For decades, E&P companies have chosen rod lift over other artificial lift types due to its ability to produce liquids efficiently from wells with low bottomhole pressures. The application of rod lift to horizontal wells has brought significant challenges including increasing depths, complex well geometry, volatile fluid compositions, high gas rates, complex chemical treatment requirements, and high rod compression and buckling tendencies.
Consequently, rod lifting has a significantly higher failure frequency (FF) in horizontal wells than in vertical ones. Root Cause Failure Analysis (RCFA) and optimization protocols in vertical fields yield FFs between 0.1 and 0.2 (meaning wells run, on average, 5 to 10 years before failure). However, after years of effort, typical horizontal fields still have FF’s between 0.5 and 2.0 (meaning wells run, on average, between 6 months to 2 years before failure). The end result is that failure repair and remediation costs comprise a significant amount of lease operating expense (LOE).
This white paper will examine the impact of automating setpoint changes in a production optimization process—in particular the application of Automated Set Point Management (ASPM) within the Ambyint InfinityRL™ product—on deep HITs and premature rod parts from fatigue.
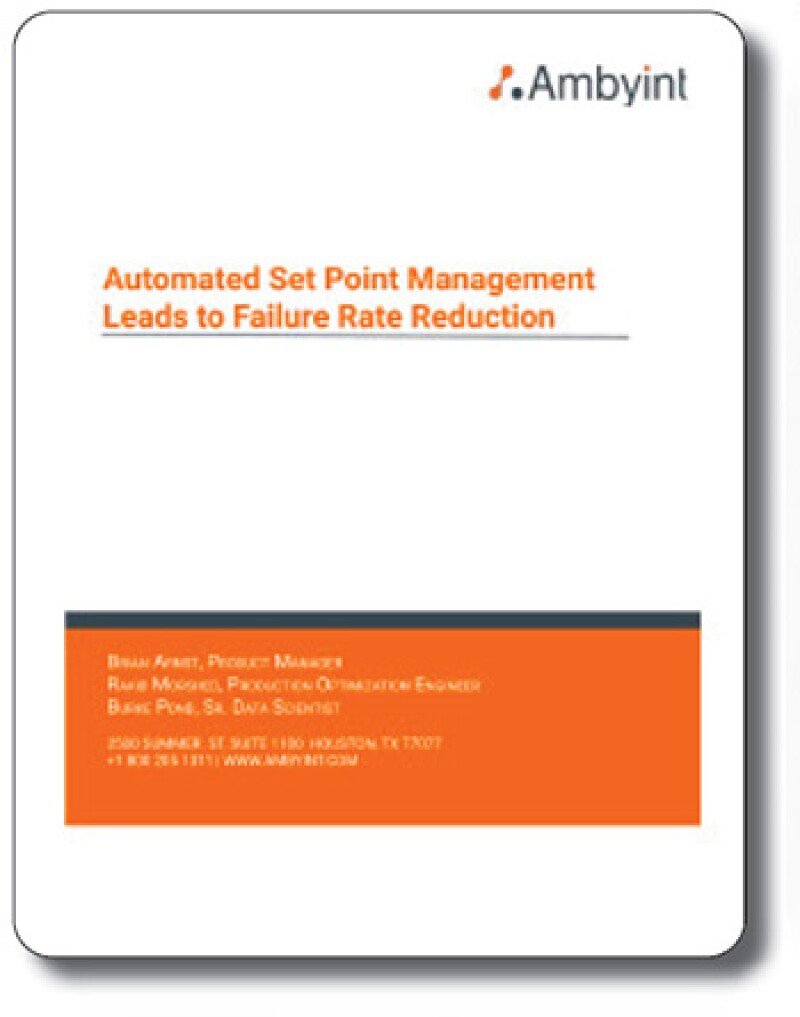
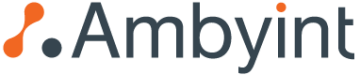