The work on the drilling floor of the PaceR801 rig revolves around a stout robot methodically picking up sections of pipe and moving them precisely over the drilling center to rapidly connect the pipe.
While it is one of many technological advances on the rig Nabors bills as “the world’s first fully automated land rig,” the robot is the one “that gets most people interested and excited,” said Travis Purvis, senior vice president, global operations for Nabors Industries Ltd.
As of 18 October, the PaceR801 had completed the first well on an ExxonMobil pad and was drilling the lateral on the second well of the three-well pad. After the third is done, the extended test will move to the next pad.
It is risky to announce who came in first in a competitive race in a secretive business. But Nabors stands out because the PaceR801 has an automated drilling floor, a range of other automated functions above and below ground, and most significantly, it is the only one using its rig to drill producing wells for a customer.
Jason Gahr, operations manager for unconventional drilling at ExxonMobil, said the research collaboration “demonstrates the ability to optimize drilling using the combined power of robotics, automation, computing, and data.”
Since the announcement, Nabors has heard from other oil companies. “There is strong interest in the rig in many markets,” Purvis said.
The companies’ interests range from automating more drilling functions by retrofitting rigs, to wanting to hire the rig, whose name is frequently shortened in conversations to R801.
There is only one PaceR801 and it is going to be tied up for a while. “We expect to drill multiple test wells on multiple pads and continue to work on the technology” with ExxonMobil, Purvis said.
It was created to show off the fruits of a 5-year drive to create a totally automated version of its Pace high-specification rig. Nabors likens it to the concept cars built by automakers to show off their vision of the future and to promote innovation within the company.
In this case, it is a vision of the near future. While the automated drilling floor is new, much of the rest is recently proven technology. Two of the drilling automation programs used—Nabors’ SmartSLIDE and SmartNAV—are already on 30% of the Nabors fleet, said Austin Groover, director of operations for smart products at Nabors. Those applications, which manage drilling of the curve and directional drilling, plus a third that automates drilling a stand of pipe, SmartDRILL, have been used by ExxonMobil for 2 years.
Maximizing the performance of a rig with multiple proven technologies plus a new one such as a robotic drilling floor required developing a system that coordinates the movements of those apps and the rig hardware while drilling.
When Nabors experts describe that process, they rely on musical metaphors, from the robot doing its little dance to a conductor leading a symphony.
“There is a human in the driller’s cabin turning the system on and hitting ‘play.’ From that point, the system is doing all the orchestrating,” Groover said. This mechanical symphony is conducted by a program called the “sequencing engine.”
Delivering on the promise of faster, better drilling requires a series of precisely executed steps with a minimum of time lost between movements.
A rig floor video would show the robot reaching over to pick up the next piece of hardware—normally a 45-ft segment of pipe that had been measured and its threads doped previously by the system. The arm then moves it over the well center and holds it vertically in place while other machines recognize the thread pattern and spin the pipe to connect it with the right level of torque. Then another application takes over to lower the drillstring to the bottom and resume drilling according to ExxonMobil’s specifications.
The number of steps actually required is far greater than one wordy, oversimplified paragraph can express. ExxonMobil is now working with Nabors to see if the innovation will translate into improved performance.
The future of automation depends on how the customers grade the drilling performance.
Speed is an obvious, required measure of performance. Better-executed well plans are also a goal, but that is much more difficult to measure, as is the impact of hole quality on future production.
Occidental Petroleum’s goal for automation is to “capture knowledge,” said John Willis, vice president for drilling and completions for onshore and carbon sequestration for Occidental, in in his keynote address at the recent IADC Advanced Rig Technology Conference (ART) covered by the IADC Drilling Contractor.
Willis was referring to capturing the most efficient way of doing a task in the control system so that a lower-skilled driller could perform at the same level as a more highly skilled driller by relying on automation to apply the lessons learned to drill a well faster and better.
So far, he said, they have not found a system that meets that standard.
Are Robots Better?
The R801 is a sign of significant progress on the journey toward fully automated drilling but remains far from the end point.
Automation has creeped into critical drilling functions, from drilling curves to minimizing stick/slip and tripping while connecting pipe.
The industry has been working toward this point for more than a decade. Work on Nabors’ drilling floor robot dates to 2008 when Equinor initially funded a Norwegian startup, Robotic Drilling Systems AS. Nabors acquired it in 2017 after the equipment was evaluated on a Norwegian test rig.
The company founder, Lars Raunholt, described the goal as “a seamless system where the machines work together.” Because sensors are continuously updating the spatial awareness program, “we do not have to stop and check if it is in the right place.”
“The robot and automation can identify what we call ‘odd objects,’” like a bottomhole assembly and get it when needed, said Josh Price, West Texas area manager for Nabors, during a presentation at a recent meeting of the IADC Advanced Rig Technology committee.
The robot made by Nabors’ Canrig unit can expand its capabilities by choosing from an array of tools, including one that can grip and spin a stand of pipe. It also can handle casing, opening the door for automating completions as well.
