As demand for energy continues to rise and conventional sources become more scarce, oil and gas companies are under pressure to pursue production through unconventional methods and enhanced oil recovery (EOR) technologies. Nearly all unconventional and enhanced recovery methods involve significant amounts of water and, therefore, specific technical and management challenges related to water.
Not only does this trend have significant implications for the water treatment business, it also calls for a new level of cooperation between the industrial water treatment sector and the oil and gas industry. With the growing and urgent need for better, commercially effective ways to handle produced water from unconventional production, the question of how the oil and gas industry will be able to access the best that the water treatment industry has to offer now shows the beginnings of a possible answer. The water treatment industry has started to appreciate the complexity of water challenges in the oil and gas industry. Likewise, the latter has begun to look to the former for solutions.
This article will review the market drivers and environmental risks behind the rising significance of water treatment in the industry, discuss how some oil and gas producers currently look at the problem of persistent water treatment technology gaps, and point the way forward for better professional collaboration among stakeholders and the development of business opportunities. The time is right for energy companies to see that they have synergies with water companies and for both sectors to recognize that the challenges of water scarcity and environmental protection are, if handled appropriately, opportunities.
Market Drivers
The current growth in the water treatment market is directly linked to oil prices and demand. With Brent crude holding just above USD 100/bbl and long-term projections predicting that oil will remain a significant portion of the energy mix, energy producers are approaching the problem of declining production from older reservoirs by extracting as much oil as possible from existing assets through the application of EOR methods, most of which require the injection of large amounts of water (miscible gas being the main exception). Extracting oil from mature fields also means that oil companies have to handle the problem of an increasing water/oil ratio (WOR) in the production process (Fig. 1). Water production estimates were approximately 250 million B/D in 2007 for a WOR of approximately 3:1 (SPE, 2011); WOR is expected to reach an average of 12 for onshore crude oil resources by 2025 (GWI, 2012).
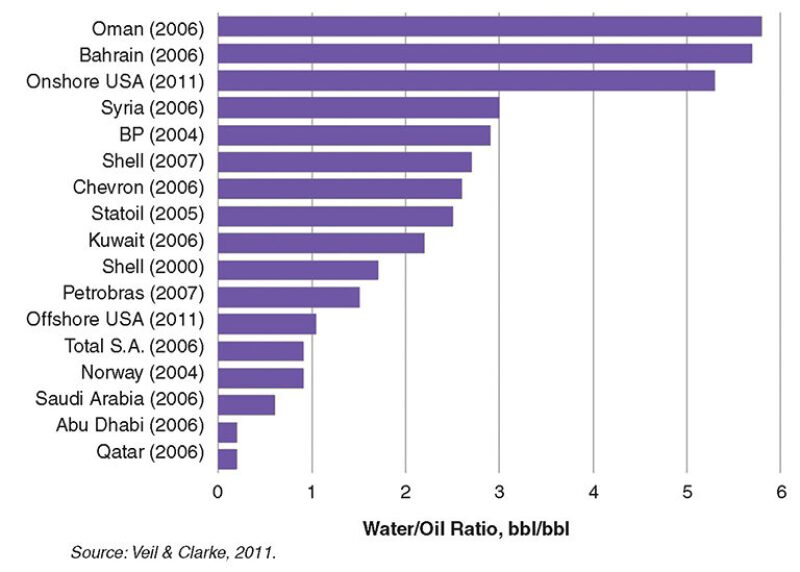
In addition to boosting production from existing fields, these same market pressures have led producers to develop unconventional geological formations such as shale rock, oil sands, and coalbeds. Nearly all forms of improved, enhanced, and unconventional extraction involve large volumes of fluid injection. Water is the natural choice because it is nonflammable, nonhazardous, and relatively cheap. Even in areas of relative water scarcity, water is still the most effective choice and involves less risk compared with alternatives. This means that water management will be a significant issue in mature and unconventional field development. As the cost of treating this water for disposal or reuse goes up, oil companies will have to increase their investment in water-efficient technologies.
Forecast growth in produced water volumes up to 2025 is shown in Fig. 2. A typical water and oil production profile of an oil well in the North Atlantic is shown in Fig. 3.
