This paper describes both design and economic considerations that lead to the selection of vacuum-insulated tubing (VIT) or vacuum-insulated casing (VIC) for the completion of thermal wells. The results shared in this paper are some of the parameters considered during thermal-well design: temperature on the casing and the tubing, and heat loss. Knowing these parameters, well integrity can be studied and the overall efficiency of the process estimated.
Introduction
The most common thermal enhanced-recovery methods are cyclic steam stimulation, steamflooding, and steam-assisted gravity drainage, which is widely used in Canada. The role of these thermal-recovery methods is to convey heat into the reservoir, mainly by convection.
×
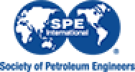
Continue Reading with SPE Membership
SPE Members: Please sign in at the top of the page for access to this member-exclusive content. If you are not a member and you find JPT content valuable, we encourage you to become a part of the SPE member community to gain full access.