An automated pipe-handling robot is a striking advance because the industry has been slow to mechanize pipe connecting. That work continues to be largely handled by crew members using increasingly sophisticated tools. (This is not the case on offshore rig floors, where the larger-diameter drillpipe is heavier and riskier to handle; the rig floors are larger, providing the space needed for traditional mechanized pipe handling).
There has been little demand for mechanical pipe-handling systems for land rigs because “humans can move really fast,” said Paul Pastusek, drilling mechanics advisor for ExxonMobil, while speaking at the ART committee meeting.
This has been a barrier to automating pipe-handling on land rigs because a mechanized process is needed for automation to take control. Pastusek said the incentive for mechanizing on shore has been low because “making it that fast is really hard.”
Nonetheless, Nabors’ Purvis said the automated system will outperform the status quo on two critical measures that motivated Nabors’ CEO Anthony Petrello to approve the development of the R801.
“We absolutely had to get people out of the red zone. He was totally motivated around that point and a belief in the ability of automaton and robotics to consistently deliver top-decile performance every time,” Purvis said.
The two goals are bound together. Getting workers off the rig floor will move people out of a hazardous area. And robotic pipe-handling speed requires a workspace free of humans. A powerful machine programmed to avoid harming people will be slowed by software ensuring it stops before hitting nearby humans, who are prone to unpredictable moves.
While there are no people on the drilling floor, the crew there previously will still be working on the rig to perform inspections, maintenance, repairs, and rig moves.
Training will be required as rigs get increasingly automated. The Nabors statement said automation will “provide reskilling opportunities for Nabors employees and the broader industry workforce.”
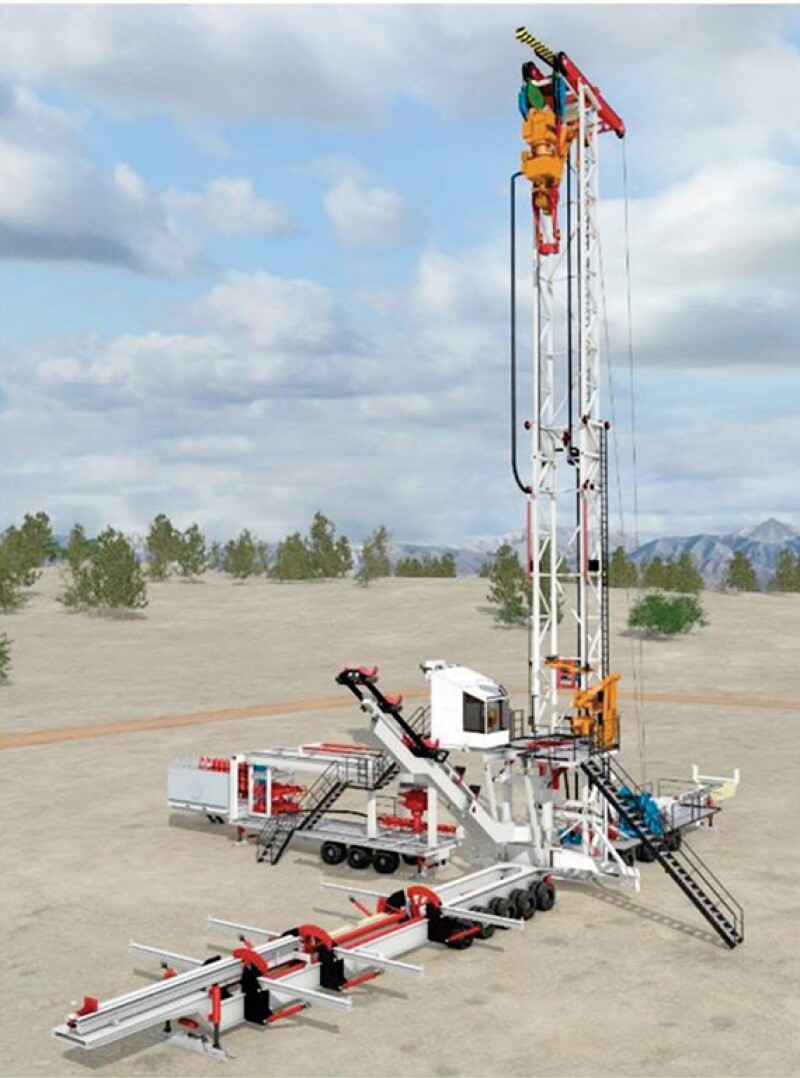
Less Than a Minute
So, how fast can Nabors’ automated rig connect pipe? The short answer is: They are not saying. The news release about the test said, “Consistent with the practices of drillers and operators on test pads, Nabors and ExxonMobil do not plan to publish performance data and results.”
A description of the robot on the Nabors website said it is capable of pipe connection times—from slips to slips—of less than 1 minute. It added the qualifier “based on early studies.”
The speed estimates are in line with those made by Huisman, which has built a land rig with automated pipe handling for Sirius Well Manufacturing Services, a drilling services joint venture between Shell and the China National Petroleum Co.
Huisman reported that the rig’s automated tripping system can handle casing at a rate of 1,800 ft/hr after the operator pushes the start button, based on performance data from a test well at a company yard in the Netherlands, said Arthur de Mul, product manager of modular rigs for Huisman (SPE 199597).