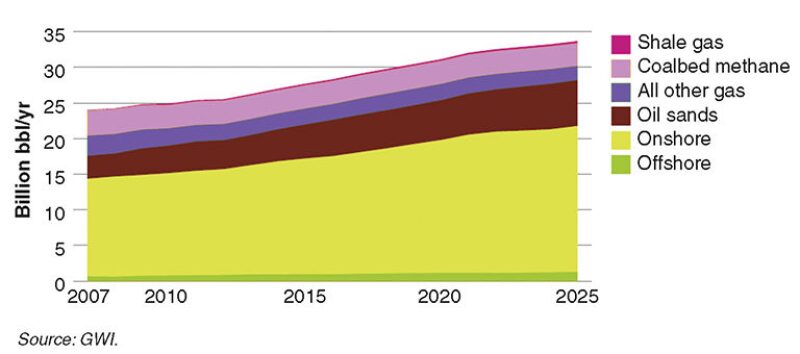
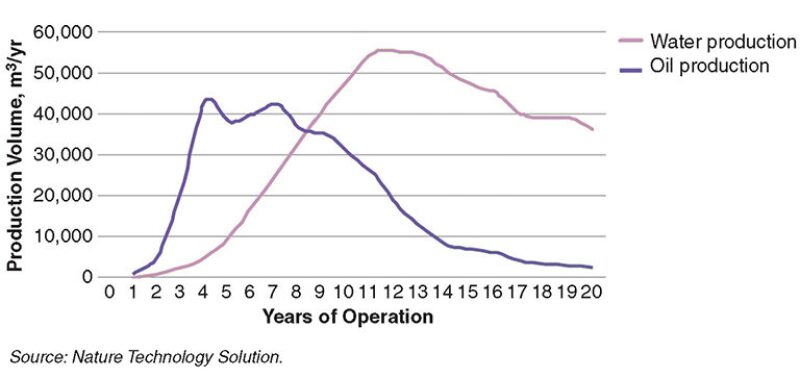
Environmental Risks
While rising market pressures are forcing a change in the value placed on water management by the industry and potentially affecting their long-term investment strategies, the environmental risk associated with the energy sector’s exposure to the water cycle also constitutes a serious issue for oil and gas companies. While these risks pertain to both onshore and offshore production, onshore water treating has specific environmental implications because of the ways water has to be sourced and disposed of in landlocked areas. Onshore water source competition from other industries, for instance, imposes limitations on freshwater acquisition and is a key driver behind the reuse of produced water for hydraulic fracturing, waterflood, and various forms of enhanced oil recovery, such as polymer and steamflood.
Furthermore, the impact of weather and droughts in many areas, especially in the United States, highlights the dependence of onshore energy production on the availability of water and the growing need for energy producers to find creative ways to promote water sustainability through the commercially effective application of water technology. In addition, oil and gas companies are increasingly concerned with incorporating the concept of sustainability into their business strategies and demonstrating to stakeholders, especially investors, that they give serious consideration to the environmental implications of their choice of production methods.
Water Technology Gaps
Because of both market and environmental pressures, the industry has given tangible recognition to the need to develop and implement alternative water treatment technologies. Over the past 5 years, a growing number of oil and gas producers, such as BP and ConocoPhillips, have created corporate venture sections within their companies with internal teams dedicated to sourcing promising new or growth technologies—and the companies developing them—with a view toward encouraging those developments through investment and then possible partnership or acquisition.
The question of how the technical challenges in the oil field might translate into market opportunities for oilfield service providers specializing in water-based technologies has been one of considerable debate not only at water industry conferences, but also at events sponsored by oil and gas producers. The trend among the oil majors in corporate venturing could go a long way toward providing the answer.
BP’s View
According to Sandra Eager, BP Ventures technology manager, BP is looking at a number of areas for development in water treatment technology. One emerging EOR technique makes use of low-salinity water. The world’s first offshore application will be on BP’s operated Clair Ridge field in the North Sea as it implements this LoSal EOR technology. The company is making use of conventional reverse osmosis membrane systems to produce low-salinity water from sea water. The requirement to minimize footprint and weight of the water treatment systems is a significant development opportunity particularly on existing oil offshore platforms, where space and weight capacity is often limited.
Membranes are sensitive to the very low levels of oil remaining in produced water using current treatments. “At the moment, we are using desalinated sea water,” Eager said. “But in the future, it would be great if we could additionally recycle produced water for low-salinity applications.” Consequently, a technology to treat produced water on site to a higher specification would be an attractive option.
However, the right technology for treating produced water, whether on low-salinity projects or in other applications, would have to be a flexible one. The chemical composition of the water and ease of oil/water separation can show a significant amount of variability from one region to another and even from well to well. Therefore, when it comes to produced water treatment, BP wants a technology that can handle a wide range of waters.
“A gap (in water treatment technology) is in handling the variability of produced water,” Eager said. “The ideal solution would be a one-size-fits-all technology that is easily adaptable and could be applied under the complex and varying circumstances that produced water presents.”
