The Longmaxi shale gas play in China is unique because of multiple tectonic deformations in its geological history. While its hydraulic fracturing design has matured after a decade-long evolution, the success of every well cannot be ensured without considering heterogeneity. To address these challenges, a multidisciplinary team was formed to work on a pad; through the team’s efforts, designed proppant volume achieved zero casing deformations, fewer screenouts, and weaker fracture hits. The key to effective mitigation was continuous 3D geological and geomechanical (G&G) modeling through ongoing iterations with field data.
Background
The Longmaxi shale play in the Sichuan Basin is approximately 20 000 km2 and is buried between 2000 and 4500 m.
×
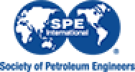
Continue Reading with SPE Membership
SPE Members: Please sign in at the top of the page for access to this member-exclusive content. If you are not a member and you find JPT content valuable, we encourage you to become a part of the SPE member community to gain full access.