Engineers that have focused on drilling and fracturing rock are now looking at ways to grow it to stop leaks.
There’s no shortage of options, and none of them threaten the future of the cement squeezes.
Two recent papers, though, offer a glimpse at the growing array of new options inspired by difficult problems ranging from plugging elusive methane leaks to long-term carbon storage.
One paper discusses healing micron-scale cracks that allow gas leaks through the annulus by injecting a mix of bacteria and chemicals into those spaces, where they create a calcium carbonate seal.
The other approach is aimed at filling large openings with methods ranging from building long, underground barrier walls to plugging faults. The idea is to pump down two streams of chemicals that meet at the leak site and build an impermeable barite barrier.
After the presentation at the SPE Reservoir Simulation Conference in March on building barite barriers, an engineer in the audience began his question by praising the paper’s author, Rami Younis, an associate professor at the University of Tulsa, for trying out some “crazy ideas.”
That would be “crazy” as in taking on the daunting challenges of delivering streams of chemicals to build an underground barrier, and how to convince engineers who fight scale for a living to keep wells flowing to introduce scale into the reservoir.
Younis’ short answer was barite can create a lasting barrier using readily available ingredients that can be delivered into remote spots. A table in the paper highlighted how other available options fail on one or both of those counts. Some are not strong and long-lasting, such as gels and nanofoams. Others are tricky to deliver, such as pumping cement or calcite.
Also, over time, cement can get brittle and break up while calcite can be attacked by strong acid, the paper said.
The leading argument for the second alternative, invented by a company called BioSqueeze, is access. The bacteria- and chemical-rich water can go in places as small as a micron, while most of the alternatives require openings more than 100 times larger. The company said the result is seven times stronger than the original.
“We use natural soil bacteria, which are not pathogens” which form rock that is similar to limestone, said Randy Hiebert, co-founder and vice president for research and development for BioSqueeze.
On the downside, the bacteria that act as a catalyst cannot survive temperatures above 170°F.
Both innovations have been greeted with skepticism.
While the technology was developed with funding from the US Department of Energy and the company has been doing commercial work for 4 years, Hiebert still must convince petroleum engineers that bacteria can quickly crystalize the company’s proprietary mix of chemicals to plug leaks.
But some nagging problems force customers to try something new. Hiebert recalled a successful job for an unnamed large oil company which had spent millions on failed solutions. The company finally called BioSqueeze, which was 17th on the list of potential providers of solutions.
Younis has been trying to gather enough evidence from lab work and computer simulations to convince federal officials that he is worthy of a research grant from the funding allocated for carbon capture and storage research.
Those are just two examples of research and startups internationally working on such novel plugging ideas. The sector has gotten a jolt of support from government programs to limit methane emissions, a major cause of global warming, and carbon capture and storage, which requires creating underground storage that essentially lasts forever.
Some are looking for additives to put into oilfield cement that react to brine coming in through a break. The fluid causes crystallization that fills the gap. Those looking for ways to do this range from Shell to a group of archeologists at the Massachusetts Institute of Technology (MIT).
MIT researchers used the latest chemical analysis devices to dissect the chemical makeup of cement gathered at a Roman archeological site, trying to figure out how concrete structures and roads built 2,000 years ago are still standing, according to a study published in AAAS Science Advances.
When they did a microscopic analysis of the material, they were puzzled by tiny white chunks, called lime clasts. They didn’t serve any obvious purpose, and the researchers couldn’t accept that careful Roman cement makers would have made cement with those impurities. Their chemical analysis supported a theory that those bits of reactive calcium came in contact with water leaking in and formed calcium carbonate which allowed the cement to heal itself.
To test their theory, they made a batch of cement using a recipe that ensured lime clasts would be in the final product. When tested, the result mirrored the calcite-filled cracks found in Roman concrete.
One sign of the growing interest in ultralong-lived cement was in a note at the end of the scientific paper describing the MIT patents covering potential uses for this discovery.
