Unfortunately, the seriousness of high-consequence events such as collisions and a loss of well control are not fully considered. In reality, Table 1 shows the extent of these consequences.
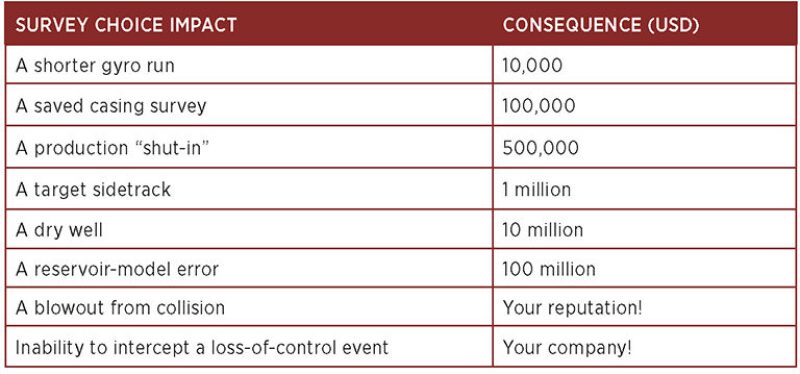
Wellbore-Collision Consequences—Larger Than Expected. Most wellbore collisions are not reported in the public domain. A review of damage resulting from wellbore collisions showed the following:
- Visible damage to impacted wells from a bit and BHA collisions based on visual inspection of recovered casing shows centimeters-wide cuts that run for meters in length.
- Damage occurs to multiple casing strings and tubing.
- Bit damage from impacts is minimal. Face damage is usually zero and side damage is minor.
These observations showed that:
- Wellbore collisions are events with major consequences.
- Minor bit damage is not indicative of the major damage that probably occurred to the intercepted well casing strings.
- Wells affected by a collision with a drilling assembly are highly likely to have lost their pressure integrity. In some cases, this damage has manifested itself only when production was resumed in the damaged well.
In addition, well collisions have occurred unexpectedly because of erroneous borehole positions in well-trajectory maps as a result of poor surveys from poor management practices. Subsequent resurveys with correct tools and practices showed significant shifts in mapped well paths explaining why the unanticipated collision had occurred. The conclusion is that the probability of a collision must be managed from both the planning and drilling phases of a well. The probability of a collision is a direct function of the survey-management program in both wells that are subject to collision. For close proximity drilling, such as cluster drilling, this means that the wellbore uncertainty in both wells must be reduced as much as possible. This demands the use of good survey practices and survey tools in all wells.
Management must be assured that the correct competencies and systems are applied to mitigate these risks.
Well-Survey Program and Slot Allocation
Developing a Survey Program. A survey program should have prominence in a drilling program so that it is not overlooked. Survey programs are key to quantifying and minimizing the risk of intersecting another wellbore or geological formation, avoiding hazards, or targeting a specific well for relief-well drilling. Surveys also define the 3D position of logs and data used by the subsurface group to define their models. Correct application of techniques to improve errors can create much better results. Running in-field referencing and sag corrections and/or using dual inclination tools, for instance, can produce more than a 70% improvement to lateral and/or vertical uncertainty compared with the basic processing applied to the measurement-while-drilling (MWD) model. These techniques can be implemented during the job, or post processed if needed. Due to the safety-critical nature of surveying operations, deviations from an agreed and approved survey program must be managed through a formal management of change procedure.
The survey program must be executed as planned for the collision-management process to be valid.
Survey Tool and Procedure Differentiation. Drilling engineers often do not differentiate between gyro tool types. The accuracy of various gyros varies with the design of gyro and it is important to make a distinction between these instruments when designing survey programs. It is important to select the right type of gyro tool and know why you are running it. The same applies for magnetic survey instruments; different instruments give different accuracies. In addition, the procedures used by the survey company determine the quality of the survey delivered from each instrument. The effect of survey-program design on borehole-position uncertainty is one of the primary reasons operators who drill and produce wells must have a formal survey-management plan.
Well pads in drilling for unconventional reserves, especially shale, are getting denser and more complex in terms of well trajectories. Companies that are not taking appropriate precautions may be taking on significant unrecognized risks.
Slot Allocation on Cluster Drilling. For cluster drilling on mutipad wells, both onshore and offshore, the sequence for slot allocation is critical to success in managing collision avoidance and costs to drill wells. It has been reported that well allocations often follow a random process that creates situations in which a complex steering of boreholes through high-density well clusters requires additional effort and cost and increases the probability of a well-collision incident. A workshop participant shared how a major operator addresses this issue in a cost- and risk-reduction manner through a process to define slot allocation.
The key message is to manage slot allocation from the outset to minimize collision risk resulting from unnecessarily complex drilling because of poor slot allocation relative to subsurface targets; a pure logic that requires some agreed planning across disciplines.