Nabors and ExxonMobil have gone further, using the R801 to drill producing wells.
Purvis said the R801 is drilling faster than high-performance rigs 5 years ago. Since then drilling has gotten faster so they will need to do better eventually. But the systematic testing program does not sound as though it is designed to set speed records early on.
When comparing automated drilling to traditional crews, it is useful to recall the fable of the tortoise and the hare, where a steady effort beat the faster runner.
When 1-day drilling records are announced, no mention is made of the rig’s performance on the next day. Chances are they are not as fast based on the connection-time data gathered by monitoring programs. They observe that the speed of the work varies from crew to crew and from day to day for each crew.
Drillers at the controls are feeling a different form of performance pressure—a growing number of routines required by customers’ evaluations of the best way to manage drilling. Either way, it is hard for workers to consistently execute specific routines over long shifts, day after day.
“There is a human-element variable in the performance outcome,” Purvis said. With automation “we can get our rig to a best-in-class level and to almost guarantee that repeatability.”
In automated drilling, the human inputs include the drilling plan and the system software. The companies are analyzing drilling performance as they go and making changes driven by their observations.
“In terms of the software, we have been learning as well,” Groover said. He said they have been removing some “overengineering” in the control software to improve performance.
Rig of the Future
The definition of the fully automated rig will evolve over time. What is considered fully automated now is this year’s version of capabilities. Rigs of the future will vary with technology advances, the evolution of the oil business, and how a list of automation issues are addressed.
High on the list are the proprietary coding and connections software and equipment that make creating an automated system using components from multiple suppliers a daunting challenge. Interoperability is needed to make hardware and software that can be integrated like the components of a personal computer.
That is certainly not the case now.
ExxonMobil is working with four companies that are primary suppliers of automation systems and three other big service companies that supply key components, Pastusek said at the ART committee meeting. “With multiple systems and multiple users, the operator has to be the system integrator.”
In his keynote speech at ART, Willis described the problems faced when trying to interconnect equipment based on different proprietary designs. “When we go to try to buy automation, it’s really hard to get,” Willis said “We’re largely limited to what’s available from individual drilling contractors. It’s very difficult, if not impossible, to take something from another third party and add that to a rig. And none of our rigs have what we would consider to be a full system of automation today,” he said.
Adding to the confusion, rigs are equipped with various combinations of software and hardware. All of which means that getting an automation system up and running takes time before it becomes possible to begin learning how to use it most effectively. “It takes 9 months to a year to put an automation system in place,” Pastusek said. By then the contract on that land rig has run out, or will soon, wasting the time spent solving the problem.
A drilling contractor would respond that this new approach to drilling requires new contract terms. Those agreements would rethink the traditional relationships, with longer-term contracts priced to reward drillers for investing in rigs that cut the days required to drill a well and improve the quality of the hole.
Rewarding productivity has proven to be a more difficult problem to describe than to solve. It is obvious that paying by the day means those who work faster are paid less, but after years of talking about the problem, there is no widely used performance-based payment system alternative to day rates.
Smarter Reactions
Rigs of the future will need to be designed to accommodate advanced digital data analysis, including adjustments based on analysis using applications provided by customers.
“We have certain apps that we want to apply on all of our rigs, so that’s a really important thing to us and it’s something that will be a factor in our rig selection in the future,” Willis said.
Based on its analysis, ExxonMobil lists 150 parameters to be programmed into rigs working for the company, covering everything from the weight on bit while drilling to rate for starting to drill, Pastusek said.
He is looking forward to a future where the systems can adjust the setpoints based on drilling data revealing unexpected changes. “Rather than preprogramming those, we will allow them to be adaptive,” Pastusek said. It is something Groover would also like to see. “There is a further opportunity to tie in more downhole data to surface automation that would be the next iteration of automation,” he said.
The number of sensors on rigs and drilling equipment continues to soar, and suppliers like Halliburton are working on improving the data gathered while drilling. Its new generation of measurement-while-drilling (MWD) tools will handle downhole processing of the data gathered, allowing it to be fed directly into an automated control system.
While the volume and quality of the data is growing, the amount that can be delivered in real time to the surface is generally limited to what can be sent using mud pulses, which deliver a limited amount of data and only work when the mud pumps are on.
Halliburton’s new MWD system will allow quicker downloads when the drillstring is pulled, but that remains far from real time. The fastest way to get data to surface would be wired pipe, which could also carry power and commands back downhole, but it is not often used.
“We hear that wired pipe is the holy grail with fast two-way communication. The reality is wired pipe has been around for 15-plus years,” said Paul Cooper, product manager, Halliburton Sperry Drilling, during an interview about the new MWD system called iStar.
The service company is involved with another automation option—taking it downhole. Halliburton has been involved in a test where the data gathered and processed downhole are used by a rotary steerable system to manage its course corrections.
“This is happening today; they are running it in the Eastern Hemisphere in a couple countries,” said Neila Kadri Bebaud, strategic business manager, Halliburton Sperry Drilling. She said there “have been 70 automated rotary steerable runs without any human involvement.”