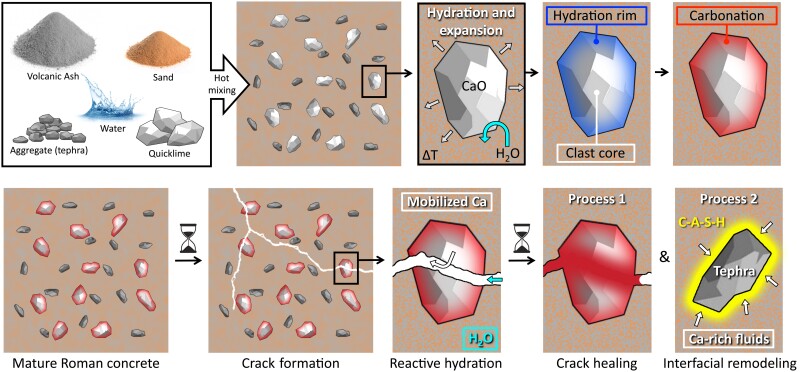
Eight-Gallon Treatment
The BioSqeeze paper described a job in Ohio, where it was called in to stop a persistent gas leak. State regulators were not going to certify the well had been properly decommissioned until they plugged the gas flowing up through small cracks in the annulus.
The well owner hired the company because it offered a treatment that could be injected into the cement barrier at the surface. Other methods would require drilling out the plugs.
Compared to the scale of most oilfield jobs, the volumes injected for the “biomineralization” sound tiny.
On day one at the Ohio wellsite, they injected 8 gallons of the company’s proprietary fluid mix over 13 minutes; the injection rate per minute slowed significantly.
Later that day, it took 16 minutes to inject that much fluid and later, 22 minutes to inject 7 gallons, suggesting the growing rock was filling the openings.
Over the next 36 hours, the injection times rose as the injected fluid volumes dropped. On day 2, they were able to inject only 4.6 gallons after nearly 2 hours of pumping.
They stopped because the injection rate had fallen from a peak of 0.56 gal/min to 0.01 gal/min. Also, the pressure falloff after pumping had shrunk, from 78% early on to 14% at the end.
Most importantly, after the Ohio well was treated, the annulus pressure dropped to zero, and regulators accepted that it had been properly plugged and abandoned, according to the paper.
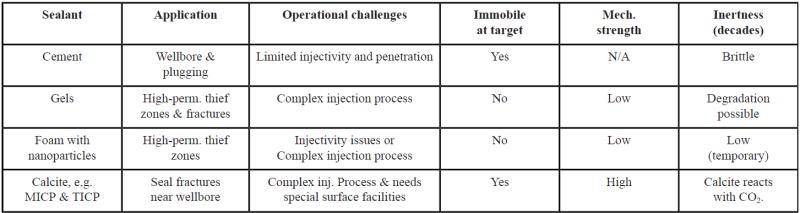
Hitting a Target
The challenge is proving that multiple injection wells can deliver the chemical streams needed to deliver the ingredients to ensure “a hydrodynamic seal forms in the leaky spot,” Younis said during his presentation.
So far, the work has been mostly lab testing and computer simulations. The simulations used groups of injection wells in patterns that echo the patterns used for water injection.
Like water injection, the fluids used are inexpensive and plentiful. But long experience with water injection for greater oil production shows it is difficult to predictably deliver streams of fluids to a subsurface target.
The effort began with lab tests. The two streams of ingredients were injected through separate tubes into a sandstone core by Jun Lu, an associate professor of petroleum engineering at The University of Tulsa.
Separate injection points were required to “avoid the rapid scale deposition that would otherwise occur within tubing,” the paper said.
After they injected 200 pore volumes of the brine components—barium and sulfate ions—Younis said, “X-ray scans of the cores showed a thin wall of barite scale had developed between the two halves.”
The paper also reported the results of two simulations in a “coupled hydrological-mechanical-chemical” transport model.
In one they created a long, thin barite curtain, which could be used to plug a leak in a gas storage site. In the second they injected a large volume targeting a smaller area that represented a fault.
In both instances the test ended with rising pressure inside the simulated space, indicating they had succeeded, like a tire holding air after patching a hole.
Based on those results, Younis is hoping to win the grant money needed to move this idea toward field testing.
FOR FURTHER READING
SPE 213099 Biomineralization: Surface Injection Eliminates Bradenhead Pressure by Randy Hiebert and John Griffin, BioSqueeze.
SPE 212221 A Numerical Study of Selective Inorganic Precipitation in Fractures To Geoengineer Resilient and Secure Underground Storage Sites by Shijun Fan, Rami M. Younis, and Jun Lu, University of Tulsa.
Hot Mixing: Mechanistic Insights Into the Durability of Ancient Roman Concrete by L.M. Seymour and J. Maragh, MIT; and P. Sabatini, DMAT SRL, et al. American Association for the Advancement of Science, Science Advances, January 2023.