As more complex EOR techniques are used, there is a need for more sophisticated monitoring of injected and produced water properties, such as chemical compositional changes. These need to be real-time to allow rapid response on the platform. “At the moment, we take samples, send them off to a lab, and, for some of the more complicated analyses, receive the results some 2 weeks later. It is not an ideal scenario. So the holy grail would be a real-time, online, multiparameter sensor,” she said.
Additional and more accurate onsite testing technology could also have further application for ensuring that new and more challenging discharge requirements are met. “It would give us the security that what we were discharging was exactly in line with environmental limits,” Eager said.
Electrocoagulation, a water treatment technology that uses electric current to bind together contaminant particles, thereby enabling more effective water filtration, is by no means a new technology. Yet, according to BP, it remains a technology that presents difficult problems in oilfield water treating. For example, its performance in use for treatment of unconventional flowback waters has resulted in mixed reports. Challenges that operators have encountered include a high tendency for fouling, struggles making it work at high volumes, and the cost.
Nevertheless, electrocoagulation has recently received renewed visibility by companies such as Halliburton, and companies, including BP, are watching it. A water treatment company with an appropriate range of electrodes and cell design that has the capacity to overcome the challenges of fouling, treatment volume, and cost would be very attractive, especially if it was shown to be robust and efficient for treatment of a wide range of upstream waters.
Another area of water technology of interest to BP is high recovery desalination, particularly for groundwater characterized as highly saline brackish waters. In water-scarce regions, where oil and gas operators need to access local brackish groundwater, it is important to maximize the recovery rate of the desalination process applied to this water. In future, standard processes designed to achieve 50% to 60% or even 70% of recovery will no longer be considered adequate. Desalination technologies capable of reliable recoveries of 80% to 90% would allow operators to cut down significantly on brackish water use, as well as reduce the extent to which brine evaporation ponds are used and the capital and operating costs associated with the construction of disposal wells and reinjection of the highly saline effluent.
ConocoPhillips’ View
Accurate onsite testing would have obvious applications for the monitoring of produced water quality or ensuring that discharge requirements are met. ConocoPhillips, however, is also looking at onsite testing technology for its added value, and Perry Berkenpas, its vice president of global production excellence, sees an oil sands application.
“The way to optimize the process and minimize the amount of water use requires online, real-time testing and those capabilities have not been in place for the types of water that we are dealing with,” he said. “Real-time monitoring is in place where you have relatively good water. But where you are dealing with relatively poor water, online testing capability has not been as strong. So we are testing some new tools right now on that front to be able to give online, real-time testing so you can adjust your process along the way.”
The advantage of onsite testing is that its embedded flexibility would provide solutions for more than one problem. In particular, it would speed up production processes, lower costs, and help oil producers manage their impact on the environment. Concern for environmental effects is a significant driver behind the corporate venturing trend among oil and gas companies and their programs for sourcing and developing new technologies.
For ConocoPhillips, it is fundamental, Berkenpas said. “Whether it is unconventionals, oil sands, or other places, what we are really looking to is where we can align and solve multiple issues. Not all water is created equal. Where the industry tends to rise to the challenge and deal with this quite well is when we deal with either improving recovery of hydrocarbons, lowering our operating costs, and, now more and more, you add a third leg to that, which is around improved environmental performance and less environmental impact. I think more and more, we are looking at where can technologies not only improve our cost structure, but improve our recovery and our environmental performance.”
Both BP and ConocoPhillips want water technologies that focus on the bigger picture. The search is out for technologies that will serve a whole host of businesses from upstream production and produced water treatment to refineries and petrochemical plants. Oil and gas producers also want technologies that address specific issues. Opportunities are there for water technology developers who know where the needs are and have valid solutions for them.
Technology Uptake Still Lengthy
Oil and gas producers are willing to take reasonable, calculated risks on certain innovations in water technology if they offer potential for increasing recovery or reducing the cost of production. Nevertheless, water technology development and uptake by the oil industry has often had a lengthy timeline, spanning decades in some cases. This is partially because only a fraction of ideas are good enough to make their way into common use in the industry. Indeed, water treatment in the oil and gas industry is typically more difficult than conventional industrial, municipal, and wastewater treatment. Yet progress is seen by industry insiders as being unreasonably slow. New ideas are hailed with a wave of enthusiasm only to be followed by failed field trials, periods of flat development, and then difficult re-entry into the market.