Survey-Database Management. Managing wellbore survey databases is critical. Good practices for managing directional data have evolved over the past 30 years. Current thinking about these practices may be summarized under four headings:
- Legal requirements of an operator
- Dealing with older data
- Threats to the integrity of existing data
- Coping with change
The operational requirements for directional surveying and well-trajectory planning generate and access a large volume of data. These can be surface locations, geological targets through to actual survey measurements. These data are critical to the safety procedures required for the prevention of well collisions, locating the wells for potential relief wells, and defining precisely where formation measurements were taken in 3D space.
These data have to be made available quickly for multiple users, multiple applications, and external clients and yet secured to prevent damage to the safety-critical wellbore-position information. Raw data should also be archived for future analysis. Operators may want to consider requiring the service companies to deliver raw data with a defined storage format for future review.
There is a need to manage data before, during, and after its acquisition; this should be undertaken in accordance with a documented plan. In this way, the data-management activities can be audited and the plan needs to be updated periodically. The types of problems that occur with survey data include QA/QC problems, lost data, and misinterpretations. Most mistakes lie in data management. The lack of a survey-data-management plan puts the quality and accuracy of gathered data at risk. Upfront investment in survey-data management is worthwhile since it becomes more difficult and expensive to rectify a database later.
Database transfers are complex undertakings. Often the link to subsurface is considered insufficient. The errors in the survey database become errors in the subsurface models, which directly affects an operator’s reserve calculations. Experience has shown that wellbore resurveying across a field resulted in revisions to the subsurface model; at times this can result in the removal of interpreted faults through leveling of correlations. The location of fault intersections can also move creating an enlarged effect on extrapolated faults. Similar effects occur when adjustments are made to correct data and surface locations.
A plan to manage the data over the lifetime of the data is essential.
Recommendations have been made through the International Oil and Gas Producers Association for guidance on standards for surveying and wellbore positioning. It has asked, from a regulatory aspect, what standards should cover the wellbore-positioning aspect of business. A technical note that relates to the outputs of the technical body (SPE WPTS) will be created in standardizing some of the practices and requirements to help guide organizations.
Collision Avoidance
Wellbore Collision Avoidance. Knowledge of the factors that affect a wellbore’s positional accuracy and how estimates of position uncertainty are used to avoid well collisions is critical to all operators and contractors undertaking cluster drilling, both offshore and onshore. The design of the well-survey program is key to achieving a well’s placement objectives for collision avoidance. Since there are different methods for calculating collision risk, it is important to understand how these different methods can be incorporated into an operation’s survey-management system. The use of magnetic ranging is a commercial service that enables the proximity of close wells to be determined from downhole measurements and, consequently, update the error model leading to a reduction of the uncertainty between them.
Position Uncertainty and Error Models. It is critical for anticollision and target sizing that the uncertainty resulting from surveys in all wells within collision reach is fully analyzed and understood. This requires the use of an appropriate error model. The results of the error model are dependent on all the major causes of error in the final survey, how they vary with location and well orientation, and also how these different error sources combine.
The ISCWSA MWD (Williamson 1999) error model includes error terms for bias and scale-factor model applied to the accelerometers and magnetometer sensors in the tool; terms for how the tool is misaligned in the borehole for the effect of drillstring interference; and since MWD tools measure relative to magnetic north, the errors in the declination values used to convert to true or grid. There are also depth-stretch and scaling errors, and sag errors. In total, there are 27 error terms defined in an MWD survey-error model.
The practice is to quantify the size of each of these error sources at one standard deviation and then use mathematical weighting functions to detail how the different error sources affect depth, inclination, and azimuth survey measurements. The different error sources are combined all along the well path and the minimum curvature method is used to quantify the resulting ellipse dimensions.
The ISCWSA Gyro Model (Torkildsen 2008) uses the same principles and framework, but has different error sources and weighting functions. Survey corrections, where relevant, can be applied resulting in the reduction in magnitude of one or two particular error terms.
The use of any error model is based upon the assumption that good survey practices have been followed: full survey QC and proper calibration and use of tool. An error model cannot repair bad data, and assumes that the results conformed to the tool-design specification. Failure to apply the correct survey practices strictly renders the results unsuitable for collision-avoidance management. Error models are invalid if the correct running procedures have not been followed.
The ISCSWA does not specify, certify, or verify tool models. The error model is a mathematical analysis to determine ellipsoids of uncertainty; the tool models must come from the tool vendor. It is critical to know which models should be used and when.
Anticollision Rules. Separation factor rule is probably the one most commonly used. However different rules can be applied at surface and on extended-reach drilling (ERD) wells, as the center-to-center distance can be vital at the top of hole, whereas on long, shallow ERD wells, where the ellipse can be up to 400 ft across, the safety-factor rule is used. In other situations a third method may be more applicable using positioning based on layering.
