As blowouts become a less frequent event in the US, specialty-outfit Wild Well Control is eyeing the market potential of the less severe, but more common, issue of sustained casing pressure in shut-in wells.
“We used to say that the rule of thumb in the US was one blowout per 1,000 wells drilled,” said Bill Mahler, executive vice president at Wild Well. “Today, it’s more like one blowout for 1,600 wells drilled.”
That dropoff is thanks to the development of shale fields, he added, explaining that similar horizontal well profiles and downhole-pressure conditions have led to a more predictable drilling environment.
However, while drilling has become safer, Wild Well believes the occurrence of formation gas leaking up the cemented annular spaces of shut-in horizontal wells remains prevalent and largely unaddressed. The company cited a recent analysis of a US shale play where 86% of surveyed wells were found to have sustained casing pressure.
Wild Well is raising the issue because its onshore well control and subsea intervention services are trying to boost sales of an epoxy resin that it says offers a stronger seal for abandonment operations.
After being sent downhole in its liquid state, a day or two later the resin will form into a solid seal around leaky packers, cracked cement jobs, or it can block off the area of gas intrusion from inside the formation rock. The resin was first introduced by CSI Technologies in 2005, a Houston-based cement service company owned by Wild Well’s parent company, Superior Energy Services.
Speaking during a media event at Wild Well’s headquarters in Houston, Mahler characterized sustained casing pressure as a “major problem” and is telling operators that in cases of abandonment, resin offers a reliable, permanent barrier whereas cement is more likely to fail and require remedial work.
“If you do your primary plug and abandonment with resin, you can eliminate all the sustained casing pressure going forward because you can push it back into the formation, especially after they’ve been fracked,” he said.
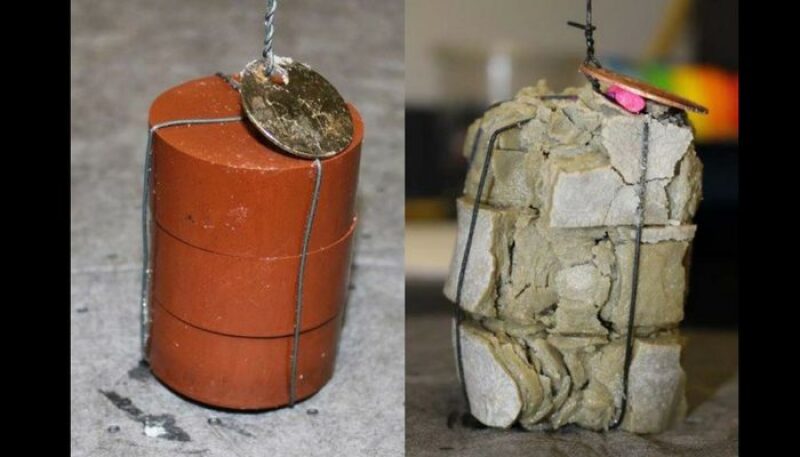
Acceptance First, Lower Cost Next
Wild Well says that laboratory tests have shown that the CSI brand of resin has five times the tensile strength and more than double the compressive strength of cement. It is further distinguished from cement because the resin is adhesive to rock and metal, solids free, chemically inert, and does not mix with water. And its rheology characteristics and controllable reaction time allow for small volumes to be placed where a seal is most needed.
These selling points may be several rungs above the key performance indicators of cement, but with a price tag of USD 4,000-6,000 per bbl, the resin is also far more expensive. Typical well cement may run USD 150 per bbl. That difference has long been the chief obstacle to uptake for the chemistry product.
Mahler said the company is hoping new validation studies will help gain wider industry acceptance. If demand for the resin were to increase to volumes comparable to cement production, then “the cost will come down tremendously, but right now it’s cost prohibitive” for the onshore market, he said.
Offshore applications have been an easier sell recently, in part because extremely low rig rates of around USD 130,000 per day have made it a more palatable option for plug and abandonment services, said Mahler.
Though the offshore track record remains limited, it has led to one important milestone: a qualification of the resin by Shell through its laboratories in the Netherlands. With that seal of approval, the hope is the international major will soon become a regular user.
And last year, the resin was used in the first lower-well abandonment that did not require a cement cap in the Gulf of Mexico. Oceaneering partnered with CSI for the work, which was granted a special waiver from US regulators to use the resin on a high-risk well that had 1,300 psi in sustained casing pressure.
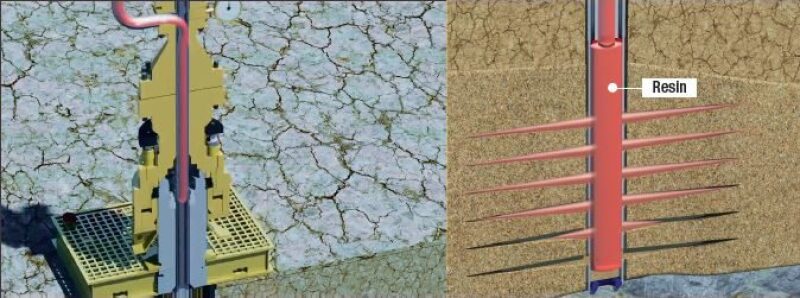
Onshore Market Dormant, For Now
US regulators have also helped the cause of the resin suppliers and offshore service providers by requiring subsea wells with sustained casing pressure be dealt with as soon as the problem is discovered.
“Those same regulations are not in place on land,” pointed out Tyler James, a technical sales lead at Wild Well. “They are probably coming, but right now [onshore operators] are still allowed to shut in and say that they are going to fix them later.”
If the onshore regulatory driver does come, it may be based on findings such as those from the recent survey of horizontal gas wells in the Fayetteville Shale of Arkansas. CSI led the study, which was sponsored by the Research Partnership to Secure Energy for America (RPSEA). Data shared by shale gas producer Southwestern Energy showed that of 100 wells it drilled in the second half of 2013, 86% experienced sustained casing pressure.
“That’s a very big number,” emphasized James, who explained that there are two main reasons so many wells suffer from the issue. The first is that cement can crack along any point in the annulus as it dries or due to subsurface vibrations, creating potential pathways for methane migration.
The other factor is that cement does not form a true bond with the steel walls of the casing, leaving tiny gaps called micro-annuluses that, while too tight for solids and liquids to move through, are wide enough for the ultra-small methane molecules to traverse.
When oil and gas operators seek to stop gas from migrating up through a cemented well, the standard industry fix has always been to push more cement downhole. These squeeze jobs were described by James as a “band-aid” because they often fail to solve the root cause.
When cement is pushed into the tight openings of a leaky pathway, the result is often a porous filter cake rather than a gas-tight seal. As cement is placed under pressure, the water phase of the cement can be pressed out into an opening, leaving behind an accumulation of dehydrated solid material.
“So what is water going to do to actually fix your micro-annulus? What is the water from the filtrate going to do to consolidate your formation? Absolutely nothing,” said James before re-emphasizing that in the same scenario resin will stay bonded to the casing and to the formation rock.