Certain concepts in water treating are impossible to develop without undertaking the time-consuming and expensive process of field trials and this has important implications for the cost of water projects and their schedules. Furthermore, all studies, whether pilot, laboratory, or field, require comparisons with other studies to be meaningful. Just because a technology works in one location with one type of fluid does not mean that it will work anywhere else. This makes it difficult to establish proper benchmarking. All these factors contribute to the time lags involved in technology uptake. Designing studies with proper benchmarking to ensure that results from different studies can be compared with one another is a priority.
Perhaps one justifiable reason for the slow uptake is the fact that getting the technology wrong on water treatment projects can be extremely costly. Problems in water treatment can cause a delay in project startup or cause serious delays in production. When mistakes are made, the true cost of water treatment can reach many times the cost of equipment.
An example of this is the experience the oil industry has had over the past 20 years with attempts to develop compact seawater deoxygenation technology. At the moment, the technology used for the deoxygenation of seawater consists of conventional vacuum and de-aeration towers. If the industry were able to implement membrane de-aeration (deoxygenation), this would not only provide a smaller and lighter system than the towers currently in use, but would also give a boost to other waterflooding technologies, including sulphate rejection and low-salinity water.
In fact, there have been significant attempts to develop membrane deoxygenation technology further over the past 2 decades. However, the failure of the most salient examples, Seaject in the 1990s and Minox in the early 2000s, has brought technology development in this area to a near standstill. The failures were costly and indicated a gap in the ability of the industry to adequately test and develop new technologies for field application. It is useful and illustrative of the problem to point out that Minox did eventually become viable, but only after Shell invested significant time and effort in re-engineering the initial design.
While implementation of membrane deoxygenation is proceeding rapidly in the onshore industrial water segment, it remains an elusive goal for oil and gas. This means that in deepwater fields, the competent design of compact seawater deoxygenation facilities is still a challenge.
A New Approach to Knowledge Sharing
The oil industry’s experience with deoxygenation technology highlights the need for a new approach to knowledge sharing within the water treatment sector. The publication of journals and research papers will not be enough to bridge the current gaps in technology development or reduce the time for technology uptake. To influence key decision makers in technology adoption and application in the oil industry, water technology developers need to establish a way of networking that gives access to the end user.
Oil and gas producers need to find water technology companies with the right technology for their particular water problem. Water technology companies want a way to present their technology solutions to producers. For that, they need to conduct pilot studies and establish a track record demonstrating that their technology can handle the variability of produced water in different areas and regions. An event for water technology experts to showcase the results of their pilot studies to decision makers in a nonmarketing, nonsales context would be an effective way to bring the two sectors together.
Last year, SPE took a significant step in this direction with the launch of the Global Integrated Workshop Series. The goal is to facilitate the sharing of water treating experiences and bring workshops to areas where there are distinct water-handling issues. The 2-day workshops are organized by top industry technical and project leaders with an even split of presentations and open discussions. Each workshop begins with a concise review of previous workshops in the series and ends with the presentation of ideas, issues, challenges, and questions for the next workshop.
To support the continued sharing of information, SPE has established an online community that workshop participants are invited to register and join. The community will provide presentation materials, previous workshop reports, participants’ contributions, and other contents from the workshops. Industry professionals will collaborate with SPE staff to ensure the technical accuracy of the materials presented online. Each posted report will build on the reports that precede it, thereby encouraging further development and refinement of ideas.
In addition, SPE is hosting a workshop on water lifecycle management in Galveston, Texas, in October. Also, to help organize all the events related to water, SPE has formed a Technical Section for Water Handling and Management.
References
Global Water Intelligence, 2012. Industrial Desalination and Water Reuse; p. 44.
Society of Petroleum Engineers, 2011. White Paper: Challenges in Reusing Produced Water; p. 1.
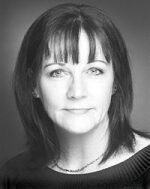
Gina Rowland is the program manager of the Business Insight Seminar series at Global Water Intelligence. Working closely with industry experts in desalination and produced water, she is responsible for identifying and implementing seminar opportunities in water treatment, especially those associated with the production of oil and gas.

John Walsh, SPE, is a consultant at Cetco Energy Services, which offers an array of technologies, products, and services for all phases of oilfield production. Previously, he was with GHD, an engineering and consultancy company specializing in water treatment. Walsh recently retired from Shell, where he was the global subject matter expert in upstream water treating. He has more than 20 years of experience in the exploration and production industry, having worked in Shell’s technical centers for half of his career and in operating assets for the other half. He has served on the SPE Board of Directors as technical director for the Projects, Facilities, and Construction discipline.