Operator’s System of Managing Wellbore Positioning Relating to Collision Avoidance. Good practices employed by a major operator were presented at the workshop. The good practice has six key elements, of which “collision avoidance” is one; other elements, notably, “directional-survey uncertainty” and “ensuring the quality of the surveys as the well is drilled” are inextricably linked to the collision-avoidance element. Any deviation from the policies mandated in the operator’s standard requires a dispensation cleared by the operator’s head of drilling. The requirement for a dispensation is therefore unusual.
A distinction between collisions with wells that could result in a health, safety, and environmental (HSE) risk and those that could not is often made. An HSE risk is typically defined as one that jeopardizes the safety of personnel or the environment.
Contractors usually make the original trajectory plan that is reviewed by the operator’s drilling engineer. Good practice demands that plans must pass both operator’s and contractor’s collision-avoidance rules. This results in two independent checks to ensure that the analysis to manage collision avoidance is assured. Traveling cylinder (Fig. 1) plots are constructed with no-go collision-avoidance lines. If the well plan and survey program fails under either the contractor’s or operator’s collision-avoidance rules, irrespective, the plan is re-evaluated, since this indicates that an unacceptable risk could be present.
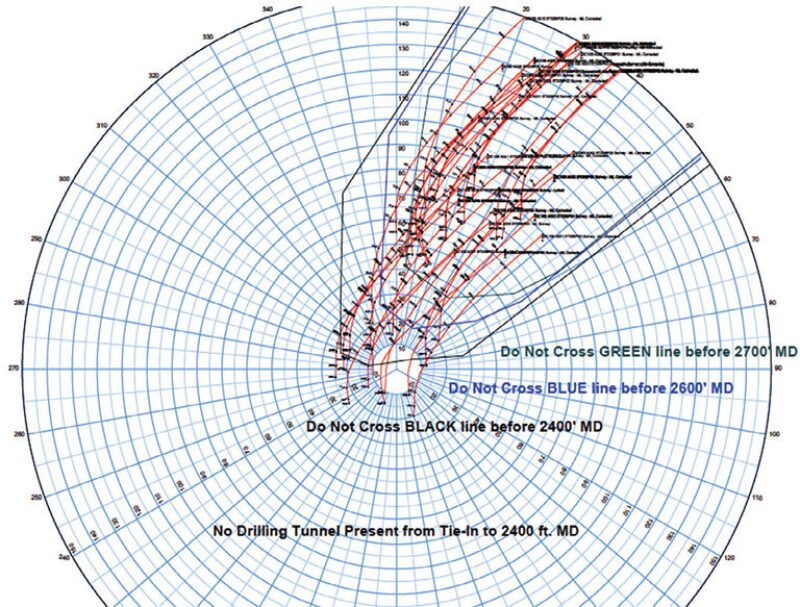
QC and control of surveys use recommended practice and are aided by comparison of high-accuracy gyro (rate, north seeking, and similar types) and MWD survey-position uncertainty. The purpose of this check is to see if the gyro ellipse is contained within the MWD ellipse (Fig. 2). If it does, the surveys can be considered good; if the gyro ellipse is outside the envelope defined by the MWD, then a resurvey is required.
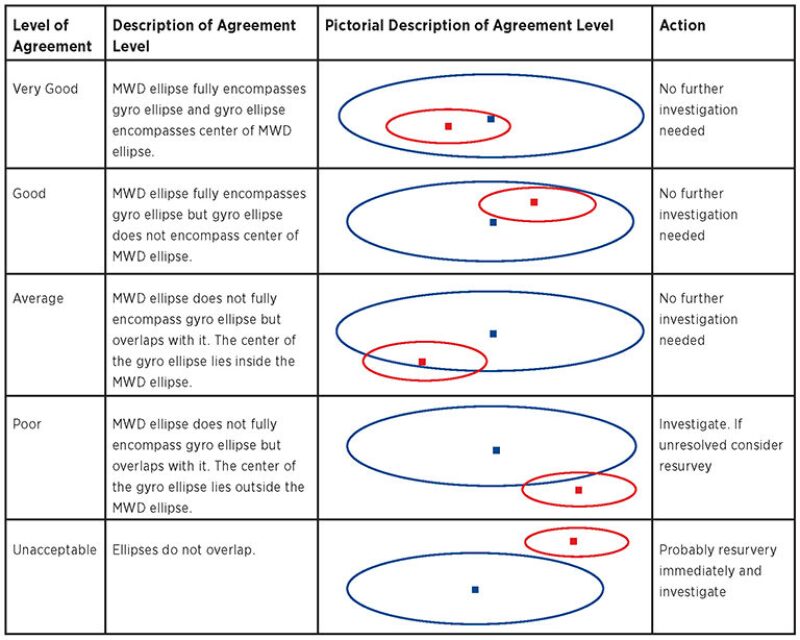
Well-Interception Techniques. This interception process applies in a similar manner to wellbore collision avoidance because the survey management and ranging-tool processes are similar. Obviously, the actions taken are diametrically opposite for avoidance and interception. Standard survey-error models are applied to the intercept (relief) and target well paths to generate ellipsoids of uncertainty. Once drilling has progressed to the point where the ellipsoids overlap, magnetic-ranging techniques are applied to determine the distance and direction between the wells. Radial and directional uncertainties define the target sector for the approaching well; the aim is to gradually reduce this uncertainty. After a ranging run (Fig. 3), the challenges include:
- Surveying or projecting an accurate inclination, azimuth, and depth at the bottom of the borehole—this is critical when a motor has been used to make a course correction before the ranging run
- Applying surface shift on target well—need for a new plan after each ranging run
- Using the ranging uncertainty window to be compliant with standard error models in software
- Propagating error models from this ranging window
