The argument for making friction reducer on site is simple: only one truck is required to deliver dry polymer vs. three loads required for the same amount of liquid additive.
For Downhole Chemical Solutions (DCS), reducing the number of trips and the amount of chemicals needed to create a stable liquid by mixing it as needed on site reduces the average cost of a gallon of friction reducer by around 30%, said Mark Van Domelen, vice president of technology for DCS.
“The business is very cutthroat and competitive on the pricing of polyacrylamide. We can reduce the cost further on friction reducer,” using dry polymer, he said.
Polyacrylamide is generally described as the key component in friction reducers. Suppliers also add some ingredients to create a stable liquid and others that are supposed to improve performance. When DCS delivers dry polymer to a well pad to mix it on-site, the only other ingredient is water provided by the customer.
It has been a winning strategy change for the private company; it has grown rapidly, even during last year’s slump. DCS increased the number of mixing units from one to 16, and dry polymer sales have grown from 10% to 90%, Van Domelen said.
One of the company’s customers is John Blevins, the chief operating officer for Houston-based Hibernia Resources III and an early adopter who was a lead author of a paper on making friction reducer on site while fracturing (SPE 204176).
Blevin, who uses the words “friction reducer” and “polymer” interchangeably, is the rare C-level executive who likes to manage operations from a frac van at a company that normally completes one pad at a time.
The polymer is polyacrylamide. When Blevin works with DCS on a well, he purchases it directly from one of the few chemical companies that will produce the polymer based on his specifications. The price on the DCS invoice will be a price per pound that covers the cost of the polymer and the service.
At Hibernia, a small private-equity and employee-owned company, there is a powerful incentive to pay close attention to the details.
“When we spend a nickel, that nickel is divided among us at some point in time. If we are efficiently frugal, we are going to be better off in the long run,” Blevins said.
The paper, which was presented at the Unconventional Resources Technology Conference (URTeC), included a chart showing stage-by-stage costs, with the average cost for dry stages ranging from 27% to 31% lower than similar stages that were fractured using liquids.
The simplicity of the mix is a plus for Blevins whose company is especially focused on how chemicals are likely to react downhole.
“We did a 6-month study before we pumped anything in the ground to make sure we had the right combination” of fracturing additives, he said. “We do study nearly every well and every landing zone to ensure the chemicals used are compatible.”
Mixing Results
Dry powder represents a small part of the friction-reducer market, but it is growing.
Those selling dry-powder mixing must respond to concerns based on some early failures. Pioneers in the business demonstrated that simply mixing friction reducer and water can literally gum up the works, forcing a fracturing job to shut down.
“You cannot just drop it into the water like guar,” Van Domelen said. Putting polyacrylamide and water together is likely to result in “polymer clumps that can clog up pumps as well as the blender.”
The URTeC paper describes the DCS-designed powder-delivery and mixing units, which are built into truck trailers. The description of what DCS does illustrates that it is hard to reliably deliver a smooth mix.
Van Domelen said it requires a high-energy mixing process. DCS’s method relies on a nozzle that uses the Bernoulli effect to create a vacuum that sucks in the powder and combines it with the specified amount of water to create a concentrated liquid. The concentrate flows into the fracture blender as needed during pressure pumping.
The trailer holding the dry polymer includes a moisture-control unit to ensure it does not clump. The water intake offers real-time chemical analysis because the makeup of the water can change in ways that may hurt performance.
To date, DCS has mixed 35 million pounds of polymer, each pound making about 2.5 gallons of concentrated friction reducer. They have completed jobs in the Permian, in Haynesville, Oklahoma, and at Eagle Ford with little downtime, Van Domelen said.
While the company does not report downtime for its jobs, Blevins said that in the 110 days of fracturing performed by Hibernia, only 2 hours were lost to downtime due to the system.
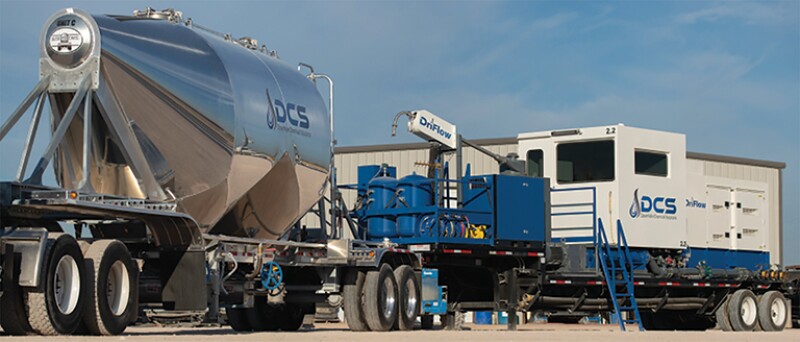
On the Fly
Producing fluid while fracturing has allowed Hibernia’s frac crews to adjust the properties of the friction reducer while pumping, even when the readouts in the fracture are not going to plan.
On one pad, Blevins said the performance was so poor that Hibernia stopped the job to bring in a different sort of polyacrylamide powder to finish the job.
“We had a change in the waters. It showed our friction reducer was not producing the same friction reduction seen in stages before,” Blevins said, adding that the work went as planned from there.
Blevins uses considerably less polymer per gallon to reduce friction when mixing polymer on site. He said that may be because the fluids in the liquid mixes form residues on hoses, leaving some of the polymer behind. He has concerns about whether some ingredients of liquid friction reducer have downsides.
Van Domelen sees no problem with liquids where the polymers are mixed with an emulsion made of mineral oil and water—which DCS sells. He said some liquids are suspensions—the polymer is delivered in a liquid that includes suspension agents, surfactants, and dispersants. Allowing that some of those ingredients may cause formation damage, Van Domelen noted that the possible production loss from friction reducers is far less than guar, the product it has largely replaced.
Switching to dry polymer simplifies purchasing somewhat. The choices offered by DCS are based on the range of polyacrylamides offered by chemical companies, and the choices are many. The polymer molecules are available in different sizes, which has its pros and cons. The cationic and anionic charge can affect the risk of damaging reactions. Each of these variables factors into the price.
Those variables are limited compared to the range of formulations available from additive makers. These manufacturers sell custom (often proprietary) blends with ingredients that promise to enhance performance.
One of the additive makers is Rockwater Energy Solutions, whose Vice President of Technology, Brian Price, said dry-cost savings need to be weighed against how that affects the performance of the fractured well. “It comes back to the applicability in a given field,” he said.
For an operator, the only way to measure what works in a well is to perform a field test. Even Blevins, who likes using powdered polymers, has not gone totally dry. Hibernia has been testing a liquid friction reducer lately. Blevins did not talk about the results, but did say he expects to go back to dry friction reducer later this year.
He is wondering if wells fractured with dry powder mixed on site in the Midland Basin of the Permian might perform better than wells fractured with liquids. So far, that is just a hunch.
“There is something there that is relevant to production,” Blevins said, adding, “We have not been able to get that analyzed yet. I think we are seeing better-producing wells, but it’s too early to tell.”
For Further Reading
SPE 204176 Dry Powder Delivery of Friction Reducers: A Step Change in Slickwater Fracturing by J. Blevins, Hibernia Resources; M. Van Domelen, Z. West, J. Rall, and D. Wakefield, Downhole Chemical Solutions.