- Making a new plan to target and then defining directional control to stay on plan
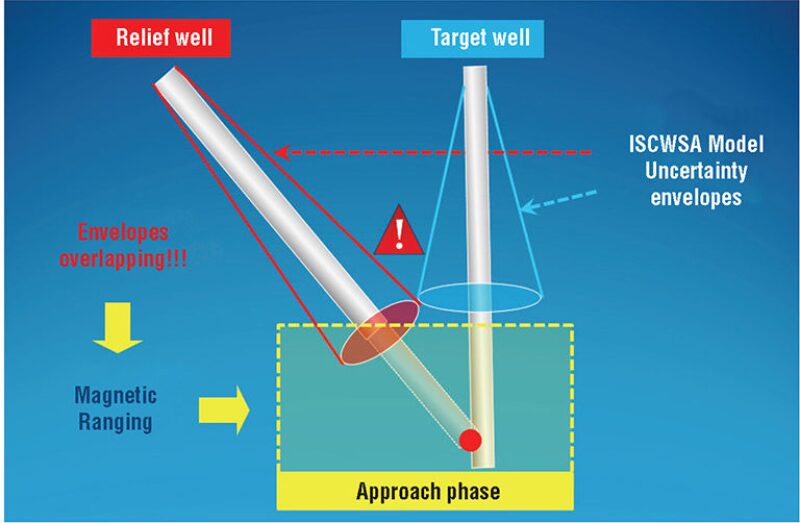
Wellbore-Ranging Techniques
There are commercially available techniques for intercepting wellbores. These techniques include passive ranging systems, as well as active ranging systems, which can involve current injection or deployment of rotating magnets. Interception applications include well intersections such as relief wells, coalbed methane drilling, wellbore re-entries for remediation, enhanced production, or plug and abandon operations, as well as applications where it is desired to maintain separation over a distance, such as steam assisted gravity drainage well twinning often employed in heavy-oil extraction.
There are many factors dictating which technique is most appropriate. Some techniques require access to the target well. Other active techniques, such as downhole current injection, do not require access to the target well but require formations conducive to the technique.
Recommendations. Treat potential wellbore collisions as high-risk events with serious consequences. Manage this risk through competent borehole-survey management to minimize the ellipsoid of uncertainty in both wells by effectively reducing the probability of a collision. Recognize that the potential for wellbore collisions has increased significantly with the rapid transition from predominantly vertical drilling to predominantly high-angle cluster drilling with the rise of shale prospects.
Treat borehole-survey errors as a critical input to subsurface modeling activities. Ensure that surveys programmed for the final well-trajectory definition meet the uncertainty requirements for subsurface modeling. Make certain that the subsurface team uses the correct data that have been quality controlled through the managed database system.
Make sure the organization has access to and uses current industry standards on wellbore surveying including Introduction to Wellbore Positioning.
Develop and maintain an up-to-date borehole-survey manual that guides engineers on the correct choices when designing wellbore-survey programs as part of a drilling program. Ensure that the programs are followed precisely during drilling operations and that deviations are only sanctioned after a formal management of change procedure and signed off with the correct management authority.
Develop a competency program for people involved in survey-database management and create/follow a database-management program to assure that all survey data are accurate, quality controlled, and correctly managed.
Acknowledgments
The authors (committee members, workshop cochairs, and scribe) acknowledge the hard work undertaken to organize and manage sessions in the workshop by the fellow committee members: Angus Jamieson, Ben Hawkinson, Benny Poedjono, Harry Wilson, Pete Clark, Philip Gurden, Robert Wylie, Simon McCulloch, Steve Grindrod, and William Allen. We also thank SPE workshop organizers Hayley Packman and Tamarin Jones and the SPE Technical Activities Manager Shasta Stephenson, who supports our Wellbore Position Technical Section at SPE.